P7 M30 & LightBurnユーザーで,切り抜き・カットがうまくできないと諦めている方へのアドバイスです
エアアシストノズルの3Dプリンターデータファイルはダウンロードセンターにあります
- レーザー彫刻機を購入したらやってみたいことリストの,上位にくるのは”切り抜き”であると思う.金属板を切り抜こうと考えることはないだろうが,木製の薄い板はできると思っている人がほとんどではないだろうか
- 薄いベニヤ板を切り抜いたオーナメントやランタンなど,目にしたことはあるのではないだろうか?少なくとも私はレーザー彫刻機を購入しようと思った大きな理由の一つである
- レーザー出力5Wクラスのレーザー彫刻機の多くの商品説明では,可能であるとうたわれている.AmazonのP7 M30 の商品説明では,”厚さ5mmの木材も切断することができる”とある
- 購入前にいろいろなブログやYouTubeを見たりしていたので,かなり難しいことはわかっていたが,お買い得価格であったので,淡い期待を抱きつつ,ポチッとした次第である
- 果たしてどうであったか?その答えは“切断や切り抜きはできるが,そのためにはレーザー出力を100%で,速度をかなりゆっくりに設定し,パスの回数も多くする必要があり,その結果切断面は黒焦げで,綺麗さはみじんもない“である.つまり何らかの作品を作るのにはかなり大変な処理が必要であろう
- レーザー出力Maxで,レーザーモジュールをゆっくりにして,さらにパス数を増やせば切断や切り抜きはできるというレベルである.もう少し詳しく説明してみる
- まずは私が作りたかったものを紹介しておく.ご存じの方もあろうかと思うが,Etsyというサイトで検索ボックスに”レーザー彫刻”で検索してみるとレーザー彫刻関連のものがたくさん見つかる.基本的にデータファイルのダウンロード販売である.本機を購入後,結構購入した.何せ美術的才能は皆無なので,画像データはフリー素材か,データの購入が入手手段となる.英語表記のサイトなのだが,商品詳細のところに翻訳ボタンがあるので心配ない.お約束であるが,海外通販サイトなので,アクセス・購入は自己責任で!
- データ形式は dxf,svg,png,jpeg,ai,pdfなど欲しい物すべてがパッケージされている(zip)ことが多い.それらから製作された見本もある.しかもリーズナブルな価格(100円なんてのもある)であるので,自分のマシンで同じものを作れるかもわからずにポチッてしまうのである
- 最初に購入したのはこれである.サイズも本機のスペック上問題なく,ワークもAmazonから入手できる適当な3mmベニヤ板があった.100mmx100mm,厚みは公称3mmで角が丸く加工されたものである.そのまま彫刻してコースターを作ったりするには使い勝手が良い.早速購入して(この手のものにはあるあるだが,厚みの実測は2.7mmであった)試しにまずは外周の切り抜きを行ってみた.前述の通り懐疑的であったから内部の彫刻は後回しでまずはカットである.心配は的中し切り抜きはあきらめることになった
- ネットを探すと,本機P7 M30用のパラメータ例がATOM STACKからリリースされている.それに準じたパラメータ設定で切り抜きを行ってみたができなかった.もし本当できるならすばらしいP7 M30!となるのだが
こちらのページのP7シリーズにPDFファイルダウンロードリンクが有る - ここでお断りしておくが,低出力ダイオードレーザーはもともと木材の“切断”は得意でないということである.綺麗に切り抜いて製作されて販売されている木製コースターなどは,ほぼほぼ炭酸ガスレーザーで製作されていると思われる.参考までに素晴らしい作品を見ることができるこちらのサイトをご紹介
- 本機は5Wクラス半導体レーザー(ダイオードレーザー)機であるため,もともと木材切断は得意でないが,彫刻性能は素晴らしいものである.安価でお手軽(小さい)でこの彫刻クオリティ!ということである.出力の大きなレーザーモジュールは,複数のレーザーをミラーで合成して高出力にしているようだが,引き換えにスポットサイズが大きくなってしまう.P7 M30はその点スポットサイズ(彫刻精度)は0.01mmとのメーカー公称値なので,彫刻の精細さは実際素晴らしい
- 前置きが長くなったが,ここからが本題.前述のように色々と試してみた結果あることに気づいた.それはベニヤ板の裏側を見ると,完全に切断されていないが,部分的に薄っすらと焼け跡・ラインが見えることである.つまり,裏面ギリギリまで切断ができている.同様の切り抜きを試したことがある方なら,あるあるだと思う
- それなら,ワークをひっくり返して,裏から反転した画像でレーザーを当ててみたらどうなるかと考えた.果たしてこの思いつきはうまく行ったのである.メリットとしては,片面に照射するレーザーのエネルギー総和を少なくすることができるため,カットラインはスッキリしたものが得られる.また,レーザーダイオードの寿命を伸ばすことができる
- 思いついたのはいいが,表裏のカットラインがずれてしまう.それでも原点付近は上手くいく(ずれが許容範囲)のだが,原点から100mm離れると看過できないレベルとなってしまう
- これはこちらの記事でも触れている.表裏だと2倍ずれてしまうので原点から彫刻限界の200mm近くの両面カットでは1mmぐらいのずれとなってしまう.これが判明したころから,このプラン断念が頭をよぎってきた
- 通常の使用では全く問題なく,むしろその精密な加工レベルに感心しているのだが,両面カットなどするから気になってしまう.この状態が続いていたのだが,ずれの原因を考えるとLightBurn,P7 M30のいずれか,または両方,あるいは両者の相性が考えられると判断
- 最初にLightBurnを疑ってみることにした.そこでレーザー彫刻界のもう一つの巨塔 LaserGRBLを試してみることにした.ずれのテストを行って,問題なければ両面カットがうまくいくはずである
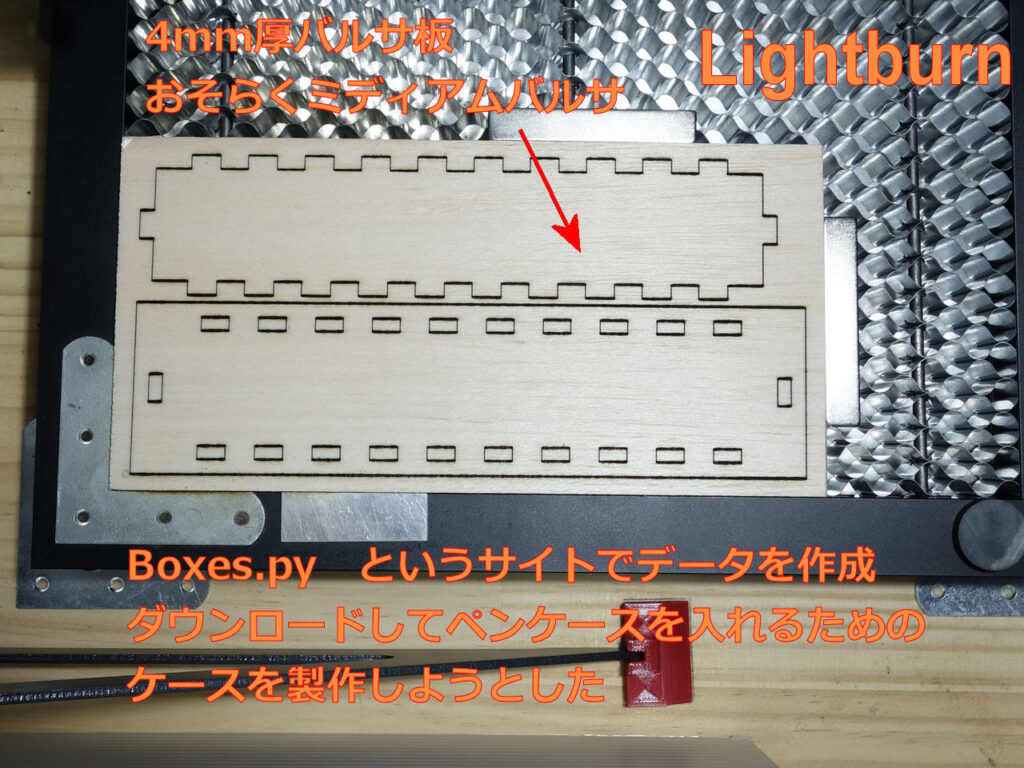
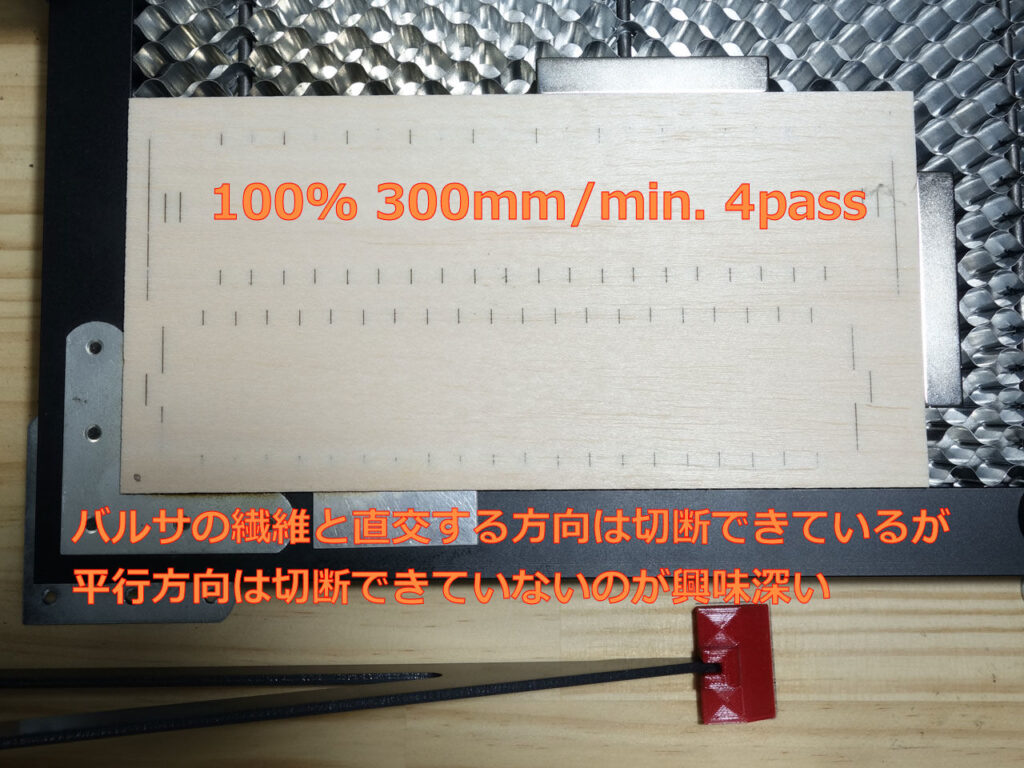
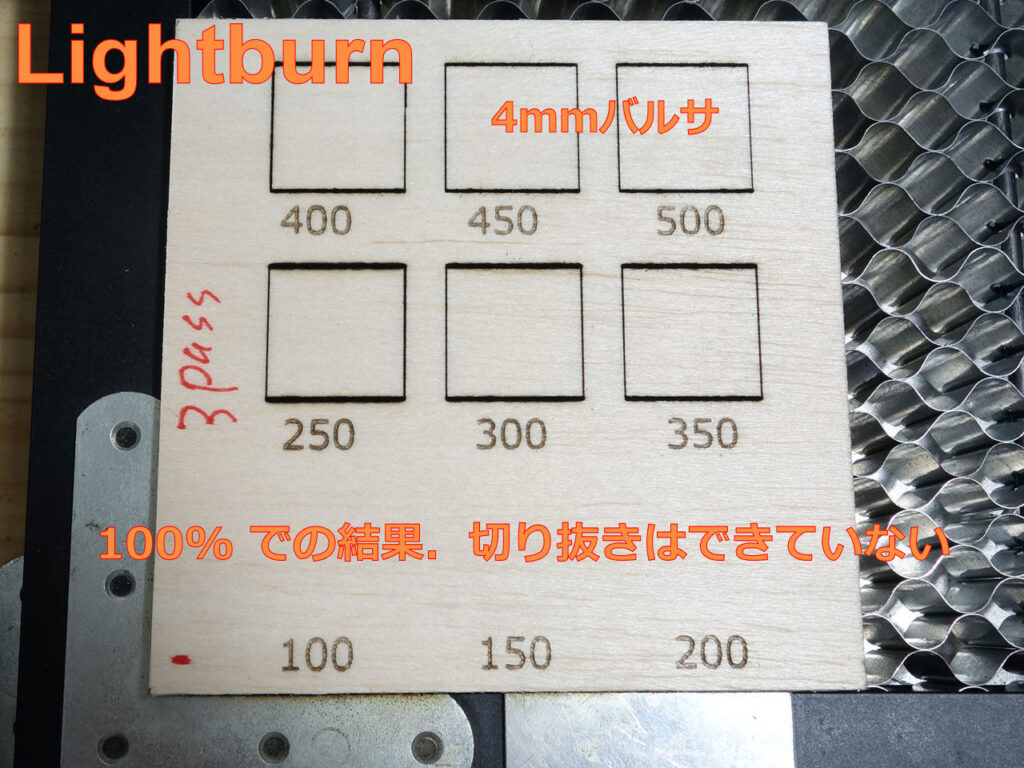
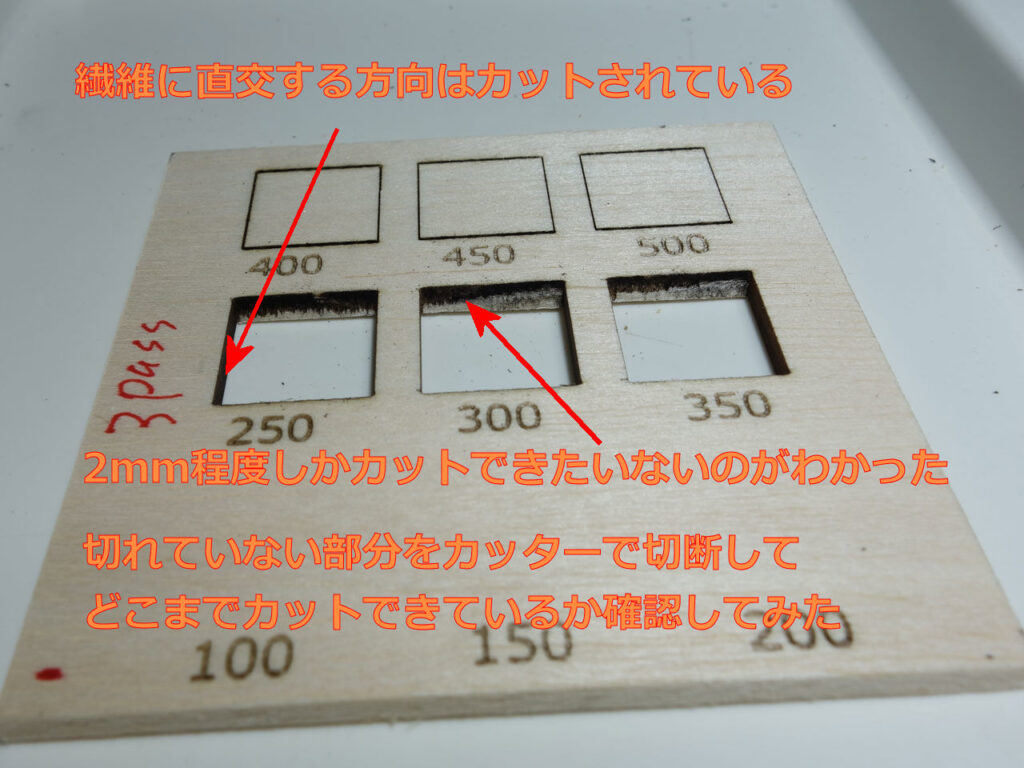
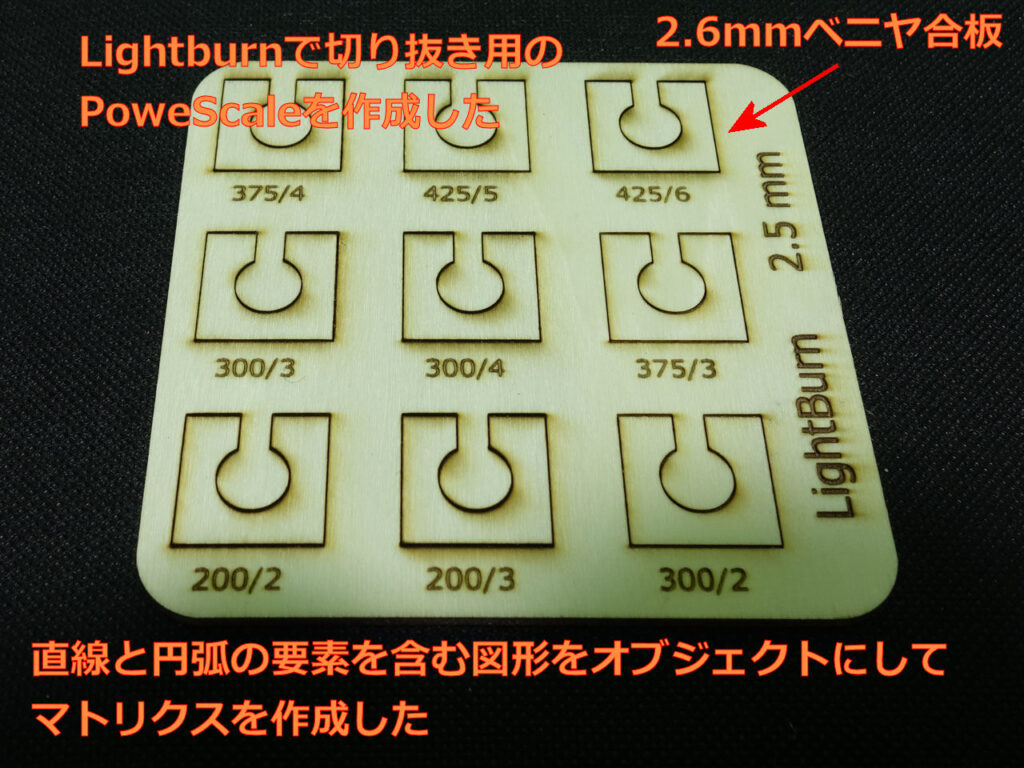
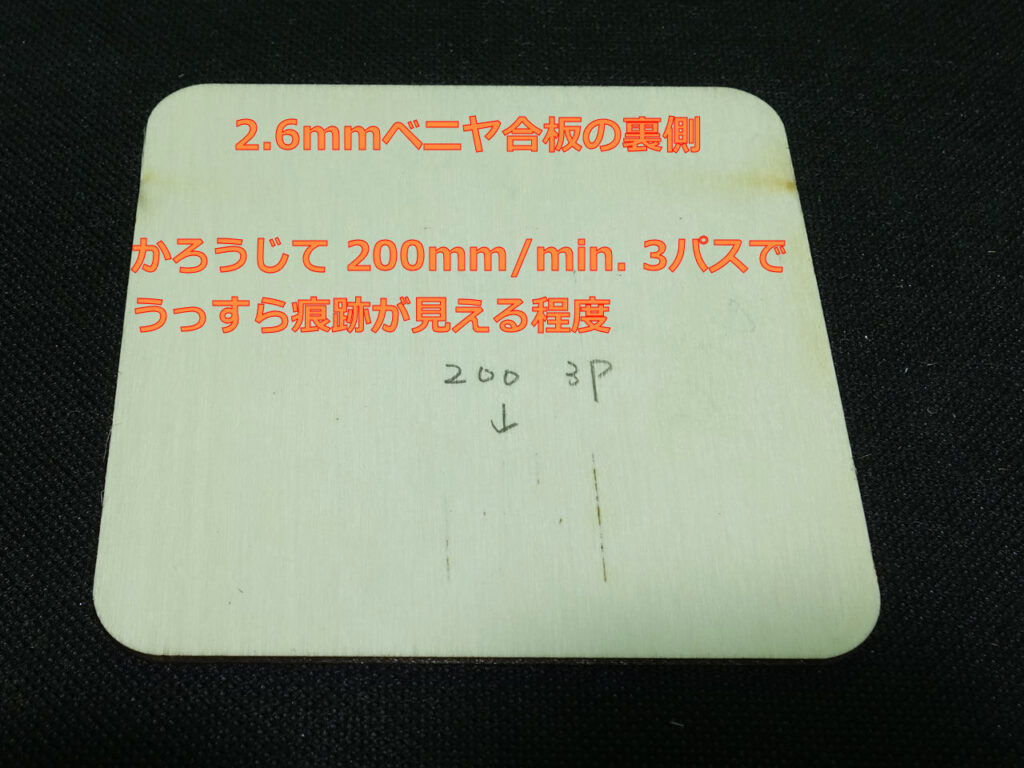
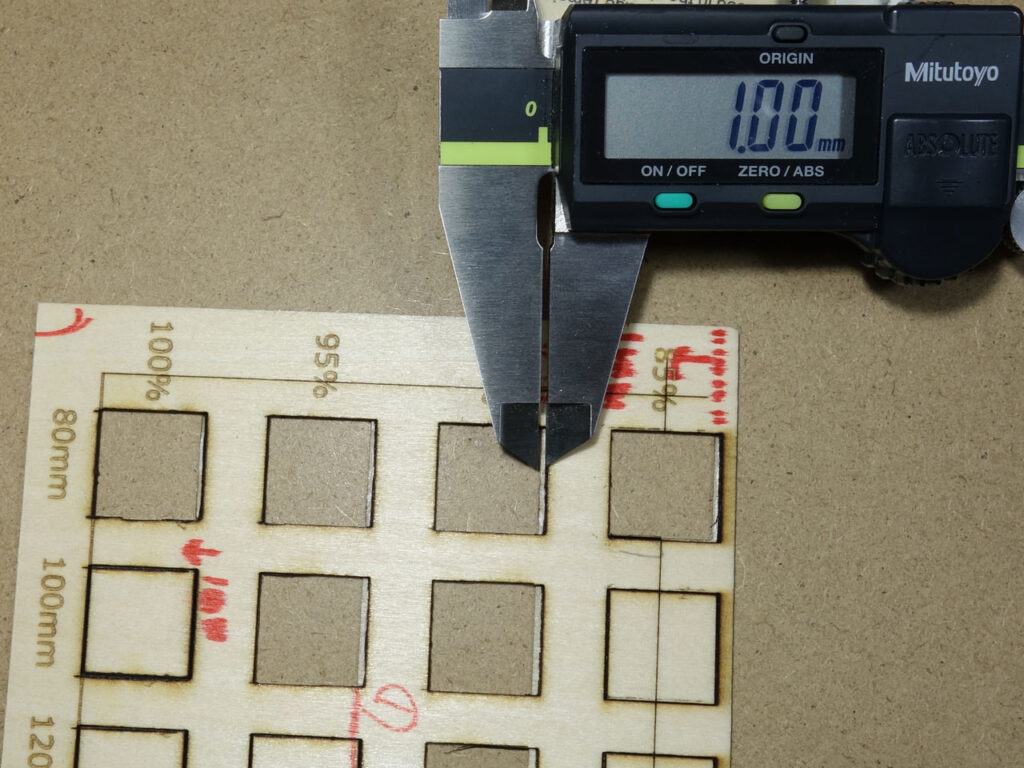
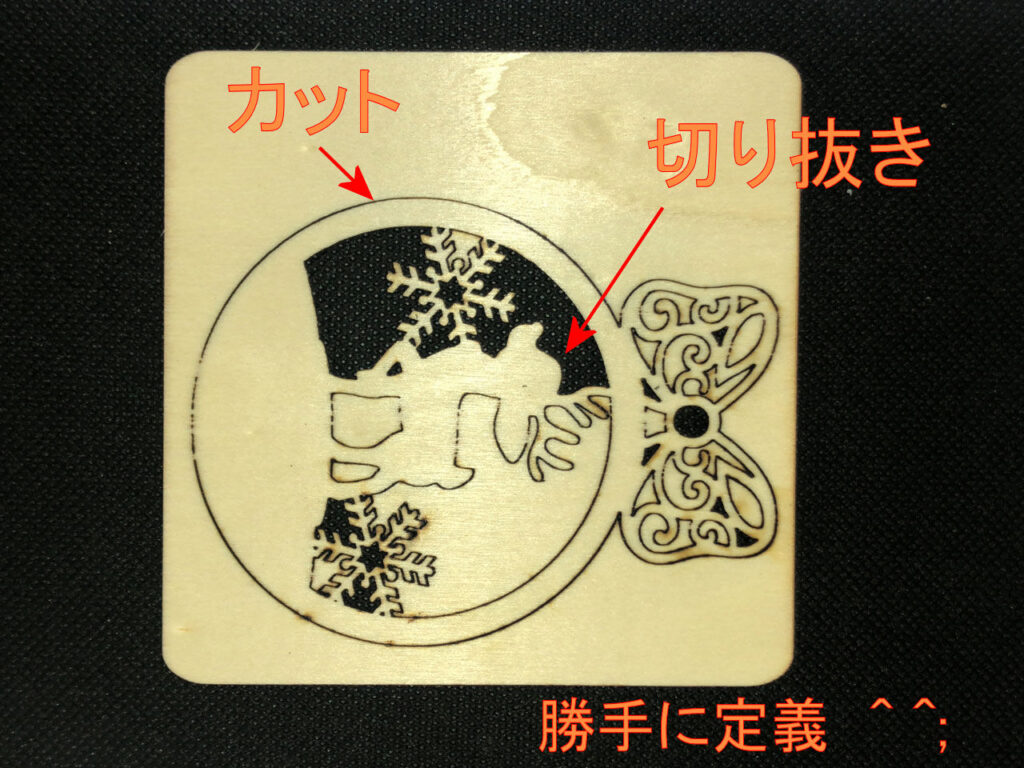
- 私が一番使うであろうワークは,Amazonで安価に購入できる100mm x 100mm のベニヤ合板である.見た目から厚さはできれば3mmのものも使ってみたい.しかし,それより薄い1.5mmや2mmのベニヤ合板を購入してオーナメントを製作してみたが,彫刻はとても満足な結果が得られたのであるが,デザインに切り抜き部分がある場合は別である
- ベニヤ合板は薄い木板を繊維の方向をずらして圧着・接着した物なので,カットはその影響を受けている節がある.綺麗にカットできる方向があったり,その直交方向はカットできないということがかなり多いことが分かった.平行な対辺のみ裏まで貫通し,他の対辺はともにカットされないか,薄っすらと点線上にカットされているが全く貫通していないということである
- うまくいかないのでたくさんテストした.パラメータの設定で何とかなると信じて.さらにはベニヤ合板の1.5mm 2mm 3mm,バルサ板の1.5mm 2mm 4mm,MDF板の1.5mm 2mm,化粧ベニヤの2.5mm,贈答品の桐箱の蓋,黒アクリル板の1mm 1.7mmなどデータを取りまくった.テストピースの残骸は山となり,ゴミ箱をいっぱいにしたが,楽しいので苦ではなかった
- しかしそれは問題の本質ではない.結局完全に貫通してカットができなければ作りたいものを作れないことになる.オーナメントはほとんどが円につるす部分(紐を通す部分)がついた形態となっている.前述の正方形のベニヤ板が,オーナメント外径でカットできなければつくることはできない.また,内部は彫刻よりも切り抜きでデザインされるのもがほとんどなので,これまた現状ではオーナメント製作は不可能ということになっている
- Etsyには,作りたくなるオーナメントのデータが多数ダウンロード販売されている.しかもほとんどが¥500以下のものである.サンプルをたくさん見て,何とかこれを作ってみたいとのモチベーションがどんどん大きくなり,いろいろと試してみるエネルギーとなった
- 閑話休題.P7 M30を購入し,ソフトはネットで評判が良かったLightburnをはじめから使用してきたのだが,ある意味それが最大の原因であったことが分かったのだ
つまり,「LaserGRBLを使えばP7 M30でも切り抜き・カットは満足いくレベルで行える」ということである - これから,詳細を書いていくが,その前にもう一つの結論を書いておく.それは...
・彫刻は Lightburnを使う
・切り抜き・カットは LaserGRBLを使う
・両方の要素を含むデザインの場合は,両者をいいとこどりで使用する
以上である.どちらも素晴らしいソフトであることが改めてわかった次第である - 本記事では,“切り抜き”と“カット”という同じような表現を使うが,ほぼ同じ意味で使用する.あえて言えば“切り抜き”はワーク(板材)から抜いて落とすように小片を切断する,”カット”はオーナメント外周をワークから切り離したり,矩形のワークの端を切り落とすイメージで使っている
- 前述の通り,Lightburnから入り,彫刻をいろいろ試した.それで大満足.そこで,切り抜き・カットを試してみたら2.5mm程度のベニヤ板を切り抜き・カットできずに失望してしまった.もし,LaserGRBLから入っていたら,切り抜き・カットで失望することもなかったはずである.しかし,その場合,Lightburnの操作性の良さには気づくのに時間がかかって,別の点で期待外れとなっていたことは容易に想像できる
- もう一度力説しておくが,”満足いく作品”を製作するには,Lightburn&LaserGRBLを連携させての使用が必須である
- 持論ではあるが”満足いく作品”とは,プレゼントしても恥ずかしくなく,喜んでもらえるレベルの作品ということである.プロの作る商品レベルではない
- そういうことなので,P7 M30ユーザーで,最初からLaserGRBLで切り抜きを行っていた方には,あまりう役に立たない情報かもしれないので,あしからず
- 今更ですが,単に私がLightBurnの使い方が間違っている,設定が間違っているなどの可能性もあるので,これまたあしからず
LaserGRBLのバージョンは日本語対応されたv7.14.0以後となります
- 両面カットでのずれはLaserGRBLでも起こるのかの検証前に,2.6mmベニヤ板(3mmと表記してあるが,実測では2.6mmだった)の切り抜きをやってみた.すると問題なく切り抜きができてしまった
- そんなはずはないと切り抜き用のPowerScaleを作ってみた
- まずは当然P7 M30を使用する前提なので,パラメータは理想的なものではなく,現実的な数値である.レーザーモジュールの移動スピードはマシン限界の3000mm/min.に近い程快適なのだがそうはいかない.希望値としては250以上はほしい.それより遅いと太くなってしまう
- レーザー照射のパワーは言わずもがな100%である.レーザー出力を固定するのがM3であるようだが,P7 M30は出力が可変できるので,M4という可変制御なモードを選択した.今後デフォルトにするであろうM4でテストした
- あとはパスの回数であるが,これは3回までならカットラインは太くならず,きれいな切断面が得られる.プラス1回で4パスをチェックできるように設定した
- 次項で詳細を紹介する
- LaserGRBLに搭載されているPowerScale作成のツールを使ってで切り抜きテスト用のデータを作成する.Lightburnの配列で作成するよりも簡単であるが,図形は正方形のみでサイズ指定はできないようである
- スピードとパス数を指定する.パラメーターの数値と指定した1行のテキストが彫刻されるが,すごく小さく彫刻されるので見づらい.テキストはデフォルトで入力されているが任意のテキストに変更できる
- Passesを指定する. from 1 to 4 とした.step size は自動的に変更される(ユーザー指定はできない)
- Speedを指定する.いろいろ試した中で from 150 to 400 Steps 6とした.step size は自動的に変更される(ユーザー指定はできない)
- テストピースをP7 M30にセットする.原点はLightBurnと同じ左手前とする
テストピースはデジタルシックネスゲージで実測した以下のものを,すべて上記PowerScaleで切り抜きテストを行う
このデジタルシックネスゲージは,計測の再現性が高く,ミツトヨのノギスとほぼ同じ値を示す
・1.8mm厚のベニヤ合板(2mmと表記されたものの実測)
・2.6mm厚のベニヤ合板(3mmと表記されたものの実測)
・2mm厚MDF
・2.5mm厚の黒カラーベニヤ合板(DIY店で購入)
・2.65mm厚の白カラーベニヤ合板(DIY店で購入)
・1.75mm黒アクリル板(2mmと表記されたものの実測) をクリックしてレーザーモジュールを原点復帰させ,
をクリックして原点として記憶させる
- パスの回数を
に設定して,
スタートボタンをクリック
なお,自作ノズルにエアアシストポンプを接続して,最大吐出量である 30L/min. で実行している
結果についての画像の一部は,状態がよく確認できるように,当ブログ記事写真サイズより大きなサイズでアップしている
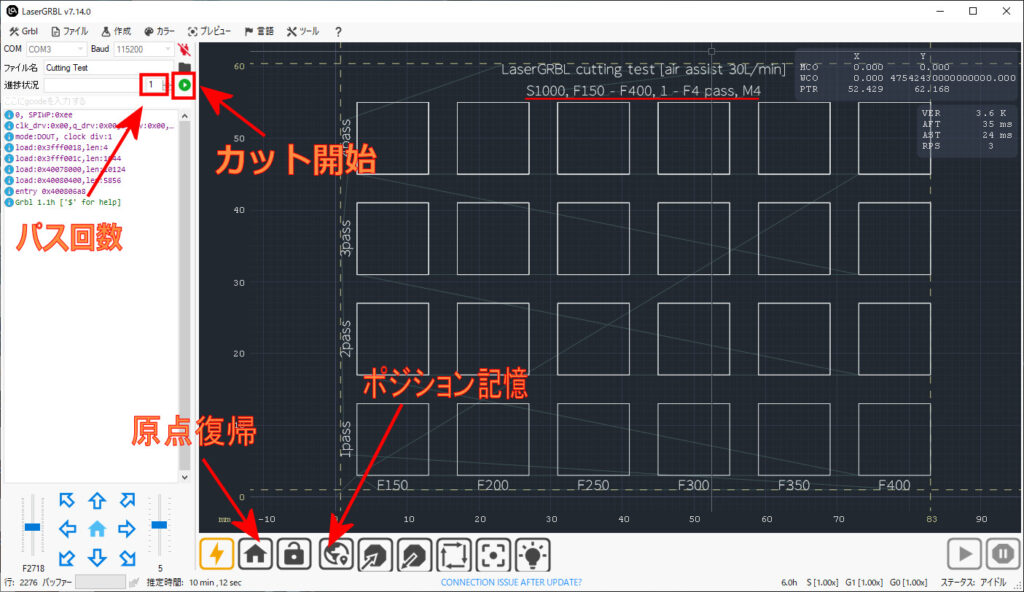
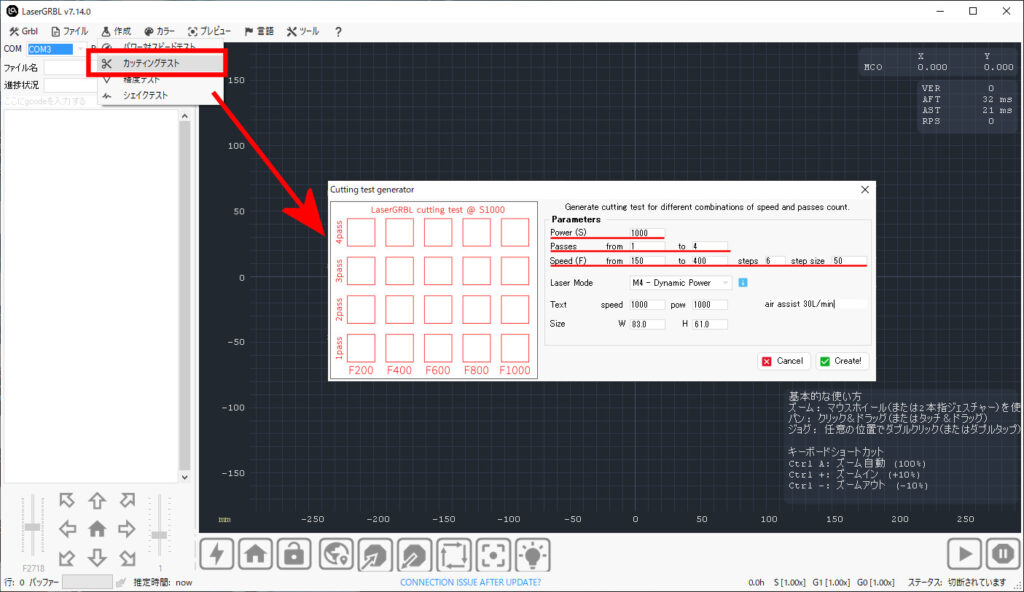
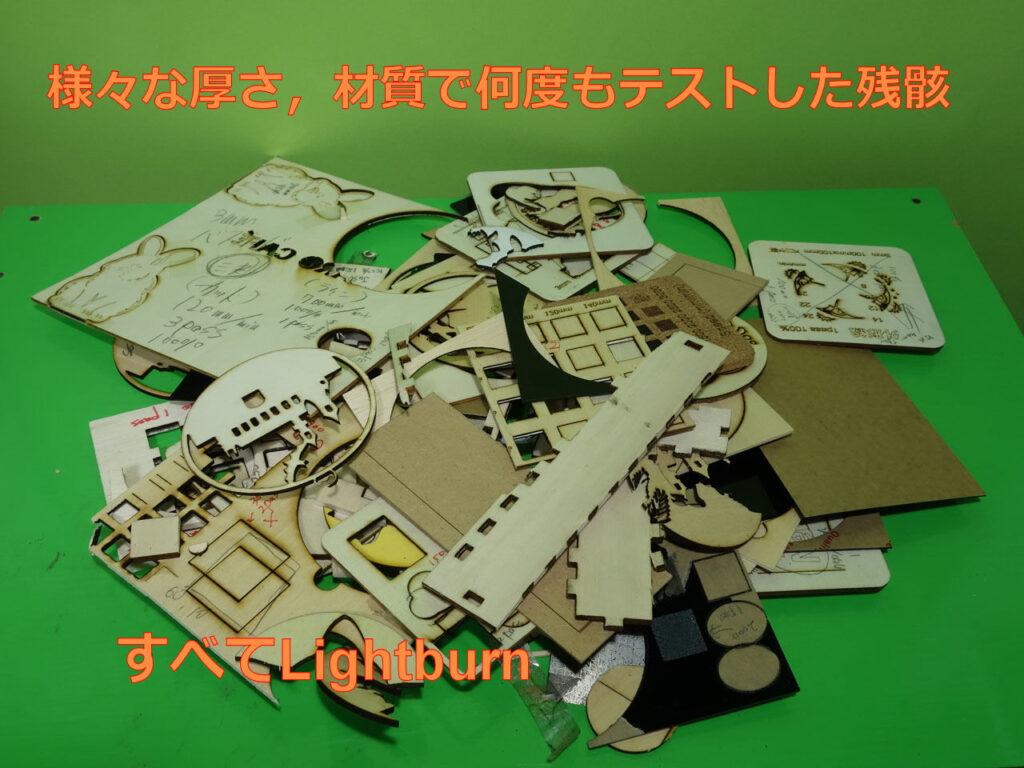
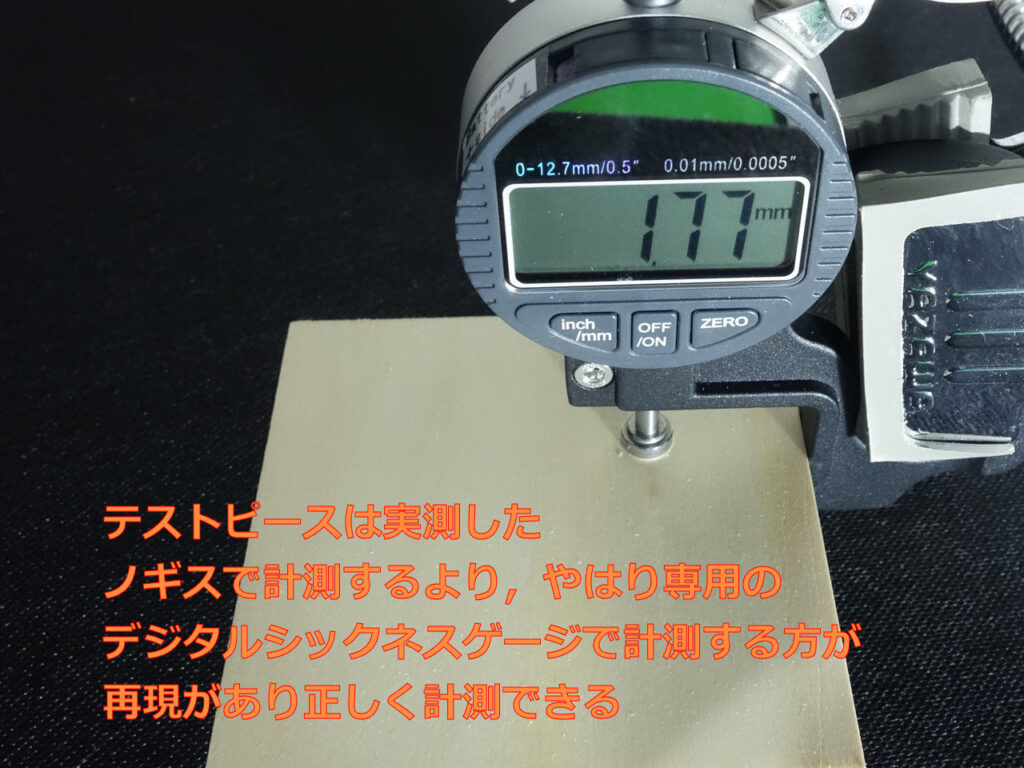
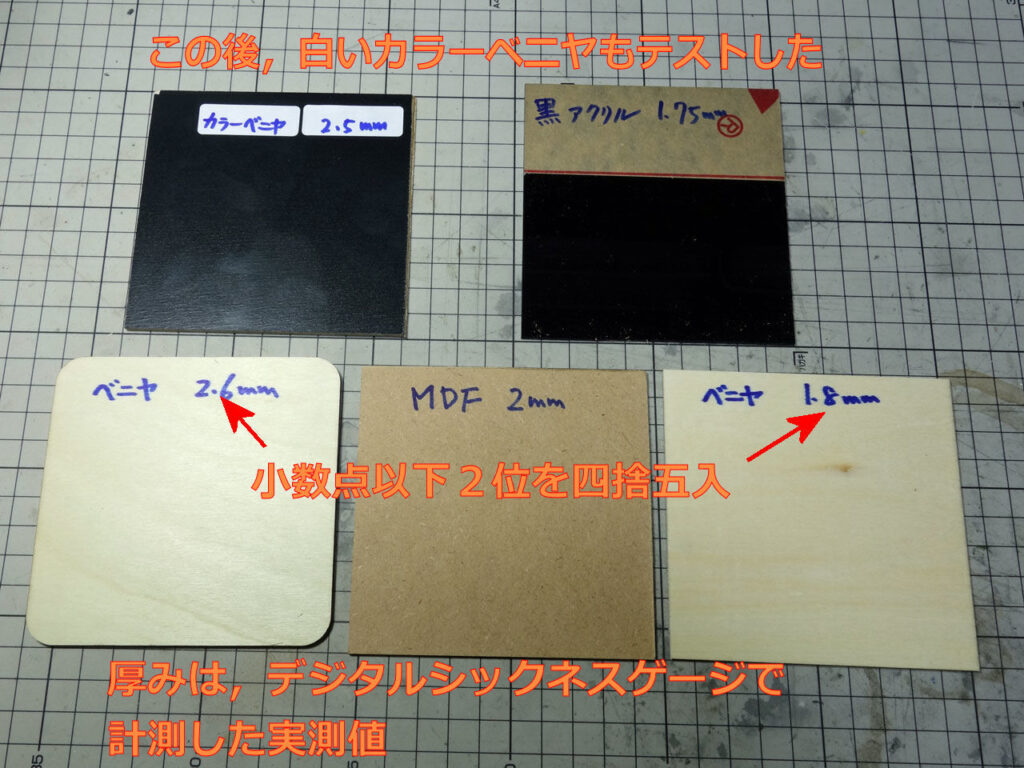
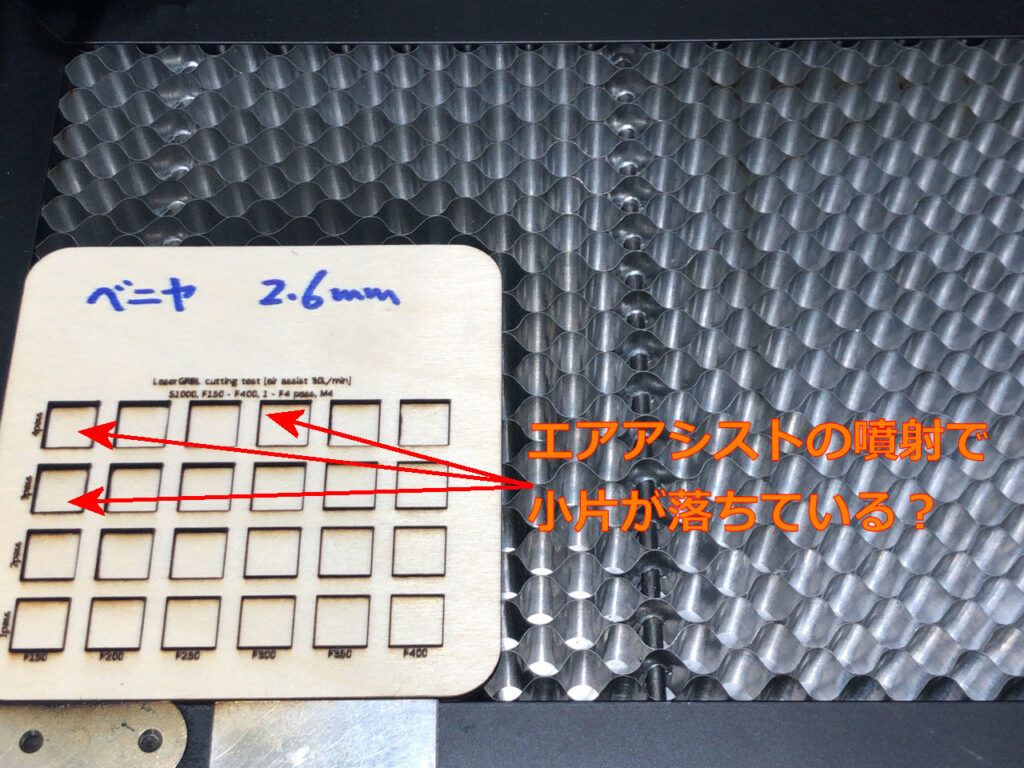
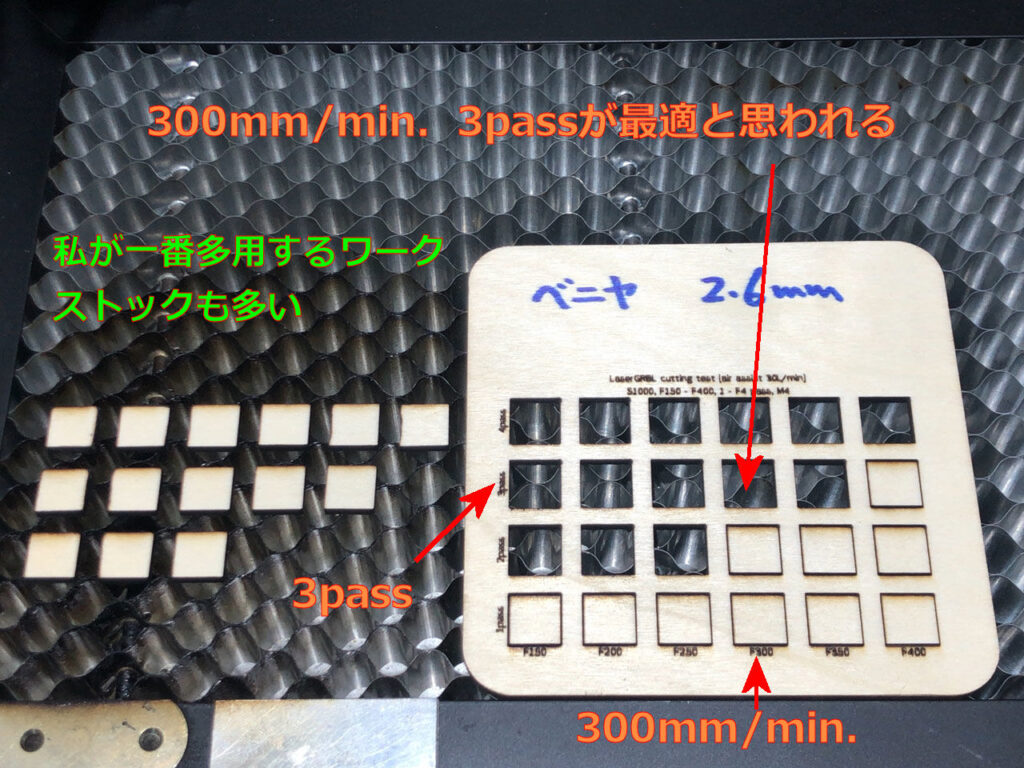
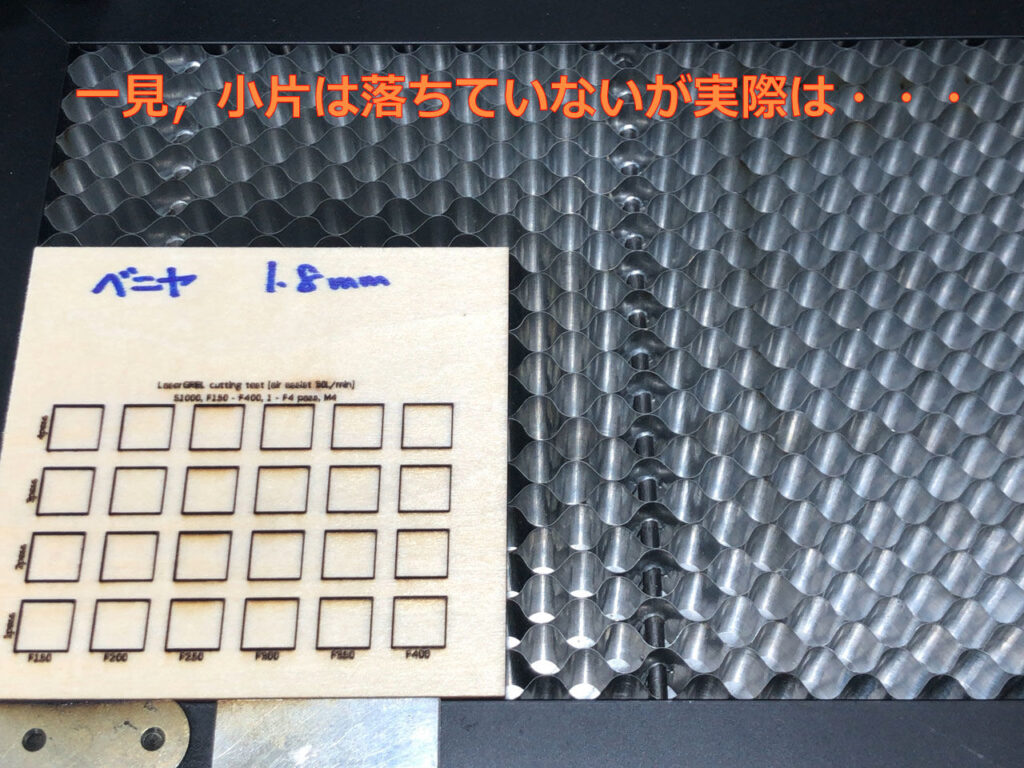
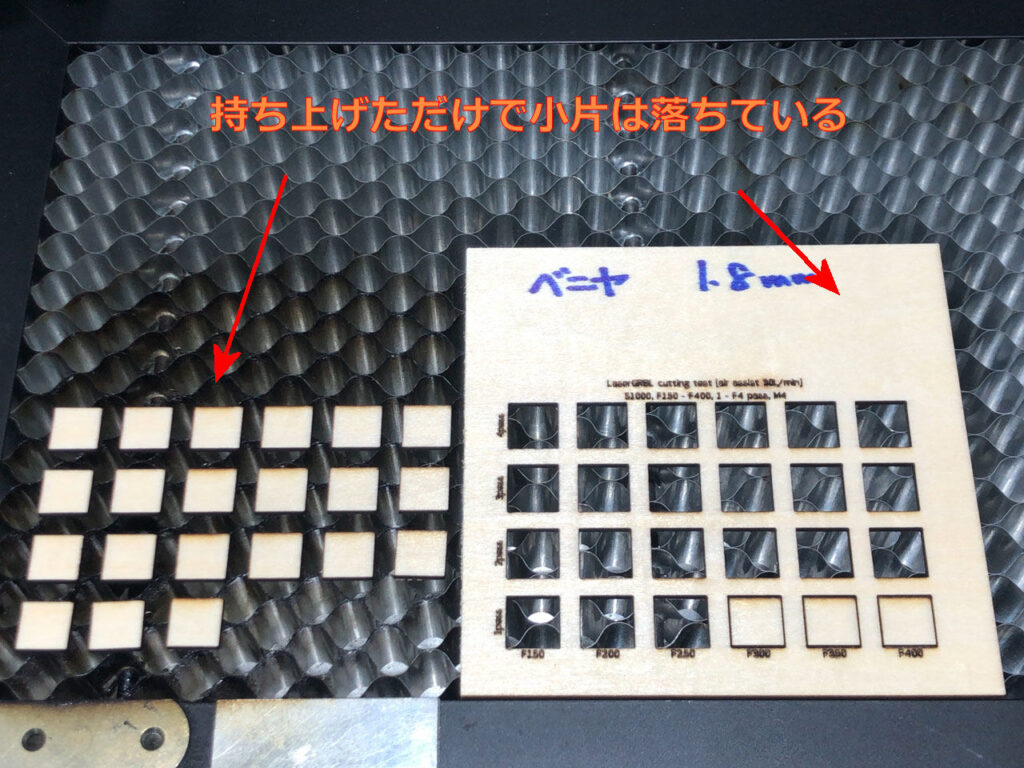
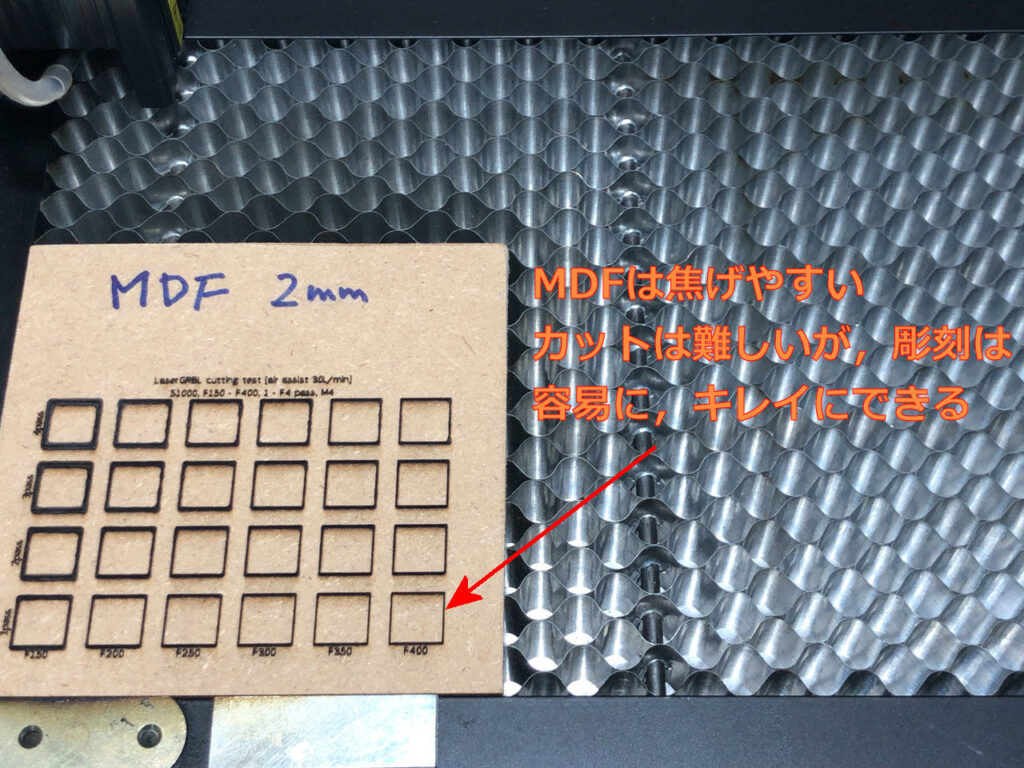
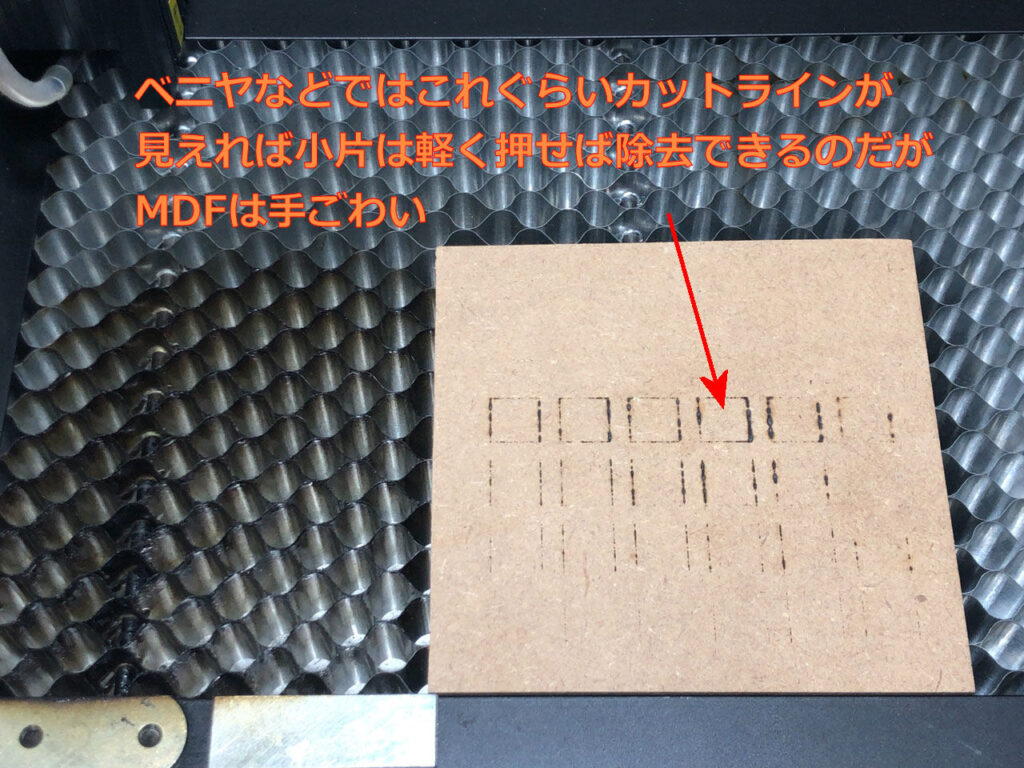
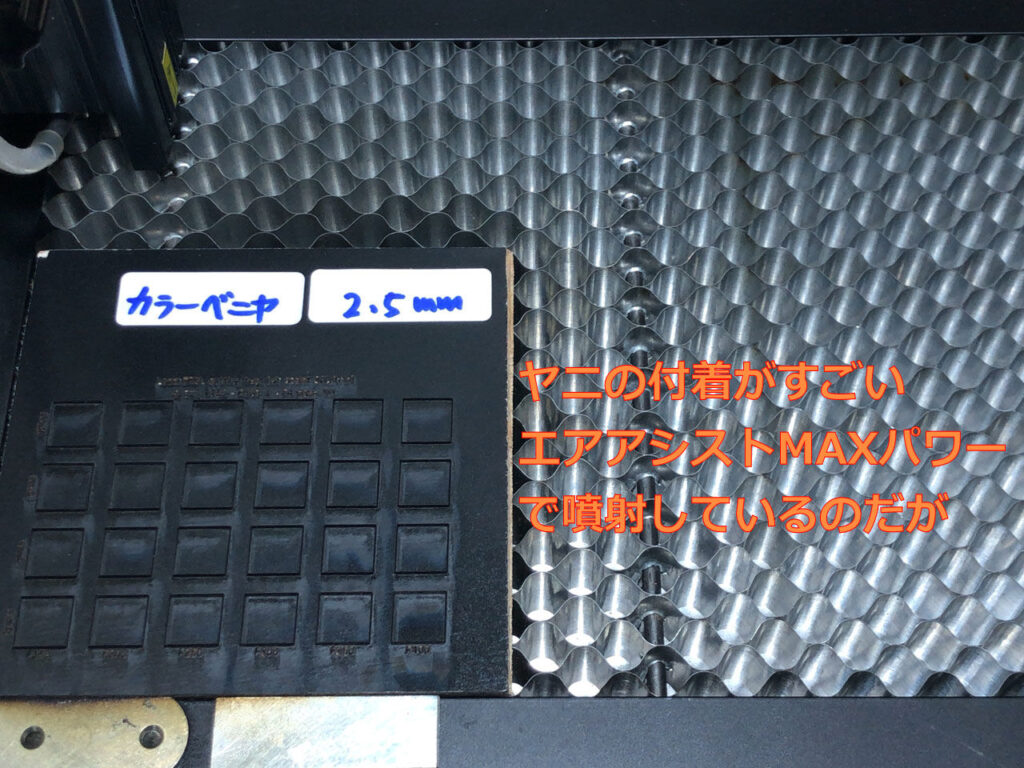
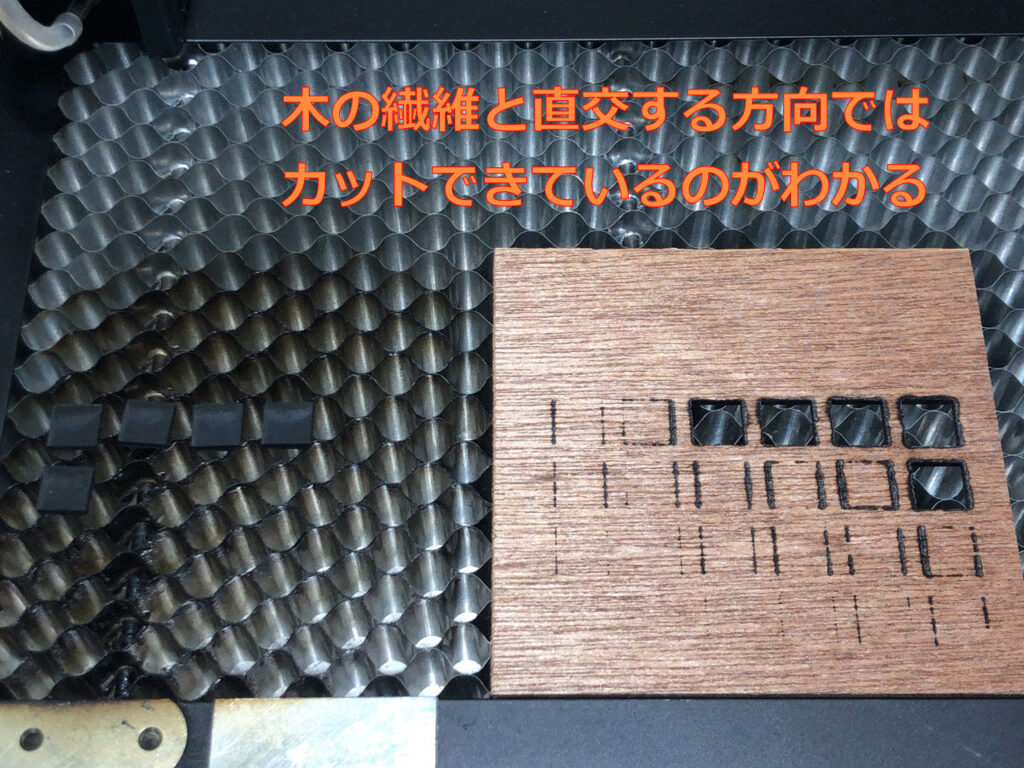
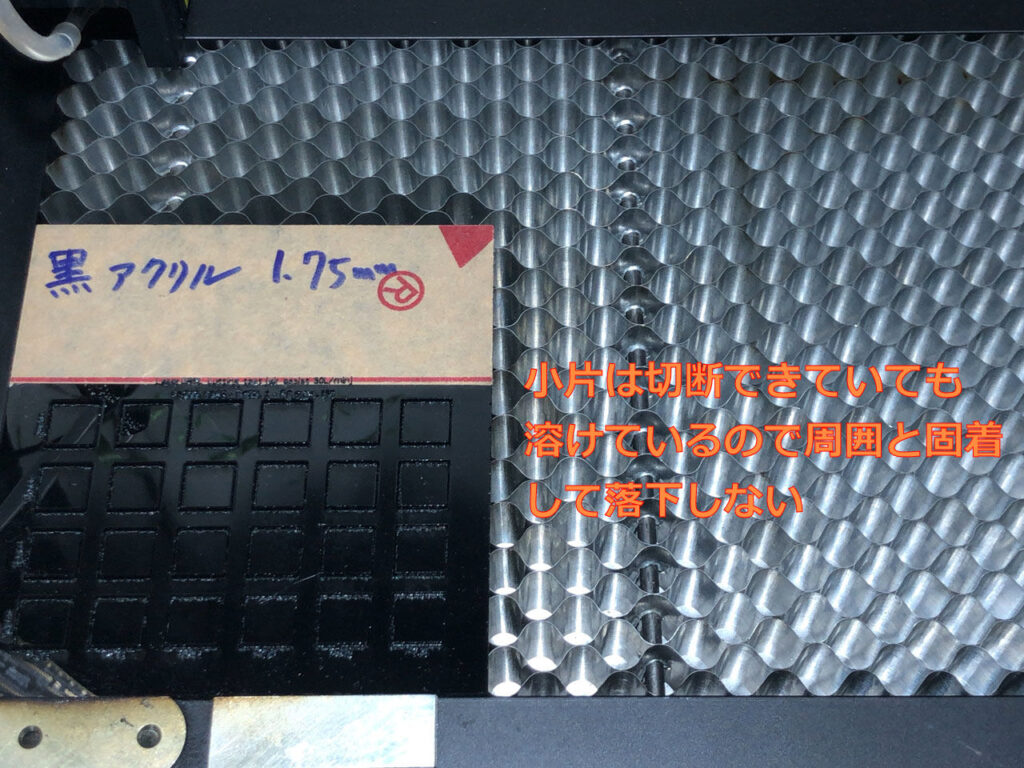

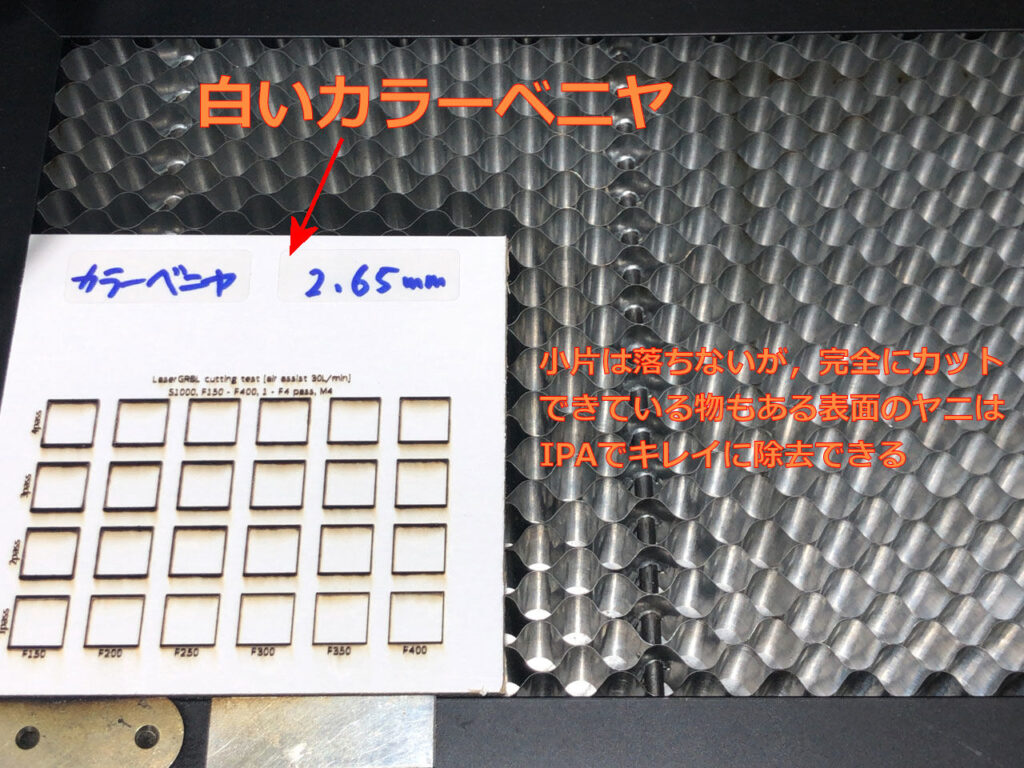
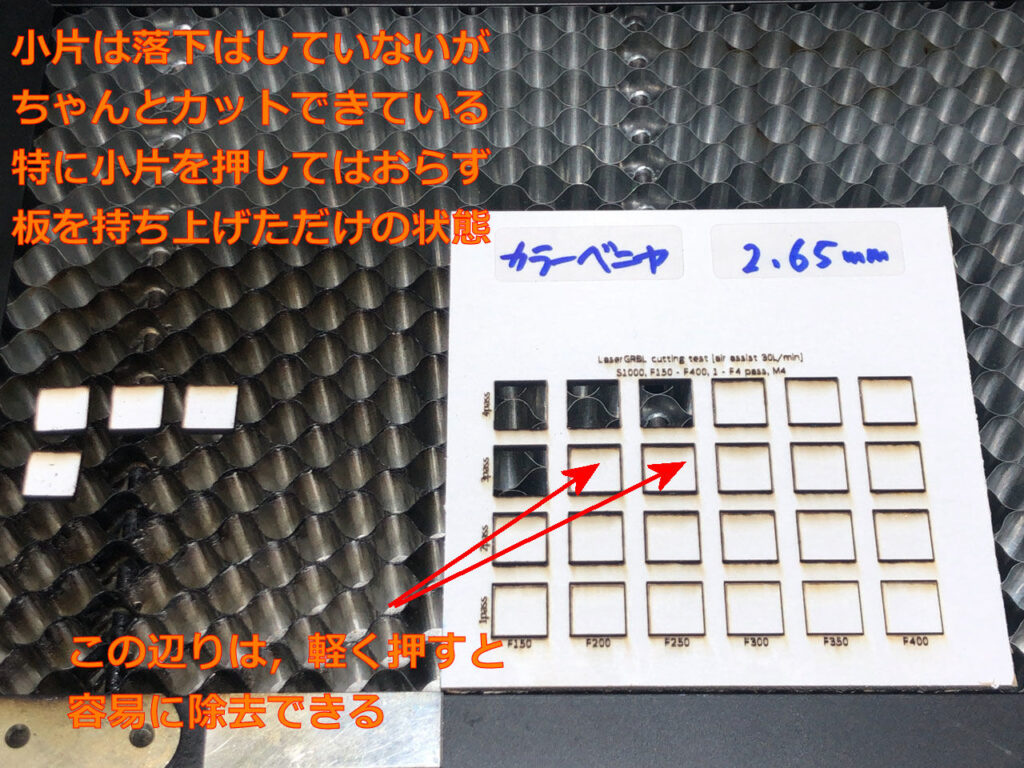
”焼け具合”を大きな画像でどうぞ
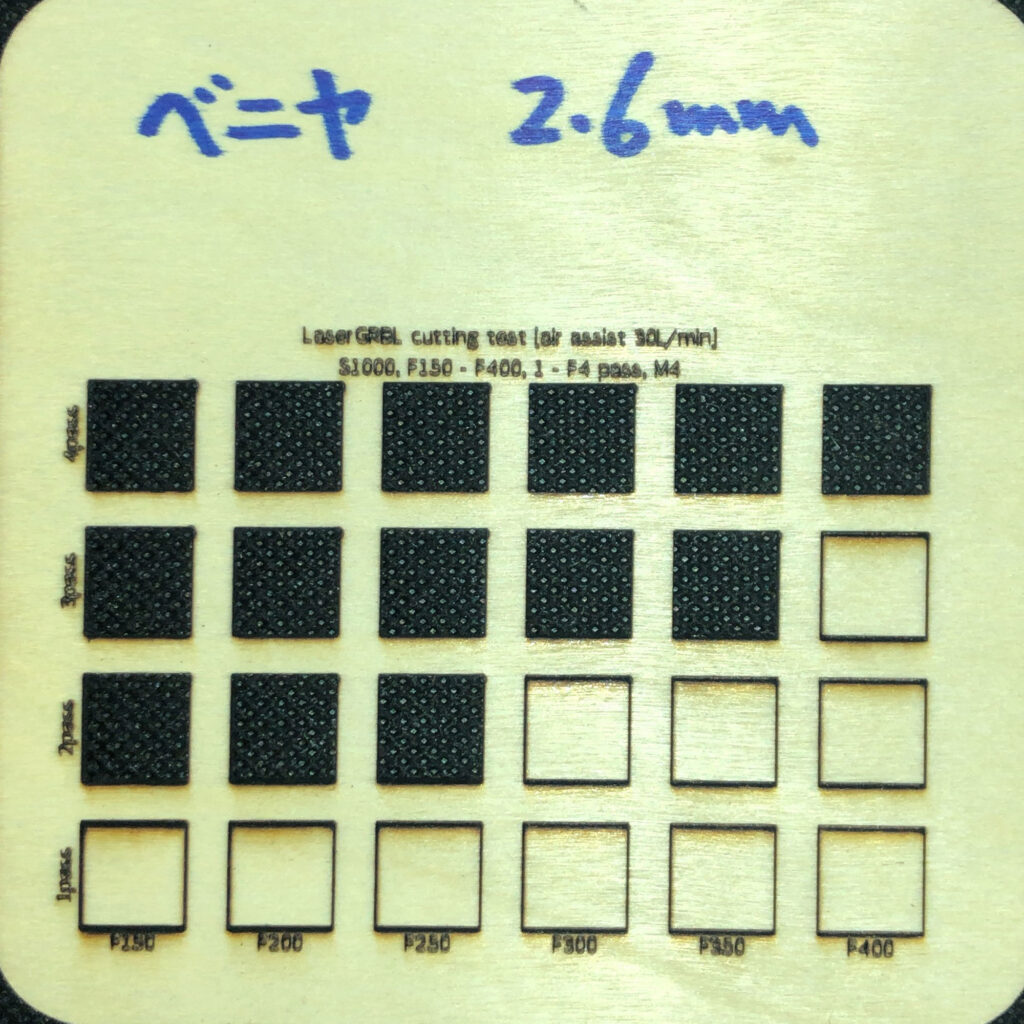
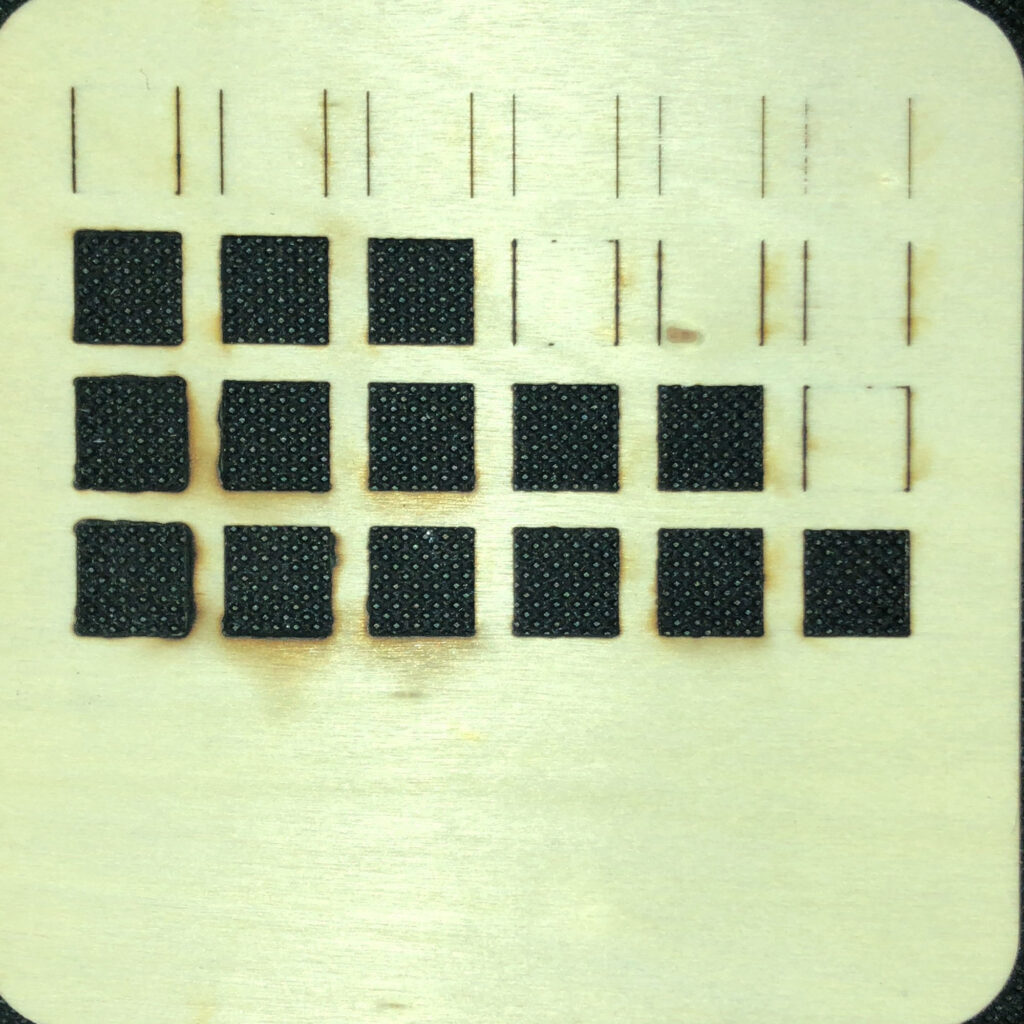
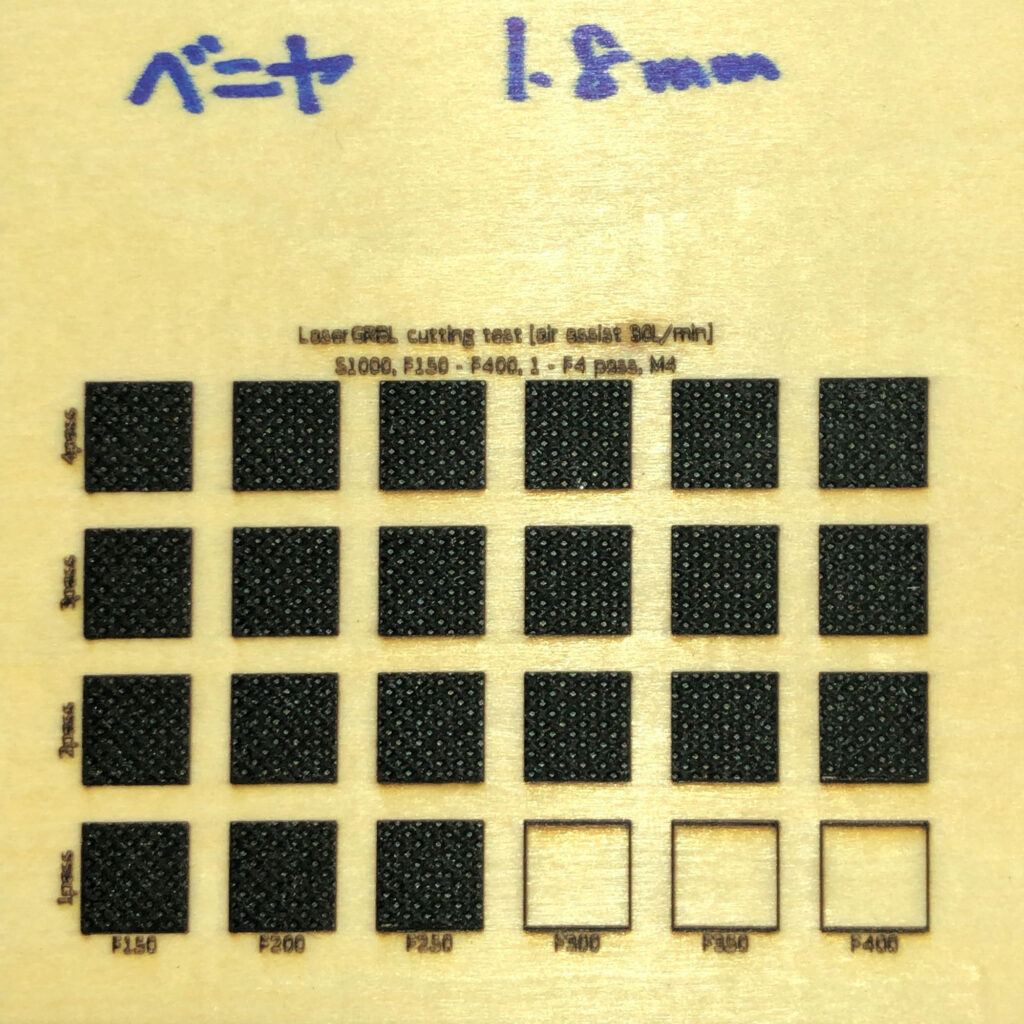
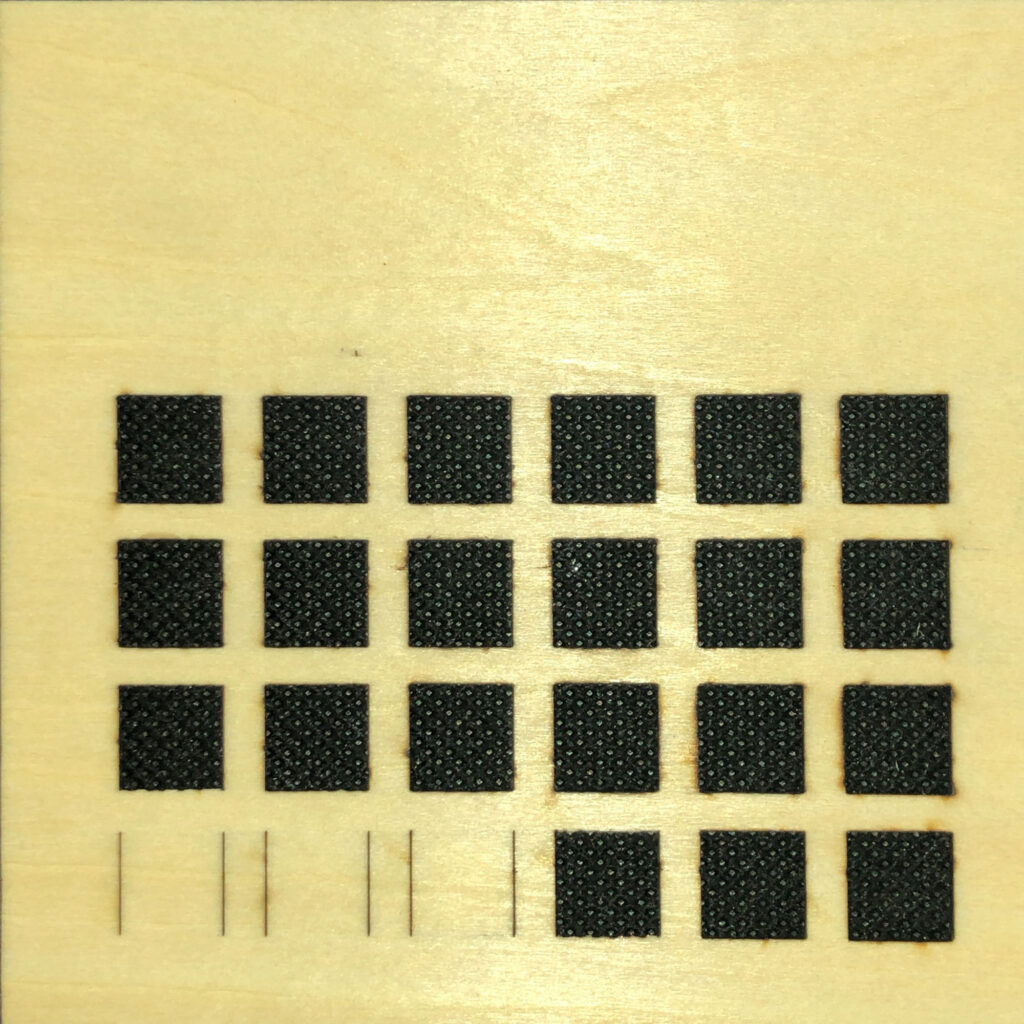
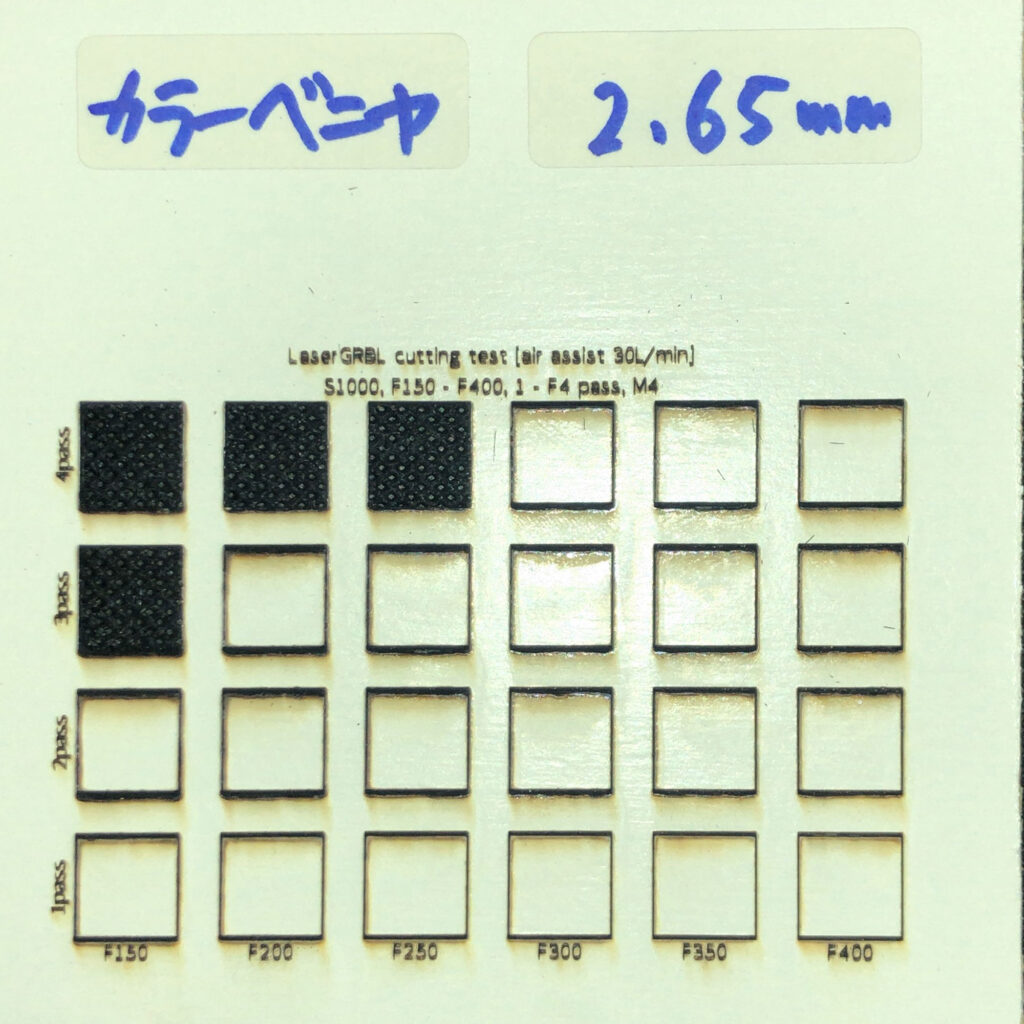
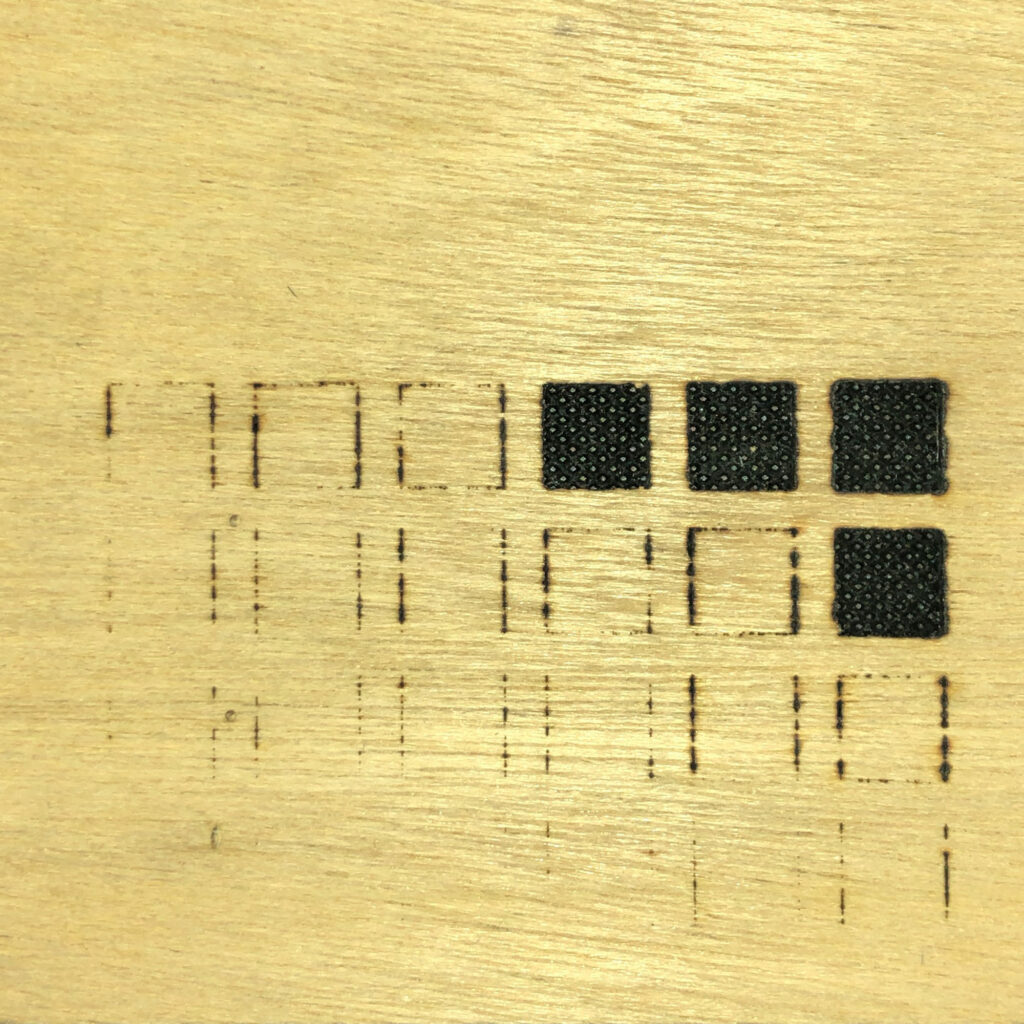
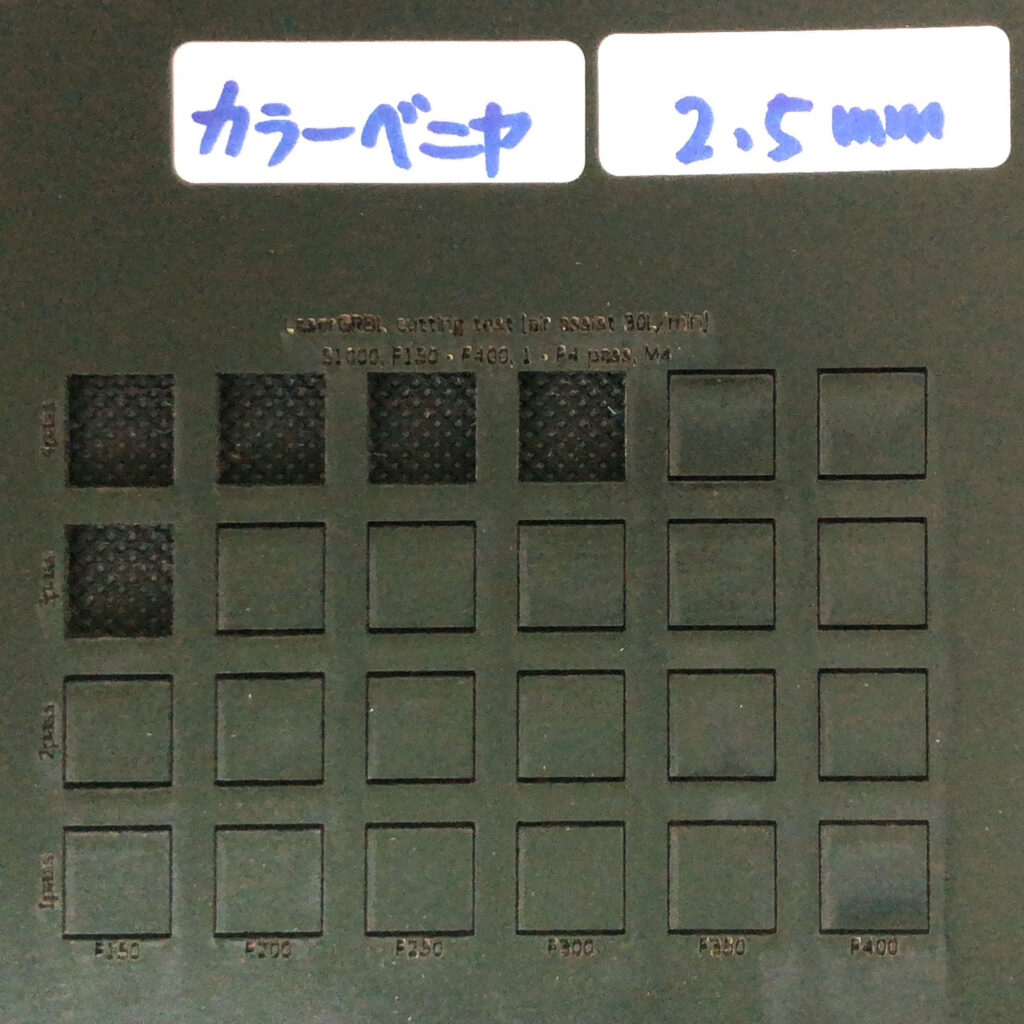

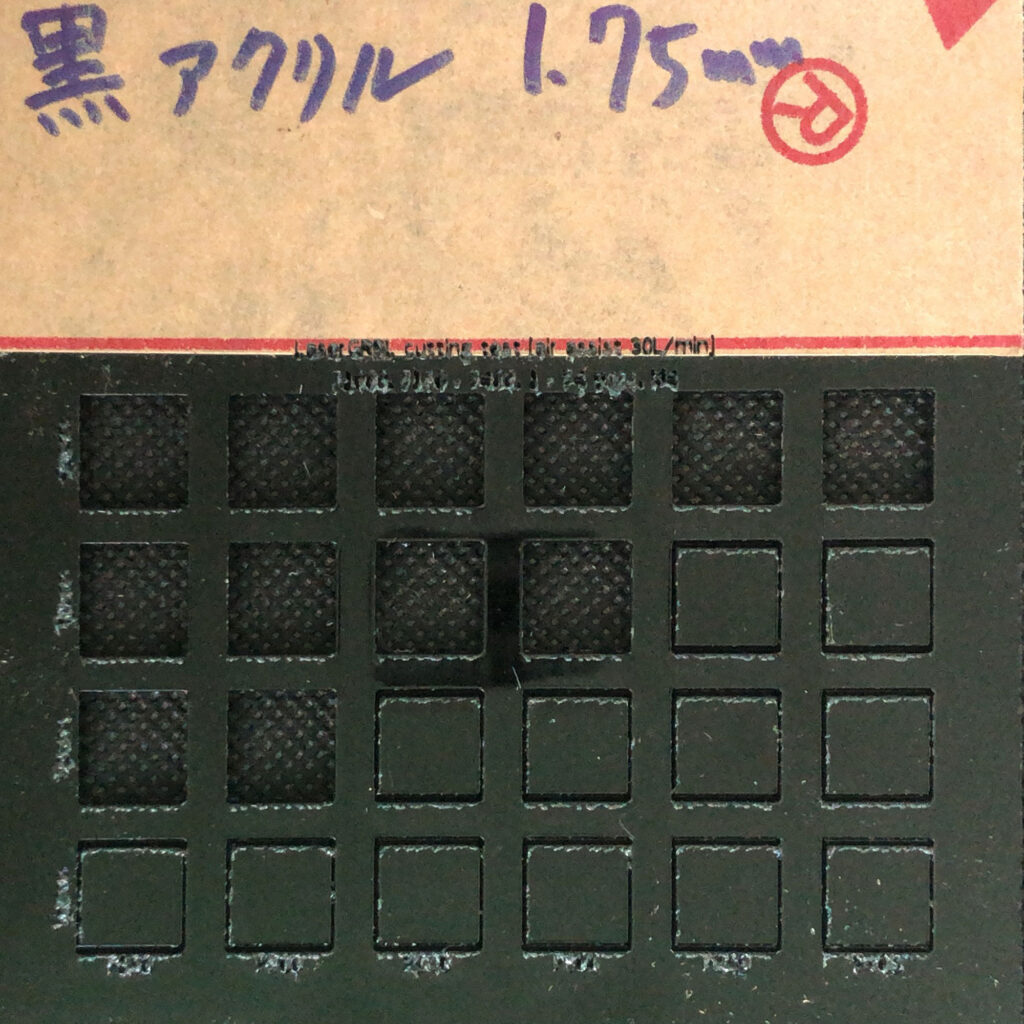
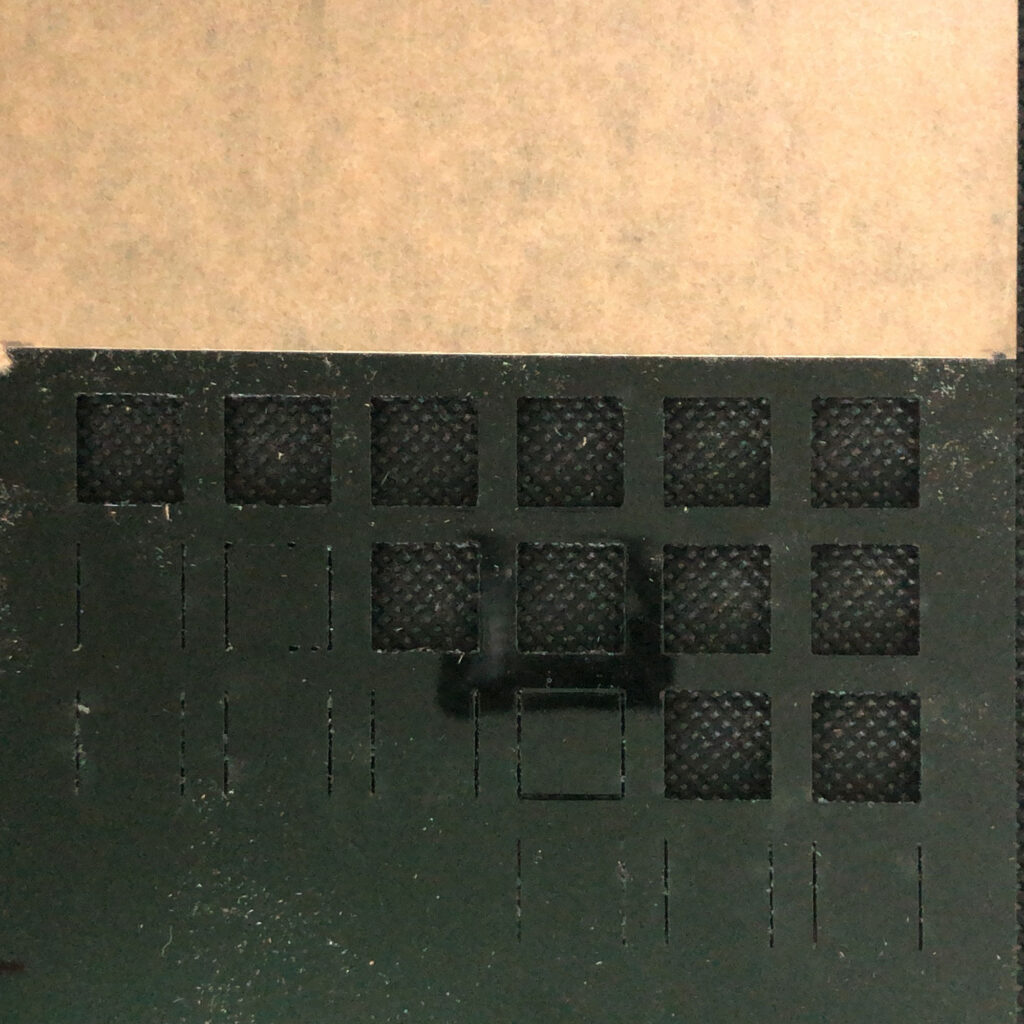
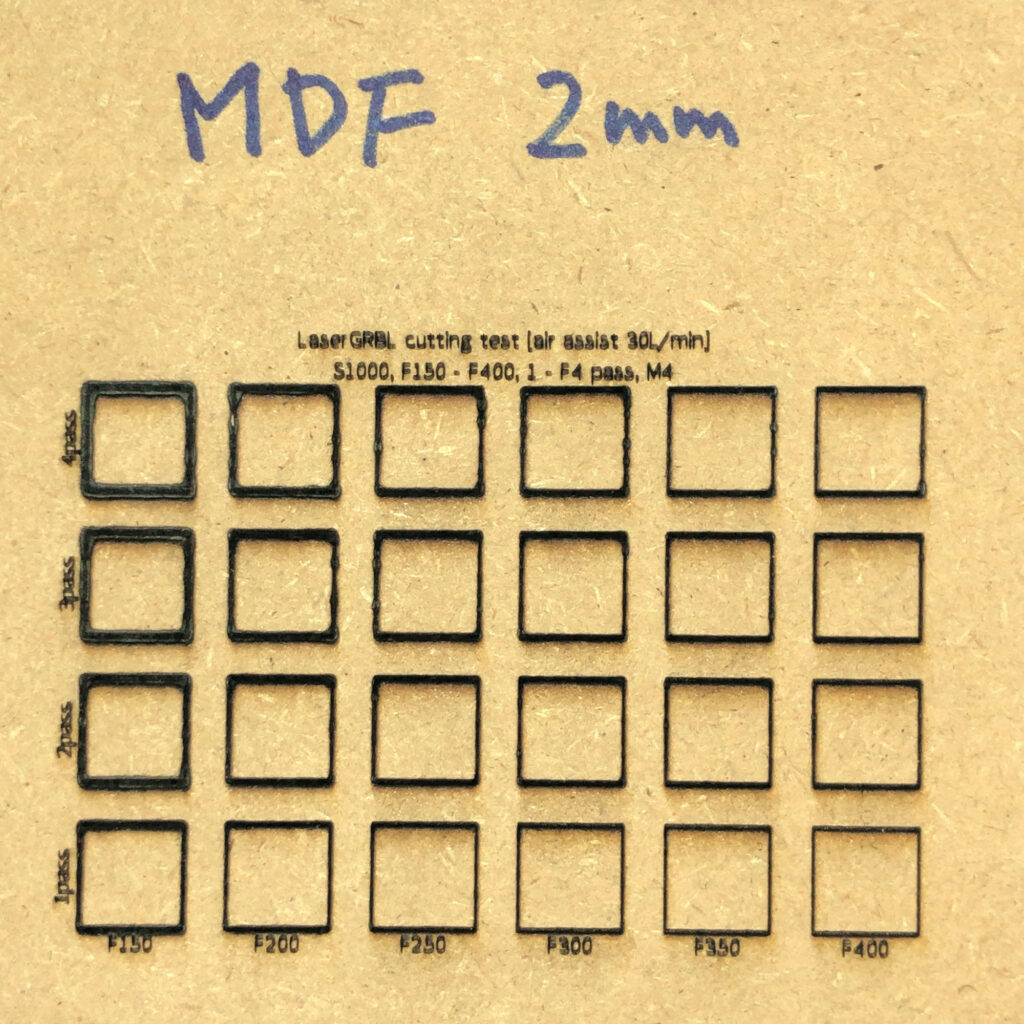
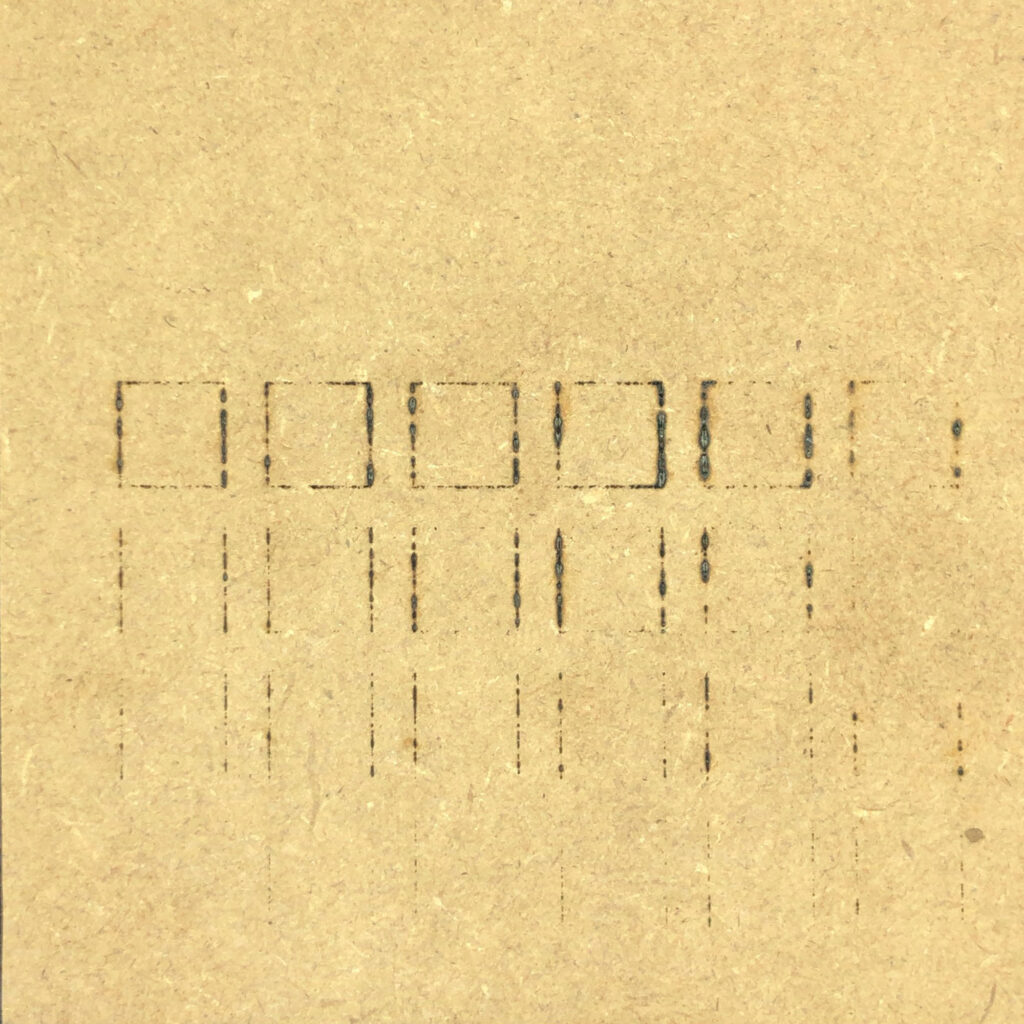
ちょっと加圧して押し出すとここまで抜ける
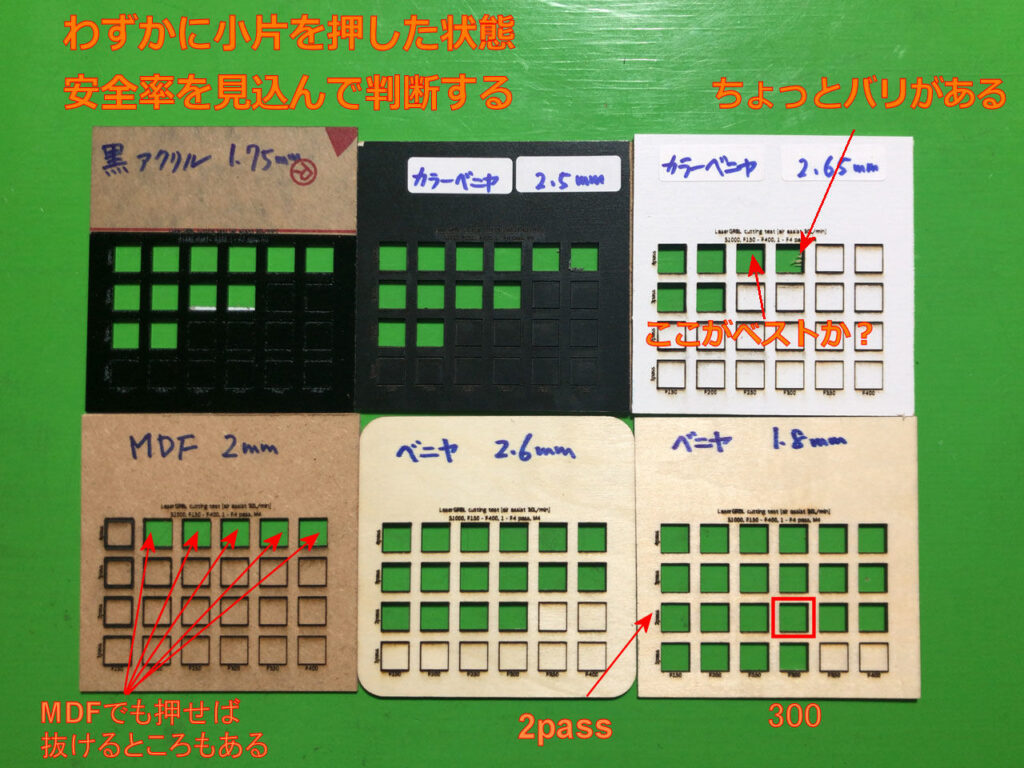
上記1.8mm ベニヤ板を PowerScaleから判断し
300mm/min. 2pass 100% で雪の結晶(SVGデータ)のカットを行ってみた
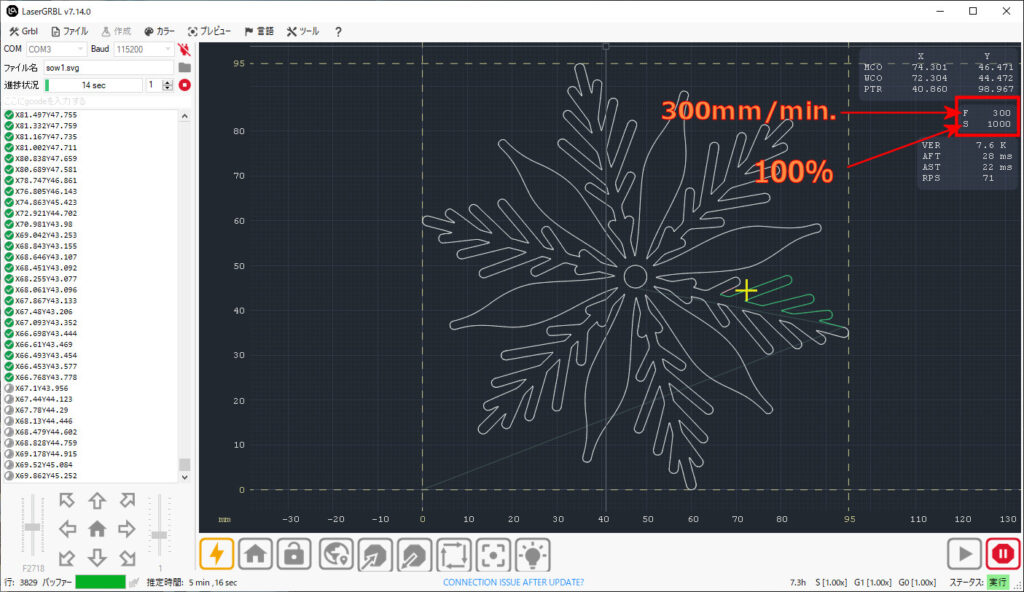
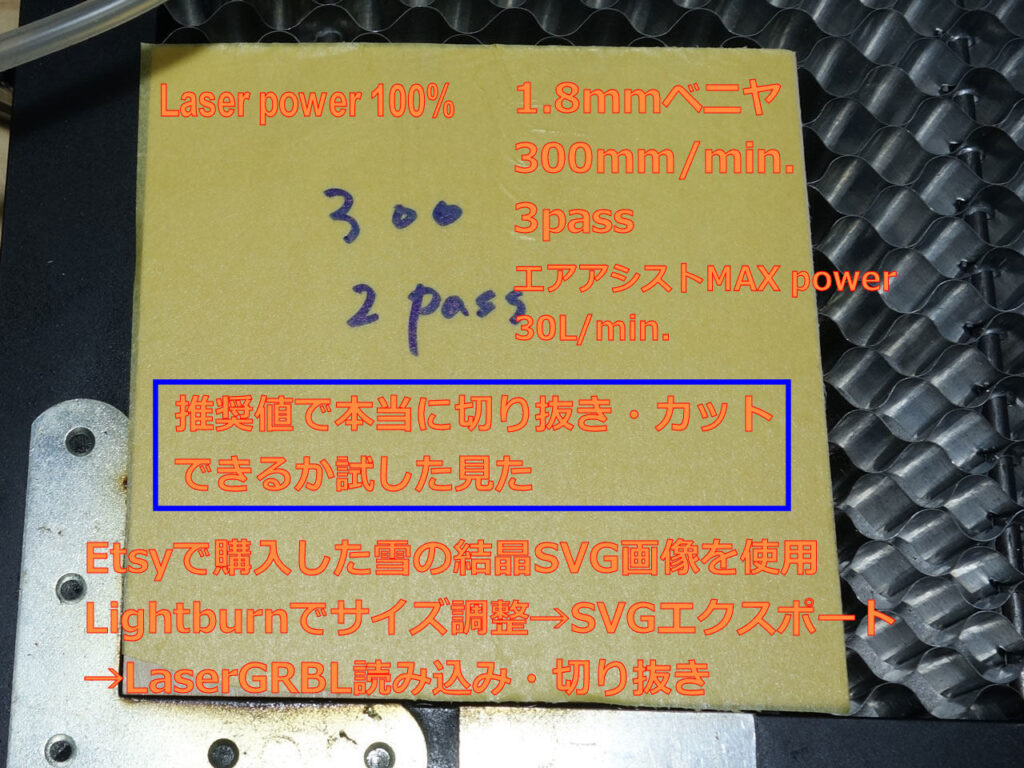
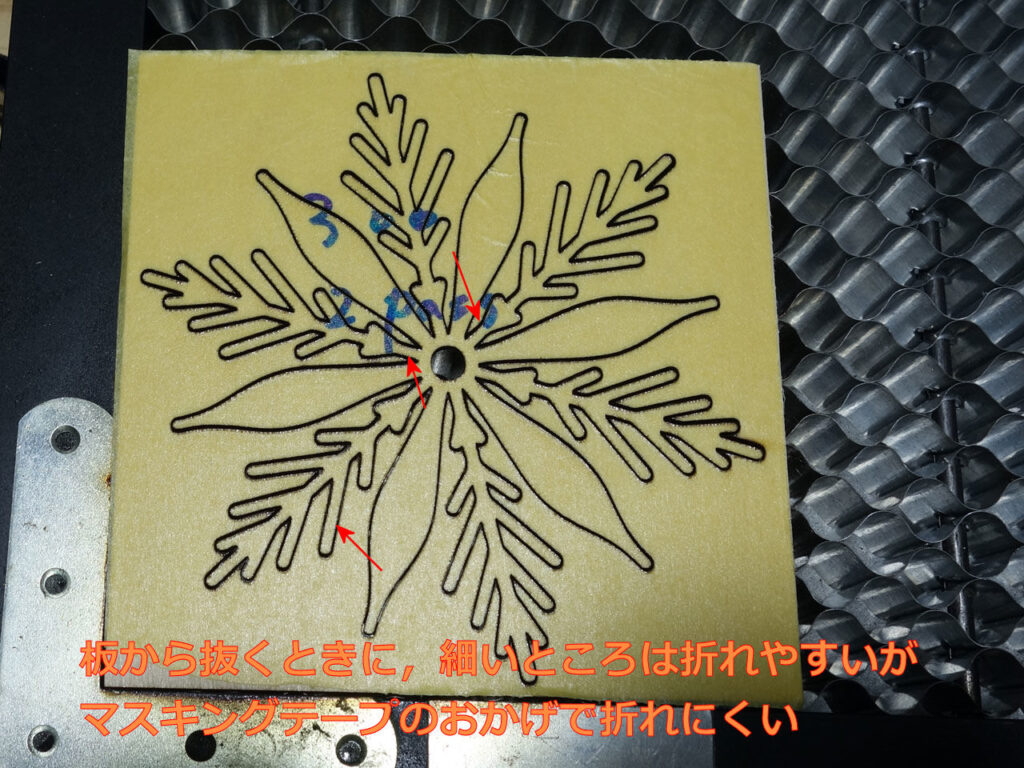
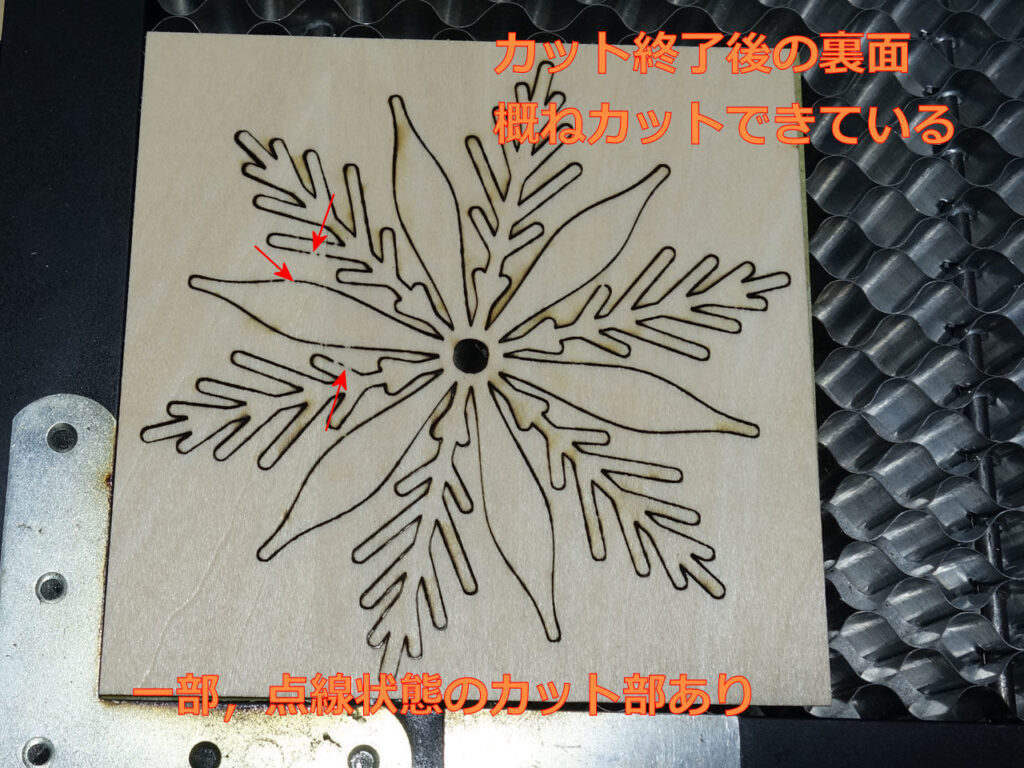
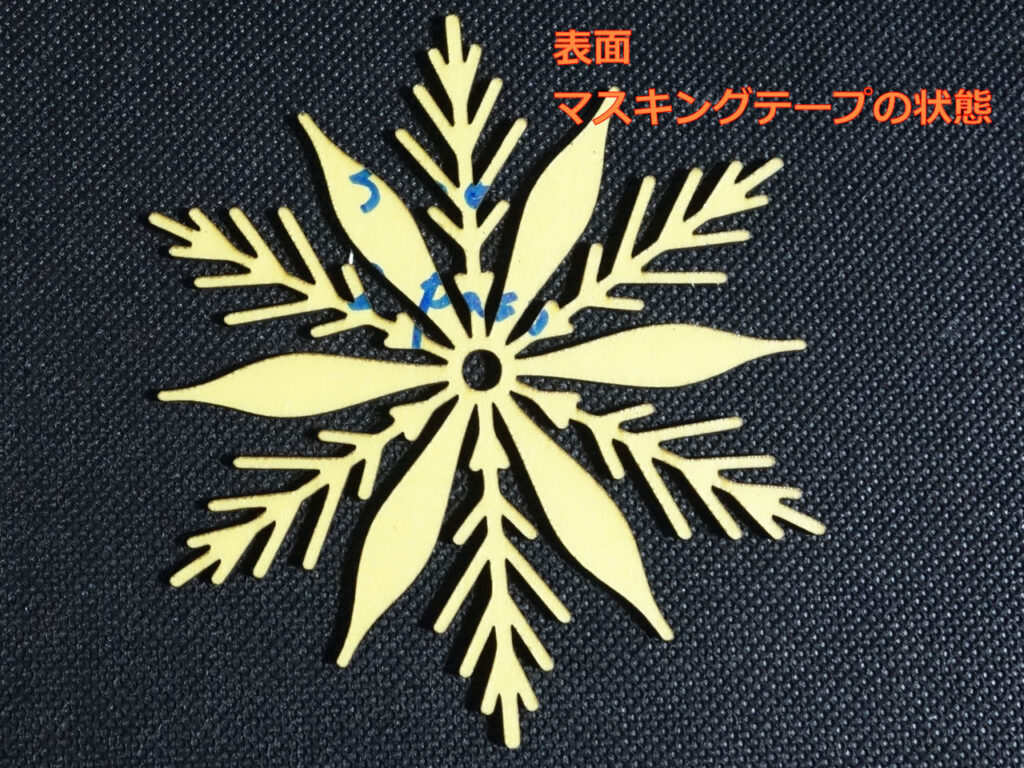
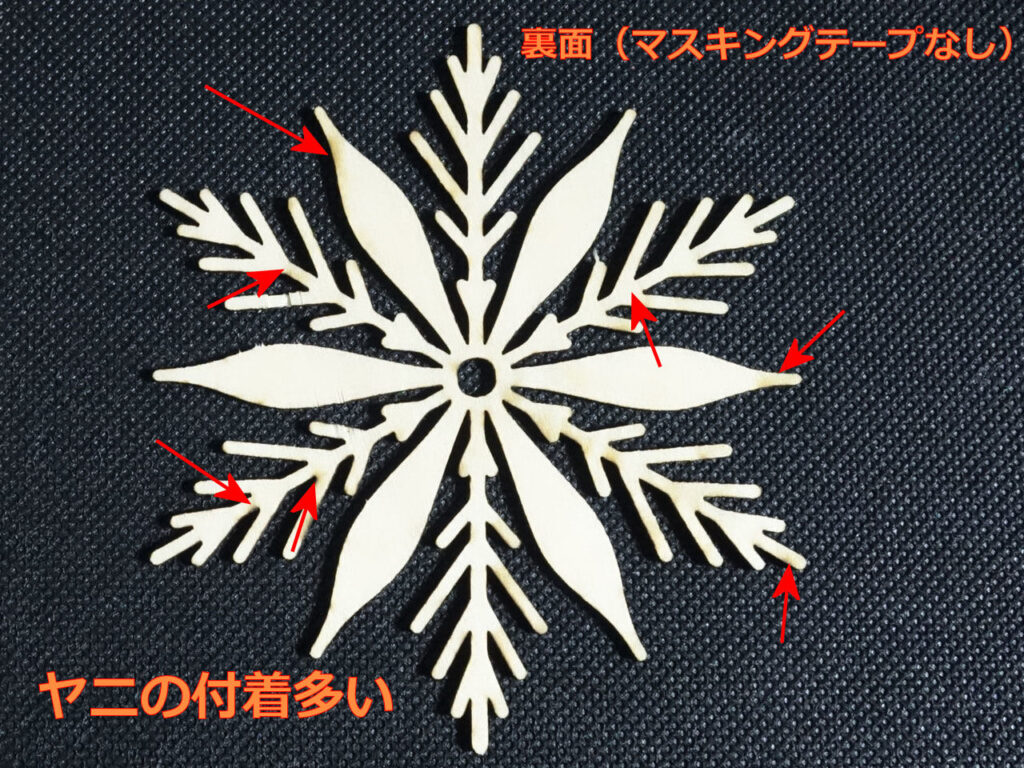
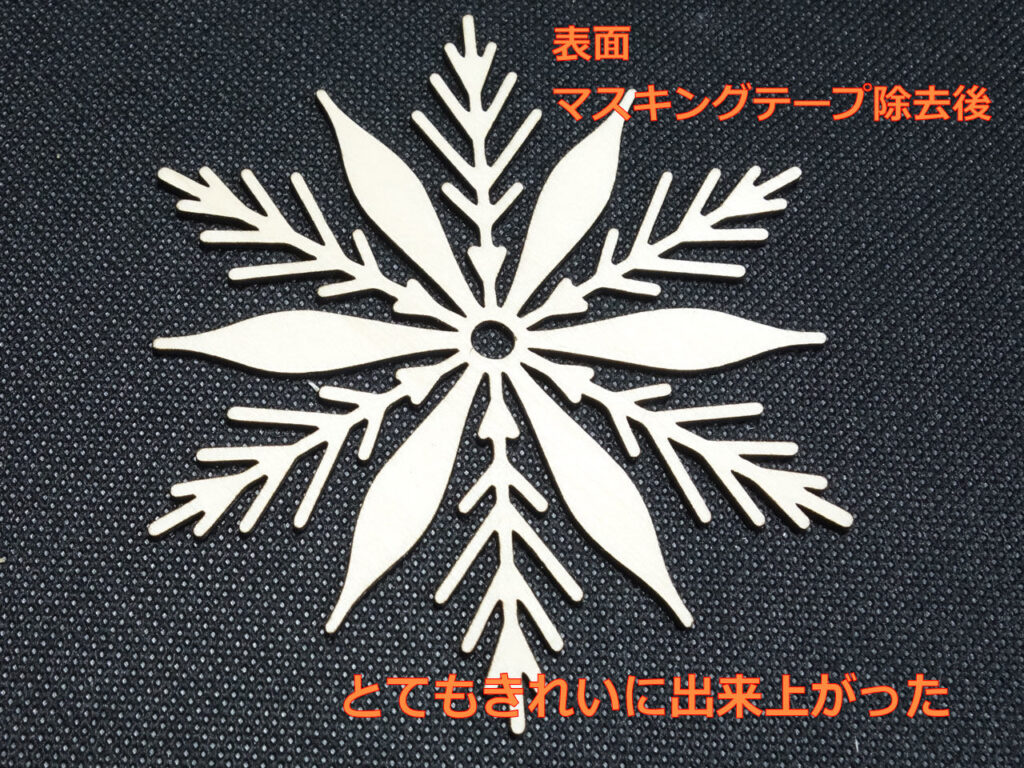
- カットができると欲が出る.カットラインは細い方がきれいであるが,パス回数が5回を越えたりスピードが150mm/min.以下だとラインは太く炭のようになってくる.ワークの材質や厚さで当然かわるが ,新しいワークでカットテストする場合,300mm/min. 3pass を目安として調整すると,少ないテストでいいパラメータが得られている
- カットする場合は当然レーザー光はワークの裏側へ貫通するので,裏面に出てきた煙があたりヤニとなって付着する.私のシステムでは裏面にもエアーを流しているのでさほど付着することはないのだが,パス数を重ねるとやはりヤニが目立ってくる.重ね合わせる場合や塗装場合の裏面なら問題ないが,そうでない場合はやはり気になってしまう.そこで一般に取られる対策がマスキングテープを裏面に貼っておくという方法がある.これは非常に有効な方法であるので私も必要時応じて貼っている.多用するのは100mmx100mmサイズであるため,幅が100mmである3Mのマスキングテープを愛用している.単純計算では両面に貼るとして,90回分となる
- もう1つの有効な方法としてエアアシストがある.これはレーザーの作用点にエアーを吹きかけて煙を飛ばし,かつ冷却を行うという方法である.その効果は絶大であることがネット情報から知ってしまった
- 上位機種には初めから実装される場合が多いようだが,P7 M30には残念ながら後付けの手段もない.こうなったら自作するしかないのである.ということで,3Dプリンターで後付けのノズルを作ってみた
- LaserGRBLできれいに,より深くカットする目的でエアアシスト機能を付加しようというプチ改造である.もちろんLightBurnでの彫刻にも有用である
- ネット情報によるとエアアシストの効果にはいくつかあるらしいことがわかった.ヤニが付きにくくするのは容易に想像できたが,カットの効率があがりより深くレーザー光がクリアに届くらしいことを知った.検証しようとも考えたが,間違いないと思い改造へと進んだ
- まずはどんなもんだかYouTubeの実例を見てみた.大出力のレーザーモジュールに初めから装備されているものが多かったのだが参考になった.勿論その効果に否定的なものはない
- 排煙問題.私の環境はある程度の排煙は結構なレベルで行えているのだが,エアーの勢いによっては部屋の中に拡散していくことが予想された.しかしそこは空気清浄機に任せることにした(運用後にわかったことだが,やはりボックス状に閉鎖されたものでないと臭いは出てしまう.煙がもくもくということではない)
- あと,考慮すべきはポンプをどうするかである.ATOMSTACKから30L/min(MAX)のエアアシストポンプが販売されているのだが如何せんお高い.1万円以下で吐出量が30L/minレベルのものはAmazonでは数少ない.しばらくまよってほしい物リストに入れておいたのだが,なんとブラックフライデーで¥6400(税込み)にプライスダウンしているのに気づいた.とはいえ,まあまあお高い
- 同じATOMSTACKであるが,ややお安いポンプもある.と言ってもお高いのだが.こちらがそのポンプであるが,商品写真に2種類のノズルが確認できる.P7 M30のレンズ保護カバーとい同じ形態にエアーを供給する部分がついている.しかしこれらのノズルがP7 M30で使用できるかは不明である
- 熱帯魚用のエアポンプで何とかならないかと思った.4年ぐらい前に,プリント基板エッチング槽を作ったときに現像液撹拌用のエアーポンプに使うために,熱帯魚用のエアーポンプを購入してあった.これの流用を考えたのだが,調べてみると最大吐出量は5L/min と無理そうであったので断念した.同じことを考える方もおられると思うが,断念をおすすめする.実際使ってみると吐出量の差は歴然である
- 将来,上位機種を買った時に絶対役に立つとも考え,ブラックフライデーが終わらないうちにとポチッた次第である.そのエアアシストポンプはこれである.ファスナー付きのハードケースが付属しているのだが,一切のマニュアルがなかった.まあ,使用方法は想像できるなので問題はないのだが.それから特定機種で使用するであろう謎のパーツも同梱されている.で,結論として買って大正解であった.耐久性は今のところ当然不明だが,吐出量はもちろん,細部の作りや振動,思ったより静かなどコストパフォーマンス大である.振動・騒音対策で底面についているインシュレータはかなりぐにゃぐにゃするが,効果は高い
- 付属品は特定のレーザーモジュールへの接続用と思われる謎の?バーツがあった.細いチューブはポリウレタンのため固くて取り回しが難しい.大きなレーザー彫刻機ならいいのかもしれない.耐圧が120PSI(約0.82MP)と高めなのでチューブの肉厚がある.そのためP7 M30のレーザーモジュールに取り付けて取り回すには,ちょっと酷かもしれない.代替としてフレキシブルな肉厚1mmのシリコンチューブを選んだ.使ってみて取り回しはとてもいいのだが,ポンプ背面から手前に持ってくる際に知らないうちに折れ曲がって,エアーが流れなくなっていたことがあった.ポンプを動かしたら要チェックである
- 最大の問題&お楽しみは,ノズルをどうするかの問題である.エアーアシストポンプから供給されるエアーを,レーザーの作用点(ワークが焼かれている点)にいかに効率的,効果的に吹き付けることができるかということである.最初のプランAは,保続しているレンズ保護カバー?に被せる形状にデザインした.しかし,アルミパイプと取り付ける位置に問題があり断念した
- 次のプランBは,レーザーモジュールのパノラマガラスを取り外し(といっても初めから外してある.そうしないとレーザーの照射位置が見づらい.もちろん,防護メガネ装着で見ている)そこに内径3mmのアルミパイプを3Dプリンターで作製したアダプターを用いて取り付ける案を試作した.この方法はお手軽であったが,エアーのあたる位置をコントロールするのが難しかった.エアーがどこにあたっているを確認できないのである
- そこで,レーザーモジュール内のレンズ保護カバー(名称不明)を取り外して,代わりのものを3Dプリンターで作製し,そこにエアー吐出口を取り付けた構造のものを製作した.これをオリジナルの取り付けネジで取り付ける.
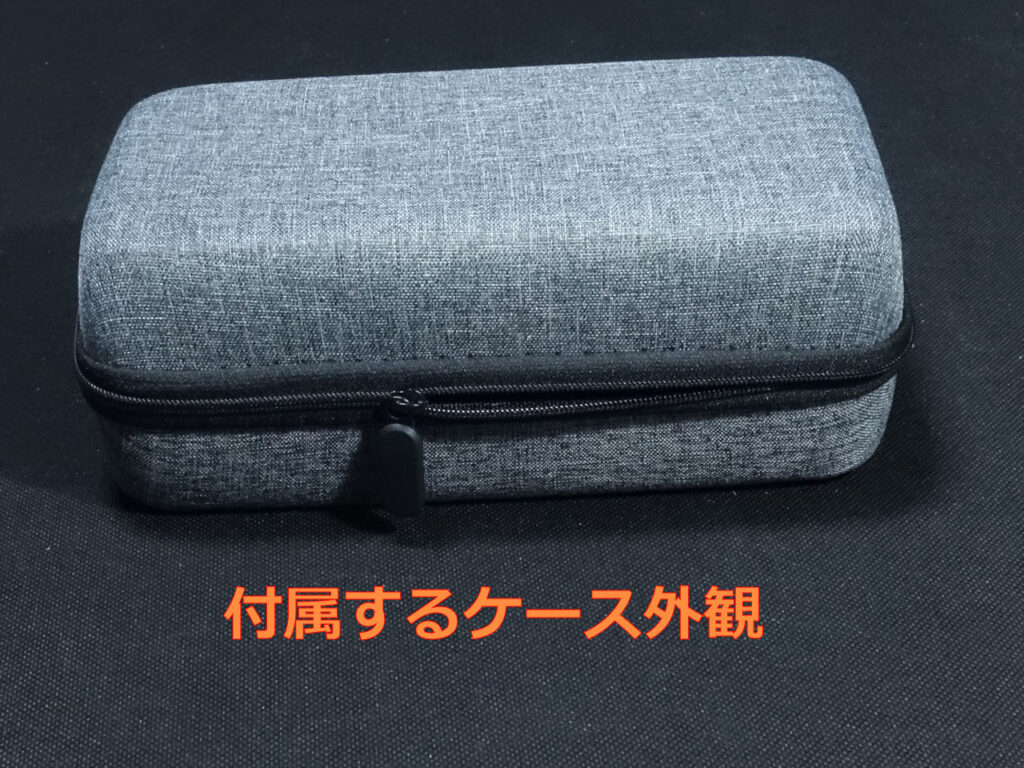
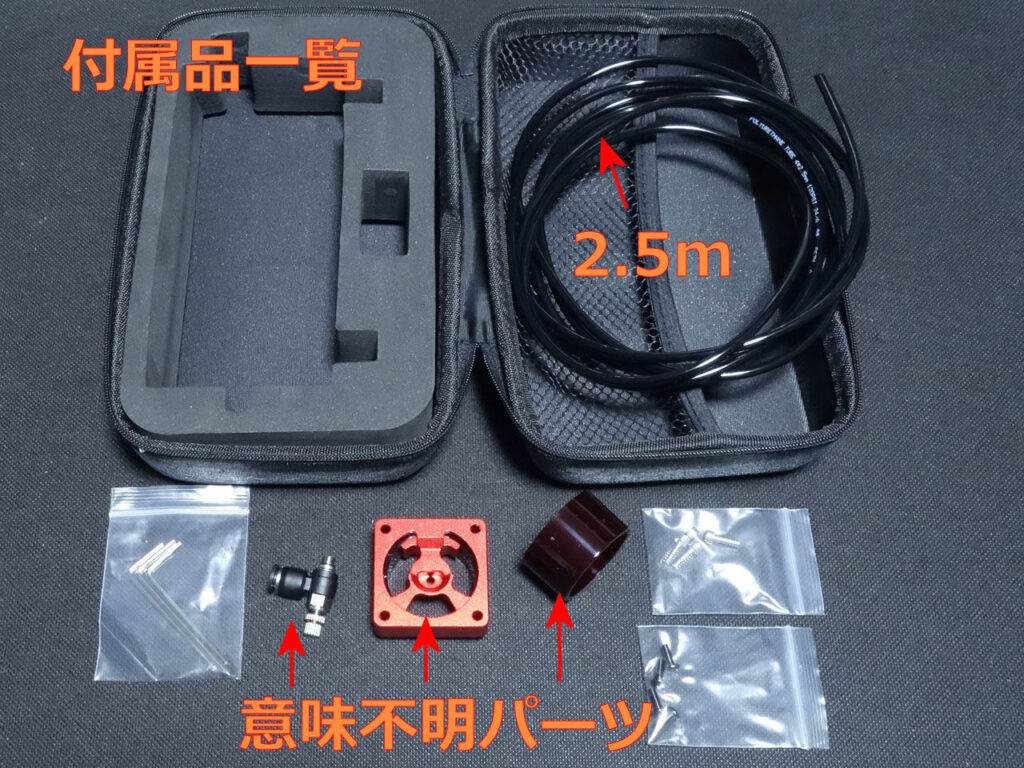
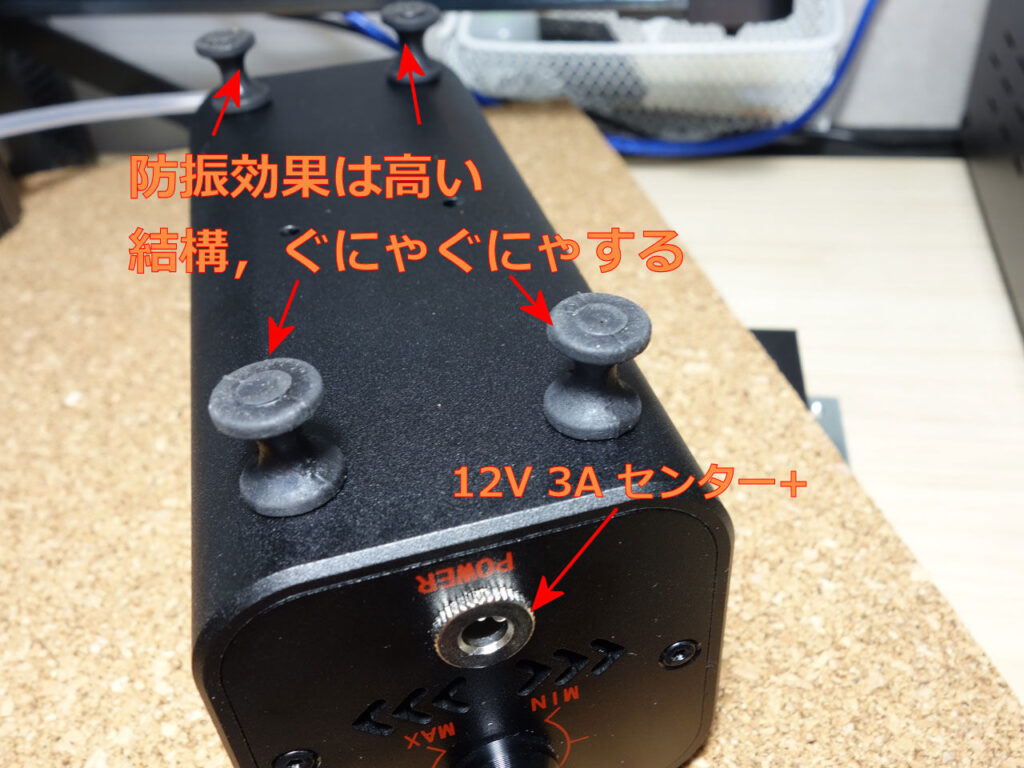
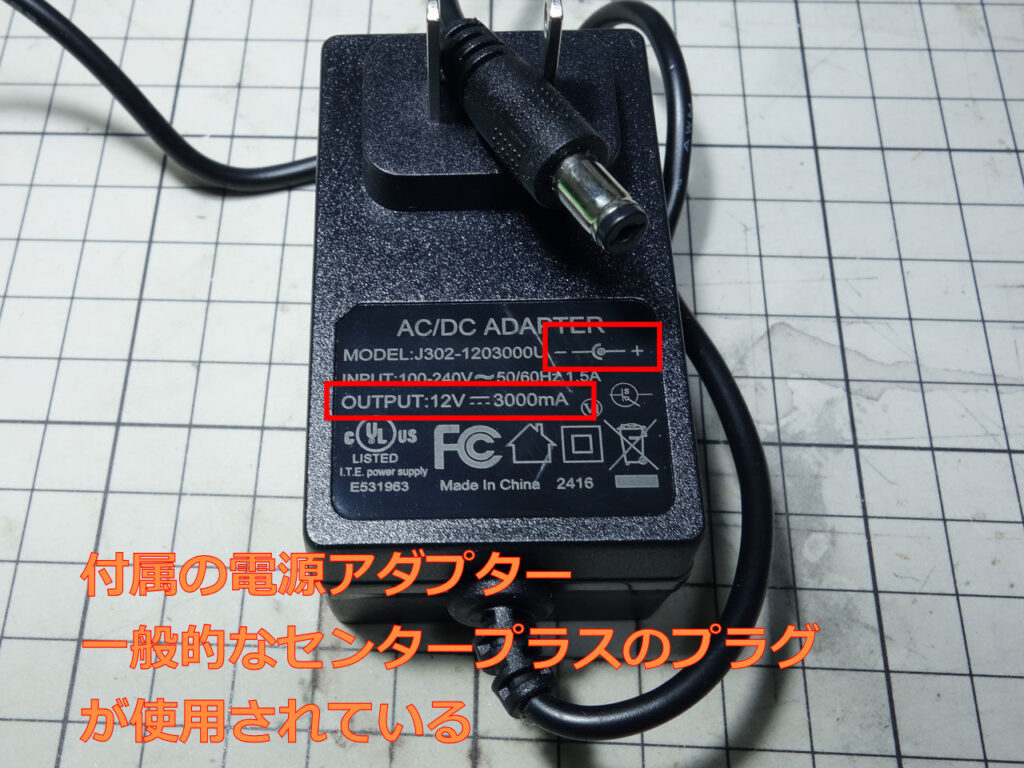
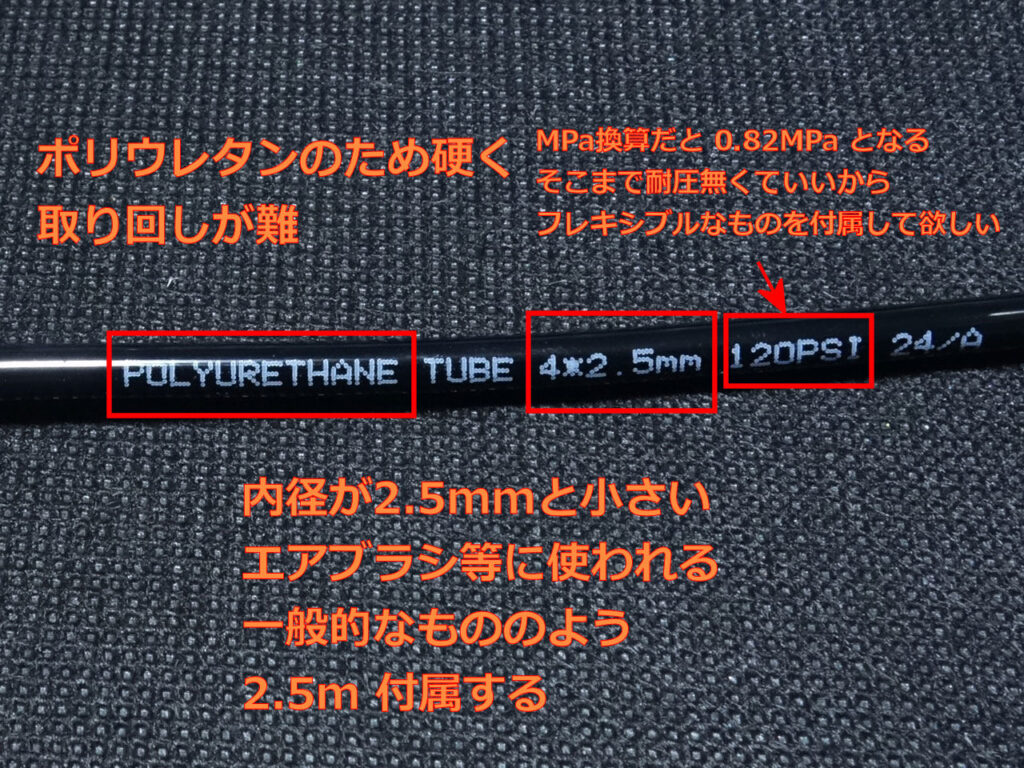

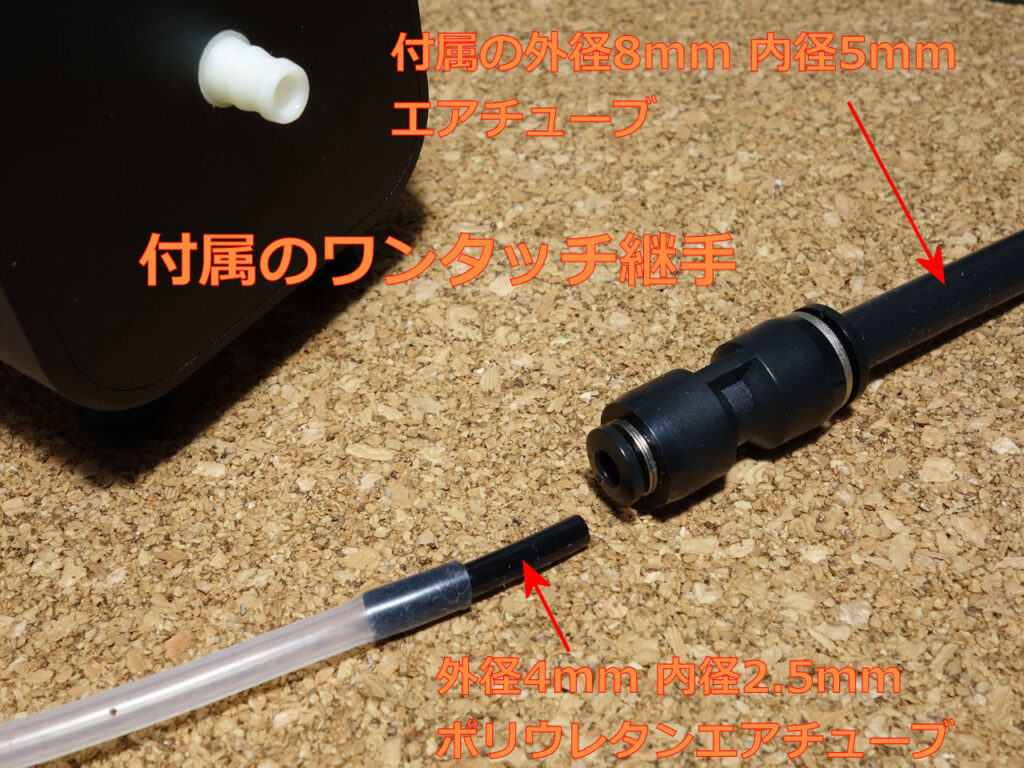
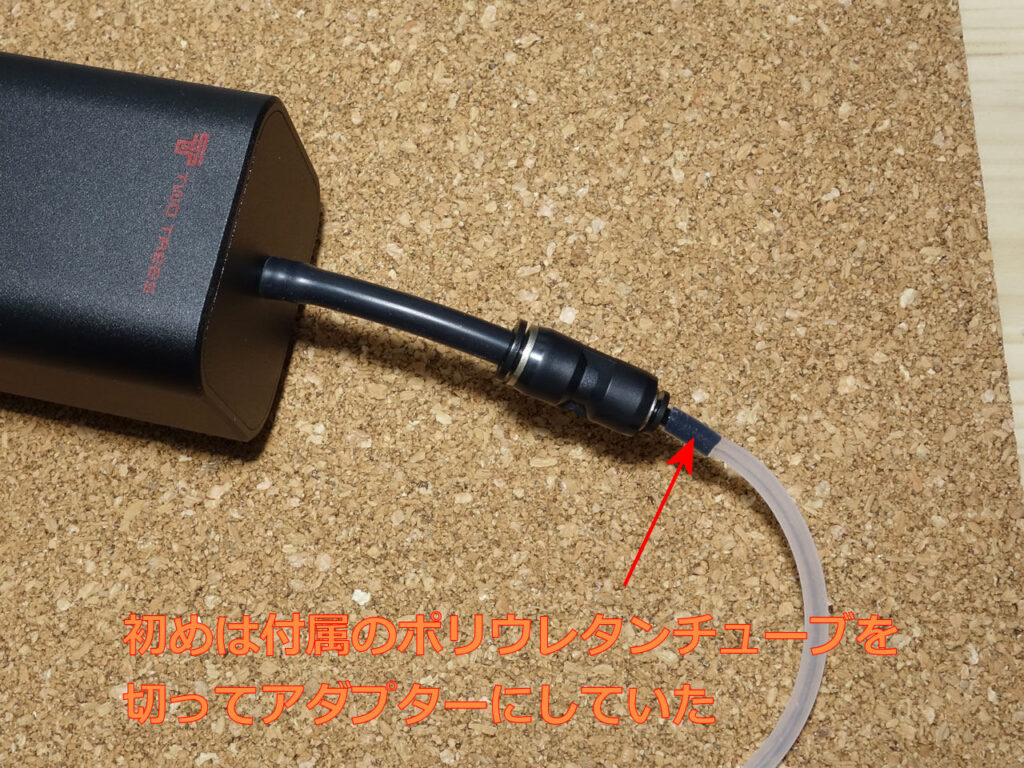
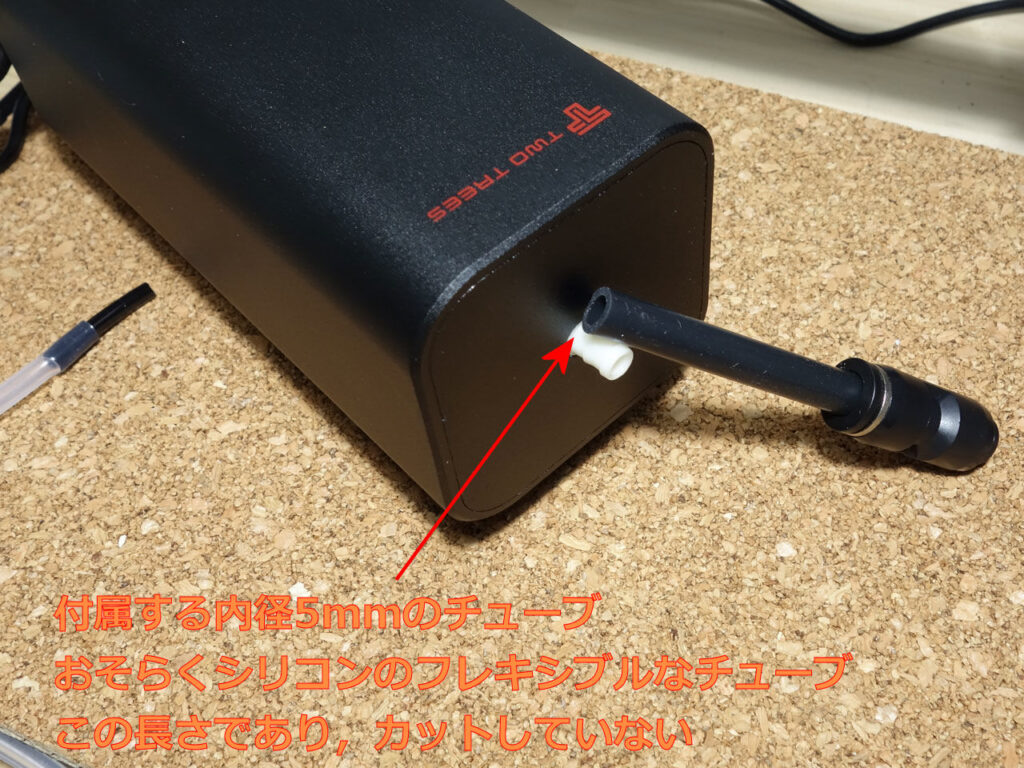
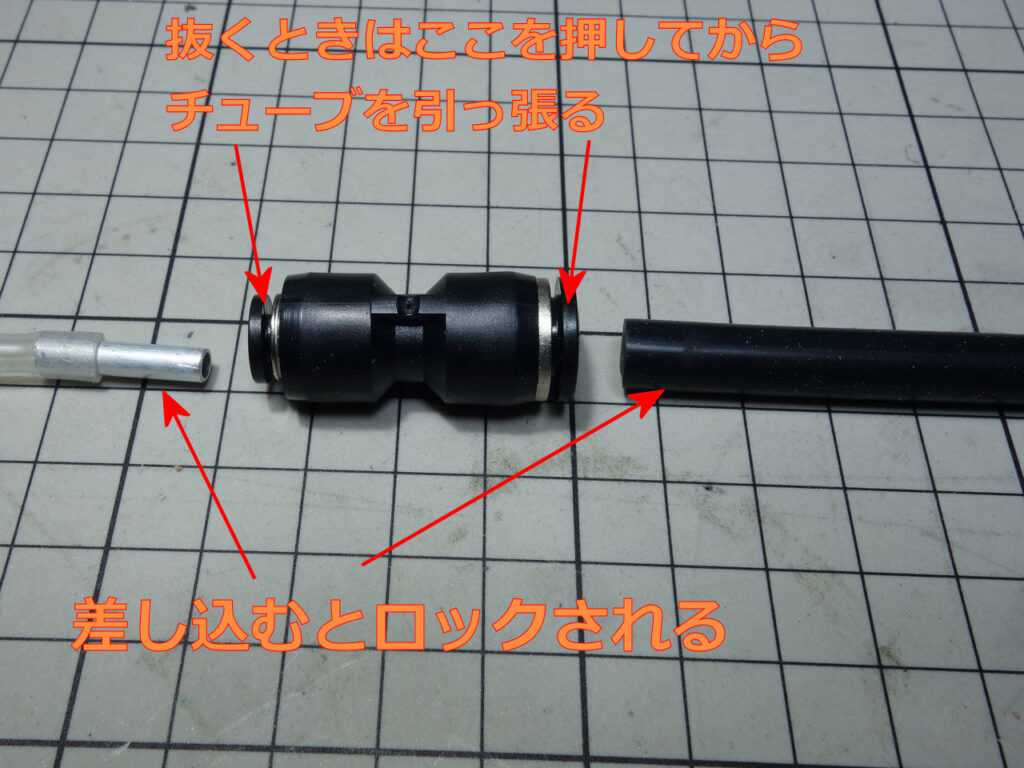
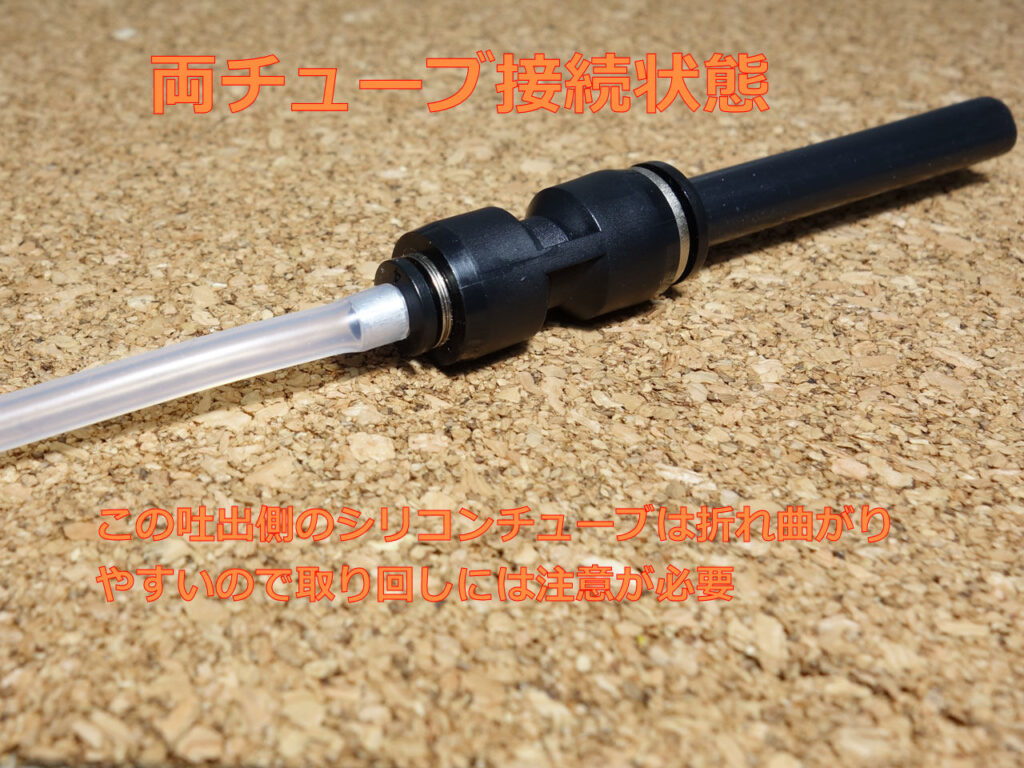
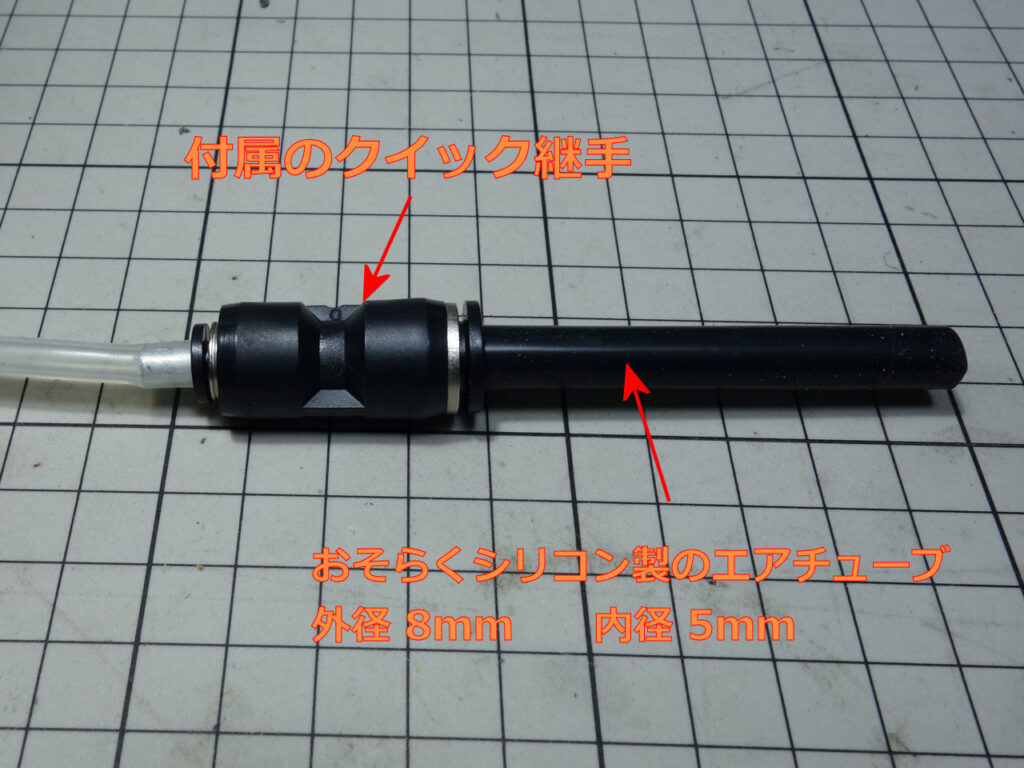
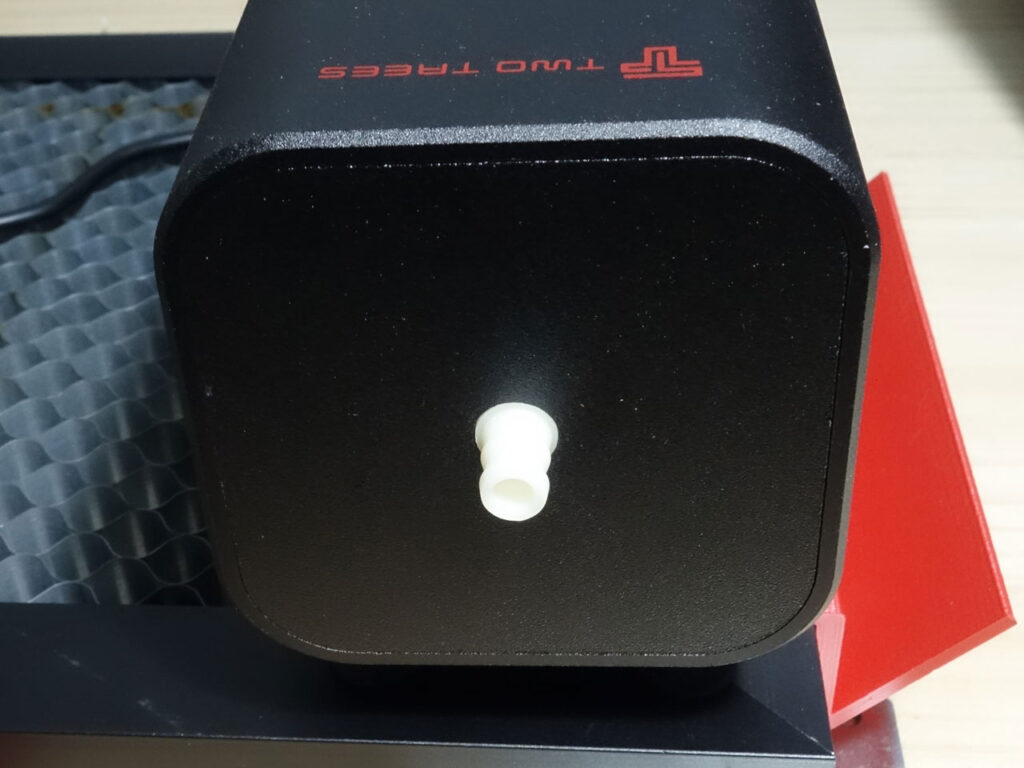
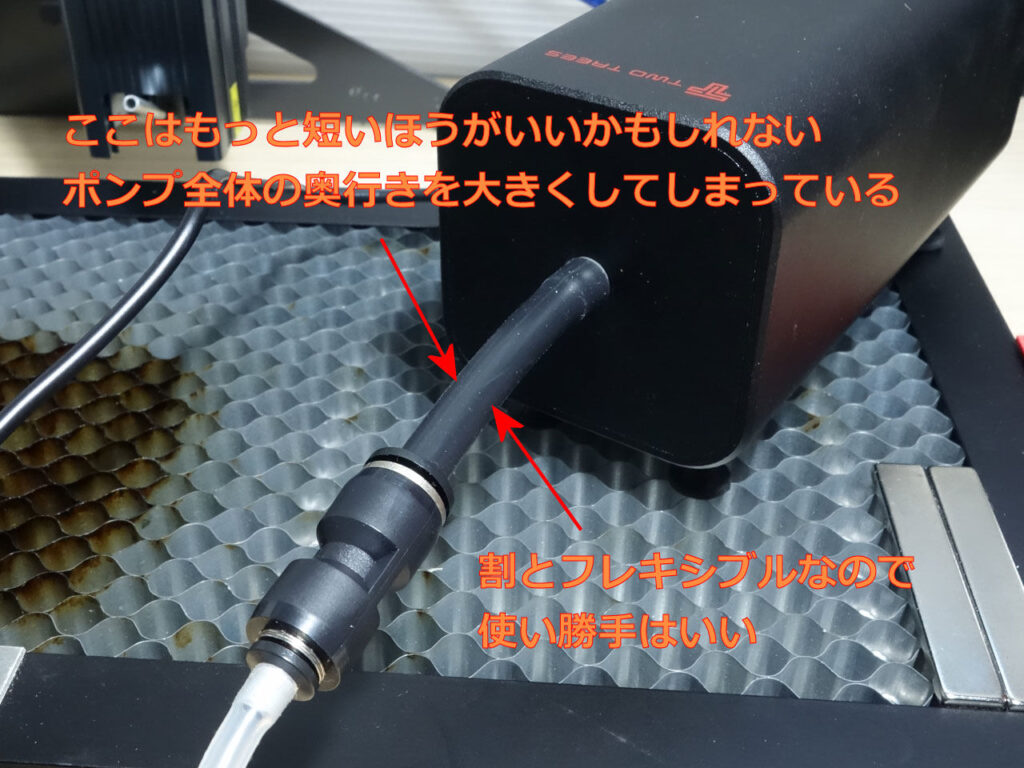
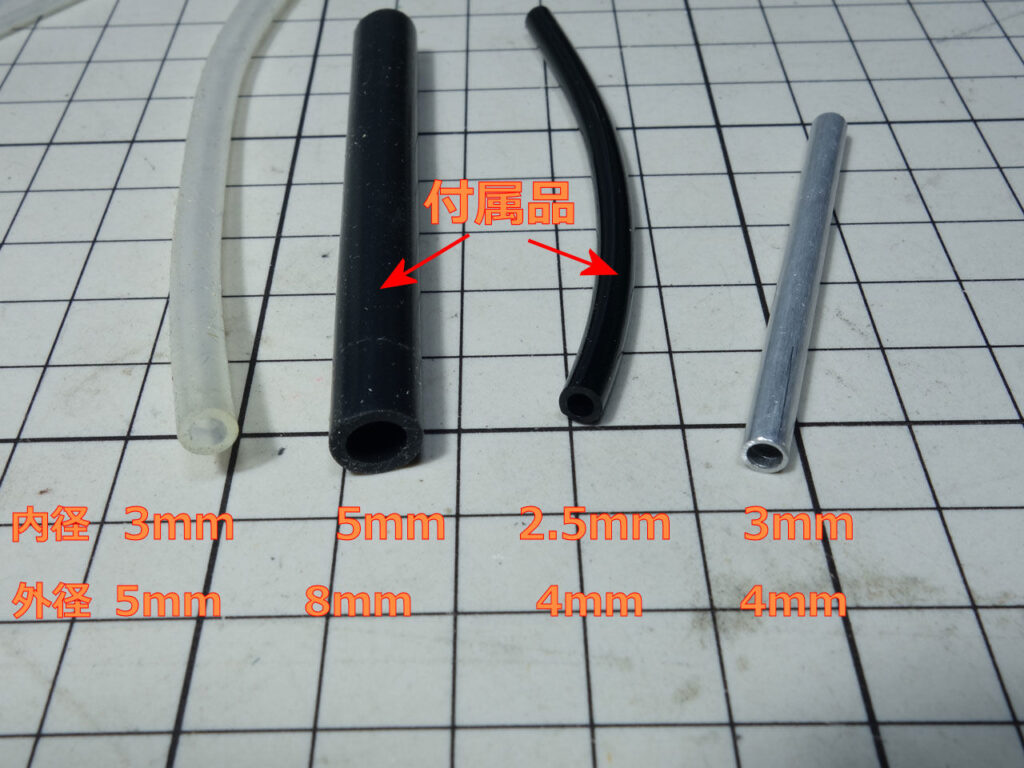
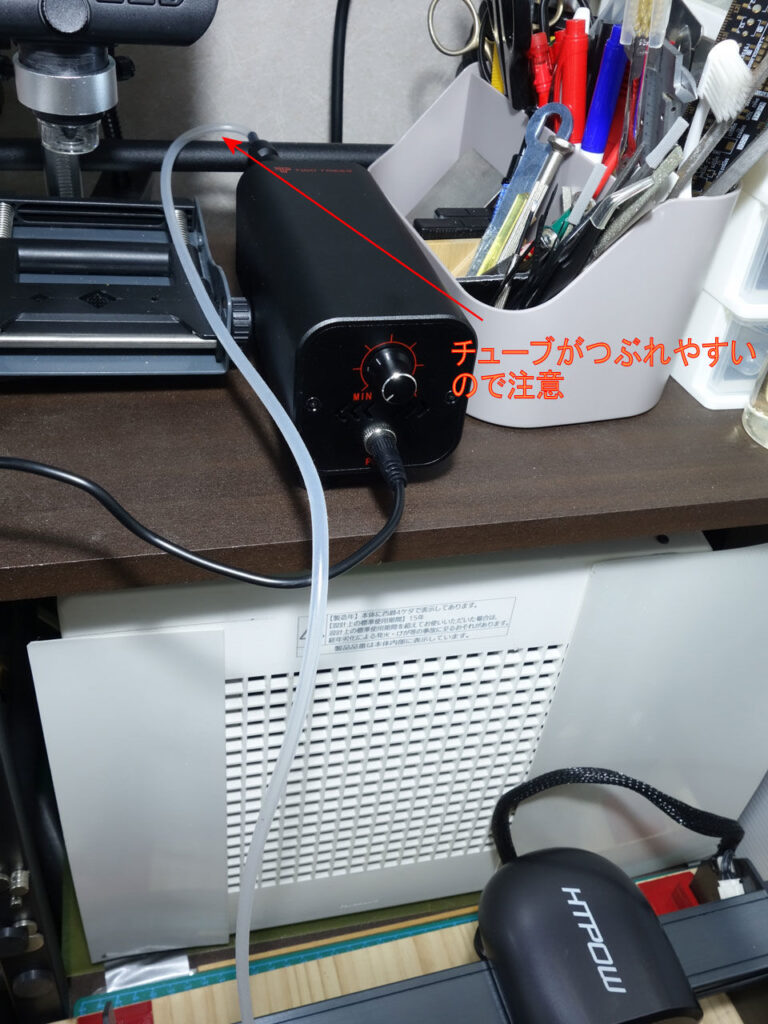
- 3Dプリンターといえば Thingiverseである.まずはここで”air assist” で検索してみた.案の定いろいろ見つかった.片っ端から確認して,どうしたらP7 M30へ応用できるかを考えた.楽しいひと時である.そのまま使えるものはなかったが,ヒントは得られた.やはりエアーはレーザーの光軸の中心と平行であるのが望ましいと考えてデザインを考えた
- レーザーモジュールを下からのぞくと,レンズを保護すると思われる穴のあいた円錐状のものが2本のネジで固定されている.この穴はレーザー光を通すためと,冷却用エアーの経路と思われる.40mmx40mmのFANが上方にあり,半導体レーザーを冷却して下へとエアーが抜けていく構造なのである.従ってこれを下流で阻害してしまうのはまずい.そうならないように円錐頂点には大きめの穴が開けてあると想像した
- 半導体の冷却はレーザーモジュール本体もヒートシンク形状なのでかなり発熱するのだろう.私の環境では右側から排煙目的でかなりのエアーがレーザーモジュールへもあたるので,思いがけない効果となっている
- このノズルは,取り外したレンズ保護カバー?類似形態であるが,センターの穴径はφ6mmとした.ここに下向きにエアーが吐き出されるような角度で,アルミパイプを差し込む吐出口を造形した.内径はアルミパイプの外径+0.1mmでφ4.1mmとしてある.この角度で真円の断面で筒状構造を印刷するのは難しいので,印刷後はドリルで整える必要がある.上方FANからのエアフローを妨げないような大きさとした
- ちなみに話はそれるが,半年ぐらいP7 M30を使った頃から,電源投入時にFANから異音がするようになった.1分ぐらいすると治まるので様子を見ている.異音と同時に振動もあるので,交換しようと考えている.その際は報告記事を書く予定
- 形状的にサポート材は必須である.機能に影響のない所に付けたのだが,見えないところとはいえ,ちょっと汚くなってしまった.ベッドと接する部はベベルを付与したデザインなのだが,やはりバリが出る.その処理に有効なのがバリ取りツールである.円筒状のワークを旋盤で端面切削した後の,内径のバリをとる動画を見て,PLAにも使えそうなので購入してみた物である.Aliexpressで購入したのだが,Amazonでも同程度の価格で購入可能
- 通常,PLAの切削は難しい.粘りがあるので鋭利な刃は食い込んでしまうのだが,このツールはハンドルをもって刃を当てると,刃が回転して絶妙な角度で刃があたってくれる.スチール材のバリ取りにも使っているが,まだ刃を交換していない.替刃が10本もついている.めちゃくちゃコストパフォーマンスが高い.円周のバリだけでなく,直線状の角のバリにも有効.初めて使ったときは使い勝手がわからずちょっと悩んだが,すぐに慣れた.
- 穴形状の部分は真円にはならないのでドリルやステップドリルで修正した.先述したがアルミパイプが入る穴はφ4.1mmの設計となっている.このサイズあたりのドリルは0.1mmきざみのラインナップがあるので助かる
- いつものようにFusionでデザインしPLAで印刷する.どうやってもサポートが必要となってしまった.PLAは高温に弱いが使ってみて特に問題はなかった
- 吐出口へは外径4mm 内径3mm のアルミパイプを差し込む.そのパイプに内径3mm 外径5mm のAmazonで購入したシリコンチューブをかぶせるように接続した.フレキシブルだが,肉厚が1mmあるので,エアー厚に負けないようである
- エアアシストポンプへの接続は,取説がないのだが,クイック継手が付属するので,適合する太いパイプをそこに差し込んで,パイプの反対側を本体の白い部分にねじ込んだ.低圧なのでホースバンドなどは不要である.クイック継手の小径側へは付属している黒いポリウレタンチューブを短く切って入れ込む.はみ出したところへAmazon購入のシリコンチューブをかぶせるように接続した.ポリウレタンチューブの内径は2.5mmなので,ここでエアフローの抵抗となってしまうのが気になっていた
- そこで,ノズルに差し込んだアルミパイプもクイック継手に差し込めることに気づいたため交換した.シリコンチューブも問題なく接続できた.これで内径を0.5mm増やすことができた.断面積比で1.44倍となる.もっとも付属の黒いチューブの内径は,メーカーがテスト行った上で最良の内径なのかも知れないが,如何せんあまりフレキシブルでないためP7 M30にはあまり向いていないと思い,換装なった次第である
- このノズルの3Dプリンター印刷用データ(STL形式)は,ダウンロードセンターに登録しておくので,自己責任でお使いください
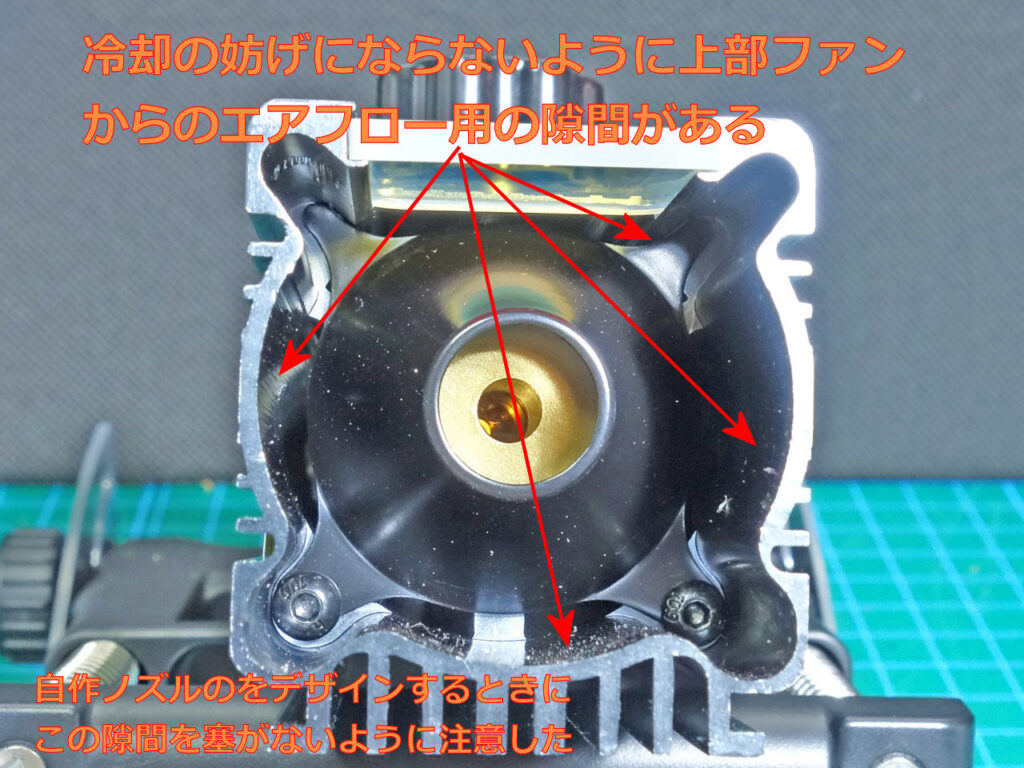
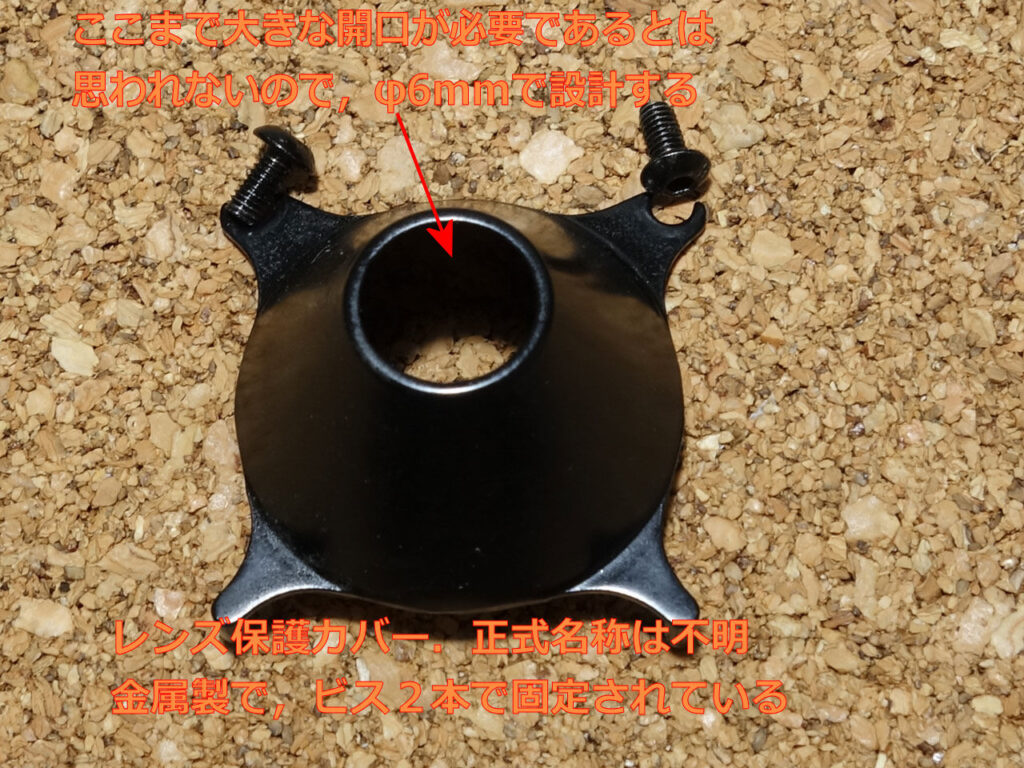
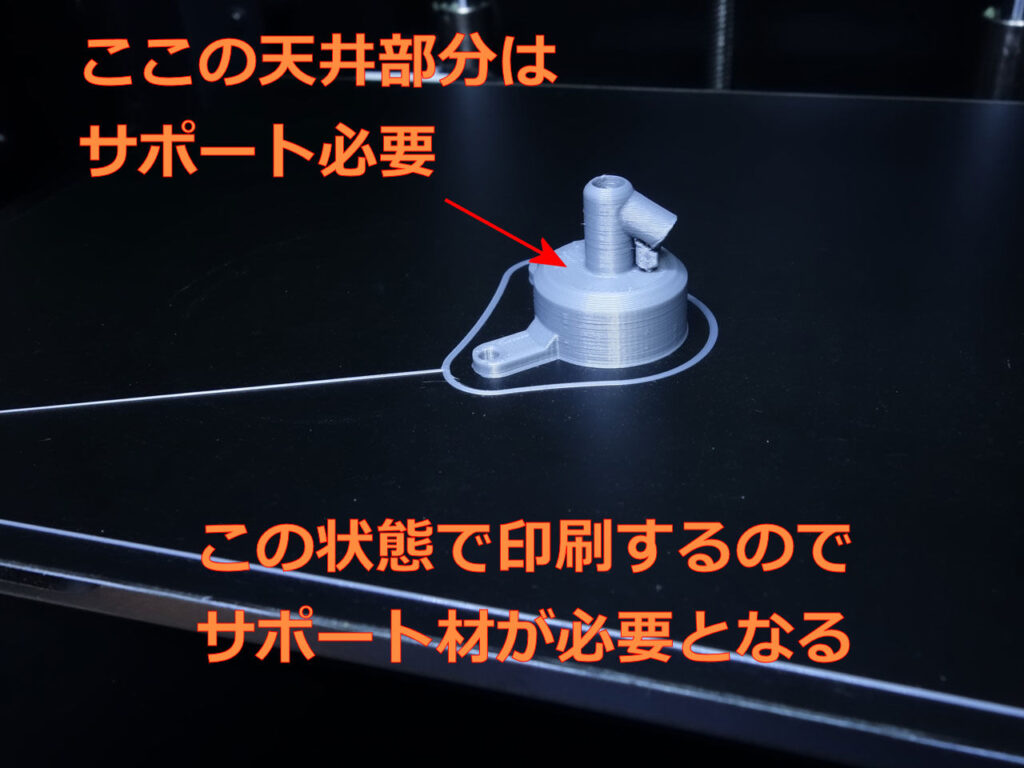
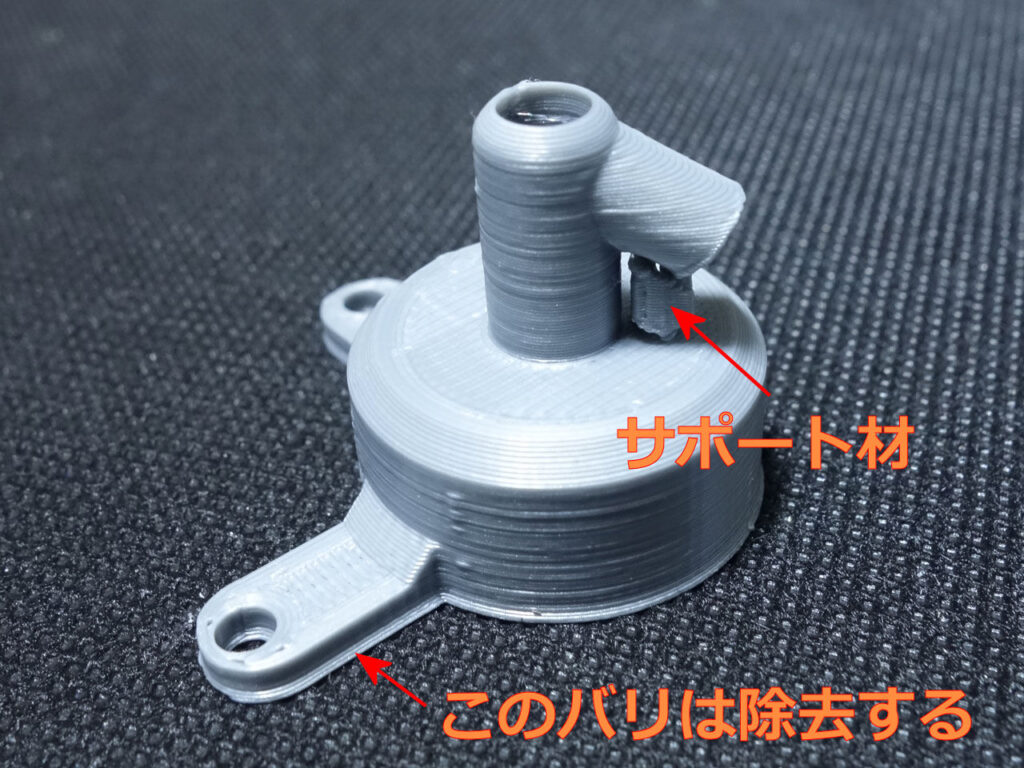
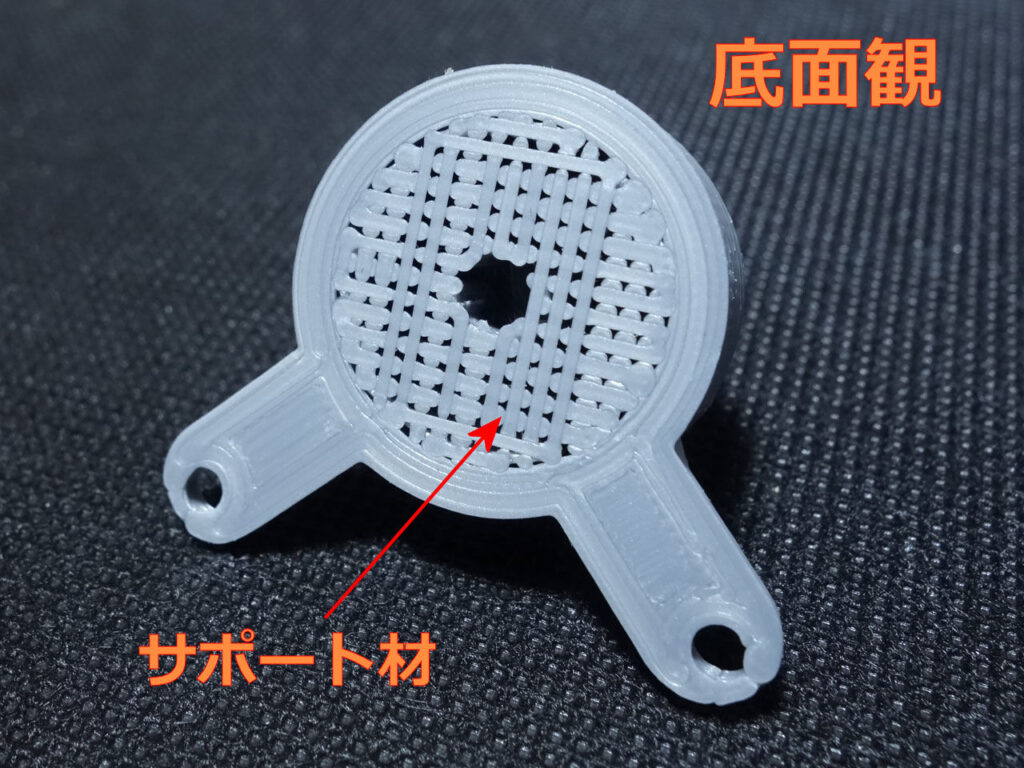
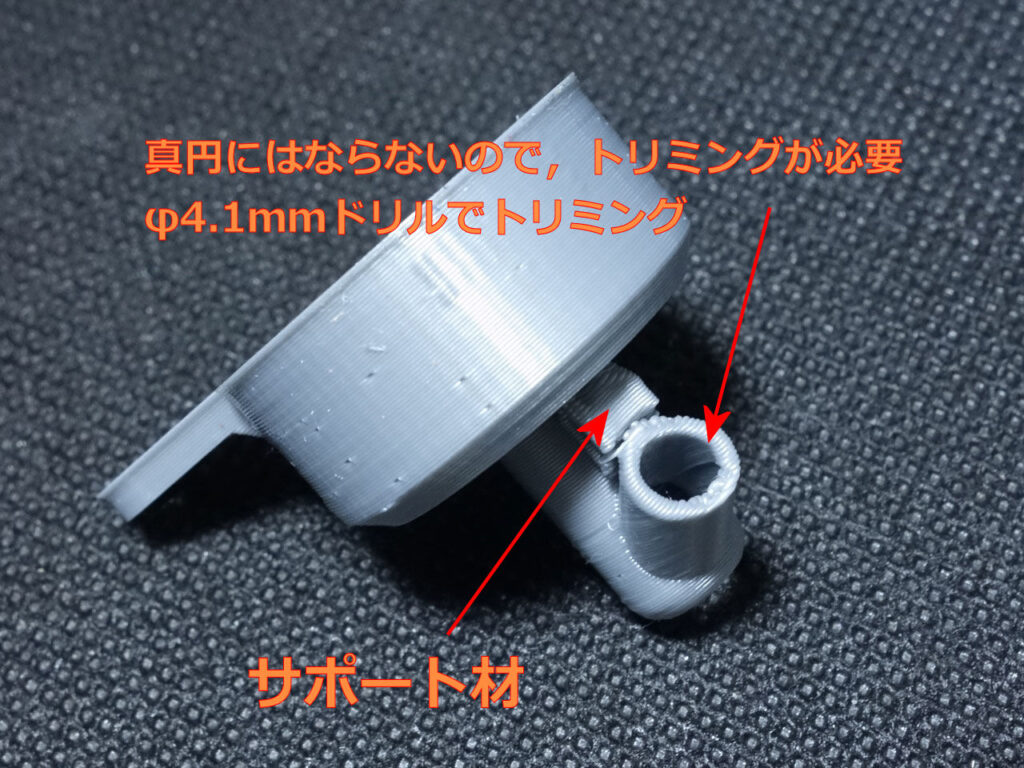
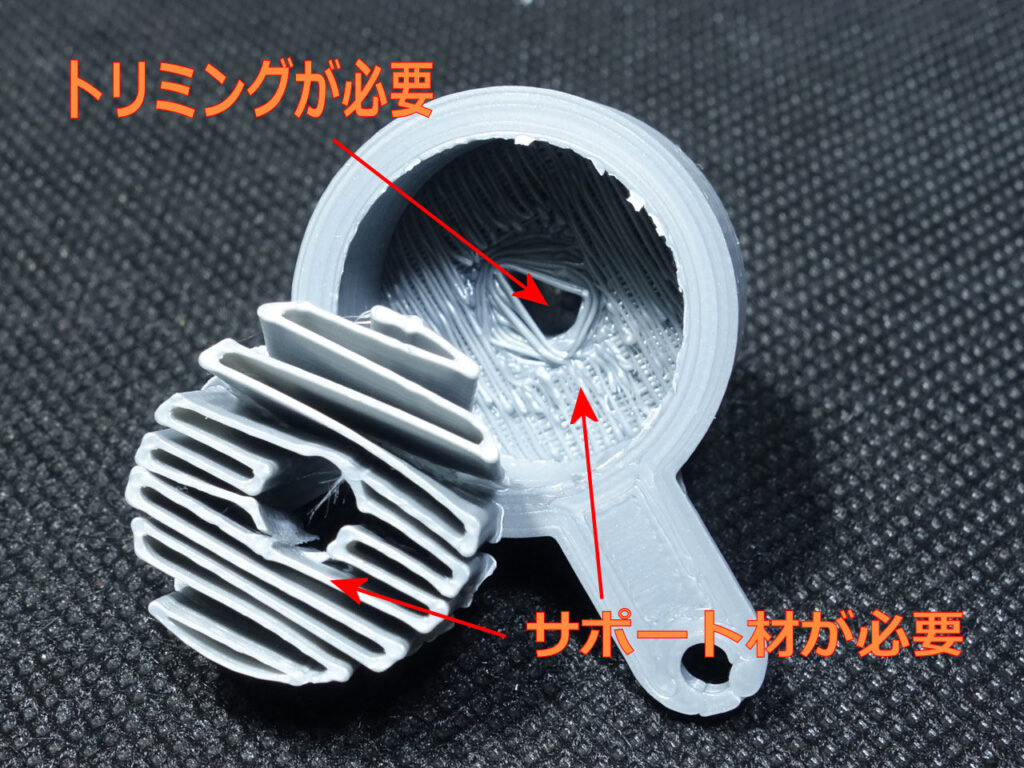
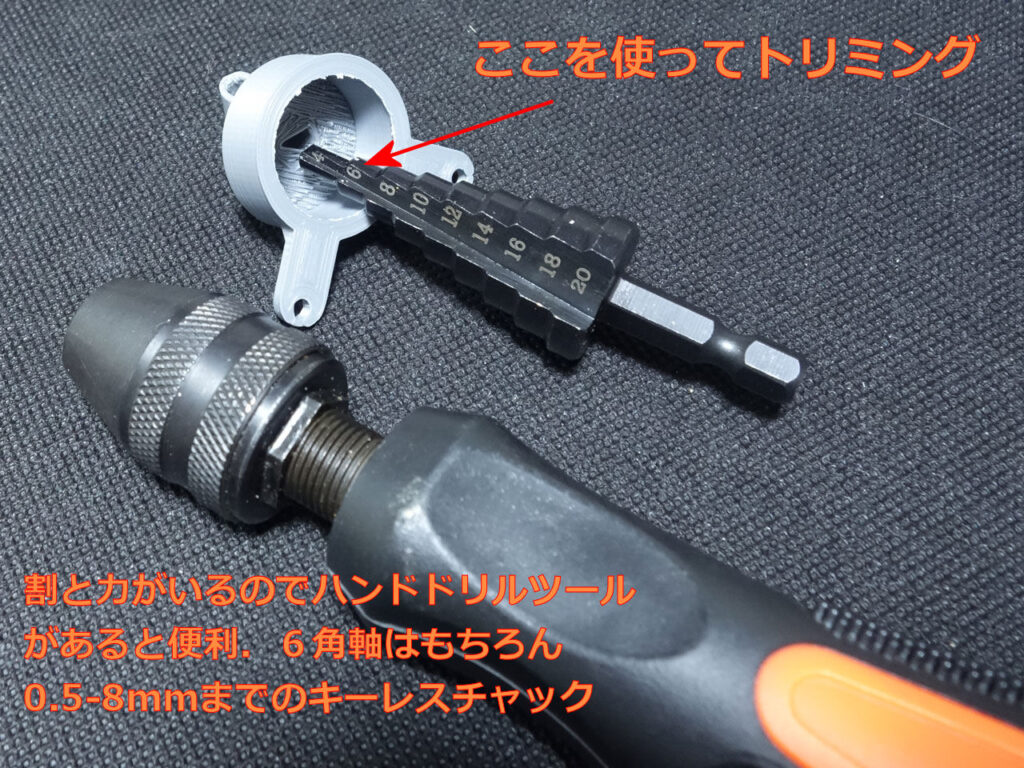
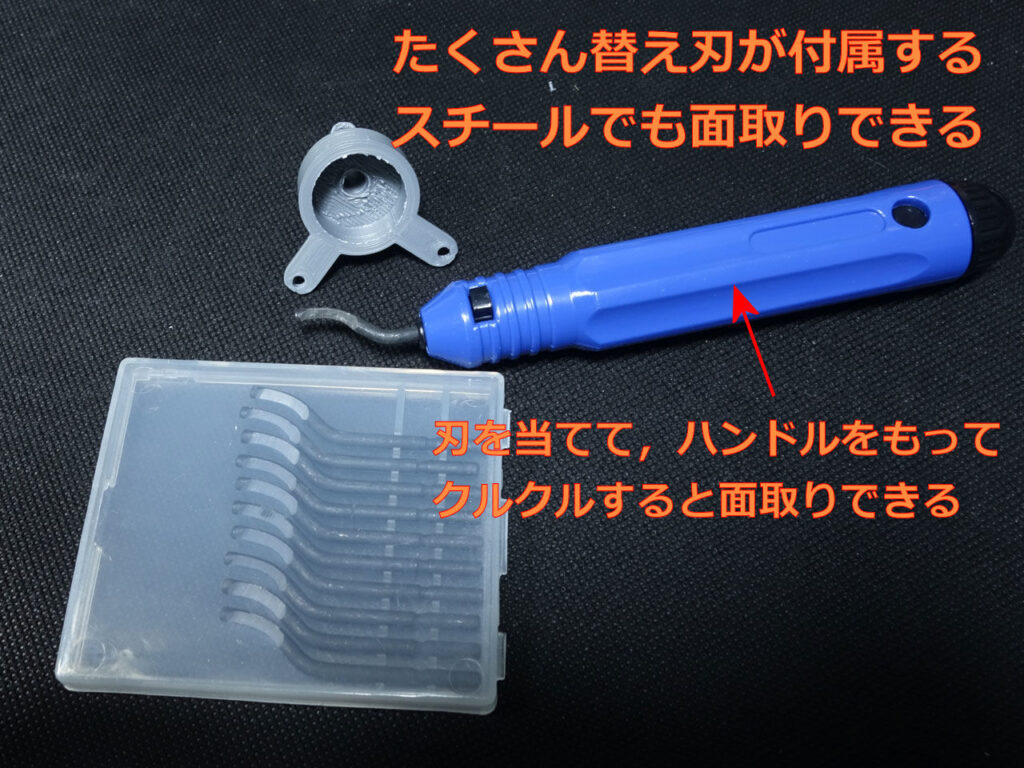
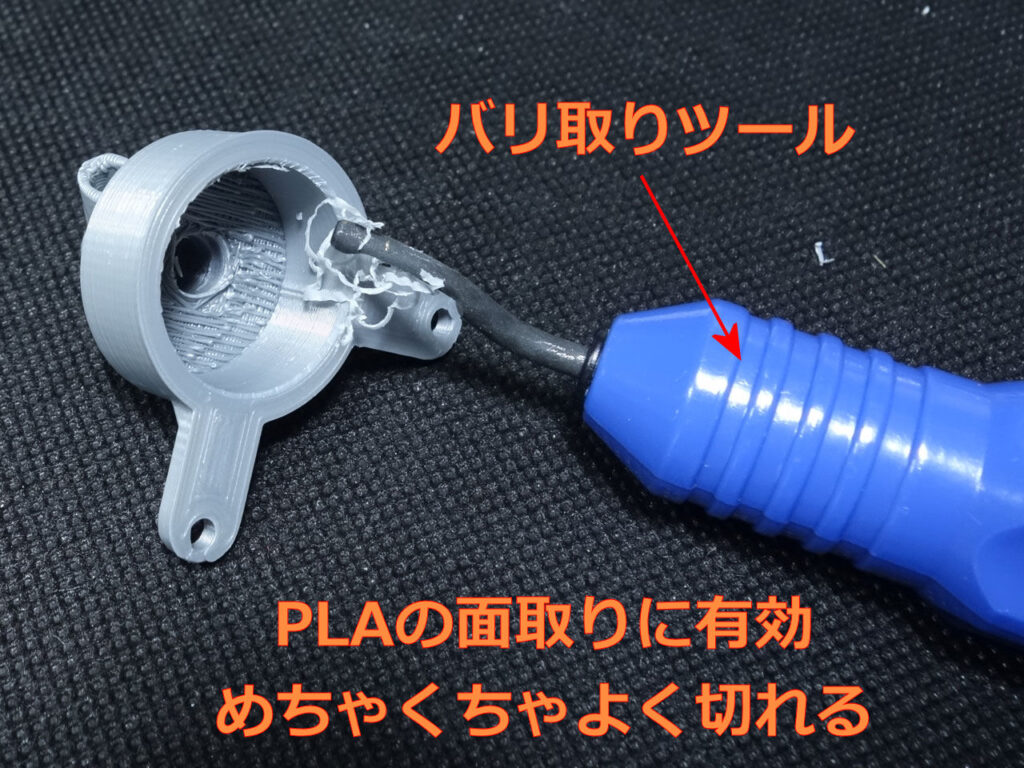
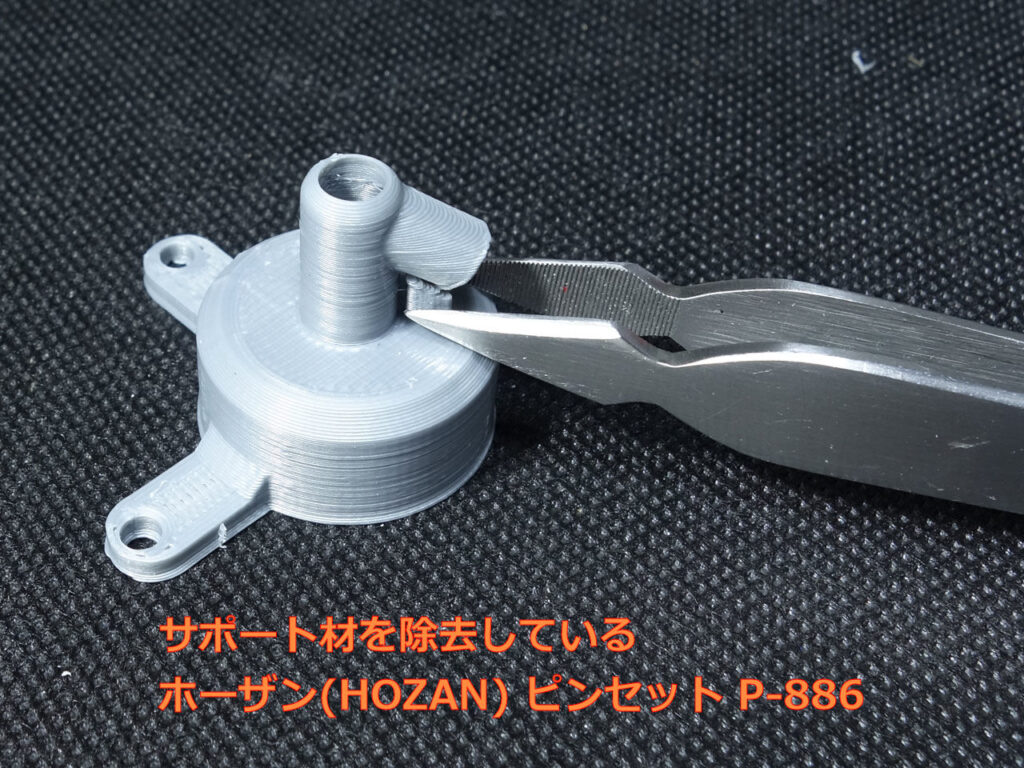
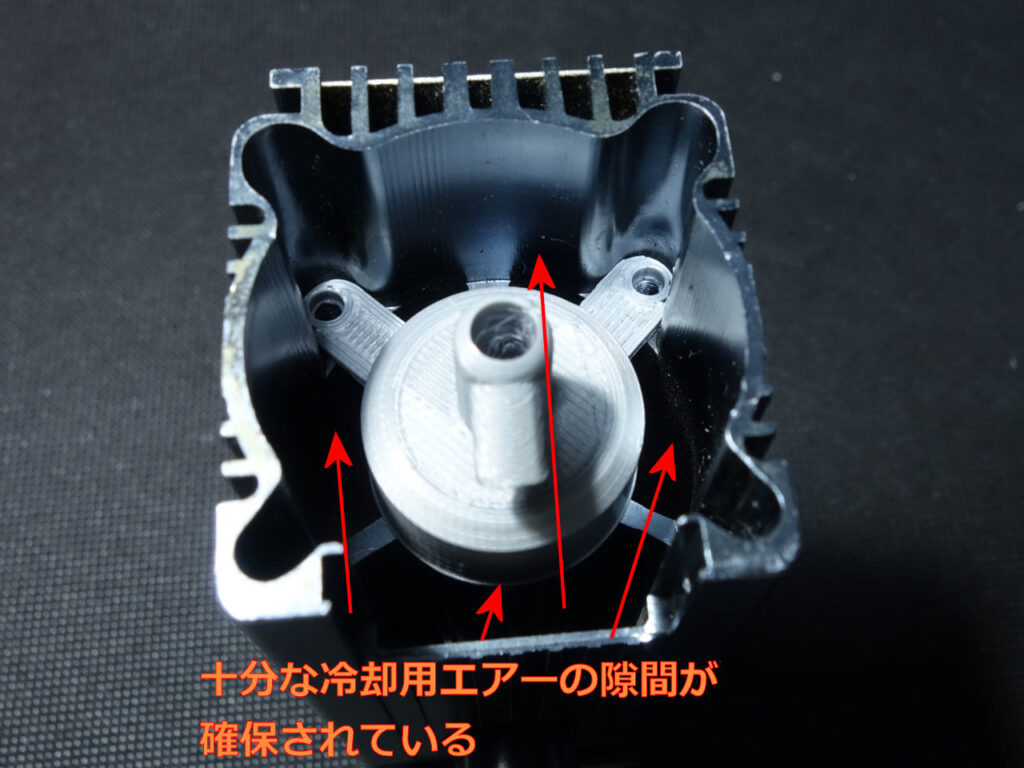
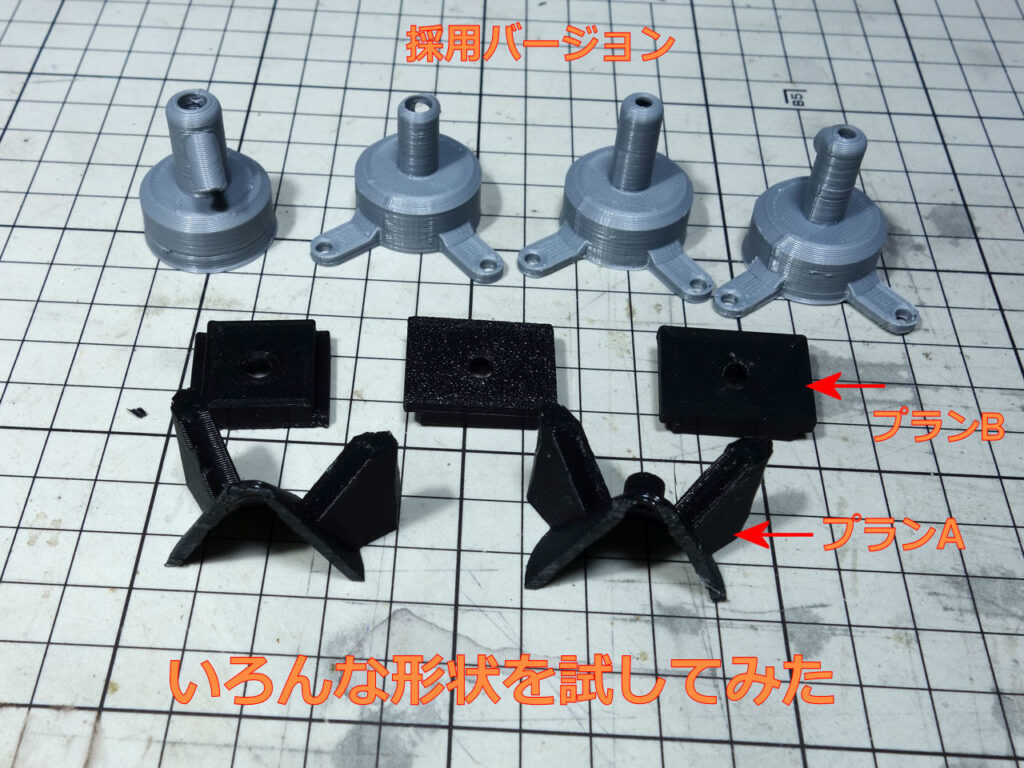
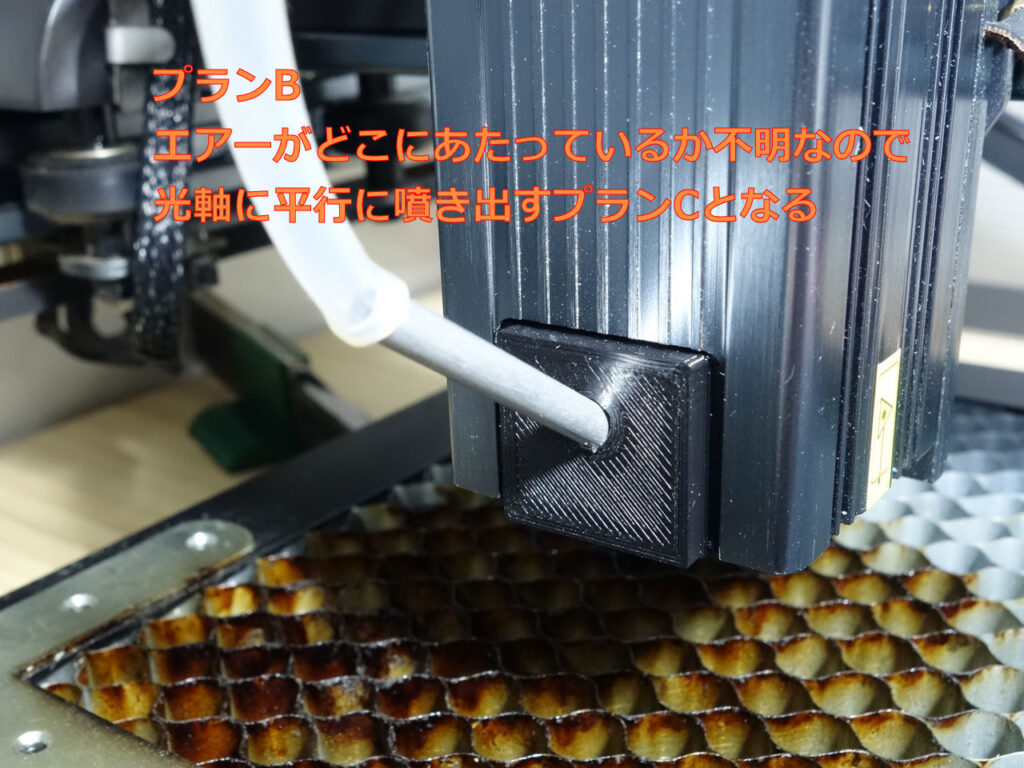
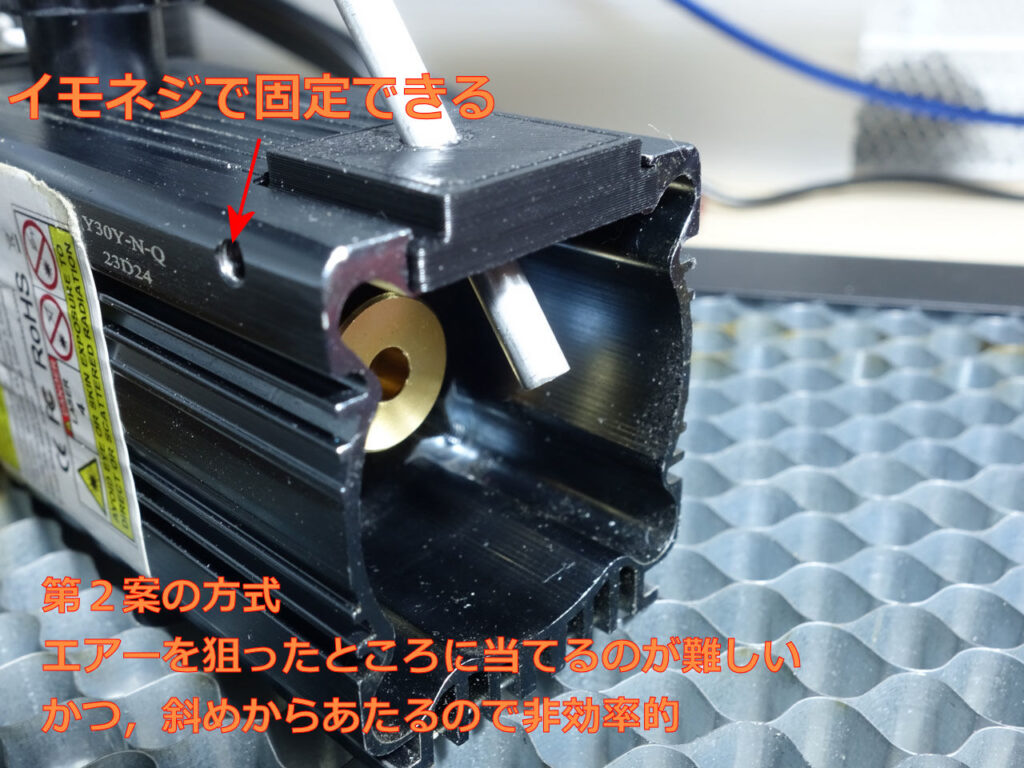
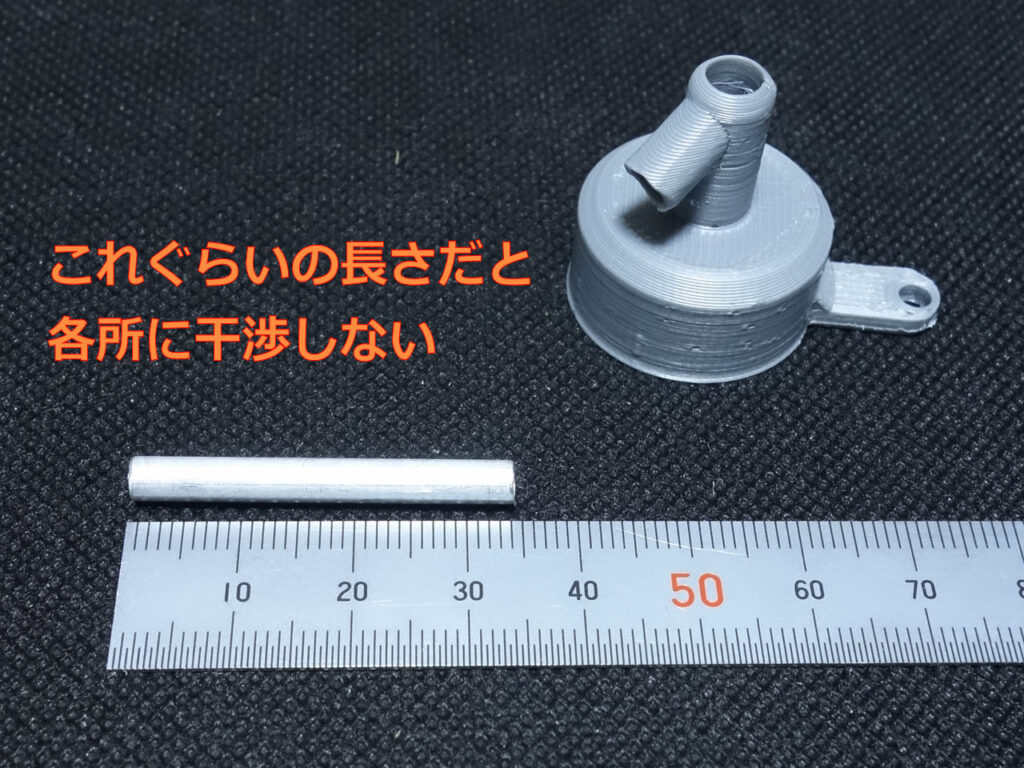
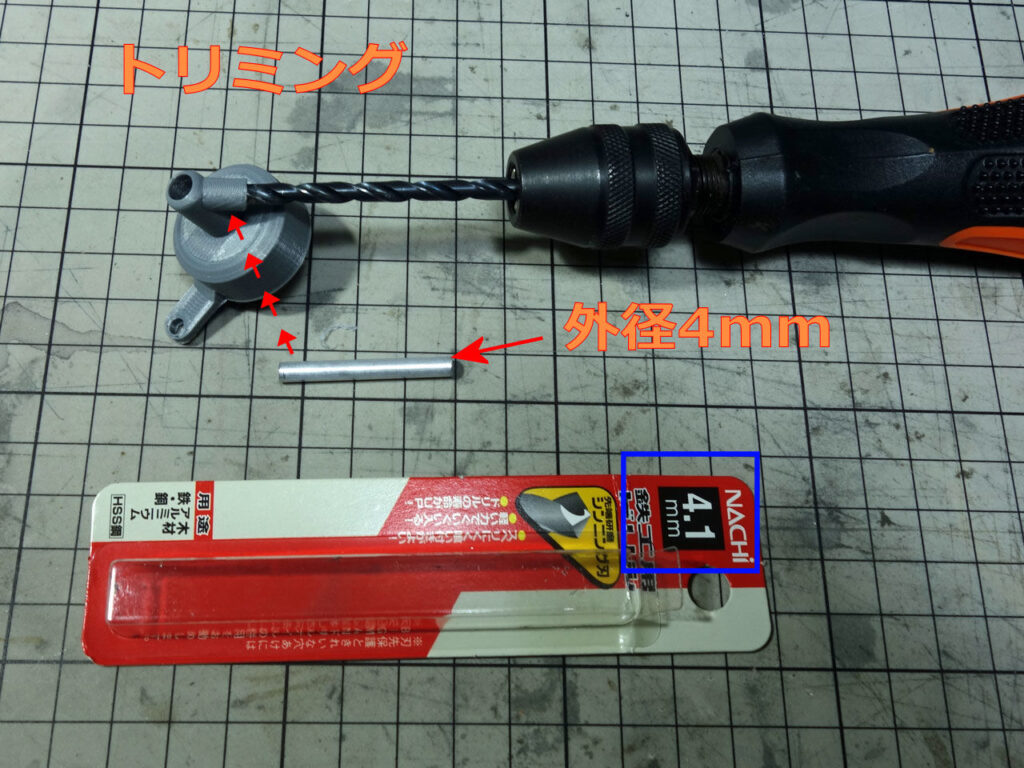
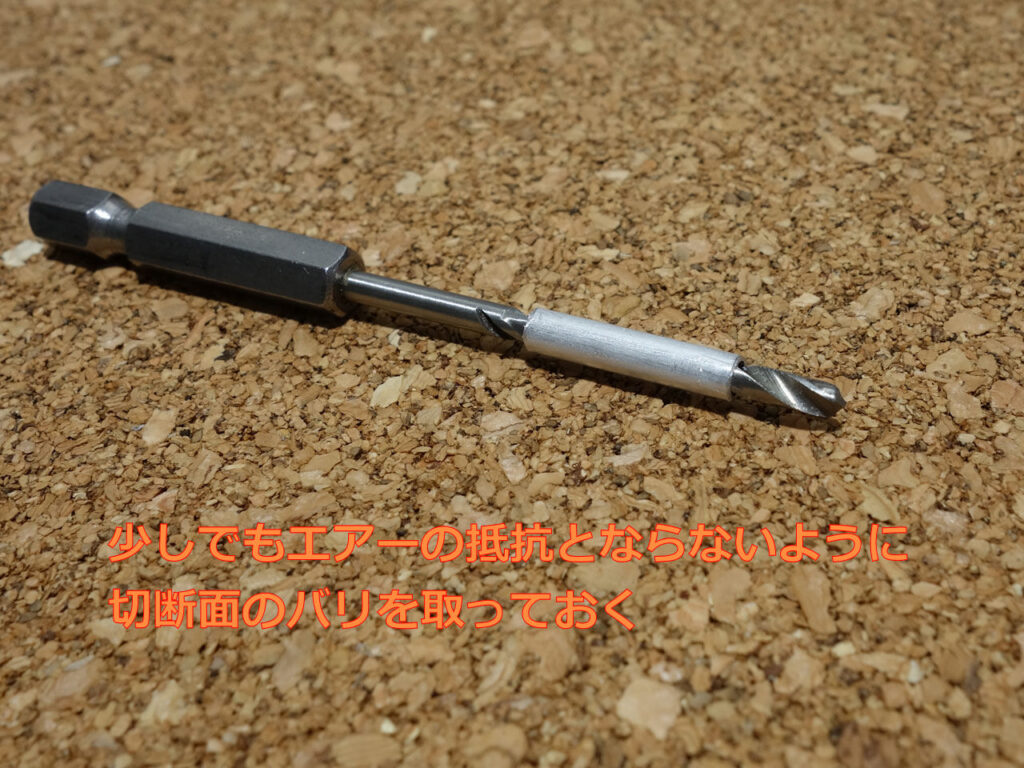
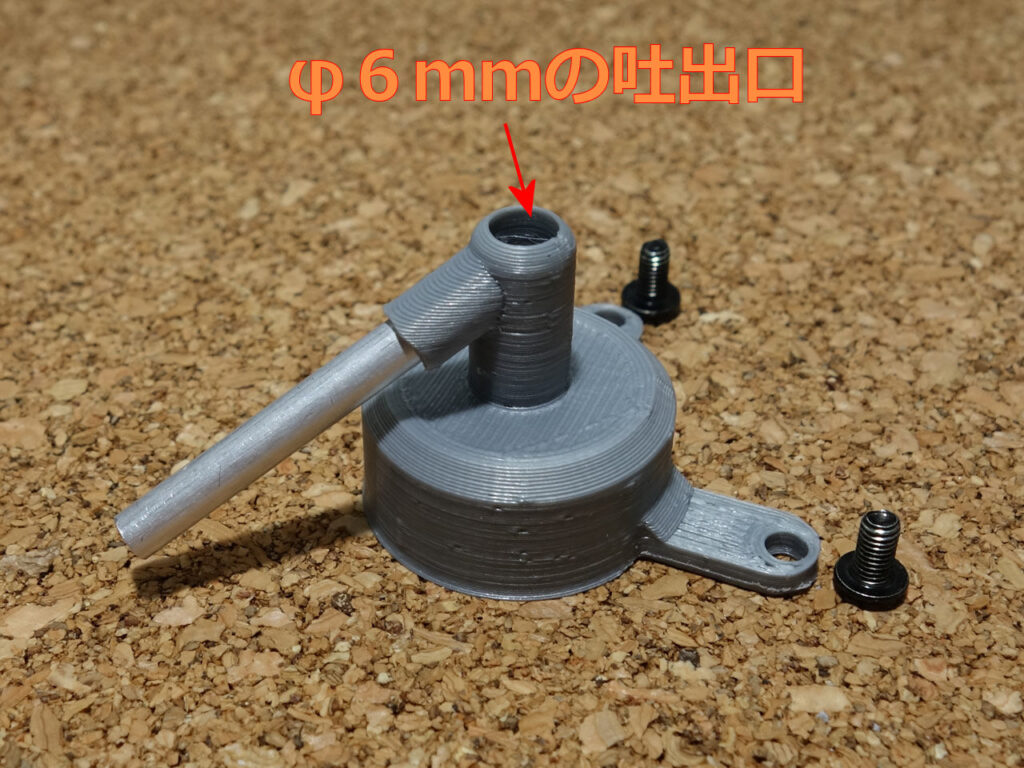
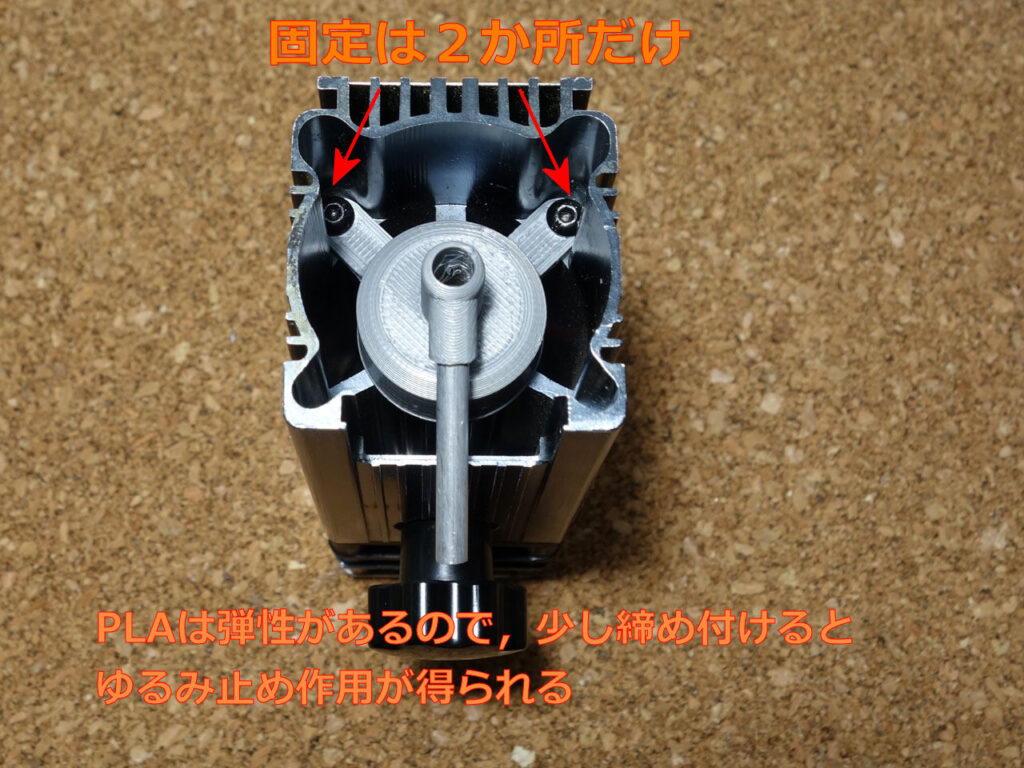
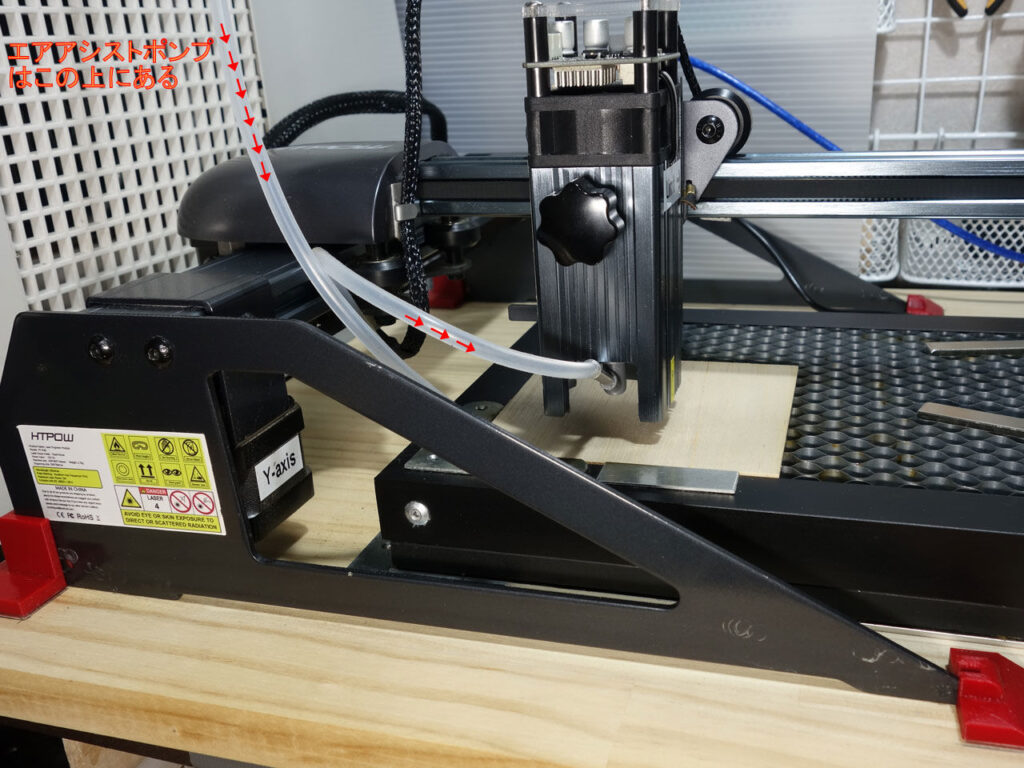
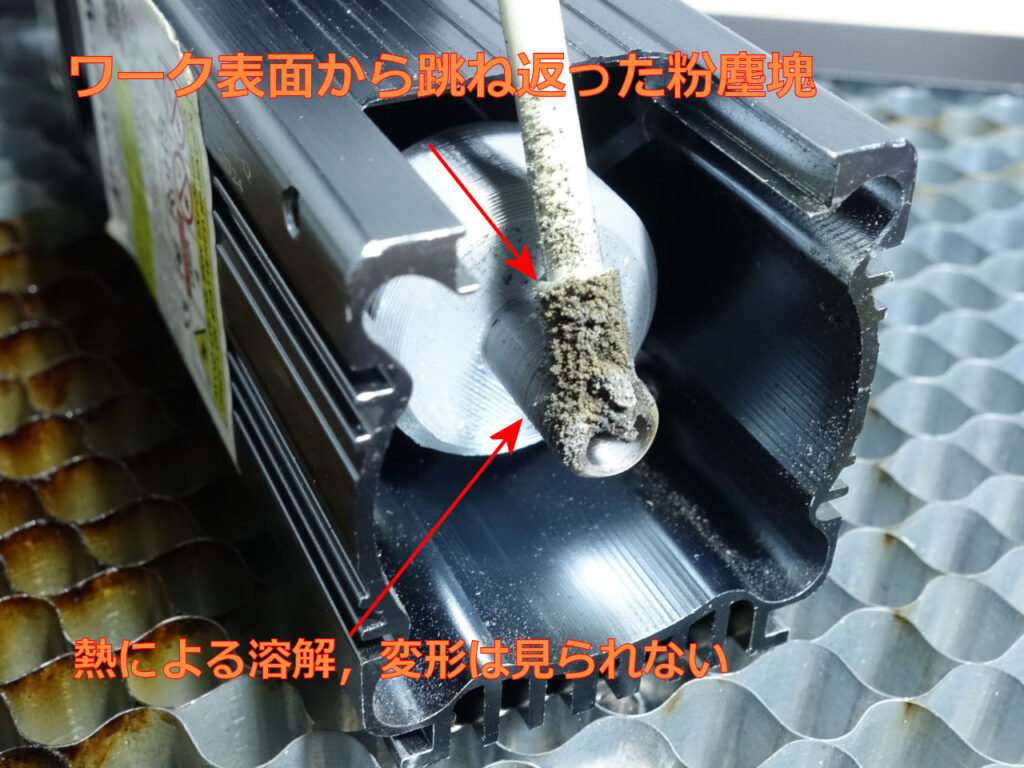
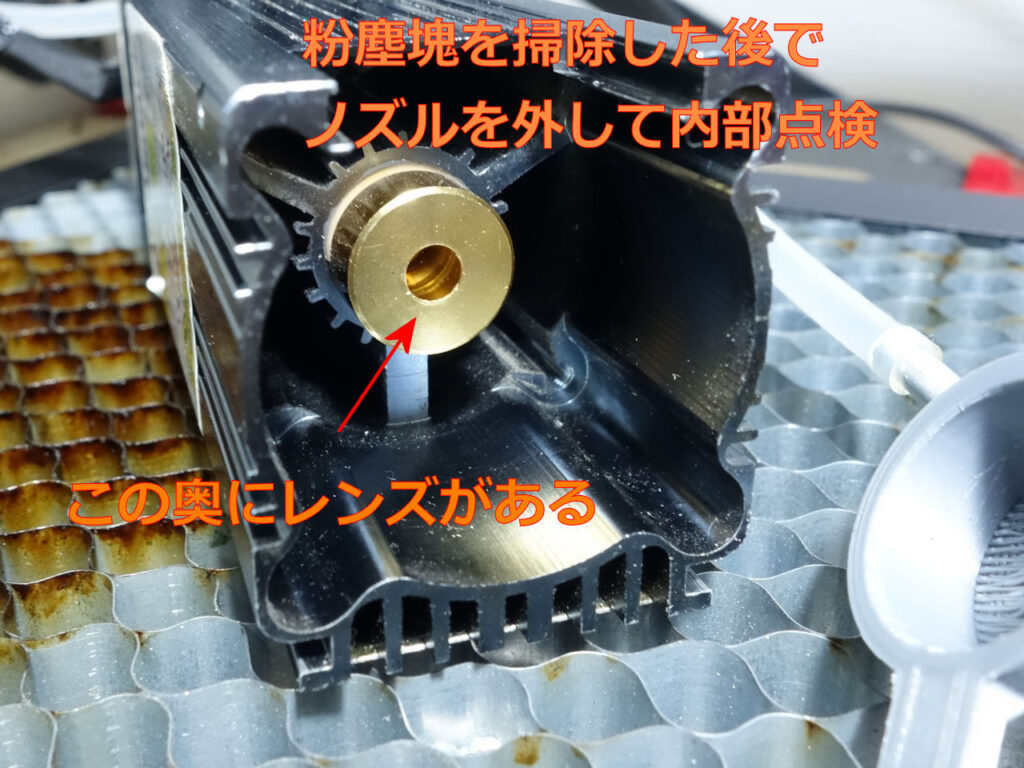
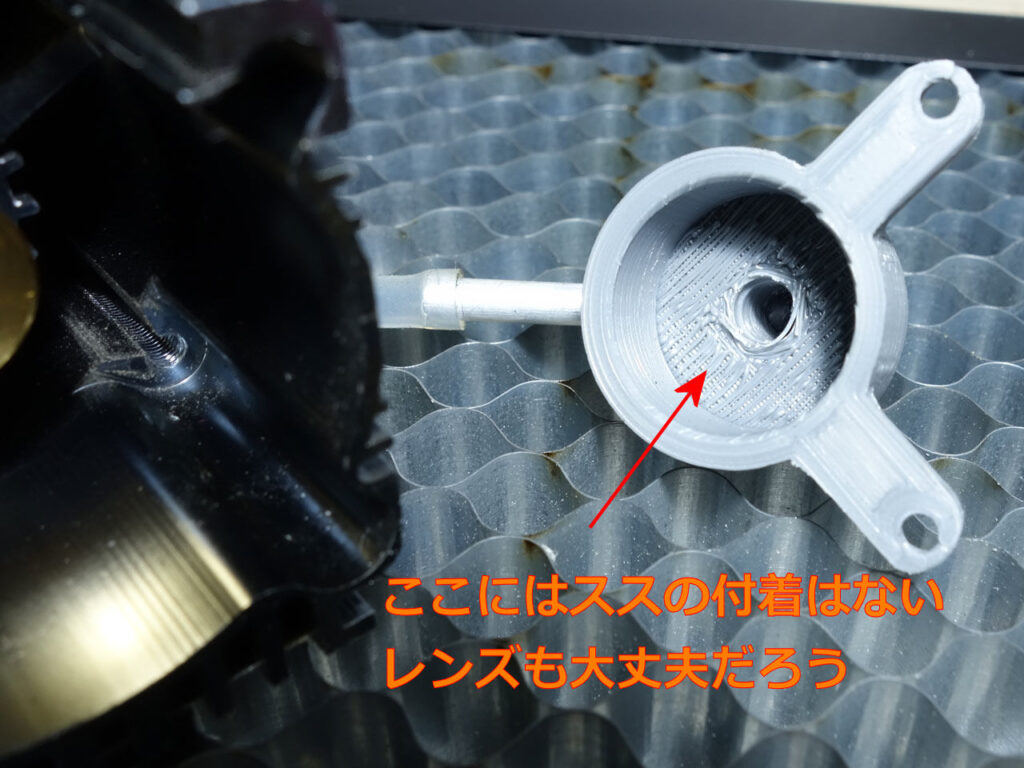
- マスキングテープは効果が大きいのは予想通りであるが,両面に用いたときも悪影響を与えあうことなく良好な結果が得られた.塗装しない場合は行っておくべきだろう.まあ剥がすのは面倒ではあるが
- 細かったり,形状によってはワークから押して抜く時に折れるのを防いでくれるのに気づいた
- 自作エアアシストノズルであるが,これも効果絶大である.全くヤニが付かないということではないがほとんど付着しなくなる.
- ネット情報の通り,切断深度は大きくなる実感がある.きれいになると同時に,同じパラメーターなら厚いワークのカットができるようになる
- マスキングテープとエアアシストの併用が最強となる.ただし,エアー吐出量が多ければ多いほどいいというわけではないというネット情報があったので,最良の結果を得るにはいろいろ試してみないといけないのだが面倒なので最大吐出量で使用しているが,結果には満足している
- 切り抜き・カットのサンプルを,オーナメント作製記録として別記事にする予定