- タップを垂直にたてるツールを製作する.対象となる素材は3Dプリンターで印刷したPLA,PETGや,アルミフラットバーである
- 垂直にあけるため,ドリルスタンドを改造,ギヤダウンしたユニットを使い電動とする
- Amazonを見ると,「タッパー」「タッパ」などと呼ばれるタップを切るさまざまなツールが販売されている.また,中華製と思しき「ハンドタッパー」なるものもある.今回製作したのは目的はタップを切るという点で同じであるが,いろいろと違いがある
- 通常,所定の下穴をドリルで開けてタップをたてるが,できるだけ垂直にたてていくため,いったんボール盤のチャックにくわえさせて垂直を出してゆっくり回転させ進めていき,かんだらタップをチャックから外してタップハンドルにタップをセットして,手でネジを切っていく
- しかしタップをチャックからそーっと外してハンドルにセットし直すのは結構気を使い,面倒なもの.タップあるあるだと思う.このあたりの対策・工夫を行った
- ボール盤のようにタップを”チャック”にセットして垂直に下穴へ食い込ませる.ある程度食い込んだらスタンドのハンドルを上げると,タップはワークに残したまま容易にタップのシャンクは”チャック”から抜けてくる.そのタップをタップハンドルにセットして,タップを切っていく.ざっとこんな感じ
- ある時モーターを探してAmazonをサーフィンしていると,面白そうなギヤダウンユニットを見つけた.その形態を見てピン!ときたのでマイリストに入れておいた.これの出番である
- どう見ても中華製である.当然のごとくAliexpressをサーフィンする.あった!当時は何故か激安であったのでスペック違いで1個¥344を5個購入した.破格の¥1636である
- モーターは370系.電圧は 6,12,24V があり,それぞれに回転数が選べる
モータ軸の回転速度は 6000r.p.mのよう - 今回の選定では6Vと12Vを購入した.6VはUSBモバイルバッテリーでの使用も考えたためである.12V は自動車バッテリー使用を考えたため
- 電流は比較的小さく12V 35r.p.m のものでは最大負荷時で1.5Aと思われる
Aliexpressから引用しておきます(URL引用) - 実際に確認してから思ったのだが,このクオリティでこの価格はヤバイ.恐るべし中華
- 購入した商品ではないが同じ型番(JGA25-370)のリンクを掲載しておきます.いつか何かに使えます! Aliexpressで買えるときに買っておこう!
- このツールもほかのnano工作機械のようにフットペダルでの運用とした.当工房のフットペダル仕様の電源は24Vとなるため,ケースを作りその中にDC-DCコンバーターを入れ,さらに回転方向反転用のスイッチをつけてタップ送りと戻しが簡単にできるような設計とした
- 一応の完成を見て,まずは3Dプリンターの失敗ストックPLAで試してみた
その時のギヤダウンユニットは12V 16r.p.m のもの.難なくタップは切れたがそんなにトルクは必要とせず,ゆっくり過ぎてイライラしたのでもっと回転数が欲くなり,12V 35r.p.m のものに変更.これが今のところベストマッチと思われる.思ったよりうまくいったのでこのギヤダウンユニットでの製作記録をご紹介
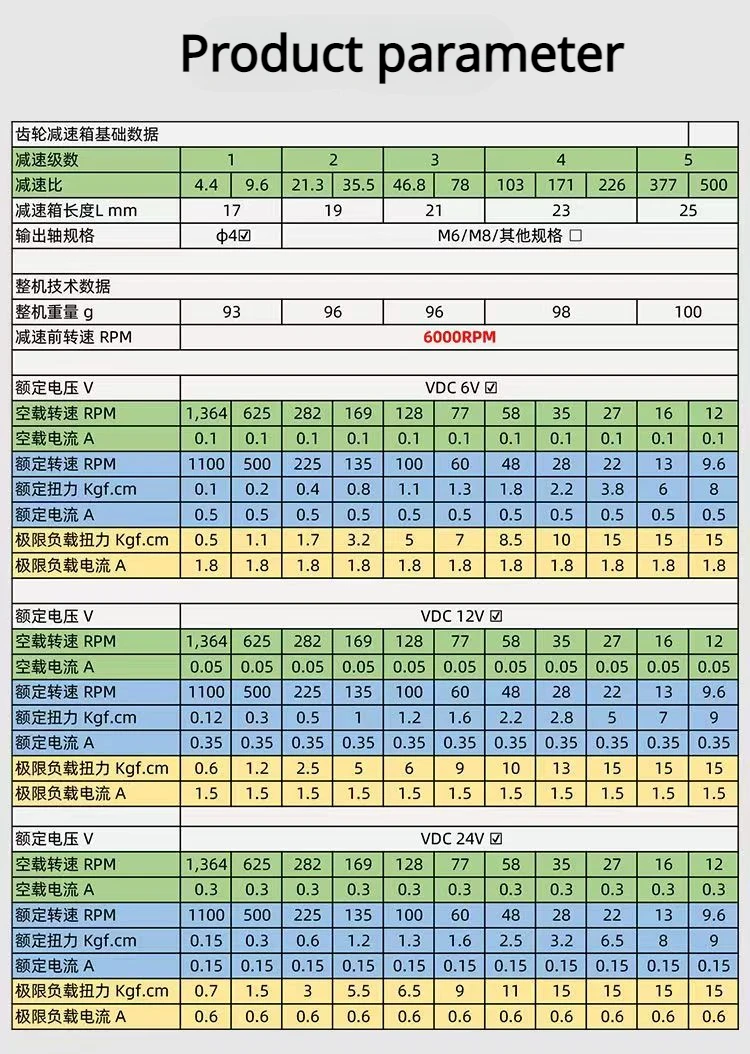
- 垂直にタップを切るには,ドリルスタンドに取り付けるのが手っとりばやい
いかにギヤダウンユニットを取り付けるかが肝である - ドリルスタンドはAmazonで一番安いものを探した.そんなにしっかりしたものである必要はないので加工しやすそうなものを選ぶ.そして購入したものがこれで¥2,999
- 手元に届いたものは予想通り手直しが必要であったが,当然望むところだ!
- まずは支柱の問題.φ25mmステンレスパイプなのだが,シームレスではなく継ぎ目がありスタンドの土台との接合・固定部分のキャップホルトを締めると簡単につぶれてしまう
- 本来の目的ならできるだけ強固に締め付ける必要があるので,これは完全NG!
がしかし,タップスタンドならまあそこまでの強度はいらないと思うので,3Dプリンターで芯材を作ってから締め付けた - ハンドルを上に上げた状態に保つスプリングが内蔵されているのだが,これが強すぎるので外してしまう.黒い側面のパネル?を3本のタッピングビスを外すことで取り外す.スプリングはフックに引っ掛けてあるだけなので容易に外せる
- ハンドルが関与する機構はガタが多いのだが,ある程度は改善するようワッシャを挟むなどの改良を行った
- 電気ドリルを取りつけ上下する部分はAmazon商品説明で「電気ドリルフレーム」と呼んでいると思われるので本記事でもそう呼ぶことにする
- シームレスではない継ぎ目のある厚さ1mm程度のパイプに,電気ドリルフレームは取り付けてある.本来のドリルスタンドの目的では不十分であるが,タップスタンドとしては問題ないのだが,念のためベース部分とのボルトを強く締めるためパイプの中に詰め物を行った.これがないと締めこむにつれて簡単にパイプはつぶれてしまう
- 電気ドリルフレームを固定するときに力が入れやすいように,ノブナットやフィットノブを使用した
- ハンドルを上下して,リニアに電気ドリルフレームが上下する範囲は,ハンドル操作範囲の中央部分のみである.動きを規制するためのシャフトが曲者で,いくら調整してもハンドル可動全範囲でリニアな動きは不可能であった.もっとも,タップのネジ部はせいぜい20mm程度のため問題はない.ちゃんと動くドリルスタンドで作れば気持ちの良いものができたと思うが値段が値段なので良しとした
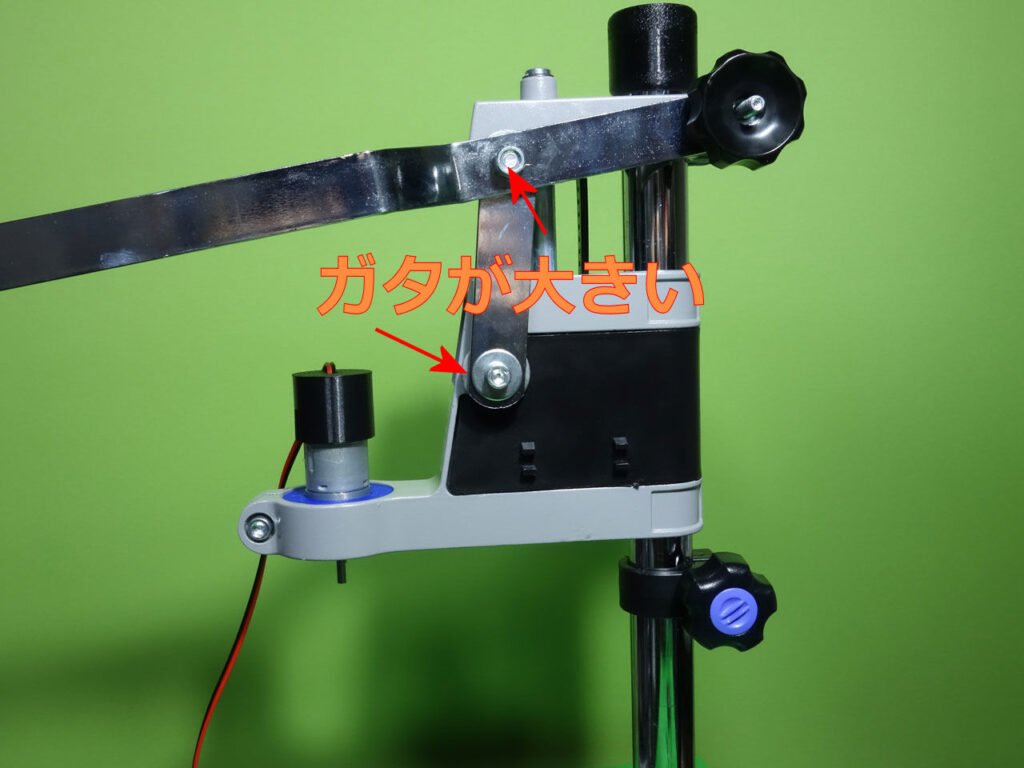
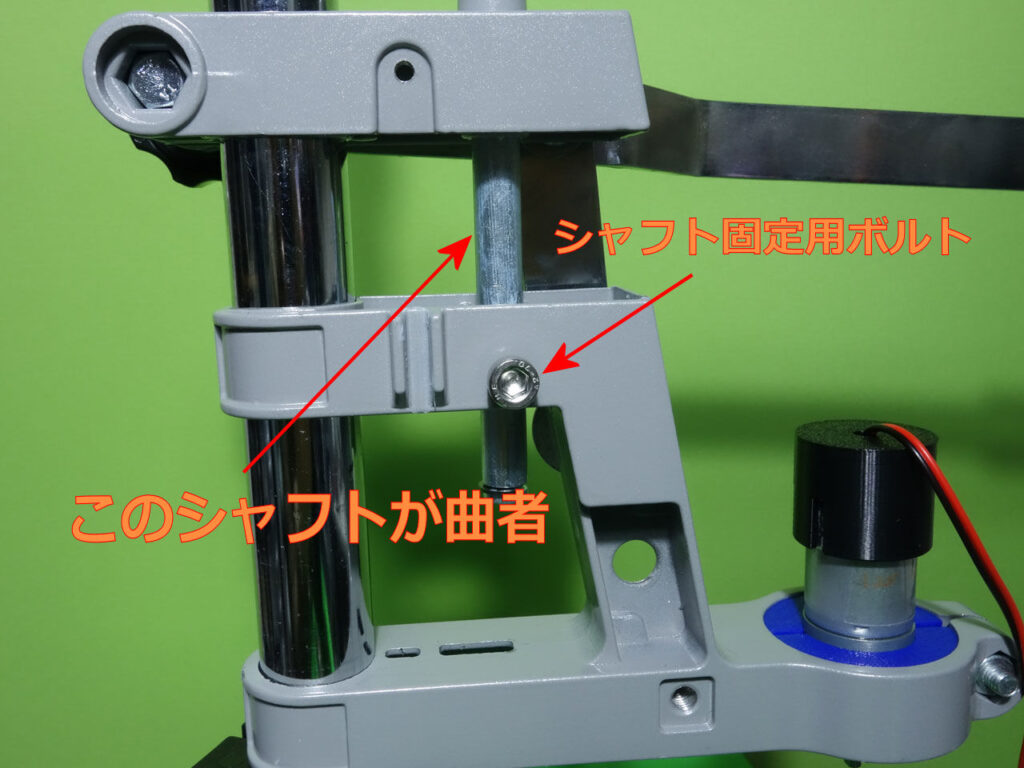
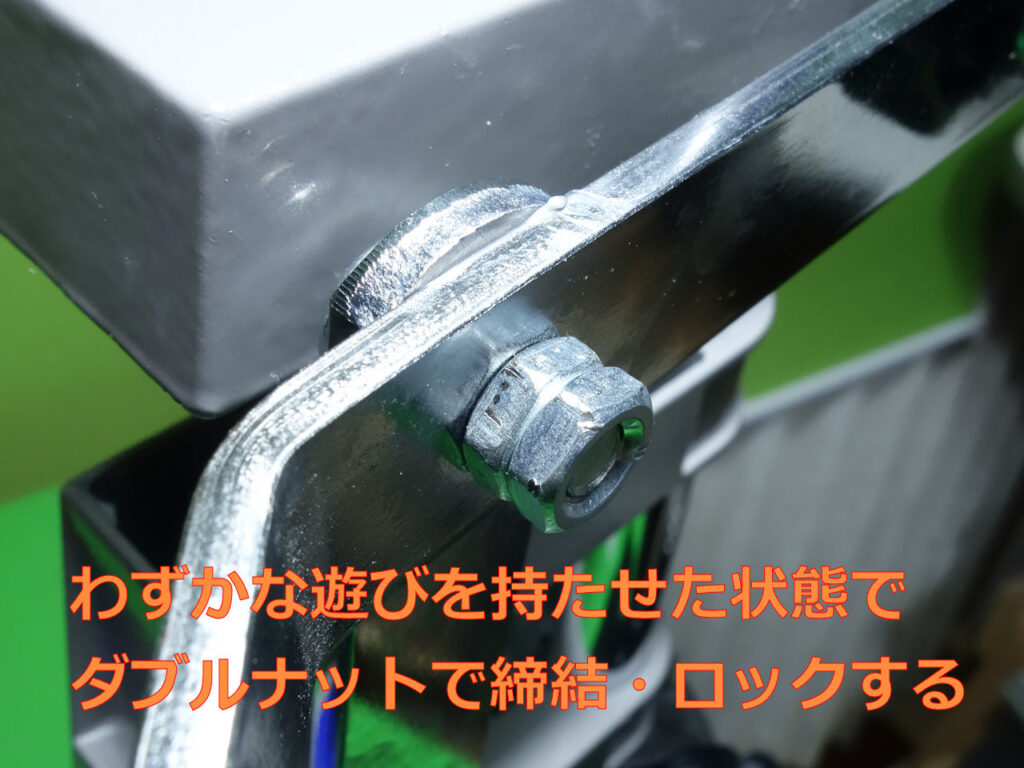
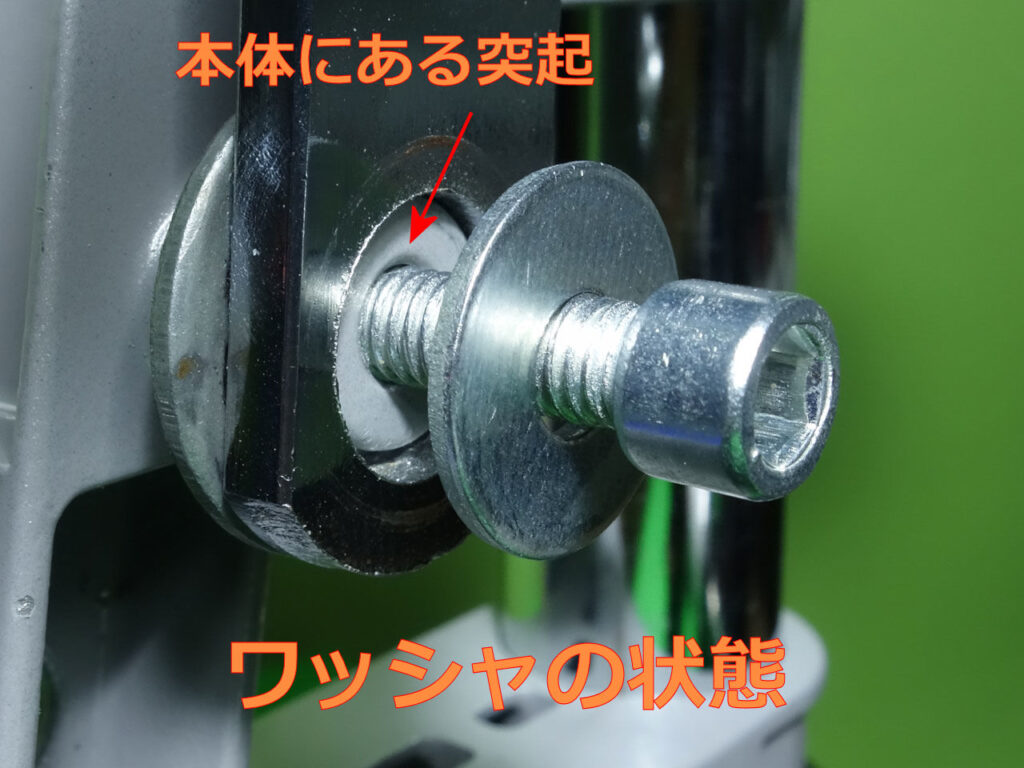
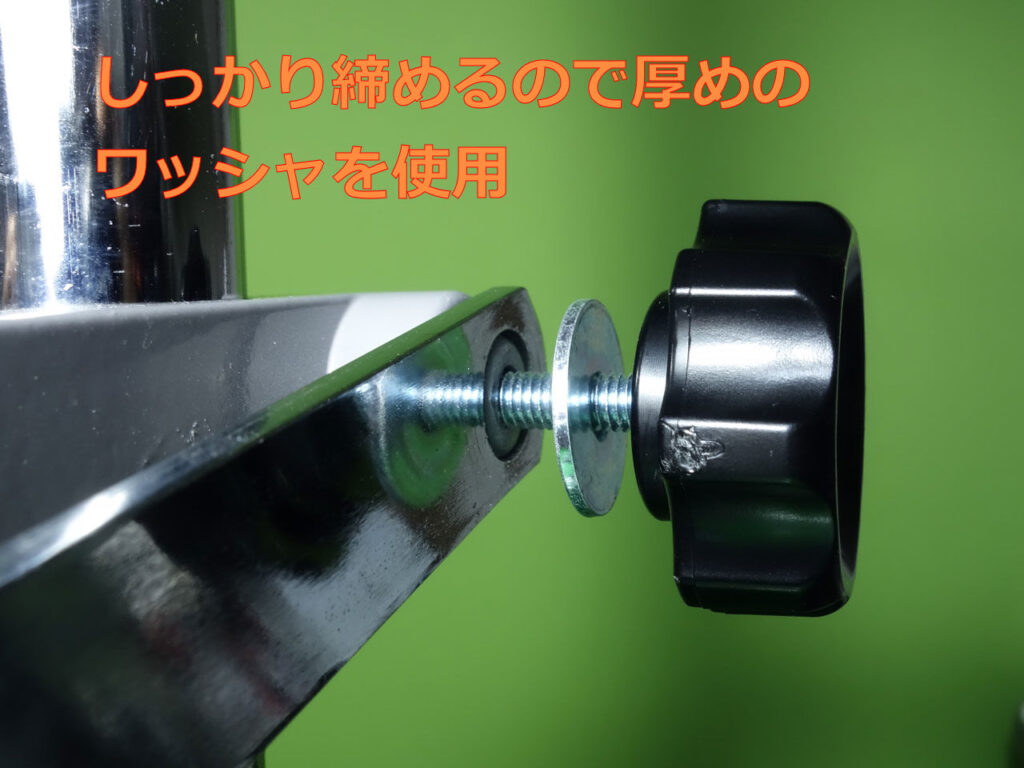
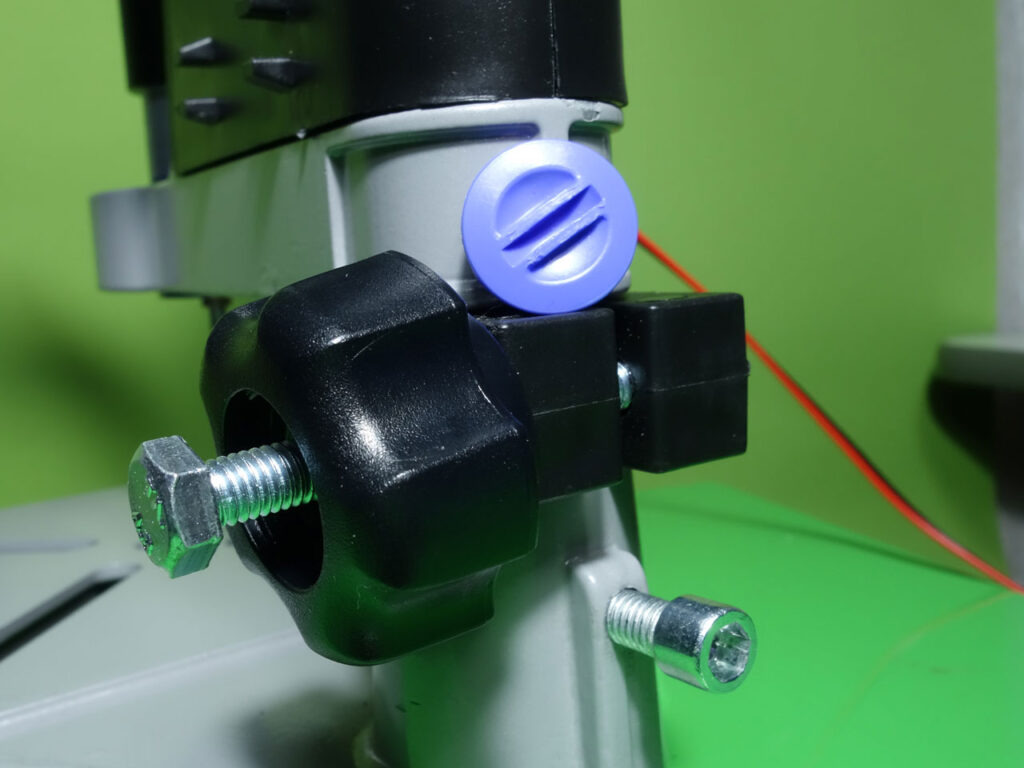
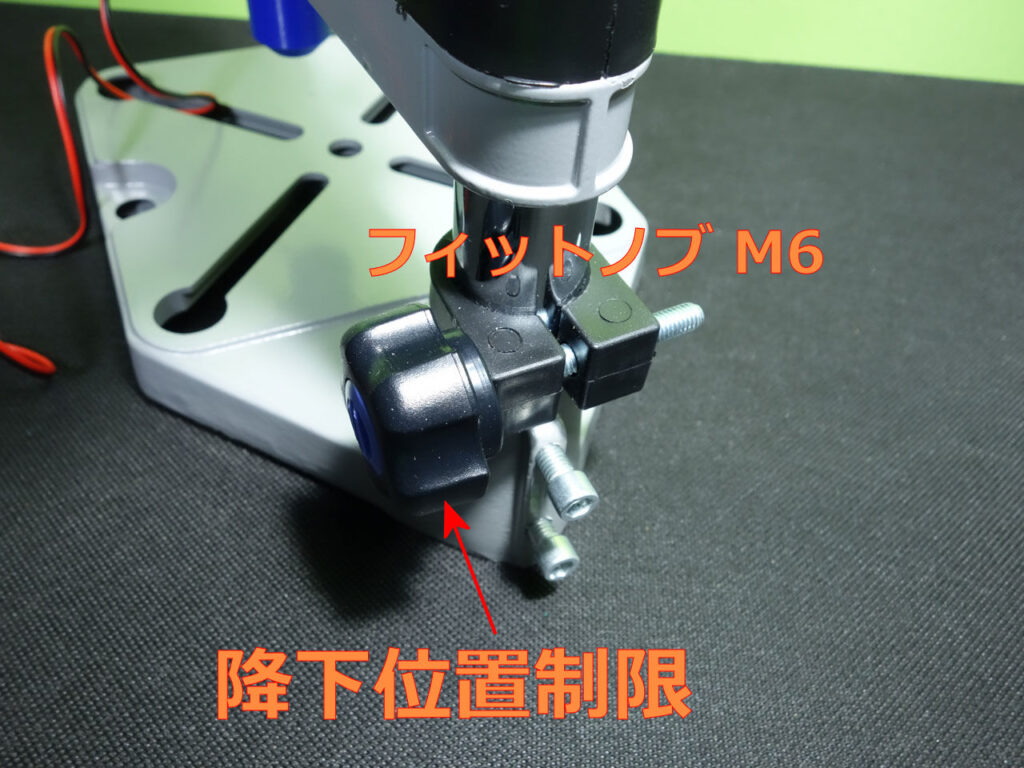
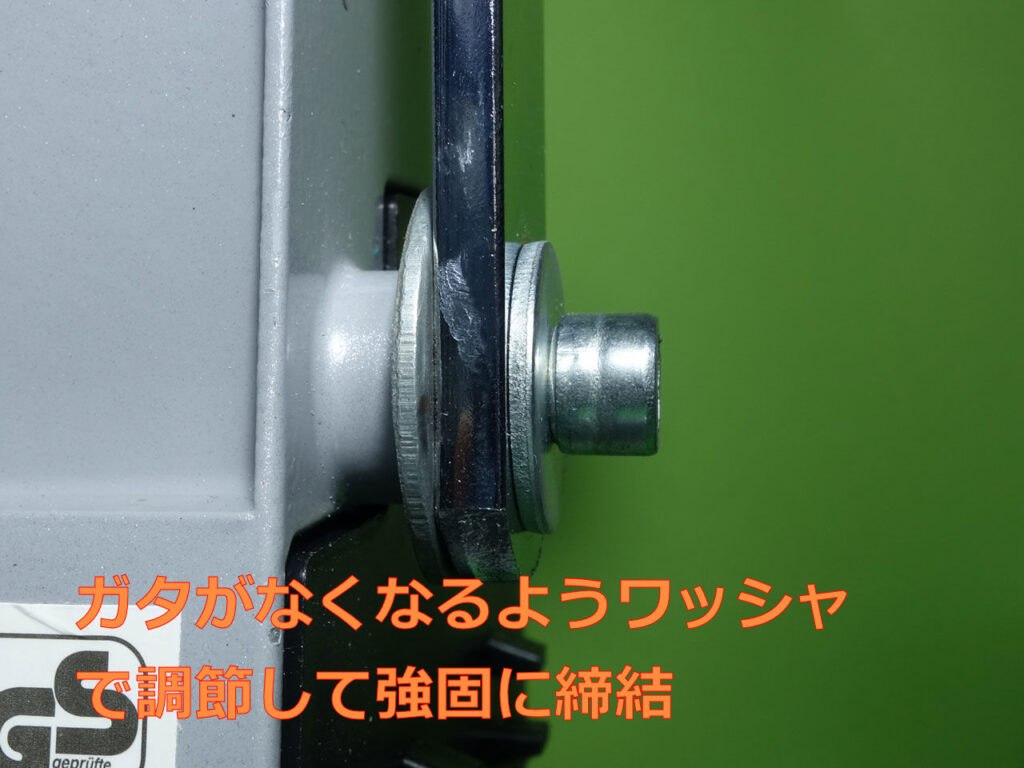
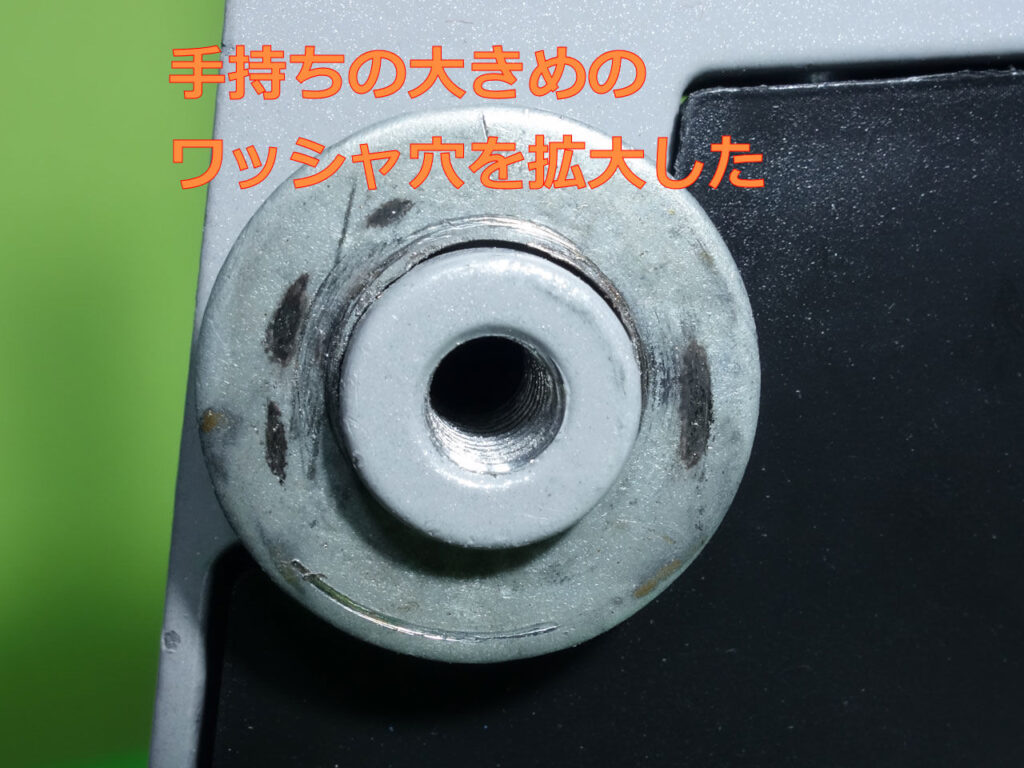

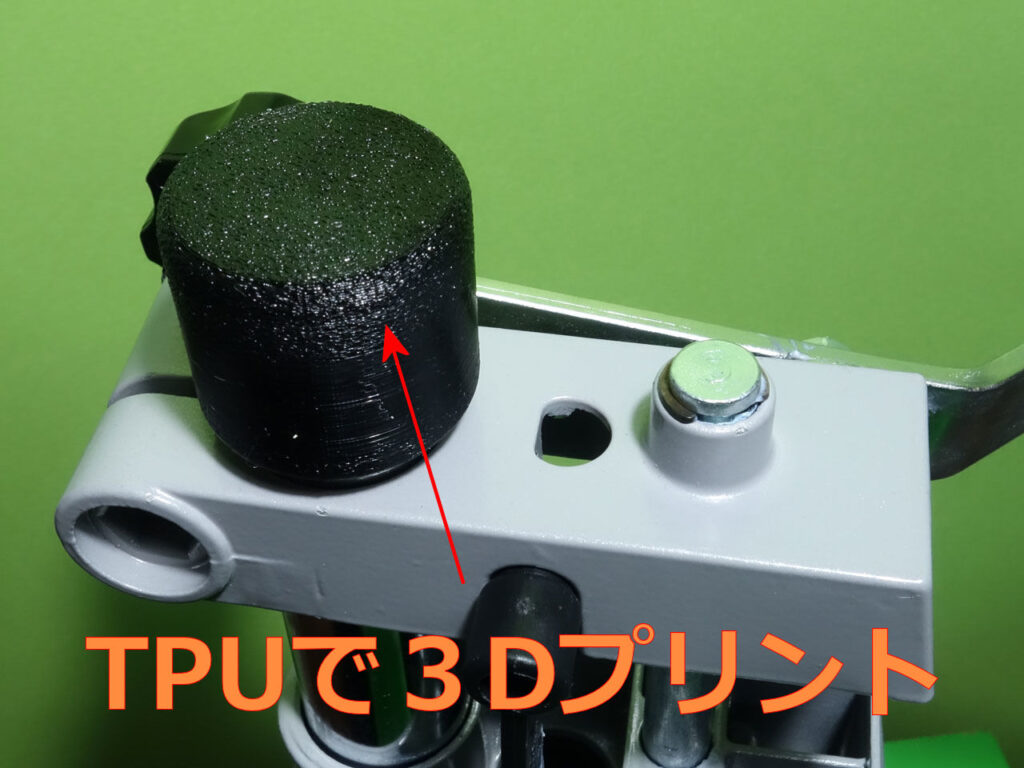
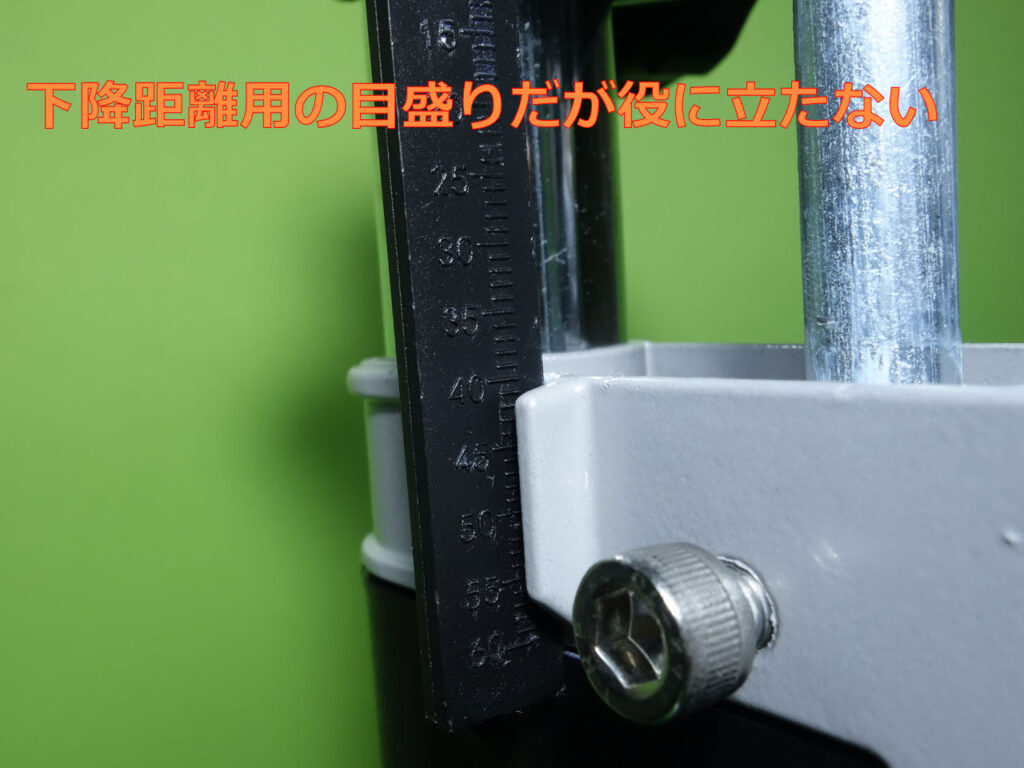
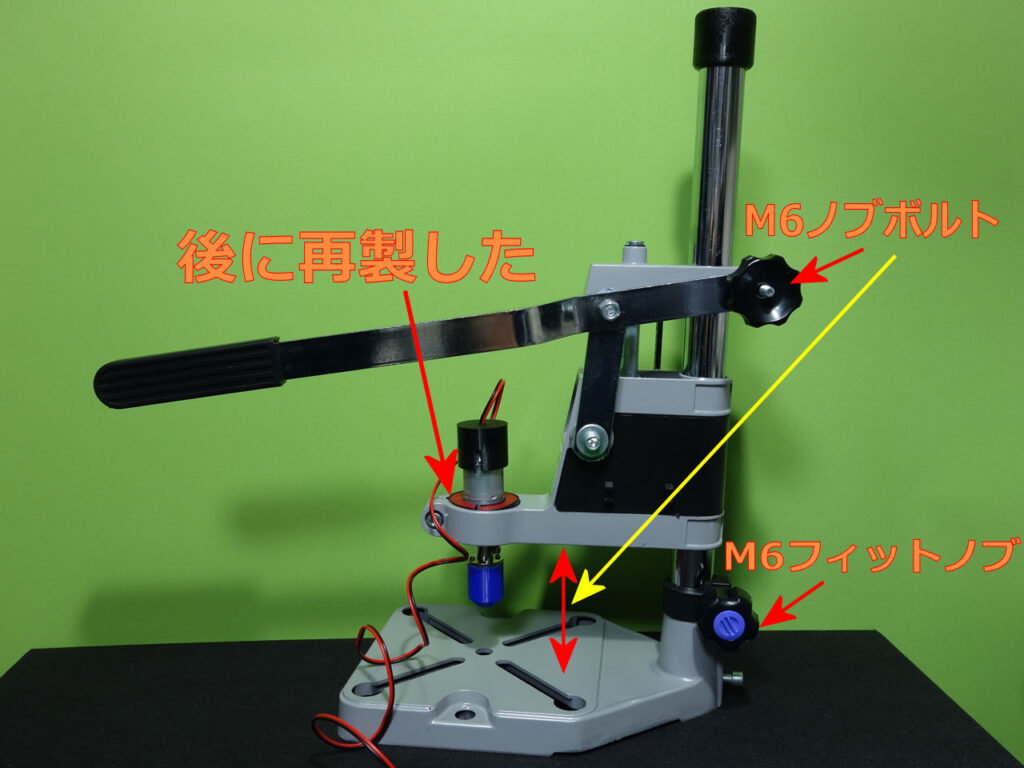
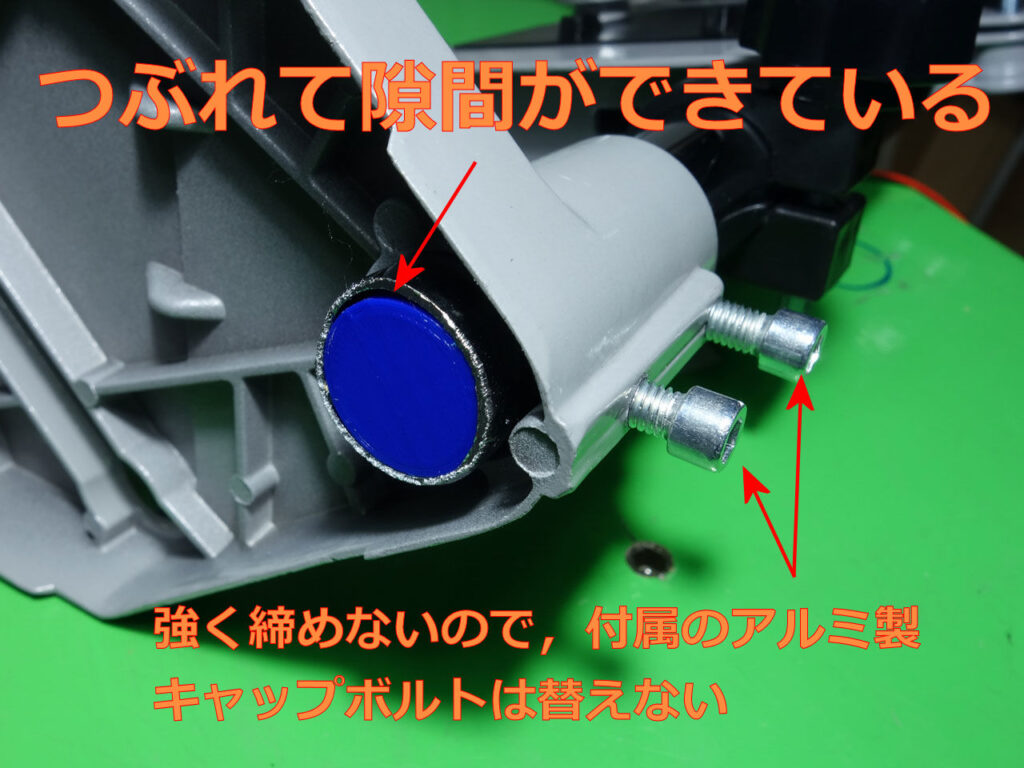
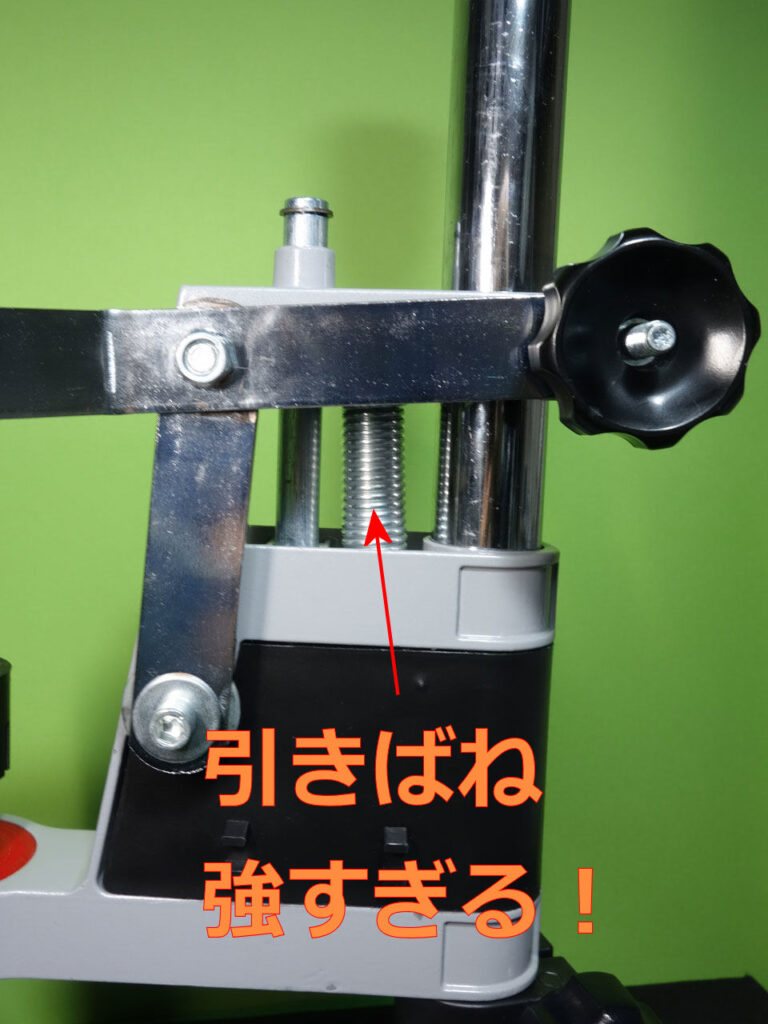
- 前述の通り,Aliexpressでの掘り出し物5点のうち,最初は12V 16r.p.mを選定した
これはPLAでの使用であったため,タップがものすごくよく切れて,もっと早く回転しても問題ないのがわかったので12V 35r.p.m に変更した - Aliexpressの商品サイトにあるスペック表を引用しておいた.電流やトルクがわかる
12V 35r.p.m のギヤダウンユニットのギヤ比/減速比は 171:1 となる
最大トルクはおそらく 13 kgf・cmと思われる.中国語なので想像ではあるが・・・
これは変換すると 1.27N・m となる. - このトルクに近いものとして,ベッセルの電動ドライバーの低回転時のトルクに近いようである.その時の電流は1.5A なので,電源もお手軽である
- ちなみにであるが,”gear” は日本では”ギア”と発音するが,JIS では”ギヤ”となっているそうである.当ブログでは,この記事以降では”ギヤ”と表現する
- ギヤダウンユニットの直径は25mmで,ドリルスタンドの把持部は38~43mmである
- ドリルスタンドの把持部にギヤダウンユニットをセットする際のアダプターを,3Dプリンターで作製した.はじめは調整が面倒なので2ピースとしていたが,その後1ピースとした
- 改良版の1ピースバージョンは,実際に使用した動画とともに後日記事にする予定です
- モーターの端子にはノイズキラーのコンデンサとZNRをはんだ付けしてある
- 切粉でショートしないように,3Dプリンターでカバーも作成した.ちょっと緩かったのでアルミテープを巻いておいた
- モーターとアダプター,アダプターとクランプは両面テープで接着してある.回転に抗するためであるが,クランプにアダプターを取り付けるのはちょっと大変である.粘着があるため滑らせて挿入することが困難となる.そこでクランプの離開部分にマイナスドライバーを差し込んでこじってクランプを開いた状態で押しこんだ.結構力がいる.のちに改良することになる
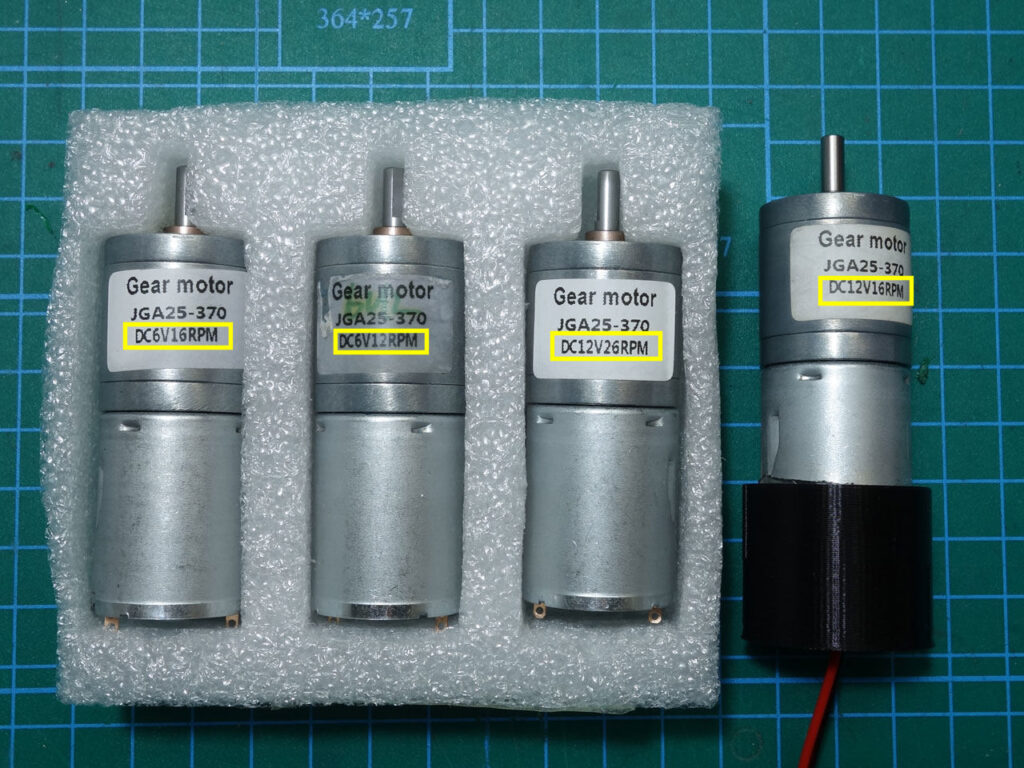
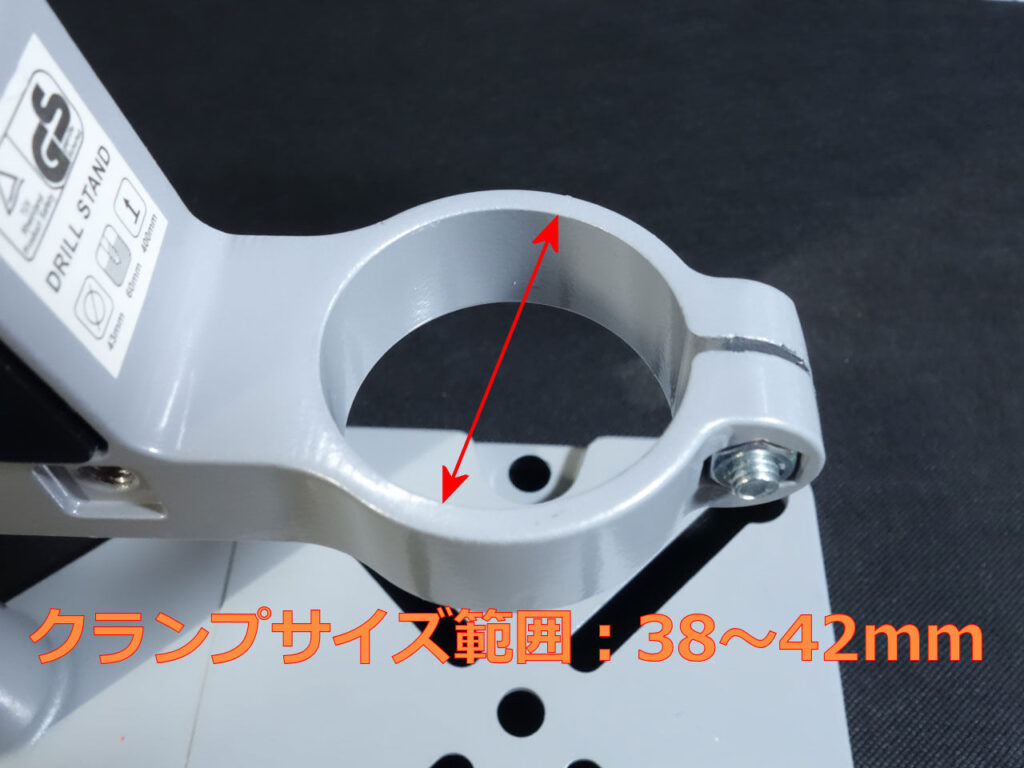
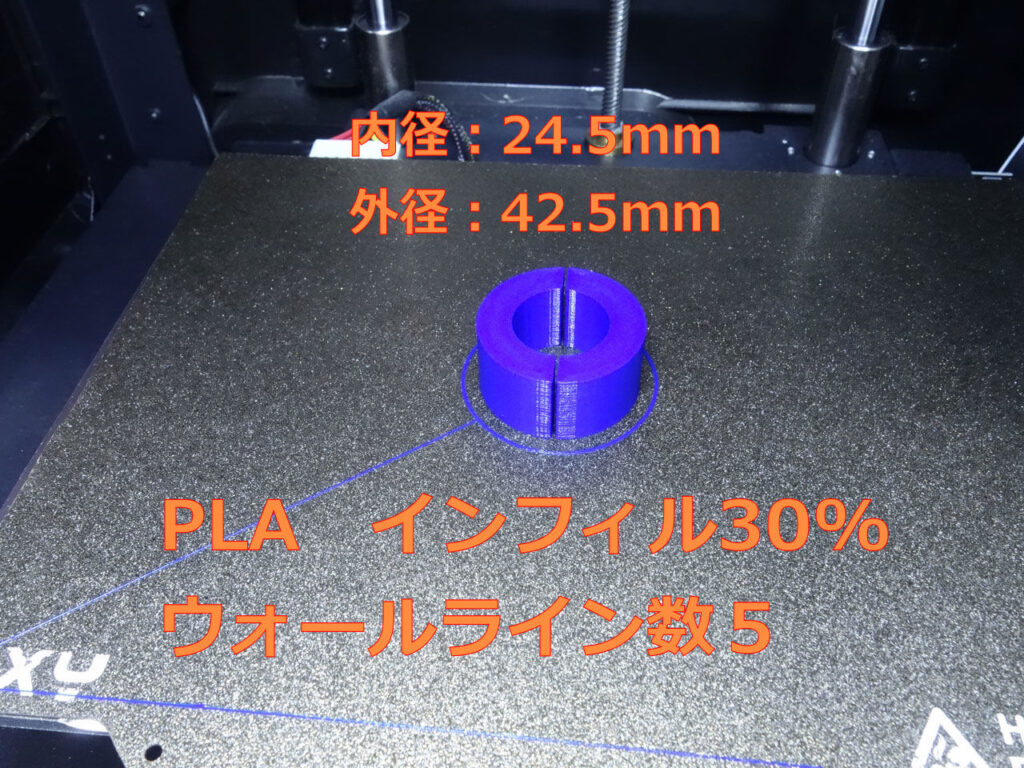
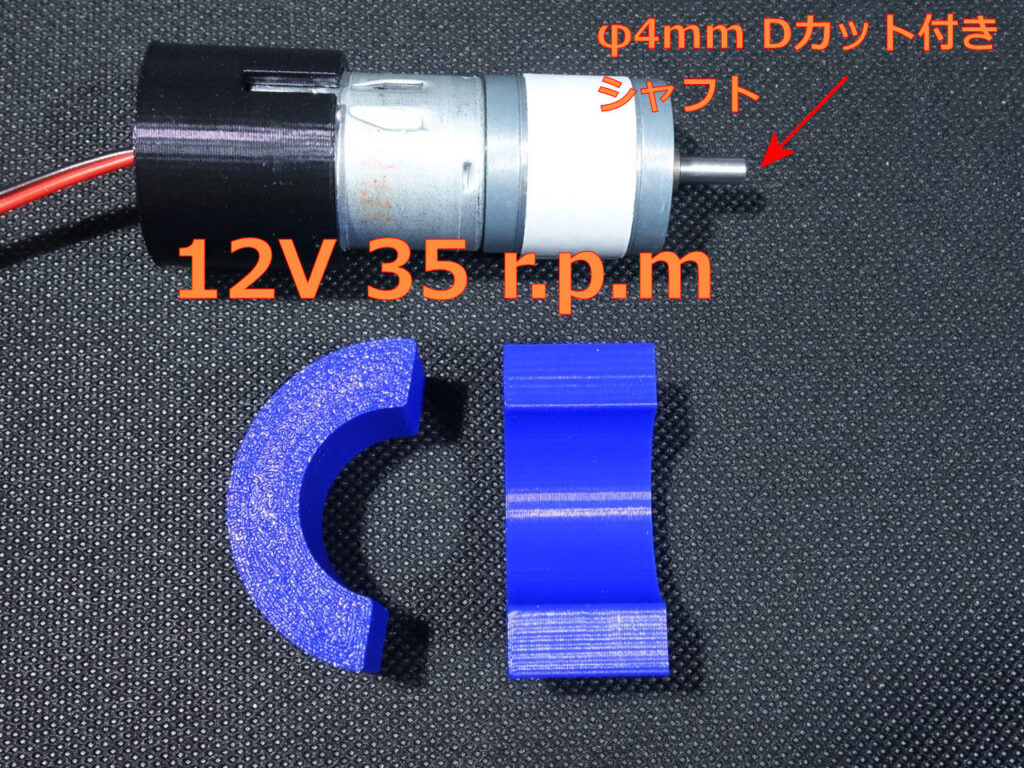
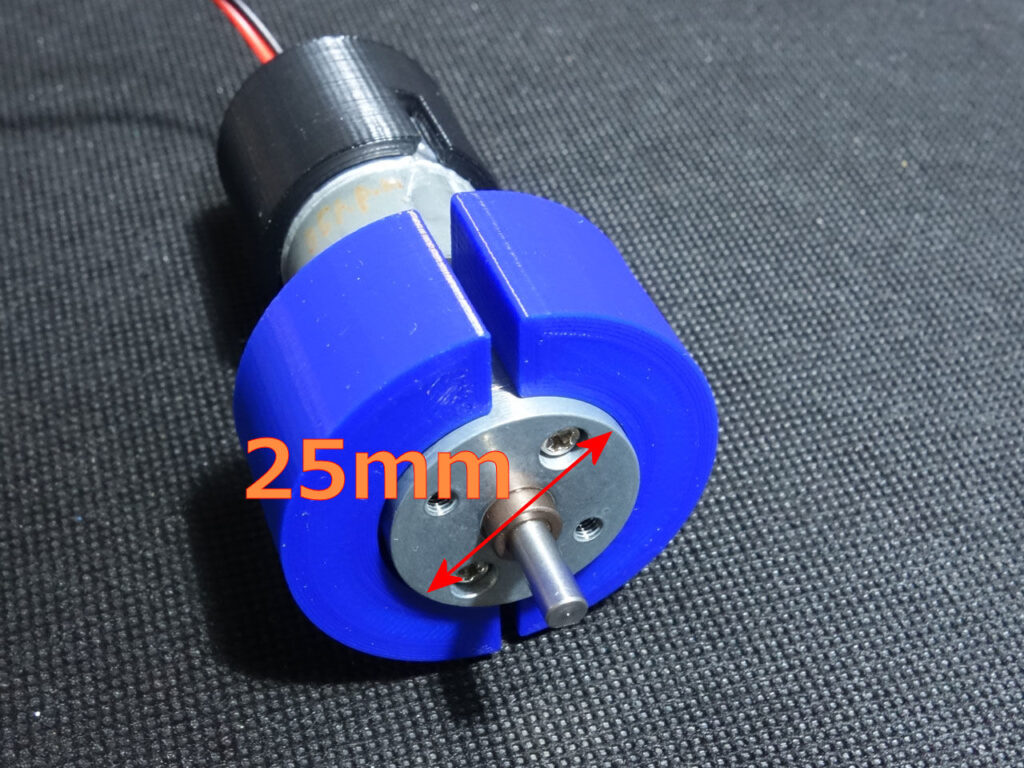
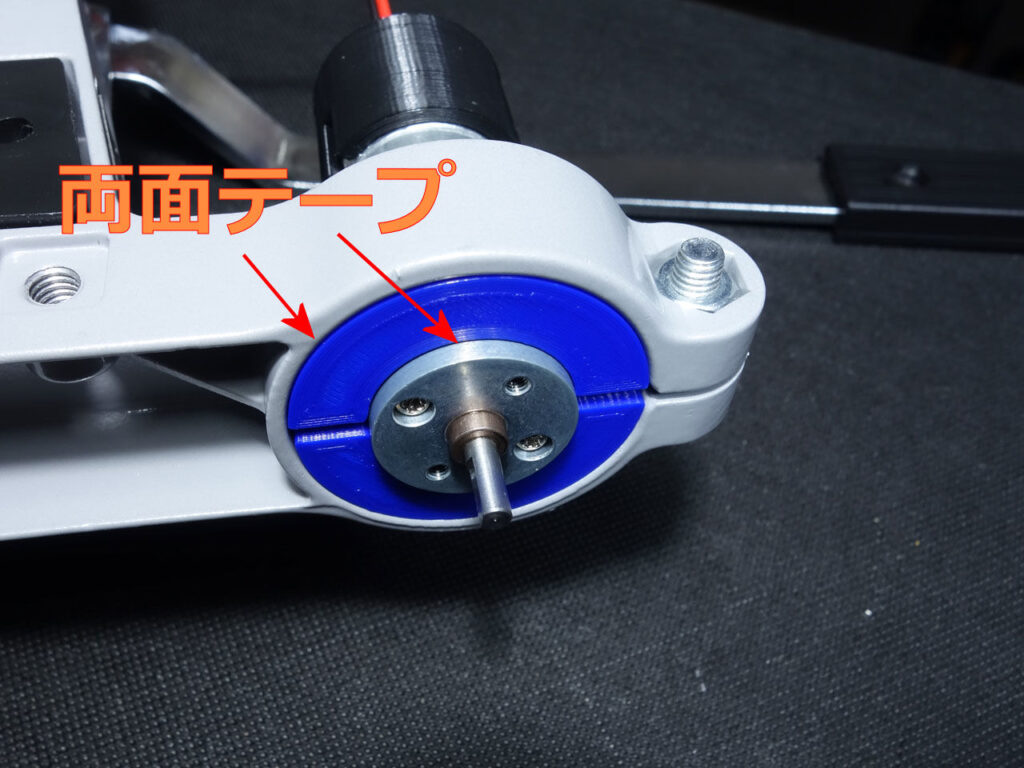

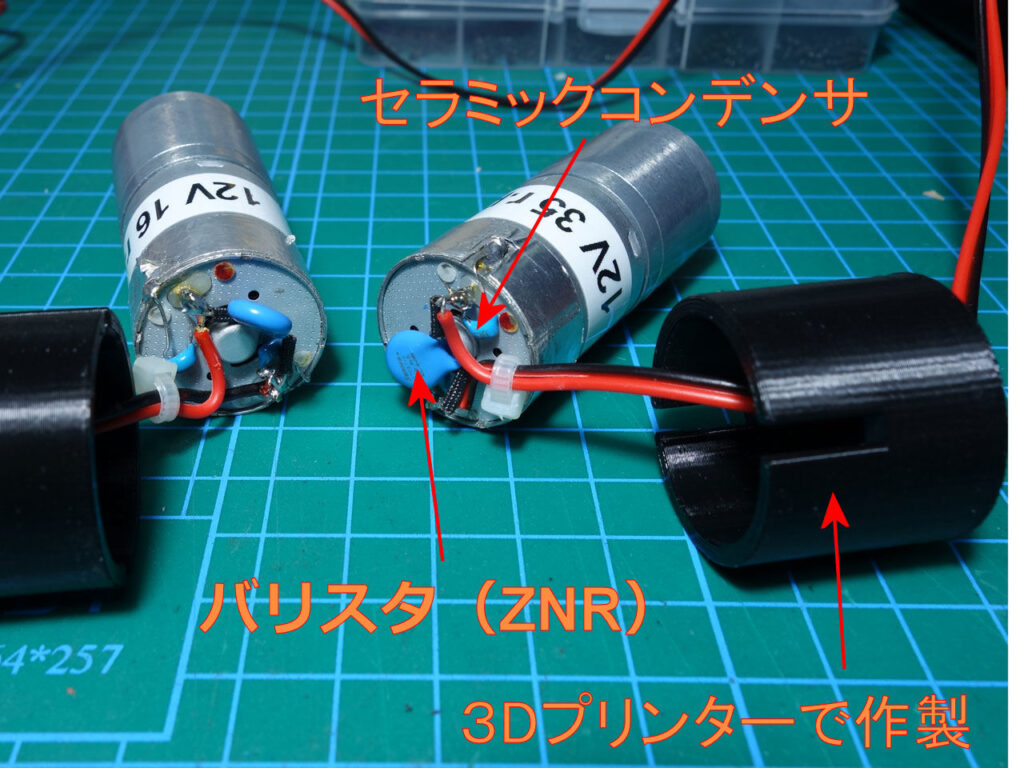
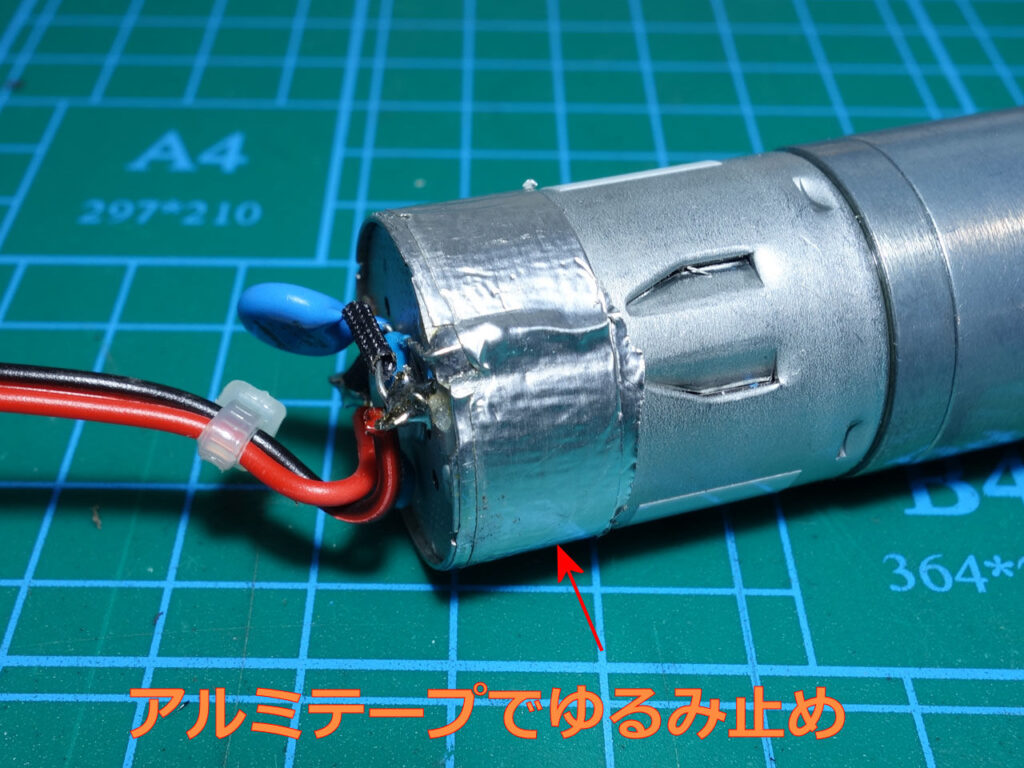
- ギヤダウンユニットのシャフトにタップをセットするためのタップホルダーを作製する.タップをしっかりと取り付けるわけではないの3Dプリンターで作製する
- Fusion360で設計した.断面図を載せておく.タップのシャンク部分(円筒部)と四角部分はいずれもルーズフィットで,容易に挿抜できる.ワークに垂直に食い込ませた状態で容易にタップが抜けるようにするためである
- シャフトの直径は4mmでDカットがある.これが重要である.かなりのトルクを受け止めるため必須の構造である.ここにリジッドフランジカップリングの固定ネジで固定する
付属のネジはM3イモネジであるが,M3x6mm のキャップボルトに変更した - このリジッドフランジカップリングをPLAで印刷したパーツにM2x8mm のタッピングビスで固定した
- このタップホルダーを,M2,M3,M4,M5 のサイズで作製した.
- タップを切るのが難しいのは,ワークがPLAなどのように硬度が強くないものである.また硬度があっても薄物は難しい.タップを切る際の力はいらないのだが,垂直な状態を保持しながら切り込んでいくのは困難なのである.そんな時このツールは役に立つ
- アルミの厚物などでは,タップを食い込ませた状態でハンドルを上げると容易にタップが垂直になった状態で取り出せる
- その状態のタップにタップハンドルをセットして,タップを切っていく
動画を公開予定だが,タップの刃がしっかりついている部分の15mmぐらいなら,アルミブロックでもタップハンドルは必要なくそのままタップできてしまった.いろいろなワークに使い分けできそうで楽しみである
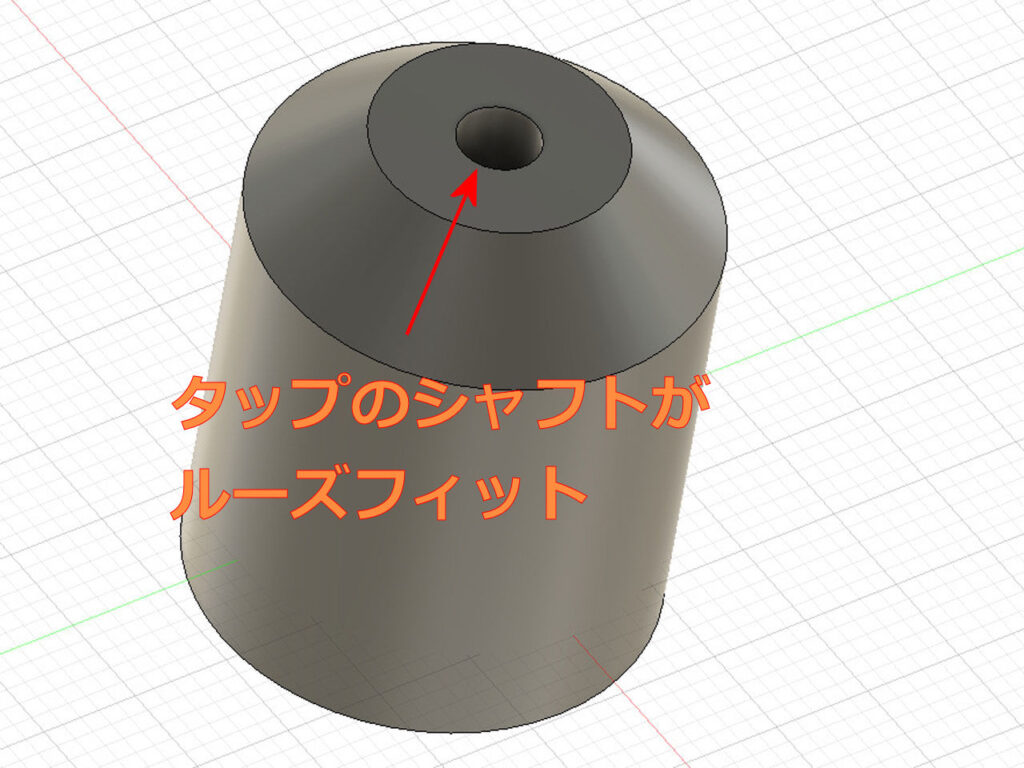
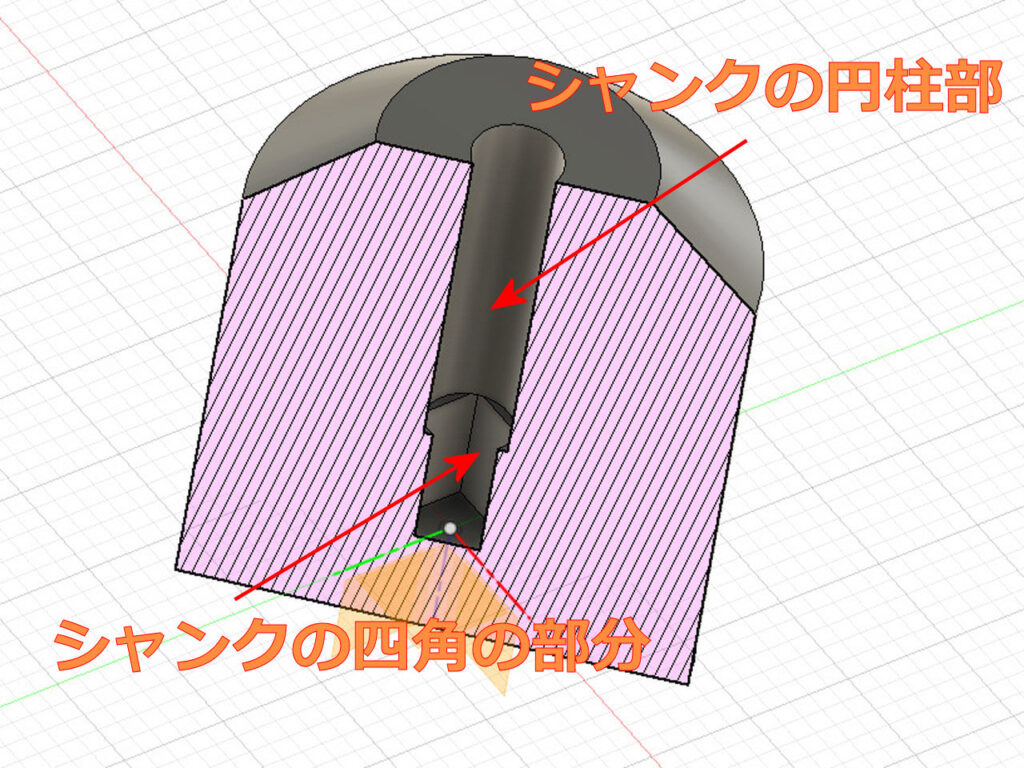
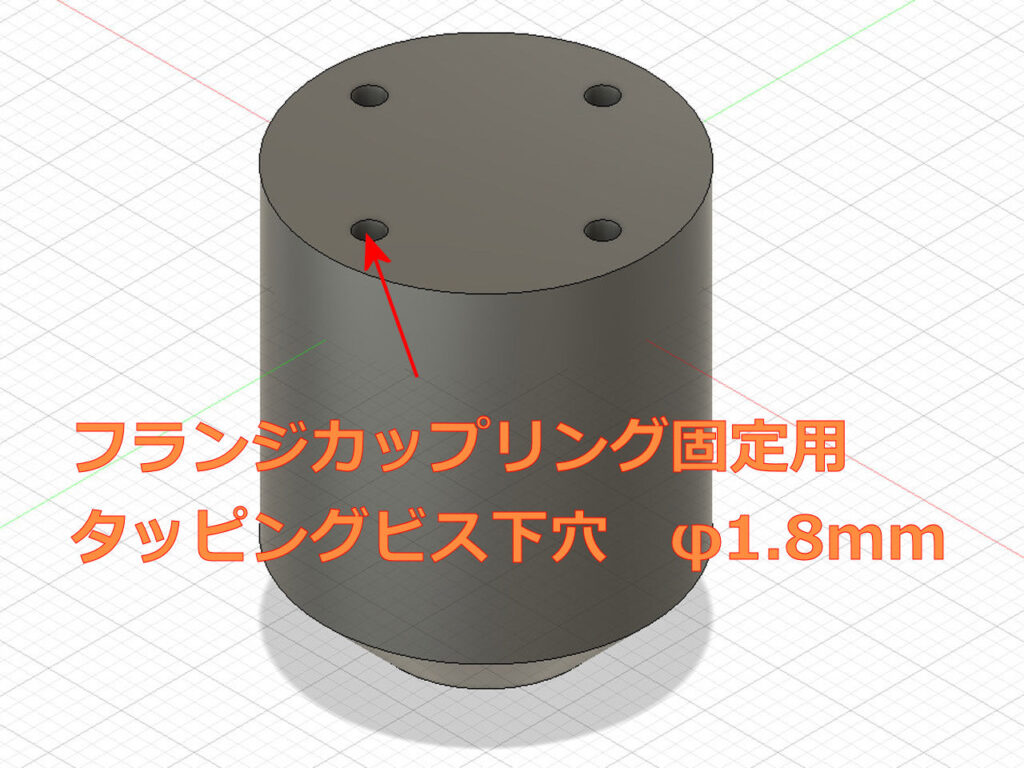
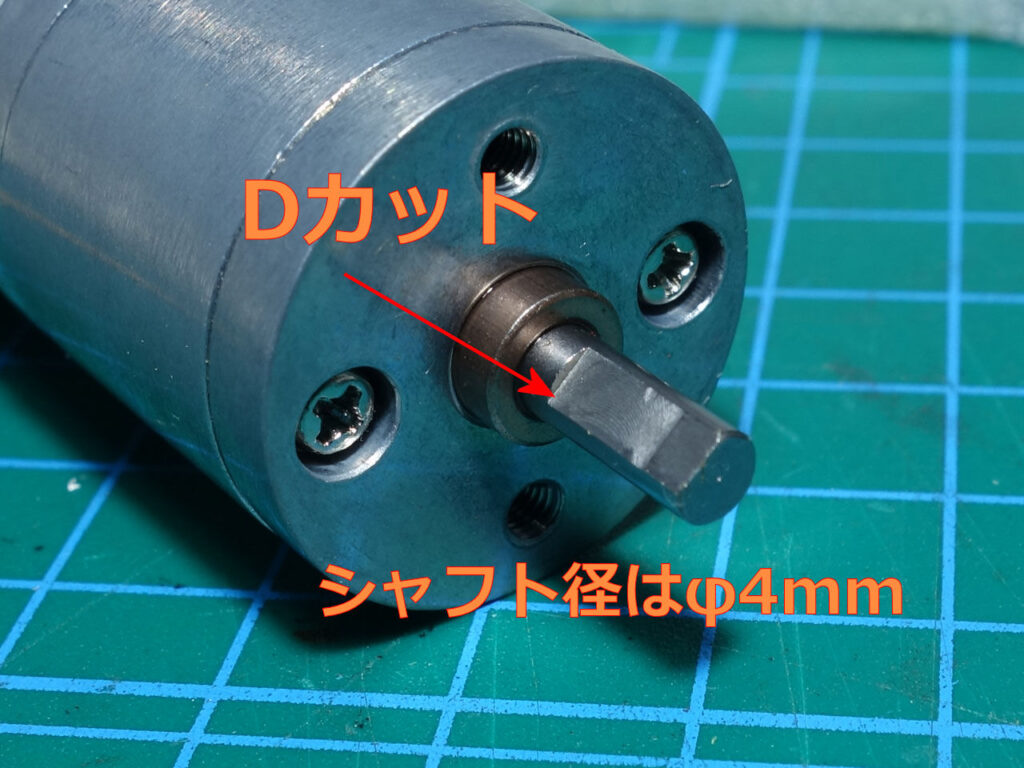

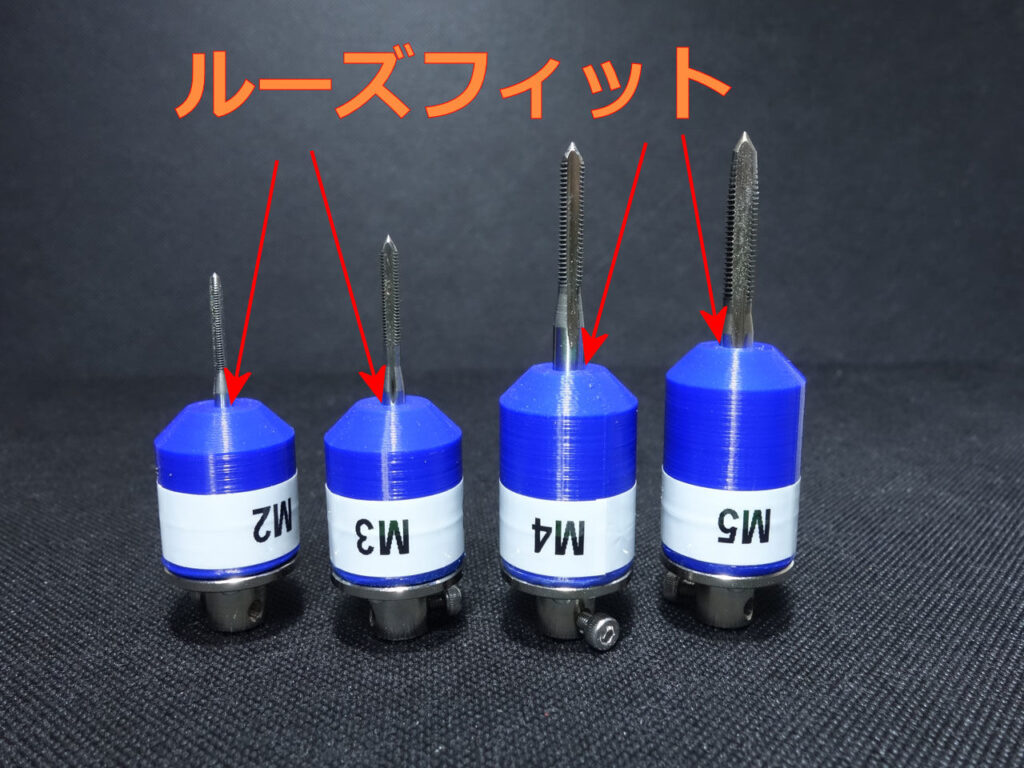
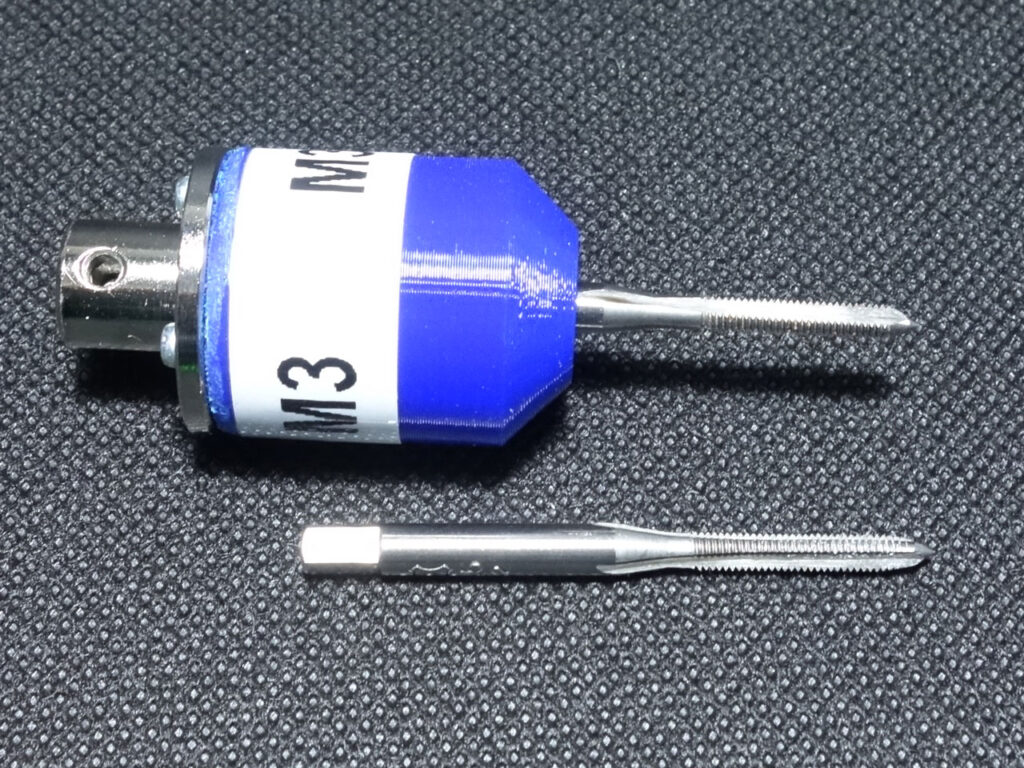
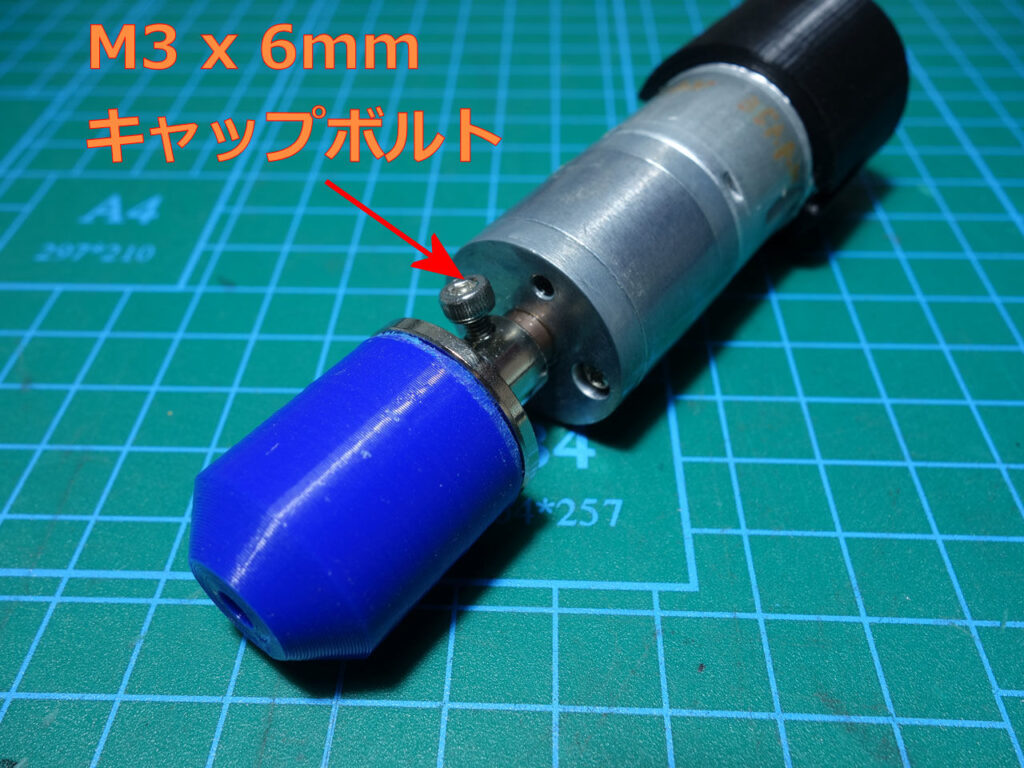
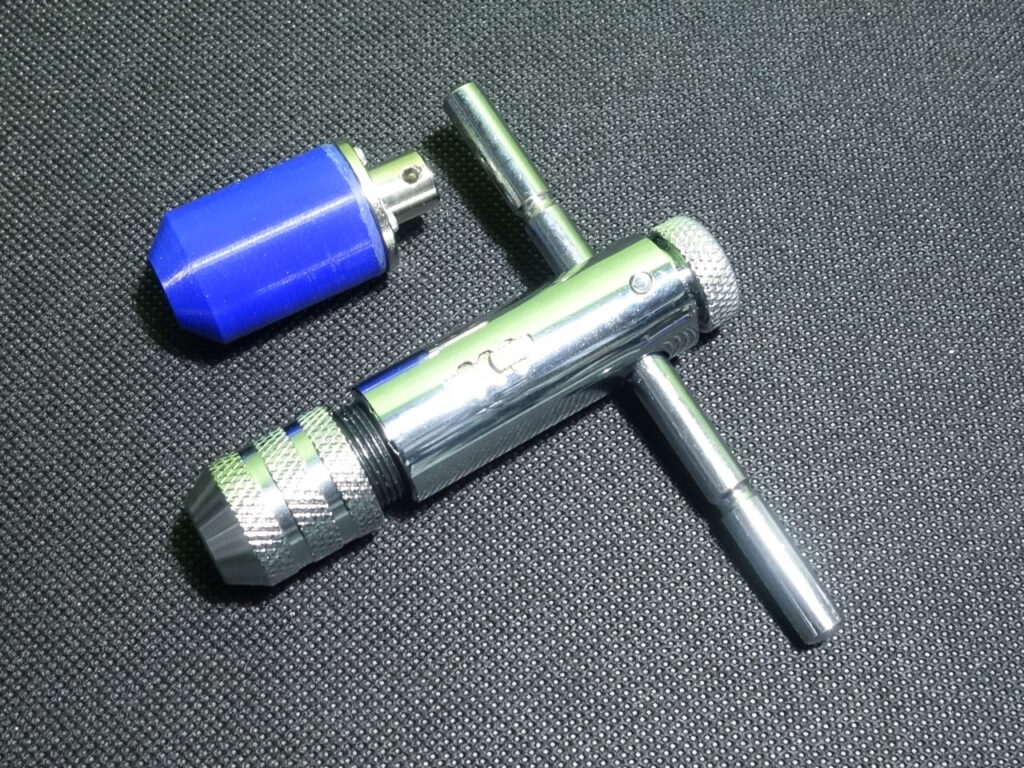
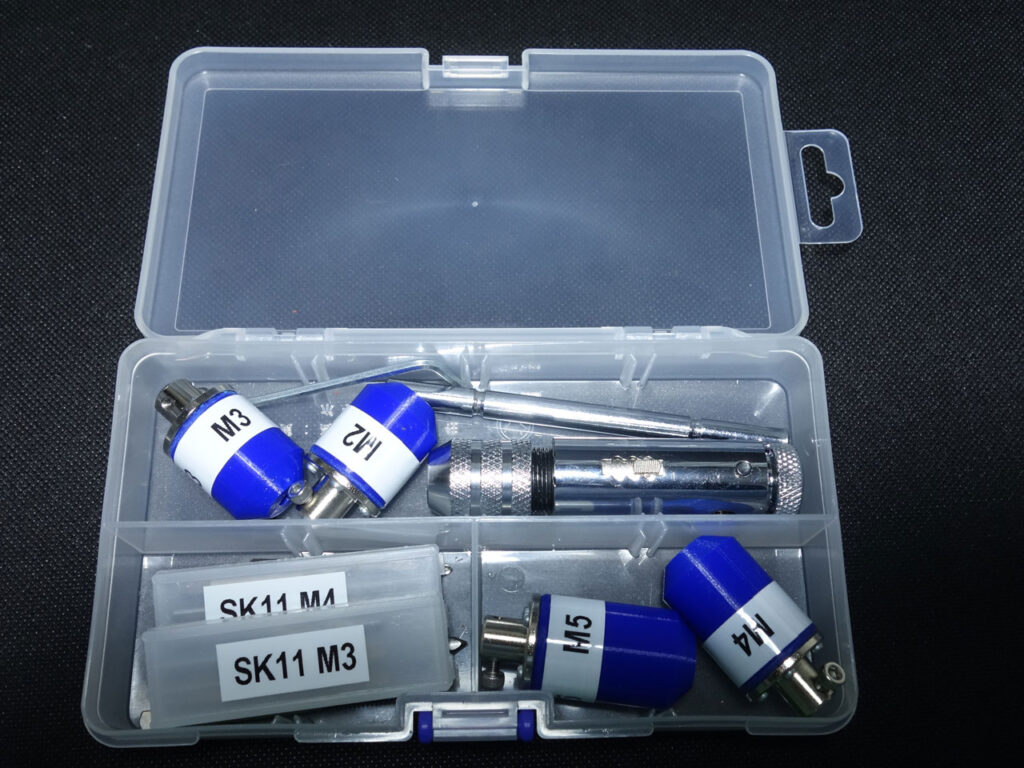
- 華奢なスタンドゆえ,作業台に固定しなければならない.スタンドのベースはの厚みは1.5mmで重量も軽い.固定は必須である
- ベースには固定用の穴が開いている.おそらくはM8のボルト使用だと思われる.しかしドリルスタンドとしての使用ではないため,M6のキャップボルトとワッシャで固定することにした
- 作業台の天板のコンパネに,M6のインサートナット(鬼目ナット)を取り付ける.下穴はφ9mmのドリルで開けておく.インサートナットにはつばなしとつば付きがあるが,今回はつばなし/M6x13mm を使用した
- インサートナットもできるだけ垂直に取り付けたいので,垂直ドリルスタンドで下穴を開けた.このスタンドはφ10mmのドリルまで対応のチャックがついているため何かと使えるがこのままでは使いにくいので改良してある
- 使用した電動ドリルはマキタの10.8V使用のもの.私の用途では大きなトルクは不要なので軽くてリーズナブルな10.8Vシリーズを愛用している.
- インサートナットの取りつけはトルクがいるので,マキタのインパクトドライバーを使用した
- 最初はM6キャップボルトを,穴からずらして使っていたがさすがにみっともないので代替えのボルトを,近くのホームセンターで見つけてきた・ワッシャとスプリングワッシャが取り付けてあるもの.プラスネジだが使い勝手がよい
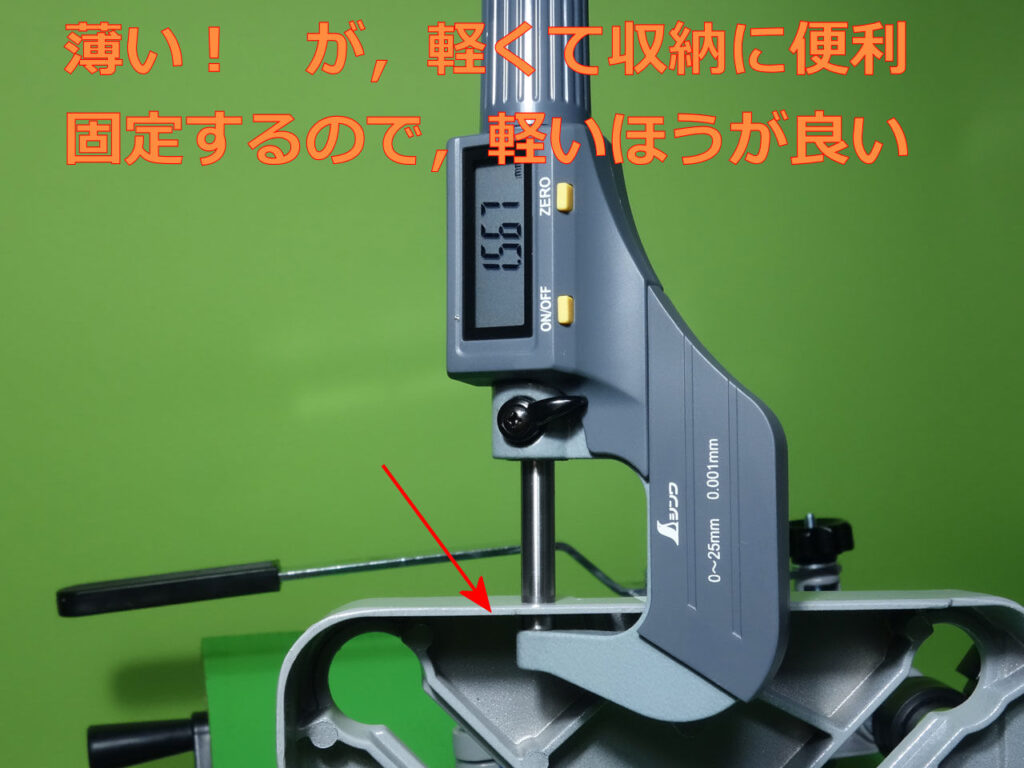
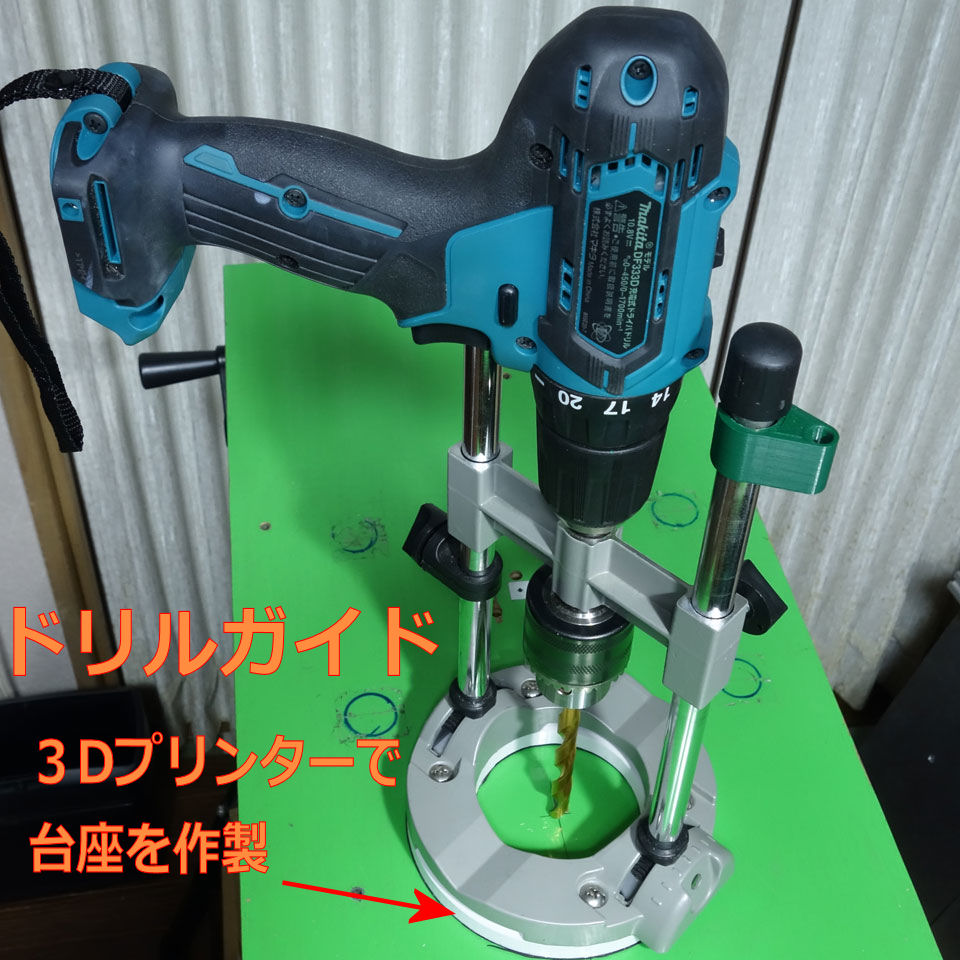
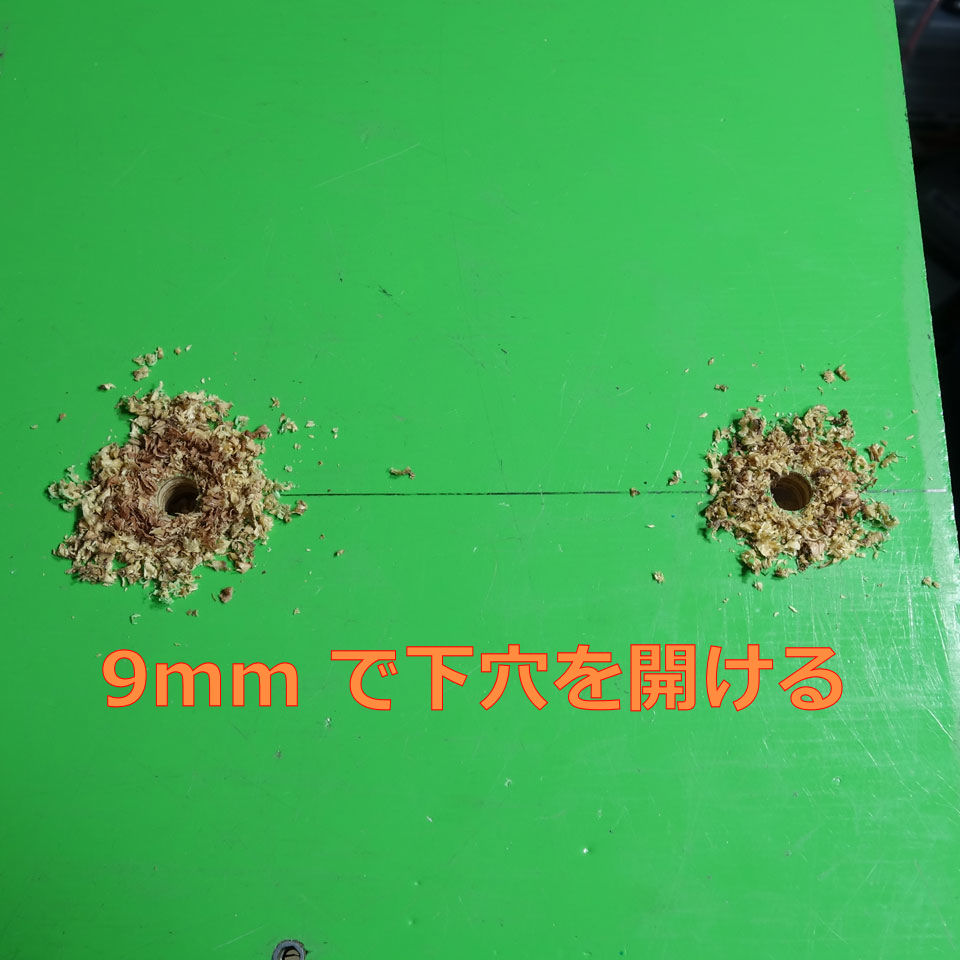

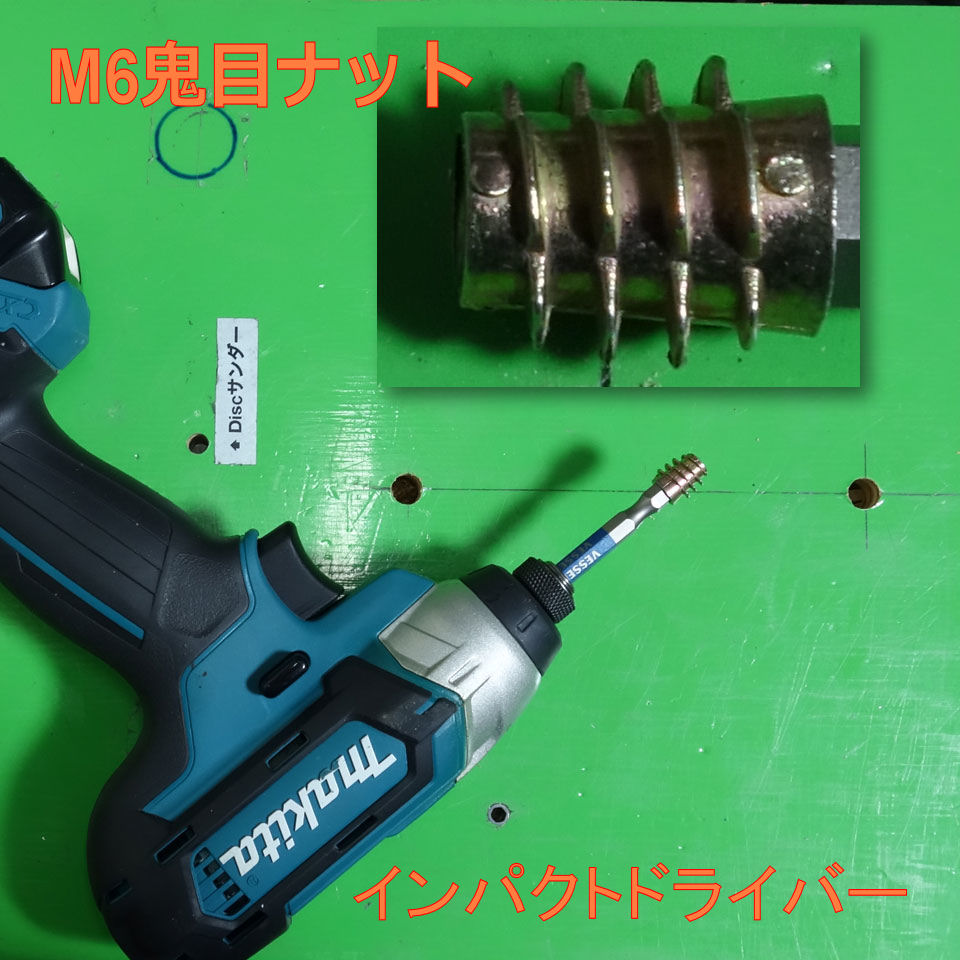
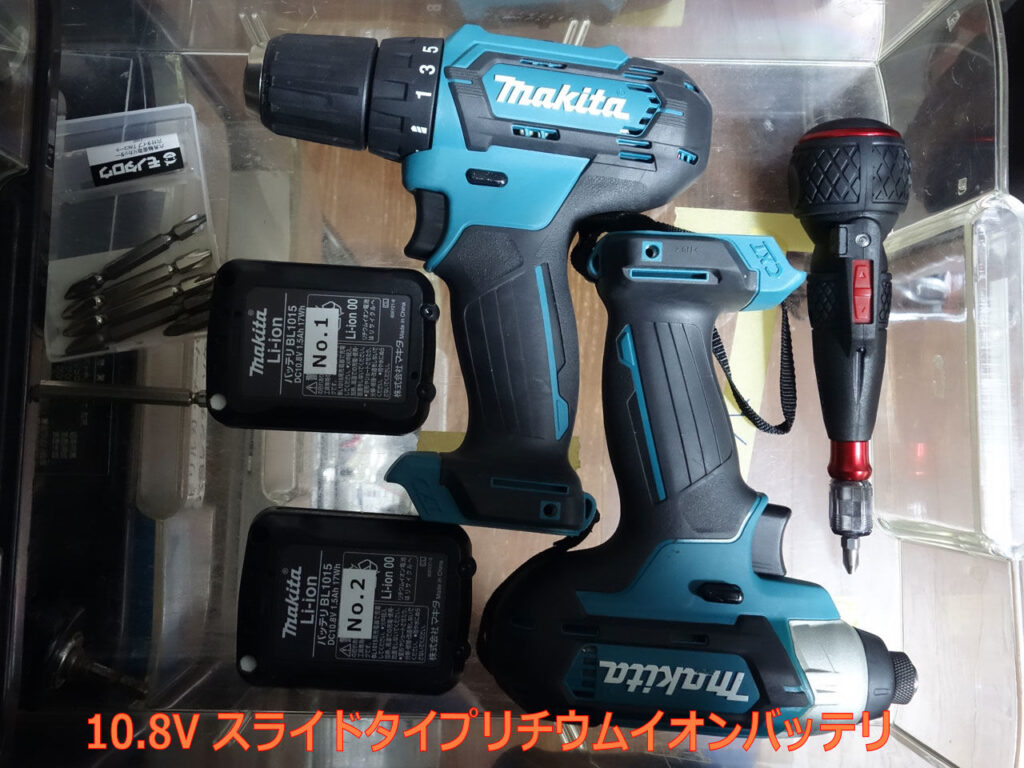
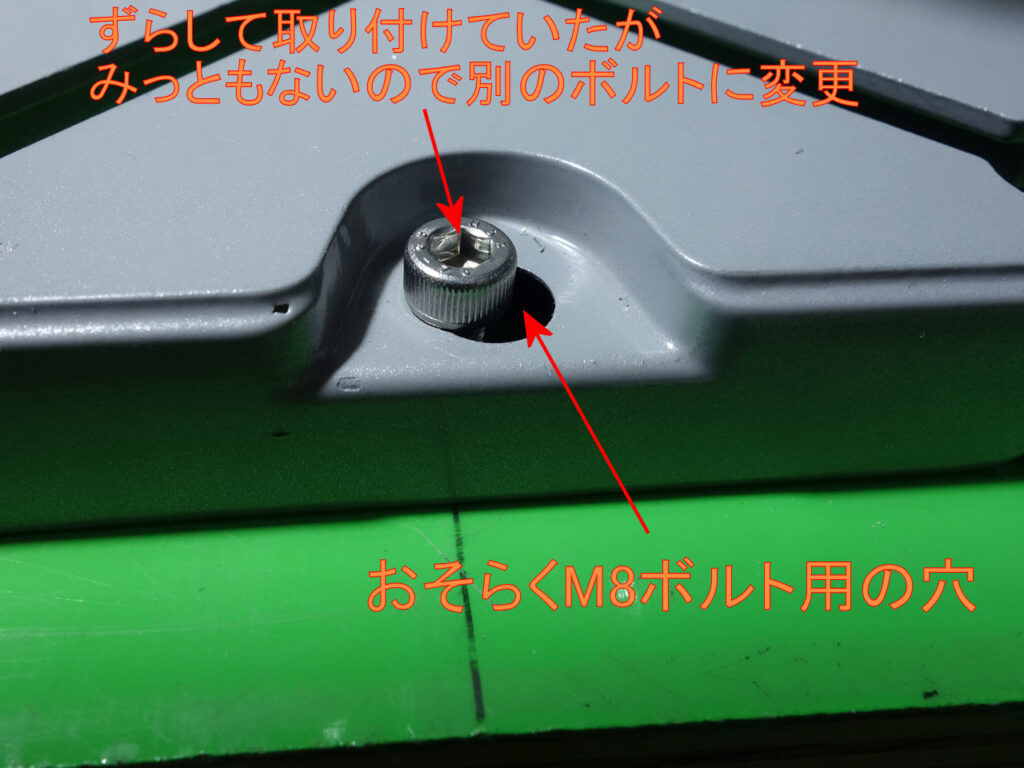
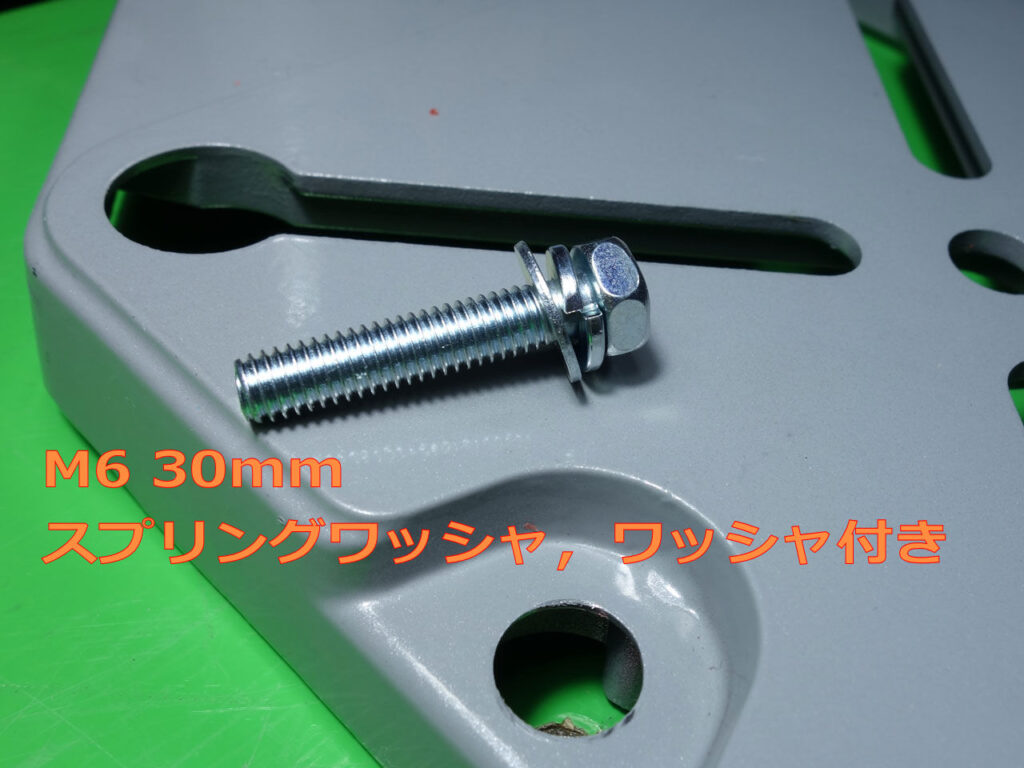
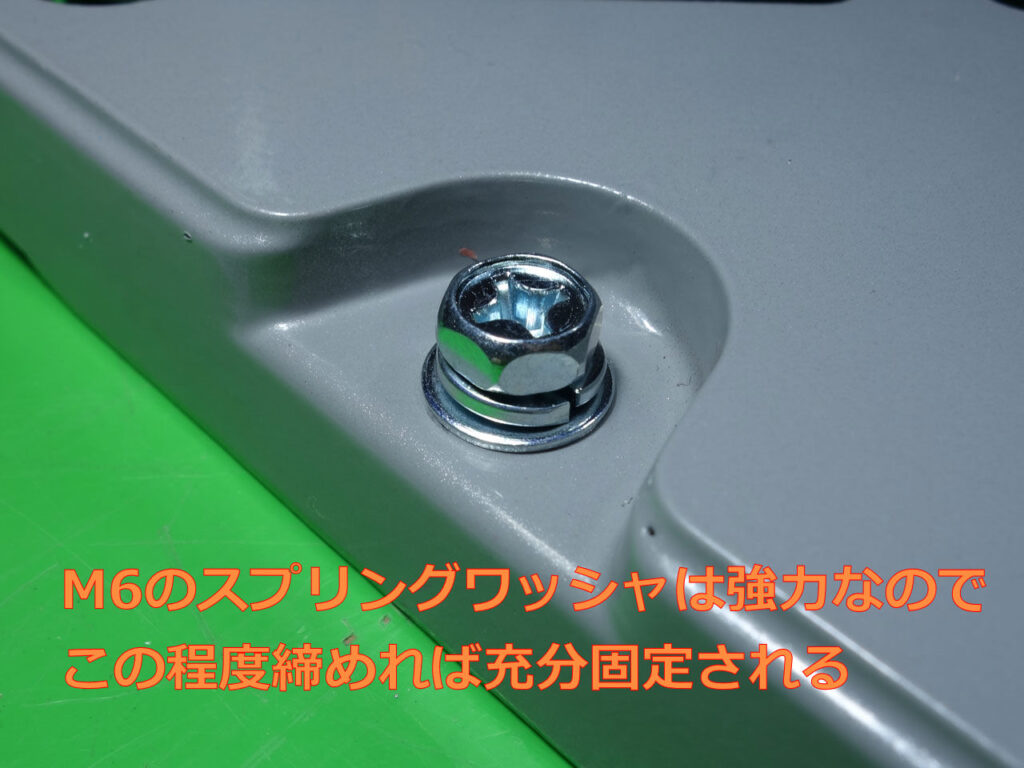
- このツールの全景を載せる.当工房の工作機械は24Vと12Vのスイッチング電源を使用している
- ちなみに24Vの電源はnanoテーブルソーに付属していたものを使っている
12Vはnano旋盤とnanoフライス盤用に購入したものである - リレーのON/OFFの切り替えはリレーON/OFF用端子に24Vを印可するかで行うが,この端子にフットペダルを通して24Vを接続している.この回路は低電流で駆動可能である
- フットペダルは交流のスイッチングを想定したものらしい.いろいろな商品のスペックを調べてみたが,直流で大電流をスイッチングできるものはなかった.直流をスイッチングすると大電流が瞬間的に生じるため,接点が持たないらしい
- 今回のような負荷がモーターの場合はフライバック電圧が生じて,大きな電流が瞬間に流れるのでフットペダルでON/OFFするのは避けるべきである.特にギヤダウンユニットのため大きなトルクがかかったままでON/OFFするのでモーター単体より注意が必要なのではないだろうか
- そこで,24Vのスイッチングといえば,車載機器用リレーである
- 24Vのスイッチング電源出力(モーター駆動用)は,アルミケースに収納された車の電装用の80Aリレーへ入る
- スイッチング電源には24V出力が2系統あるので,モーター用とリレーON/OFF用は簡単に別回路で使用できる
- ギヤダウンユニットは12Vなので,スイッチボックス内でDC-DCコンバータで電圧変換している.変換後は2回路2接点のトグルスイッチを通してギヤダウンユニットへ電力を供給する
- トグルスイッチはモーターの回転方向を反転させている.配線方法はいろいろあるが今回はこちらのサイトに載っている方法がわかりやすいと思う
- スイッチボックスは3Dプリンターで作製している.最近マイブームの作製方法で底板をビス止めする方法である.ビスはM3x8の皿ビスを使っている.今後はこれに統一しようおと考えたため,たくさん入って¥910のこれを購入した.
- 本来皿ビスなので皿穴加工が必要だが,なくても使えるので皿ネジは便利である
Fusion360で設計時に皿穴のスケッチをかけるように勉強した - トグルスイッチには切粉が入りそうなので防水キャップをつけている.nano工作機械関連でトグルスイッチを使う場合はこれを使用している.単純な2ピンのON/OFFのものである.防水キャップのために購入したということになった.まあ,ちょっとした用途には便利なサイズなのでいいかなと.手持ちで同サイズの他のトグルスイッチにも使えてしまうことが多かった
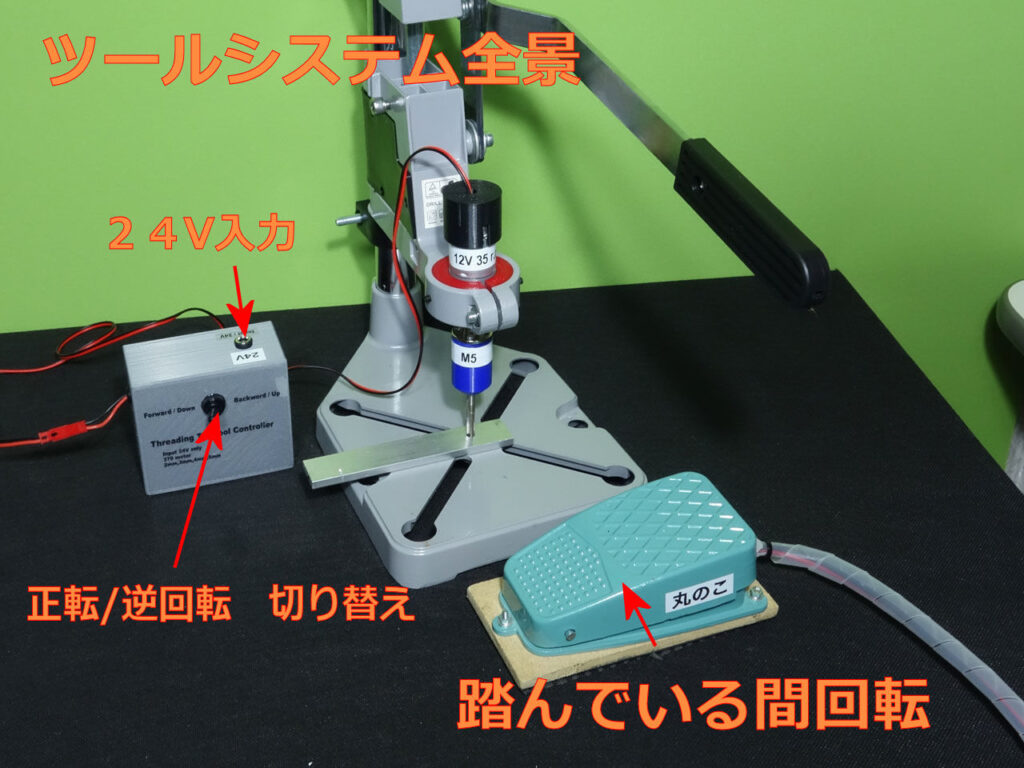
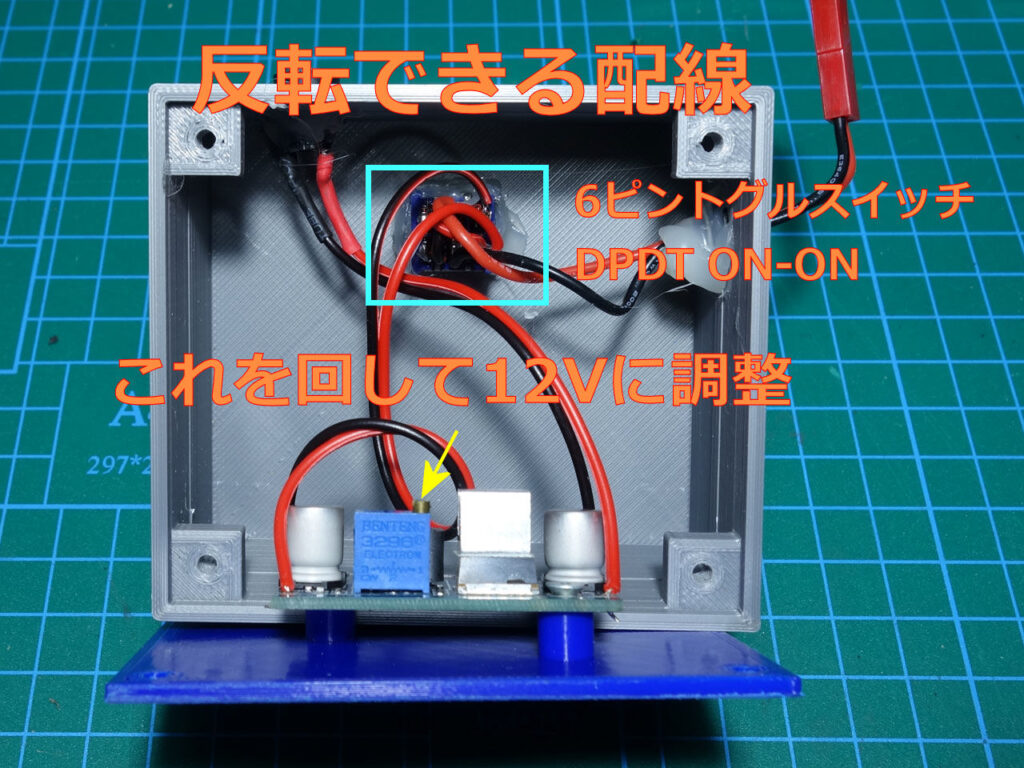
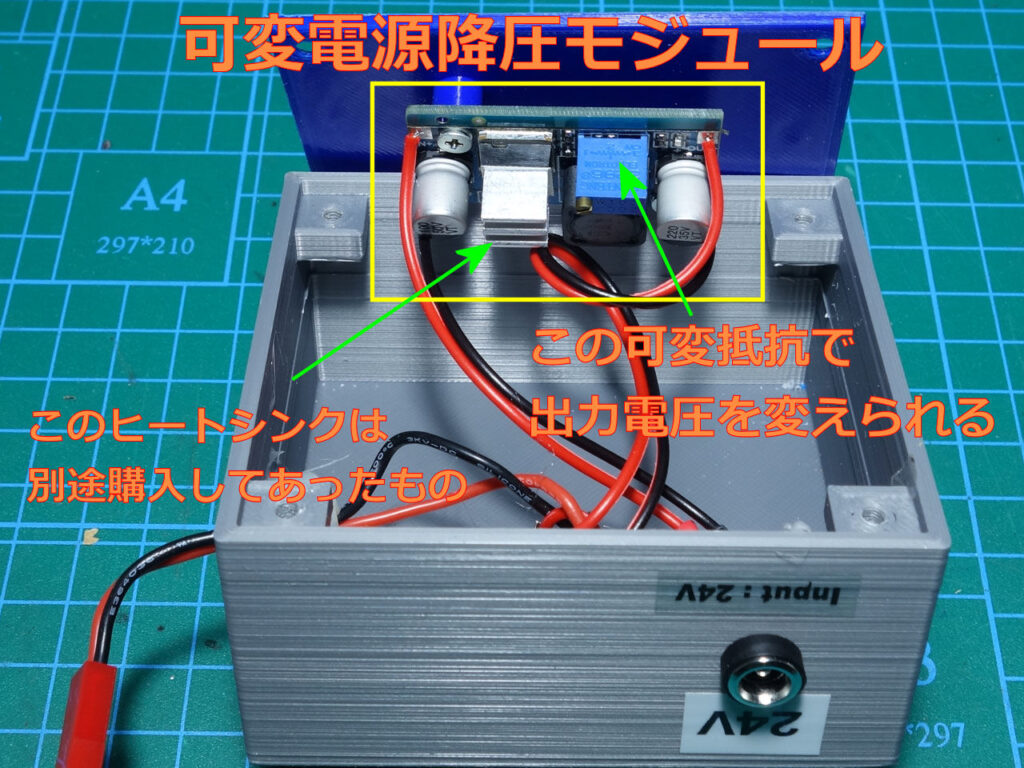
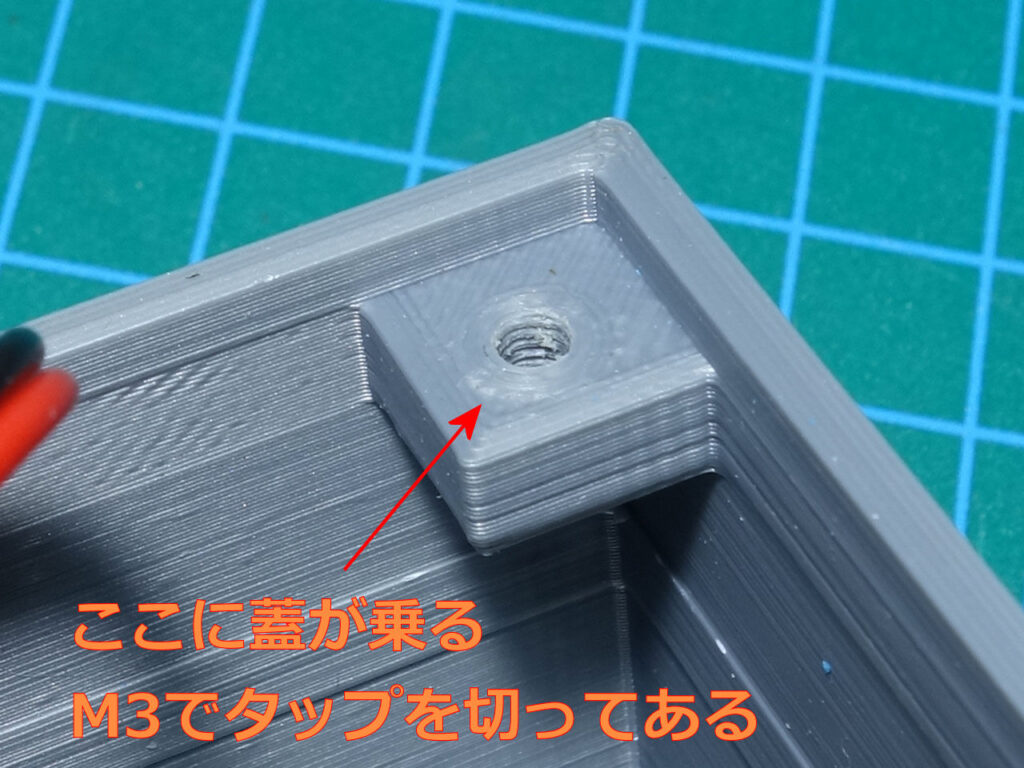
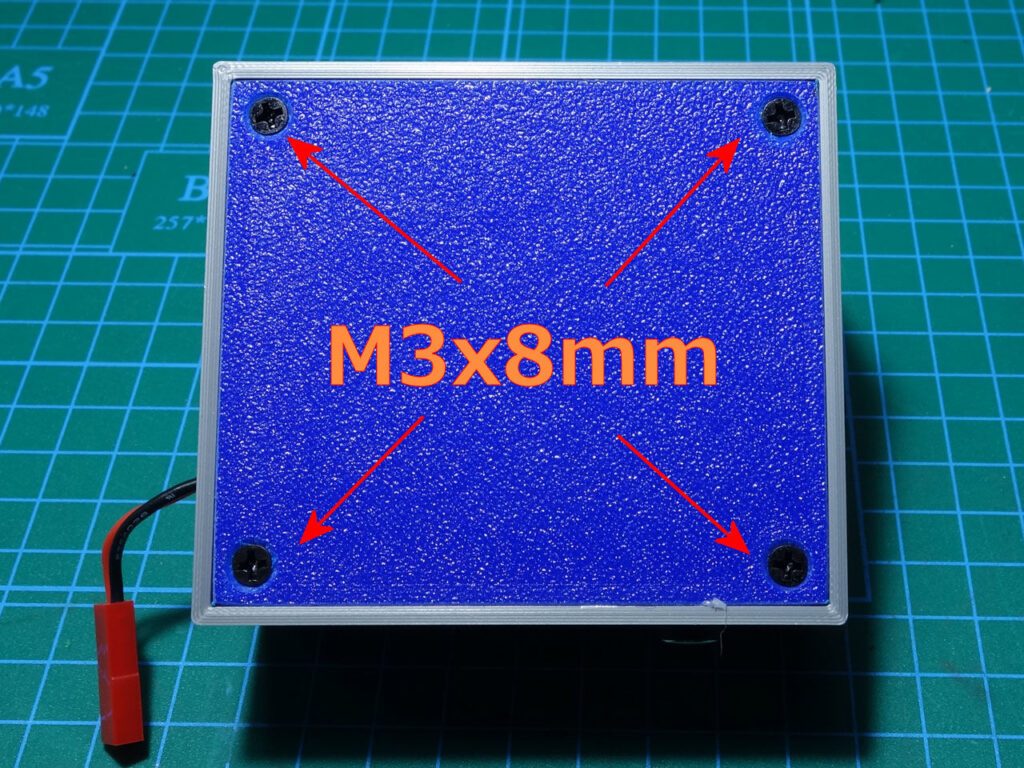
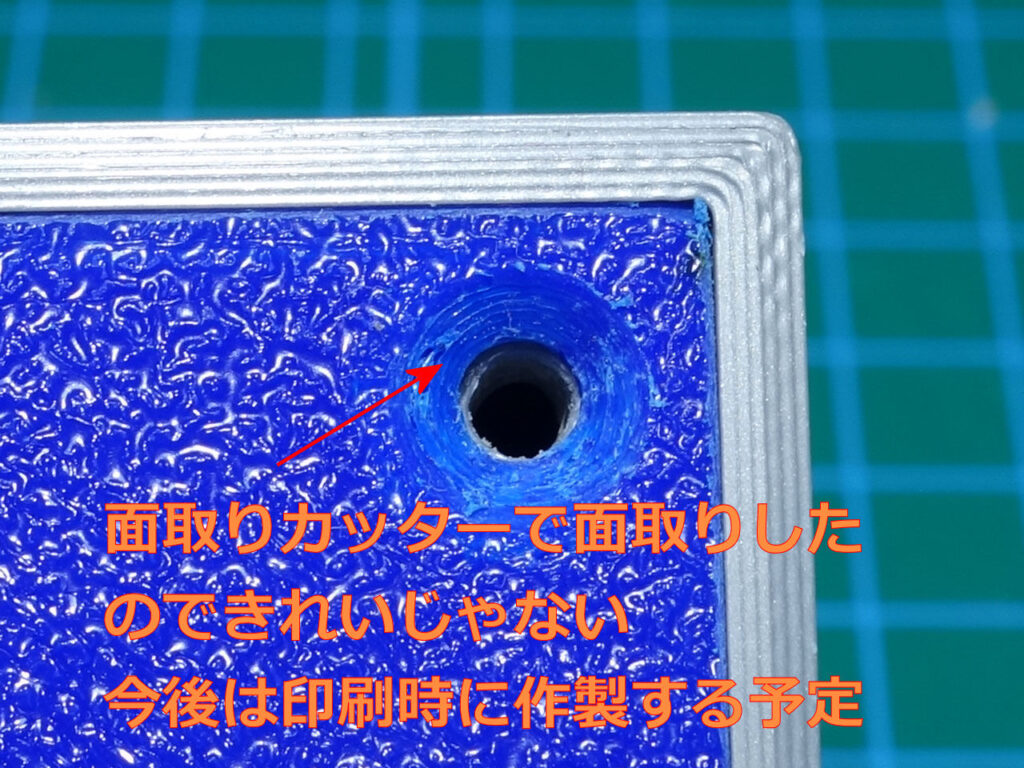
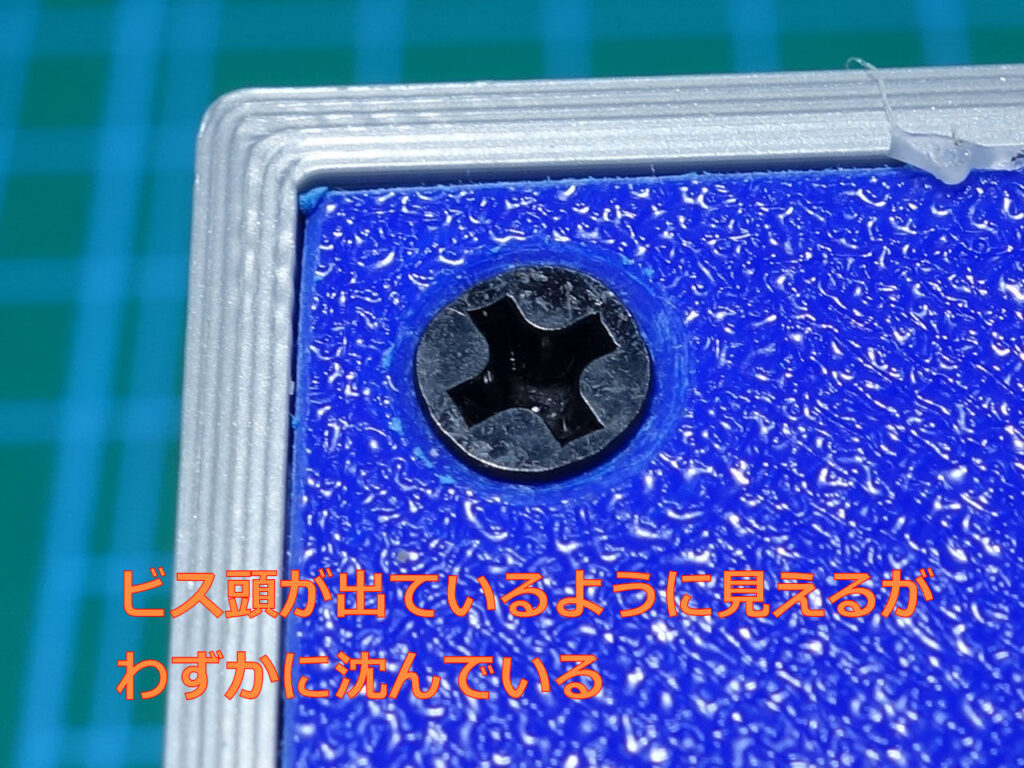
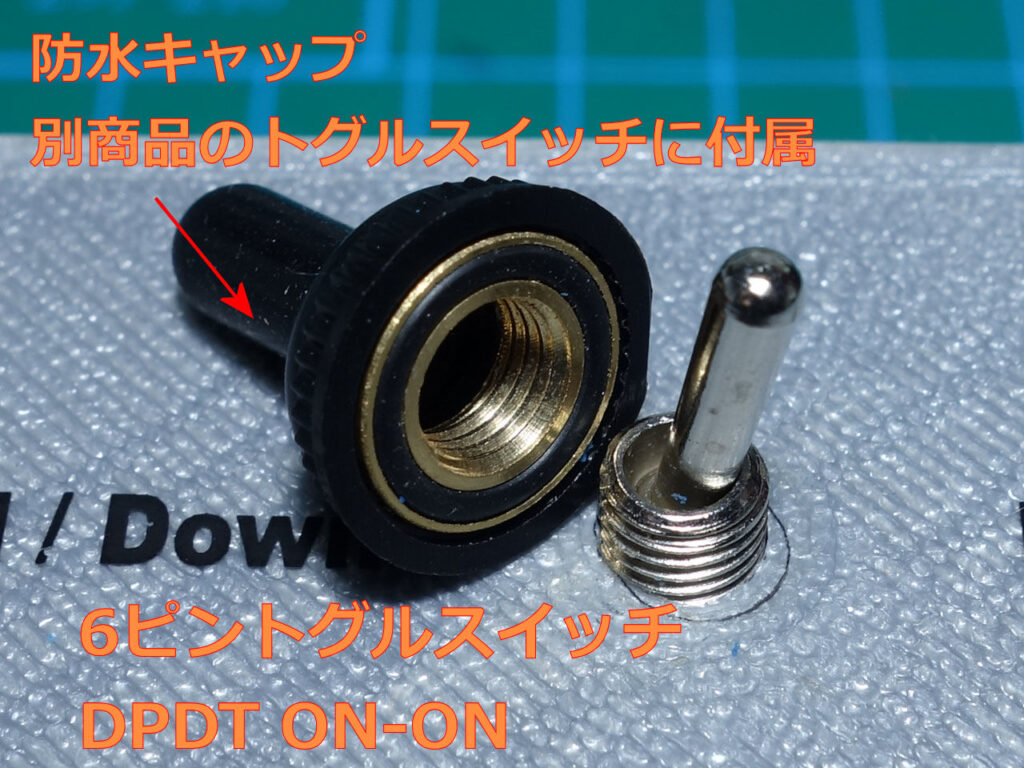
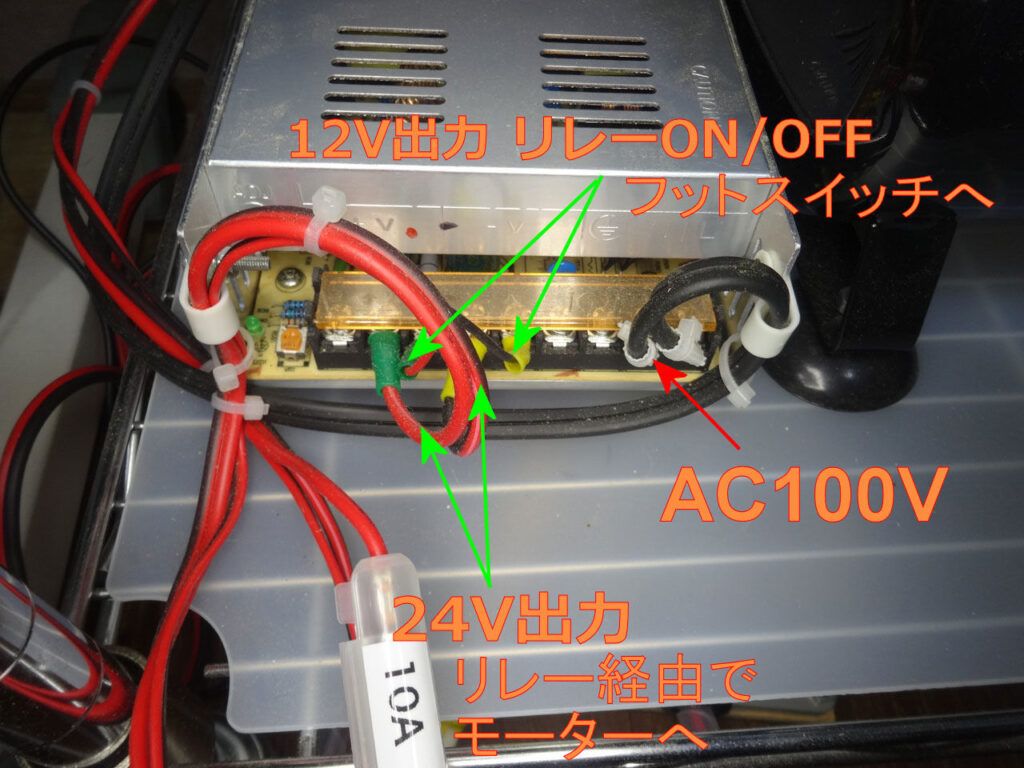
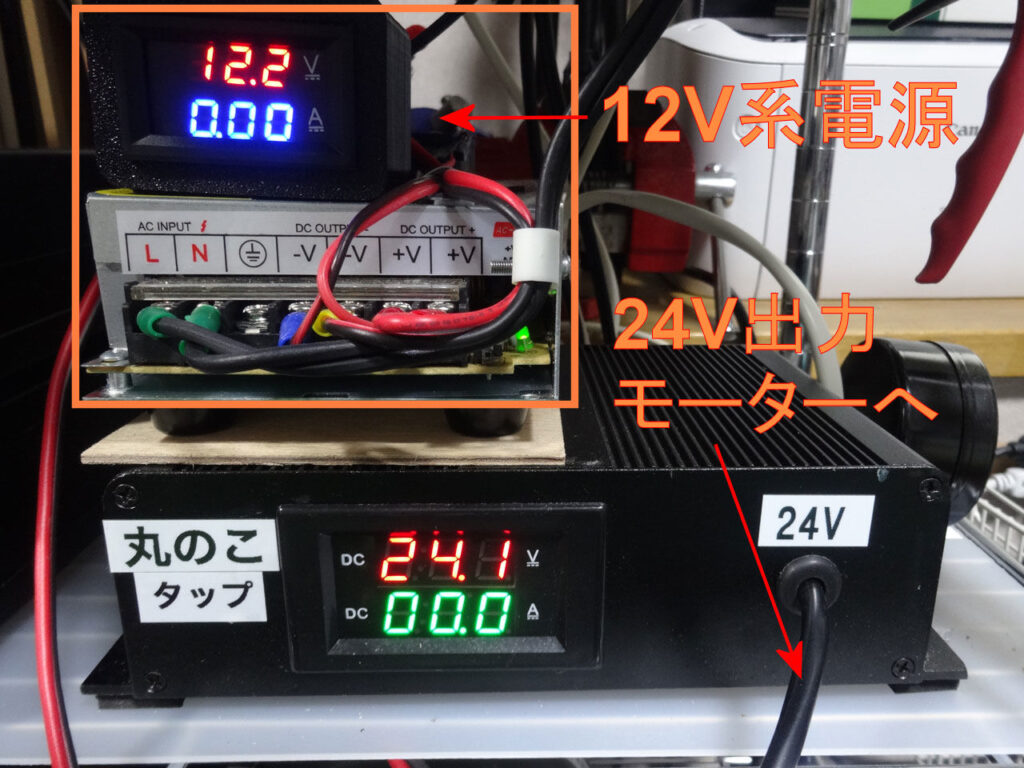
- さあタップ切りというところで,ちょっと改良した.無謀にもタップの刃部分と同じぐらいの20mm角アルミ角材が手持ちであったので,これに挑戦しようと考えた.さらにトルクのある12r.p.mのギヤダウンユニットを使用することにした
- メインに使うのは35r.p.mのギヤダウンユニットなので,交換が簡単にできないと大問題となる.将来ほかのギヤ比のものに変えることもありうるので追加改造を行った
- ギヤダウンユニットとスタンドのクランプは両面テープで回転防止をして取り付けていたが,これだとギヤ比が異なるギヤダウンユニットと交換が面倒になってしまう
- そこで,アダプターの形状を1ピースのものに変更した.トルクが上がれば当然クランプとギヤダウンユニットは滑る可能性があるため,滑り止め対策は両面テープではなくイモネジで行うことにした
- ギヤダウンユニットとアダプターは,IPAでよく脱脂した後で両面テープで固定した
- ドリルスタンドのクランプに1対のM4ネジを切り,イモネジを2本で回転止めとした
PLAのため,いい塩梅で食い込んでくれた - しかし,いくら滑り止めを施してもできるだけ隙間がないようなアダプターを作製したのでギヤダウンユニットをセットするのに苦労した.C形状なのでカット部分にドライバーを差し込んで広げて挿入する
- そして,M4x6mm のイモネジで固定する.イモネジセットを眺めてこれにした
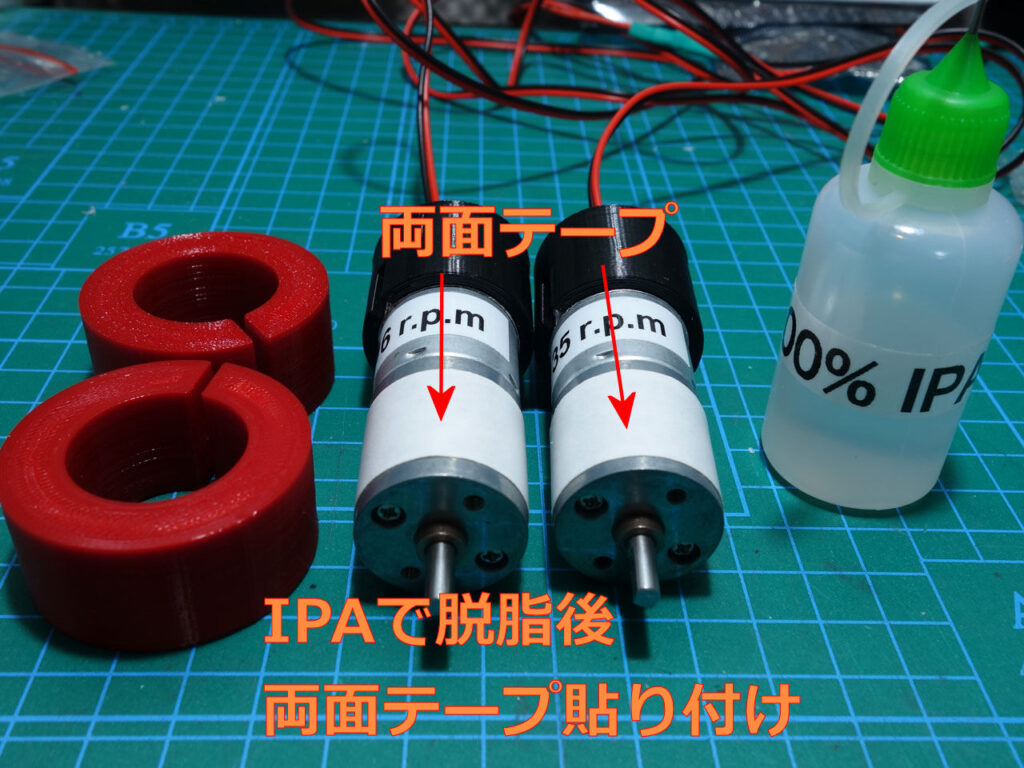
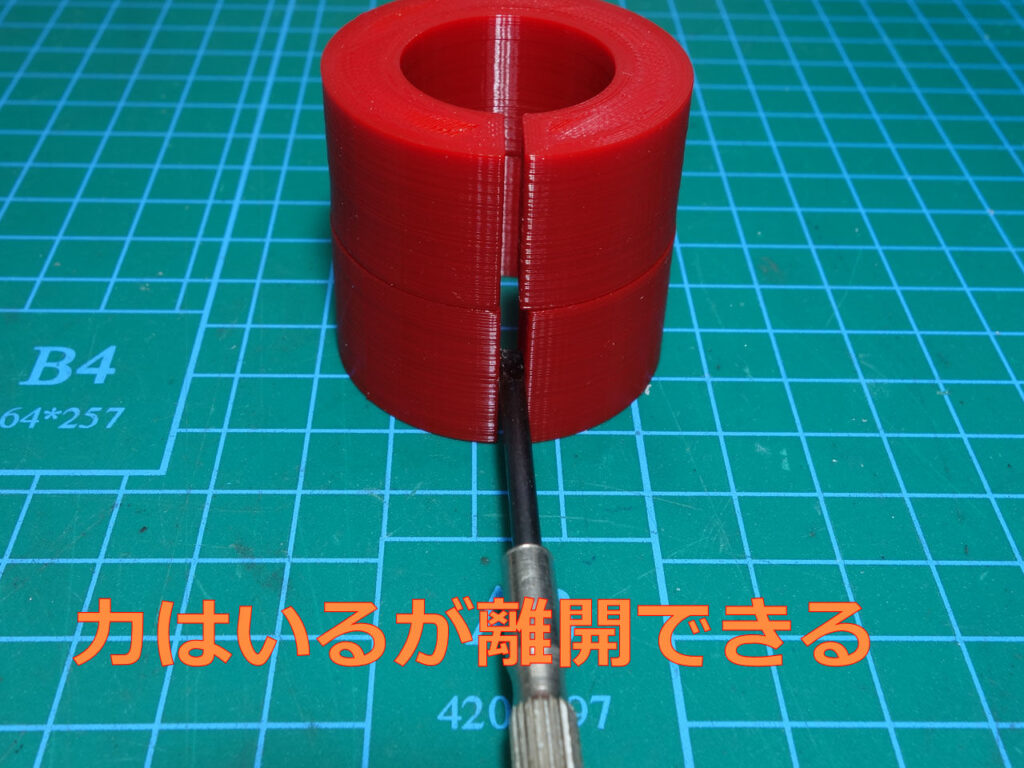
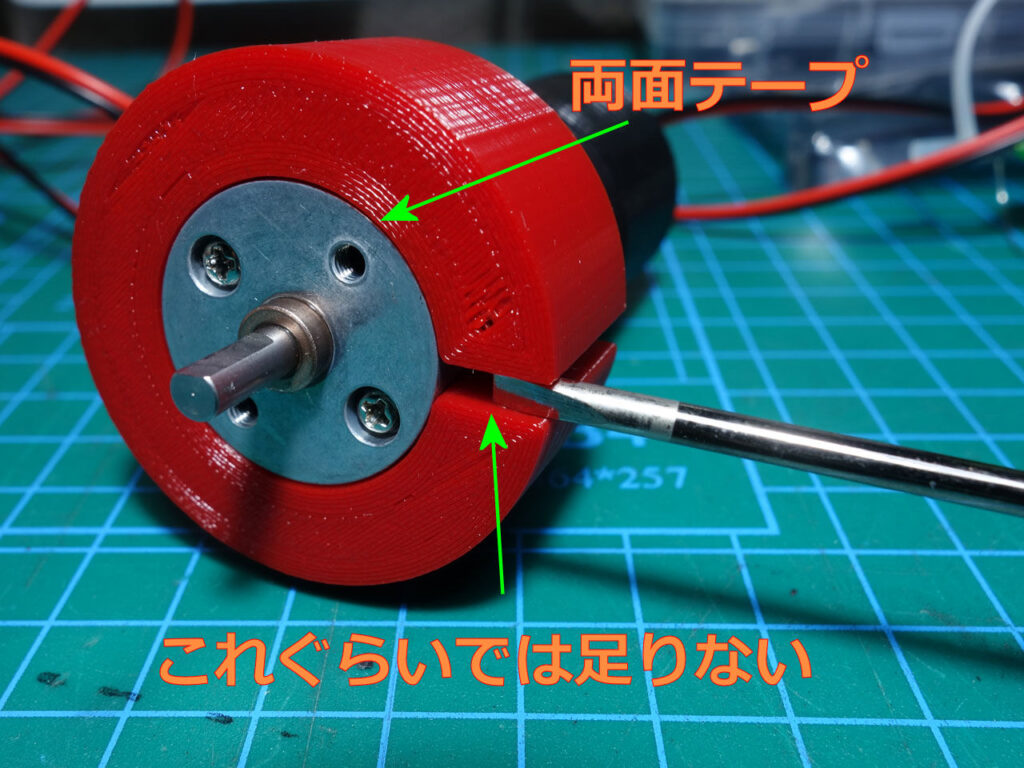
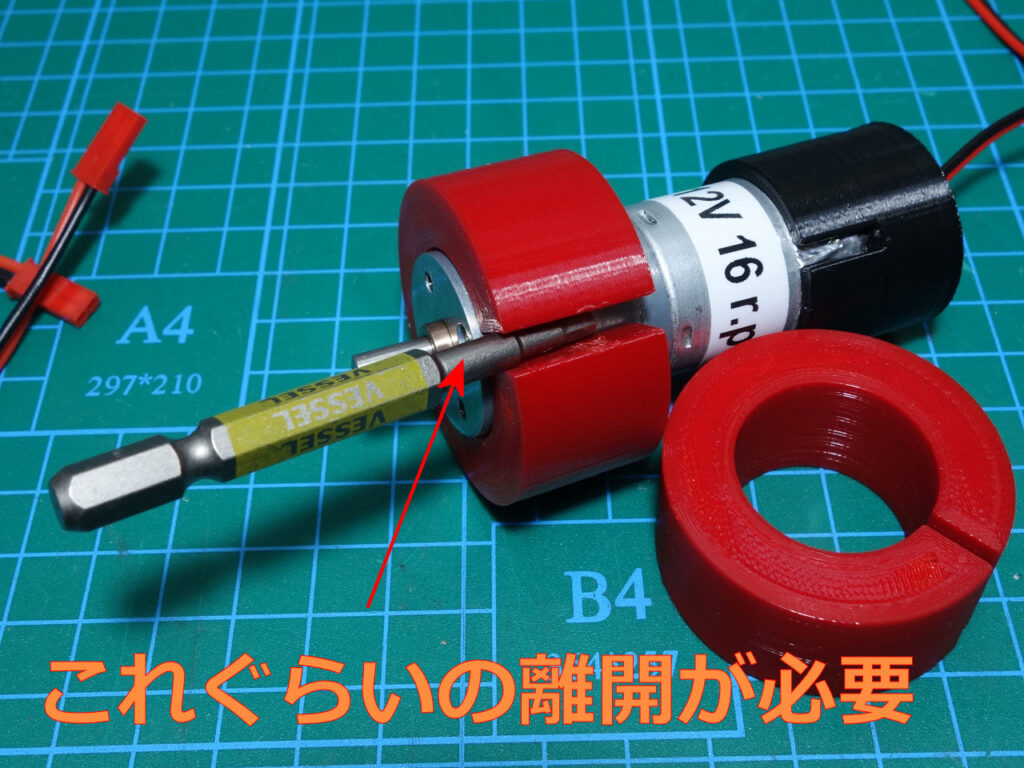
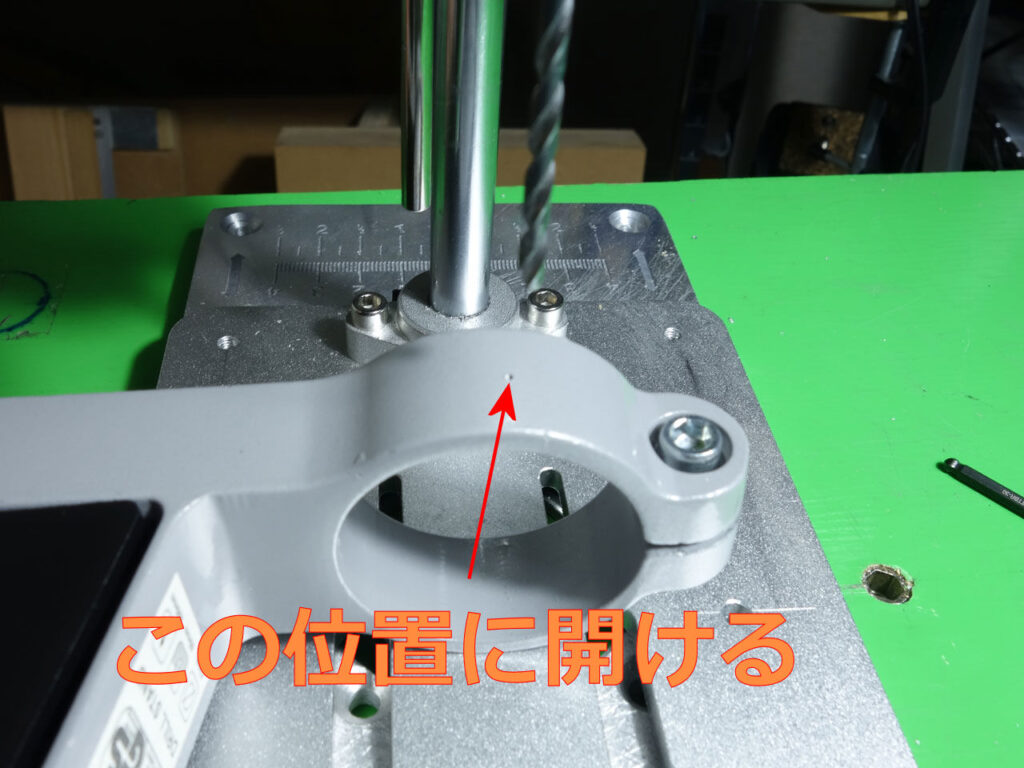
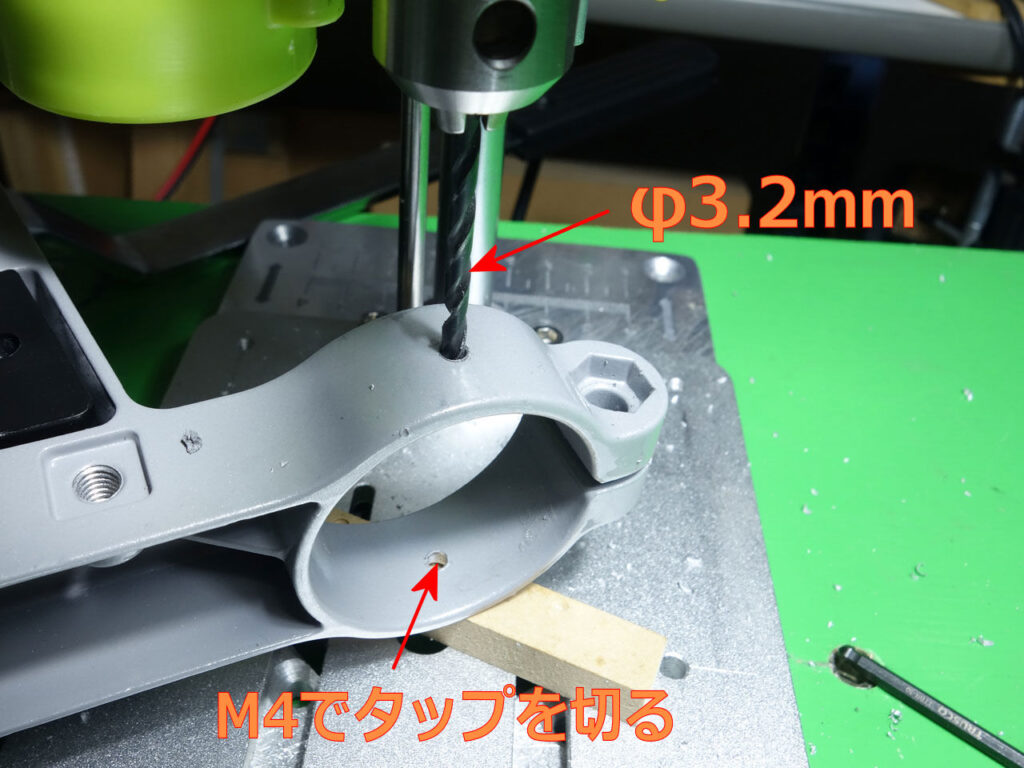
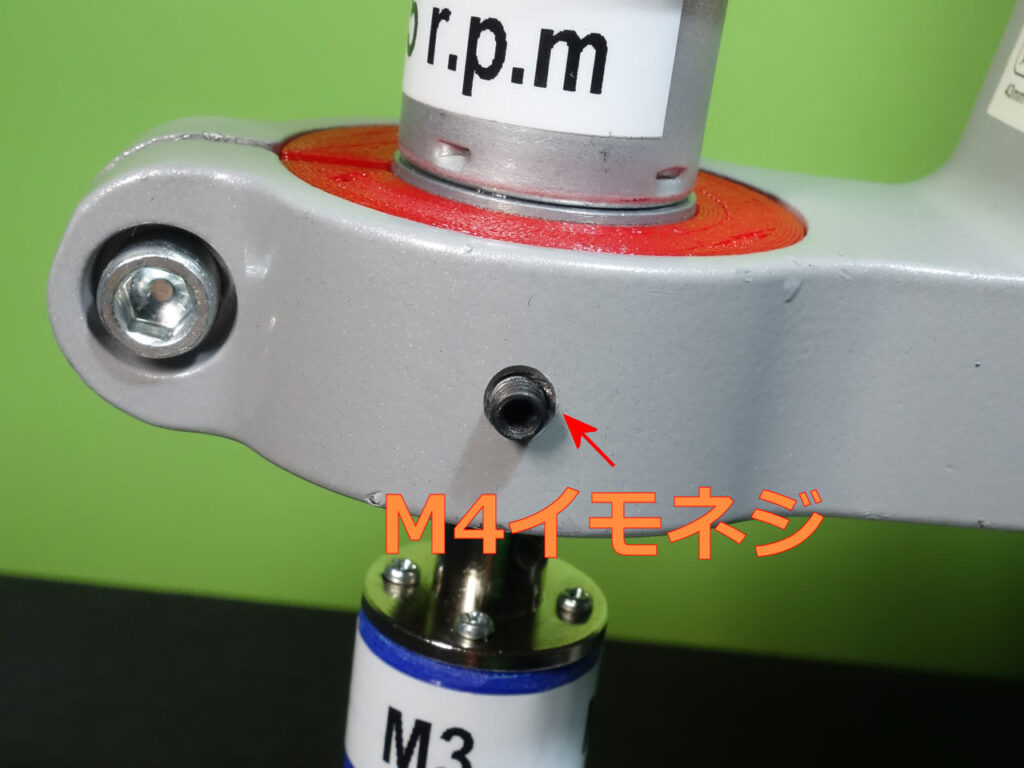
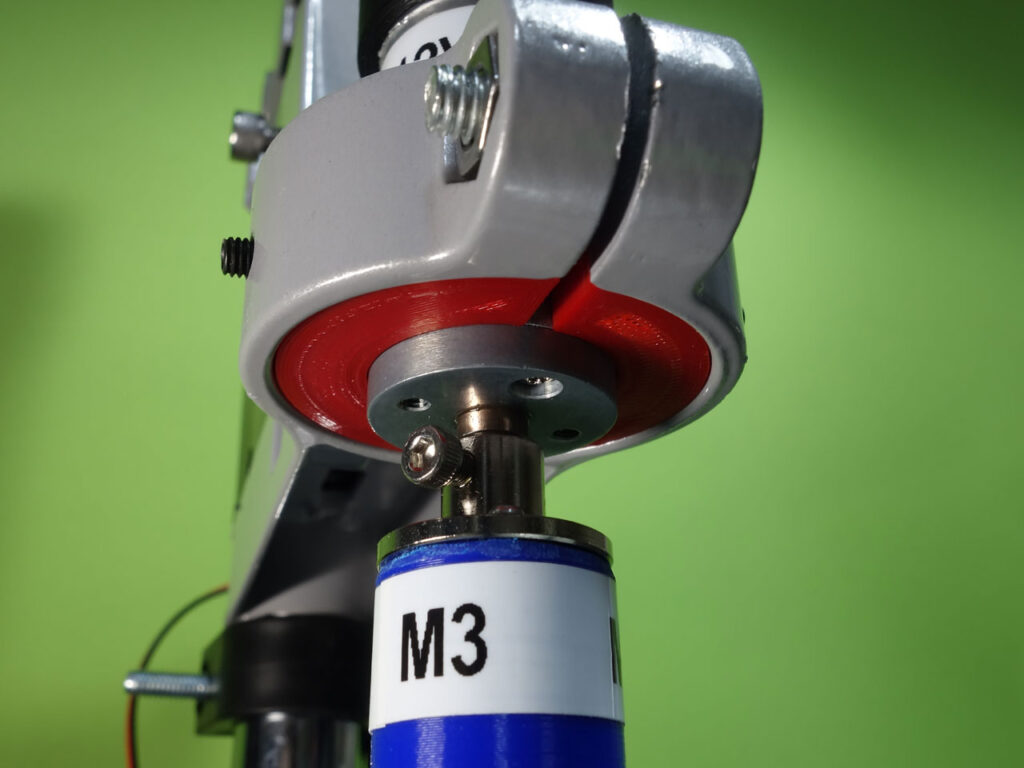
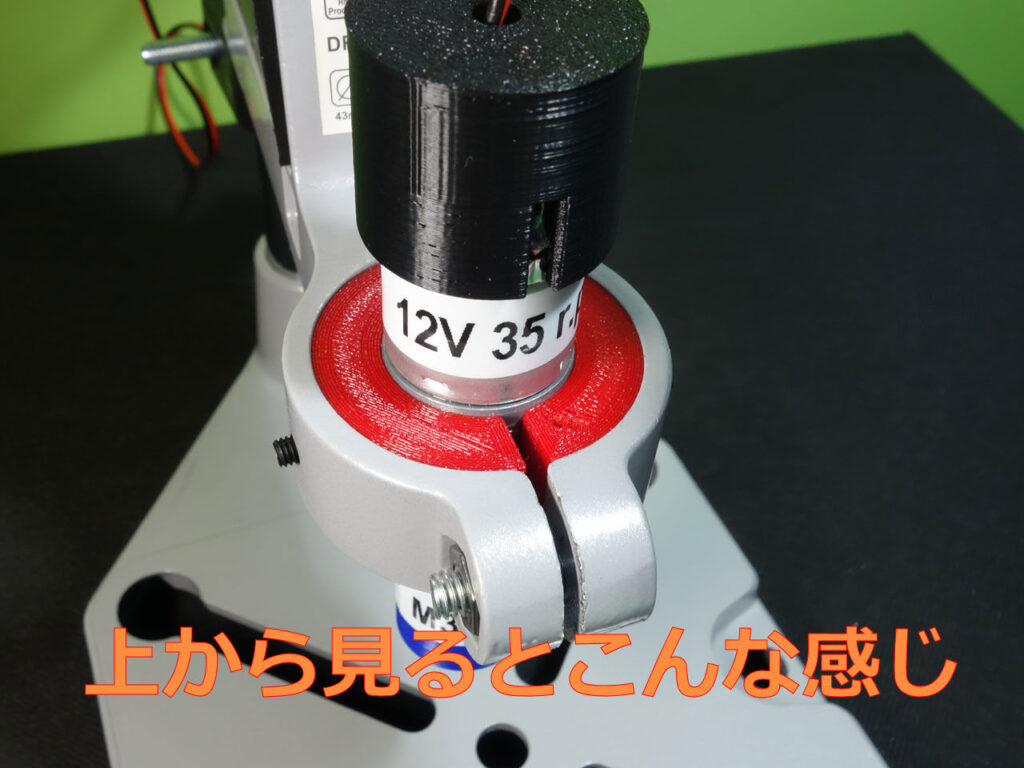
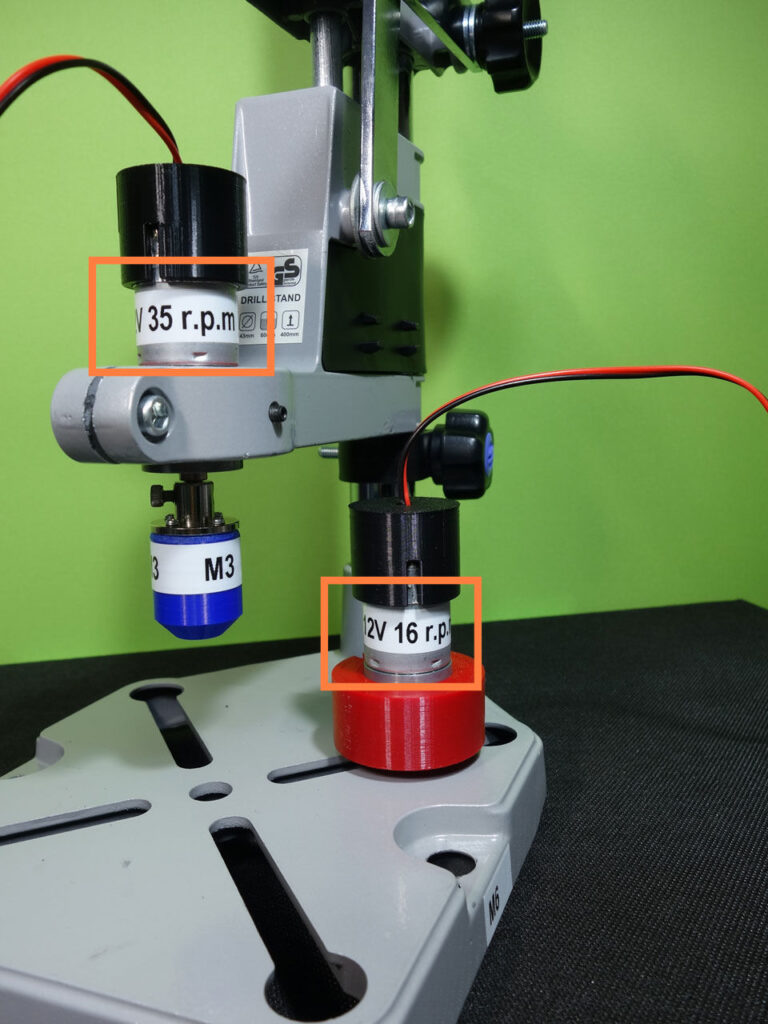
- 上記改良のついでに,ワークが回転しないようにするクランプをつけた
- タップを切り始めるとき,ワークは左手を軽く添えてタップが中心に入っていくように押さえておく.仮にワークが完全に固定されていると,CNCのように座標で操作するわけではないのでちょっとでも下穴の中心からずれていると正しくタップが切れない
”手指の感覚” 最強説である - タップが進んでいくと,ワークが回転する.そこで,浮かないようにクランプで抑えつつアルミフレームをストッパーとして使用する.なかなか使い勝手がいい
- パーツとして,20×20 200mmアルミフレームとトグルクランプを使用した
- このアルミフレームは,nanoフライス盤のバイスを自作しようと購入しておいたものである.購入時4本で¥422! 思わず長いのも買ってしまった
20×20 600mm 4本組で,これも破格の¥1267!
長くでも,切断には困らない.nanoテーブルソーなら楽勝である - トグルクランプは5個組であったが,何のかんので使い切ったので,なくならないうちに再購入することにした
- アルムフレームをスタンドベースに固定するための大きなツマミを作った.3Dプリンターでツマミし印刷して,加熱したM4x15mmキャップボルトを加熱後圧入した
- 圧入は垂直に行う必要があるため,ドリルガイドのチャックにキャップボルトをくわえさせポケトーチで加熱した.作業の動画あります
- Tスロットナットでアルミフレームに固定するが,つまみに凸部を作ってありここがドリルスタンドベース裏側にあるスロットにはまり,締めつけを容易となる
- クランプとアルミフレームはM4x8mmキャップボルトとTスプリングナットで固定することにしたのだが,結構きつくて今回の用途には向いていないようである.後日変更した

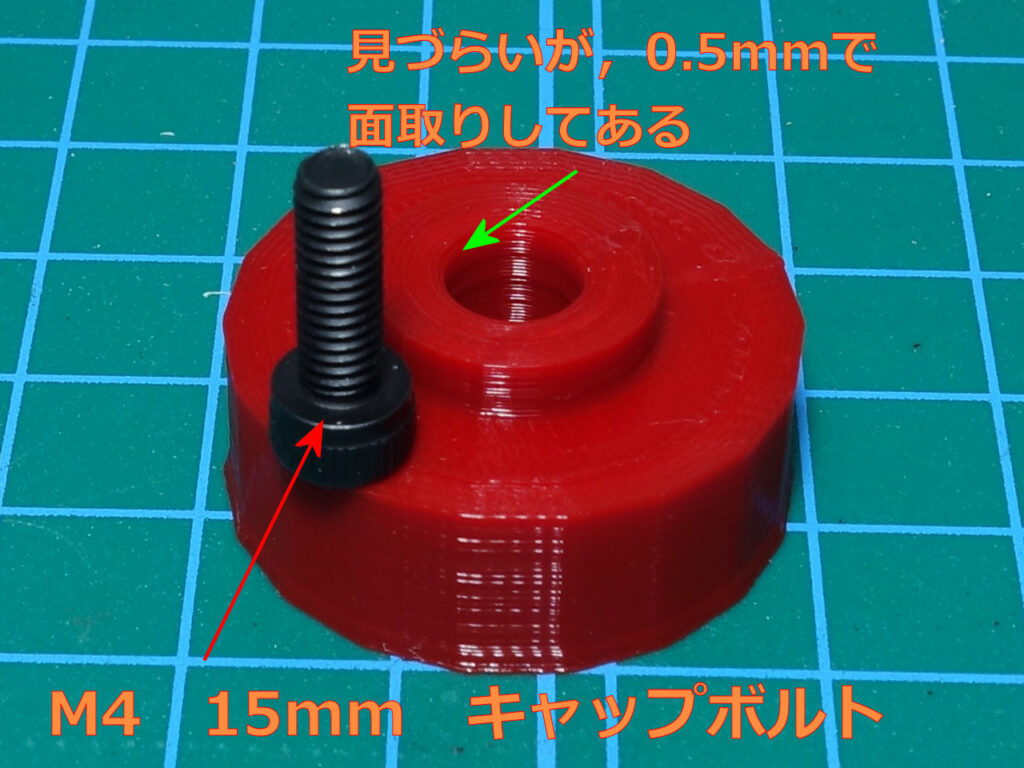
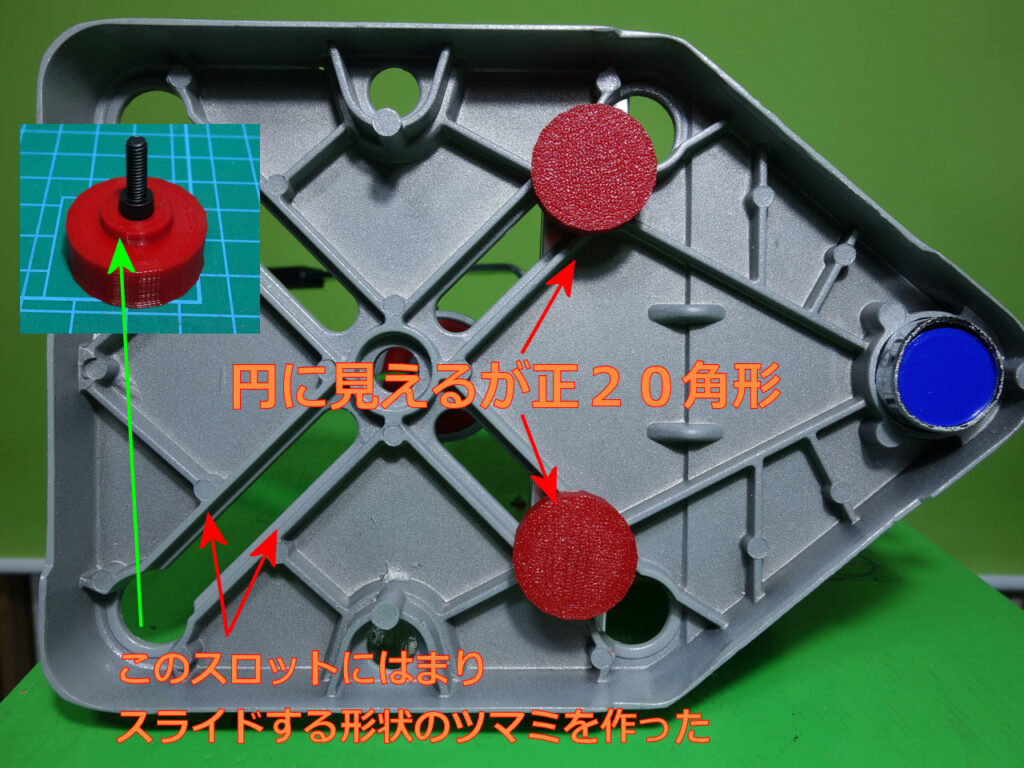
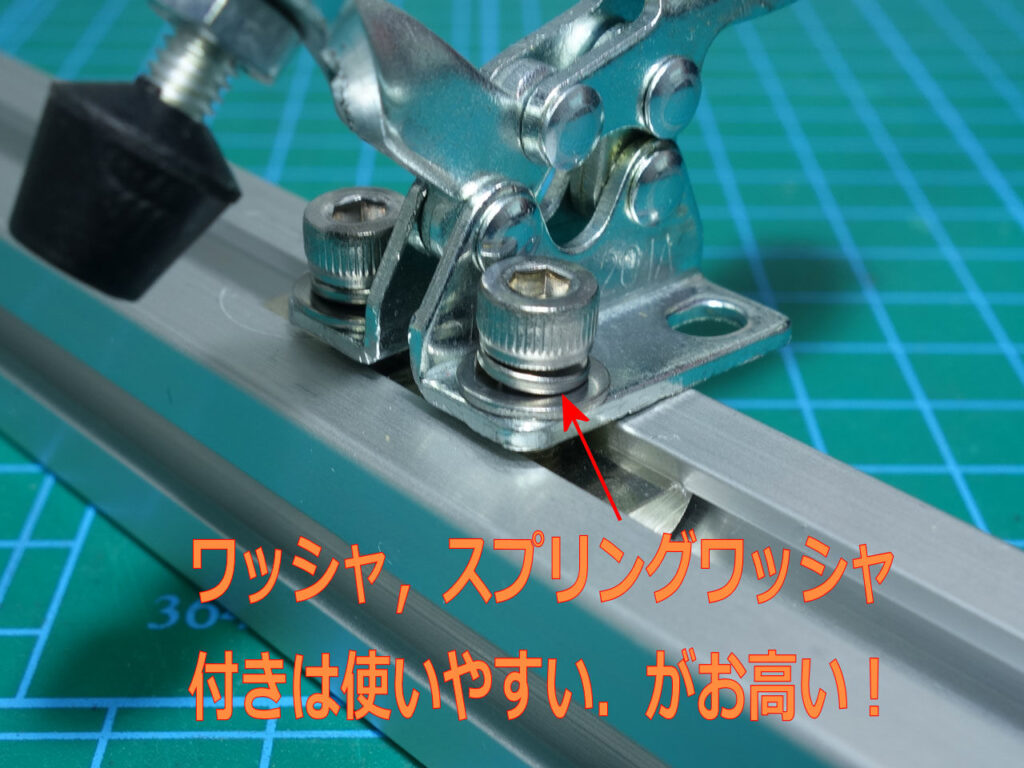
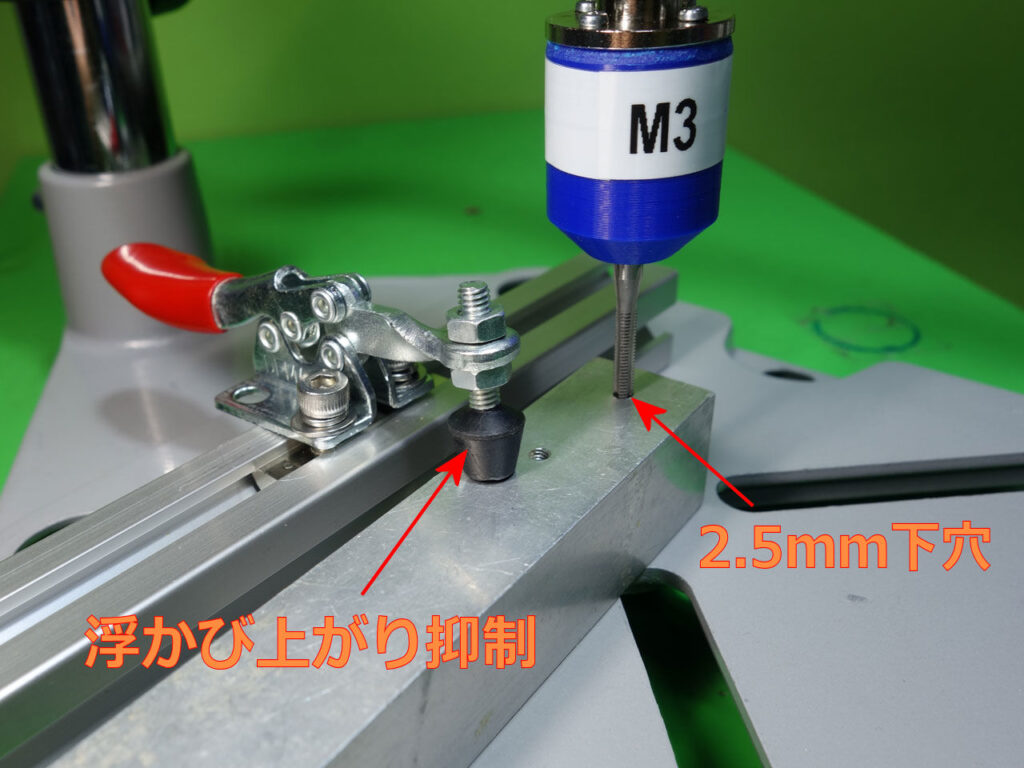
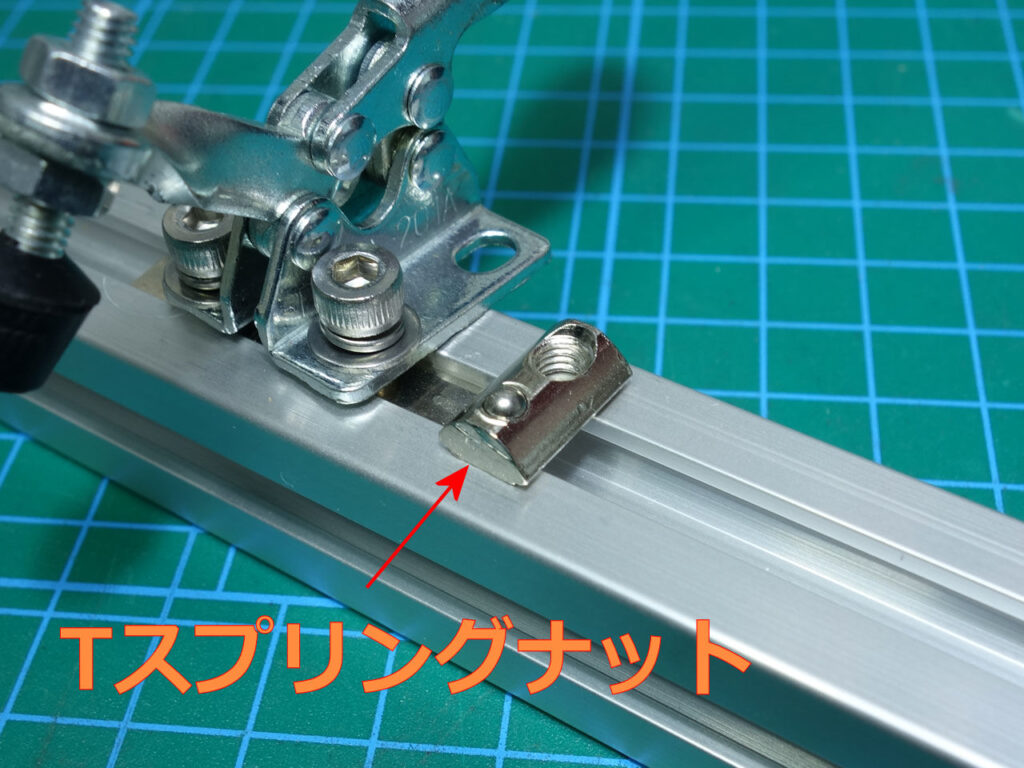
- 5mmアルミフラットバーにM5キャップボルト用にタップを切ってみた.ギヤダウンユニットは35r.p.mのギヤダウンユニットを使用した.
- 手持ちの5mmアルミフラットバーに,一般的な下穴径φ4.2mmを開ける.スペーサーとしてコンパネの切れ端をかませて,バイスに固定した.いとも簡単にタップが切れた.アルミはある程度の硬さがあるが,5mm厚だとタップはぐらつきやすく,少しでも曲がるとそのまま進んでしまう.本ツールは効果大であった
- 20mmアルミ角材に貫通するタップ切りに挑戦した.さすがにトルクがいりそうなので12r.p.mのギヤダウンユニットを使用した
- 20mmアルミ角材の手持ちがあったので試してみることに.何に使った忘れたがすでにM3のメネジが切ってあった.この穴をM4キャップボルト用に切りなおすことにする.そのため下穴をφ3.2ドリルで開けた
- 穴が2つあるので,1つはタップハンドル用,もう一つ電動タップで試すことにした
- タップハンドル用は,先タップ,中タップと途中までタップを電動タップで切り,その後タップハンドルに加えなおして貫通してネジを切る
- もう一つは,貫通するまで電動タップで行うというもの.いささか無謀のような気がしたがどうしても試してみたかった
- タップハンドルでの使い方が,当初考えていた使い方であったが,アルミならタップの刃がある範囲なら問題ないことが分かった.タップの刃部の長さはおよそ18mm程度なのでアルミ板もその程度なっら問題なく貫通させてタップを切れることが分かった
- 電動で貫通させるなら中タップが良さそうである.タップの種類はこちらが参考になる
- 電子工作の構想中のプロジェクトに使うパーツを作製.固定用ネジ穴を切ってみた
- Adruinoでタッチパネル液晶を使った電子工作が面白い.タッチパネル液晶はいろんなサイズがある.数年前は小さなサイズしかAmazonで購入できなかったのでもっぱら2.8inchの液晶パネルモジュールを使っていたが,最近 3.2inch, 3.5inch, 4.0inchと種類が増えてきた
- ブレッドボードに液晶やマイコンモジュールを刺して配線していたのだが,それらをつなぐ配線が多くかなり面倒なのである.調べてみるとドライバは違えど設定ファイルのUser_Setup.h を変更すれば,同じ結線で行けることが判明(まだ試してないが)
- またもっと深刻な問題は,ブレッドボードと電線の接触不良がことである.そのため配線ミスがなくても動作不良で悩むことになる.画像にもあるように電線がスパゲティ状態なのである
- そこで,マイコンとタッチパネル液晶は,はんだ付けで結線しすることを考えた
- マイコンはESP32-DevKitCがハイコストパフォーマンスであるので,これを選定
Aliexpressには,このモジュール用の開発ボードがある.マイコンと結線するのではなくこの開発ボードをタッチ液晶パネルを結線する.メリットとして,プログラムを書き込んだら外してそのままプリント基板等にはんだ付けできる - タッチパネル液晶は,ゼロプレッシャーICソケットにセットする.ソケットの反対側は移動可能なブリッジを3Dプリンターで作製する
- これらを1枚のアクリル板に配置する.その時,各モジュールの高さを合わせるために下駄をはかせる.この下駄も3Dプリンターで作製し,各モジュールはM3ビスでねじ止めする
- このメネジを切るのに,当ツールを使用した.PLAは金属と比べかなり高度が落ちるためタップが少しでも曲がっていると,容易にずれていく.当ツールは薄物と硬度がない材料に絶大な効果を発揮する
- たとえボール盤のチャックにタップをくわえさせ,垂直にかませたとしても以後のタップを切るときに,まっすぐ切り込んでいかない.何度も失敗している
- 下駄に開ける下穴はビスがM3のためφ2.5mmとなる.このサイズの穴を3Dプリンターで印刷すると,1層目でまず形が崩れて失敗する確率大である.そこで,1層目は穴を開けずにフラットで印刷されるようにスケッチを描いて(Fusion360)印刷後,φ2.5mmドリルで貫通させるのがコツである
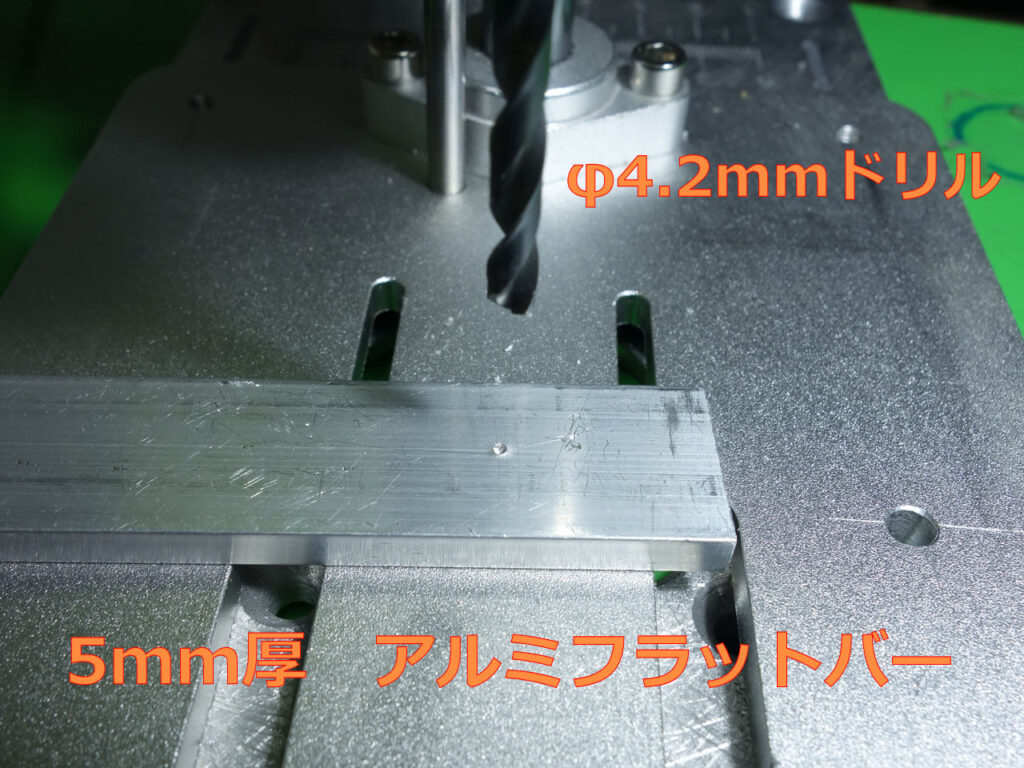
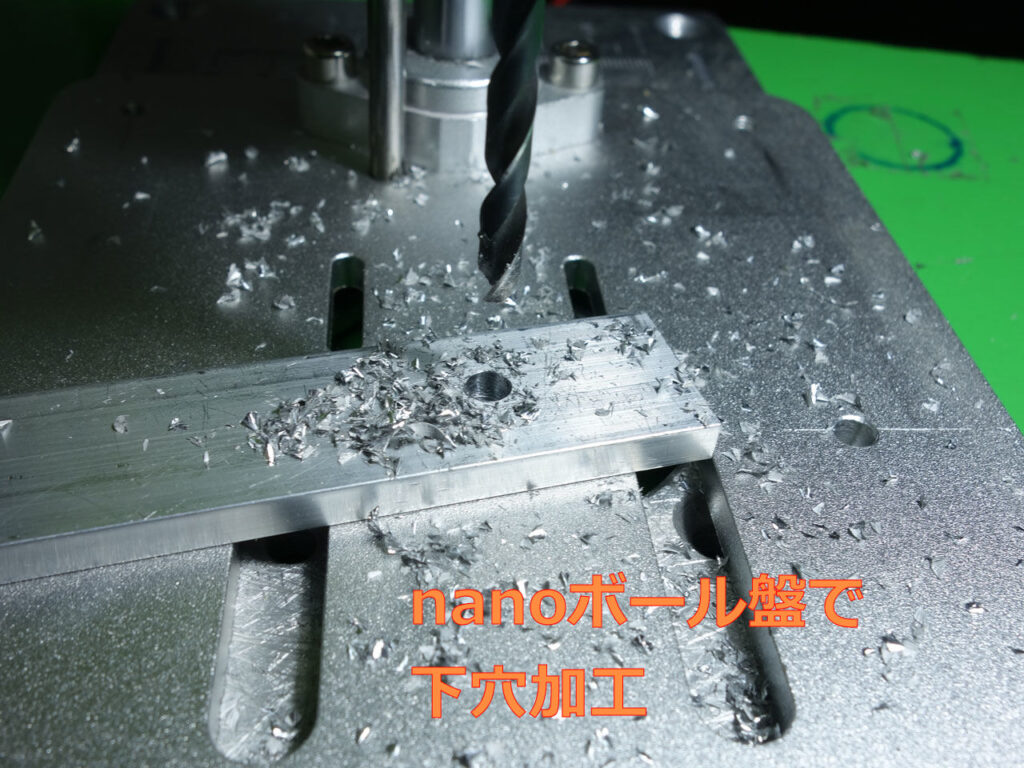
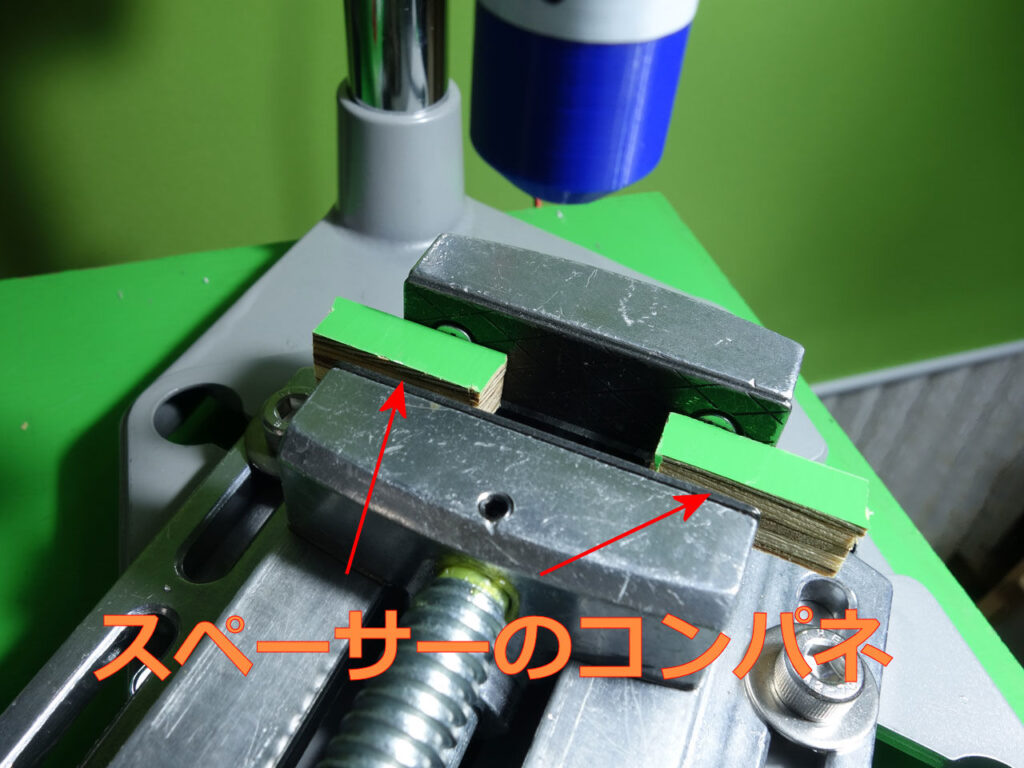
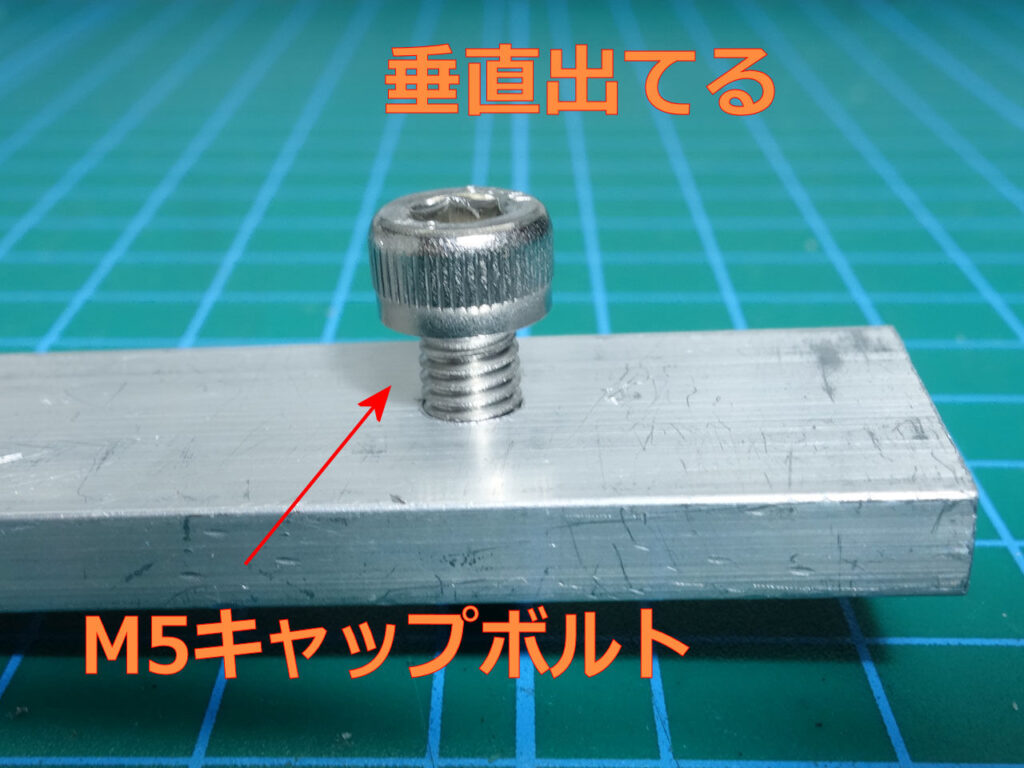
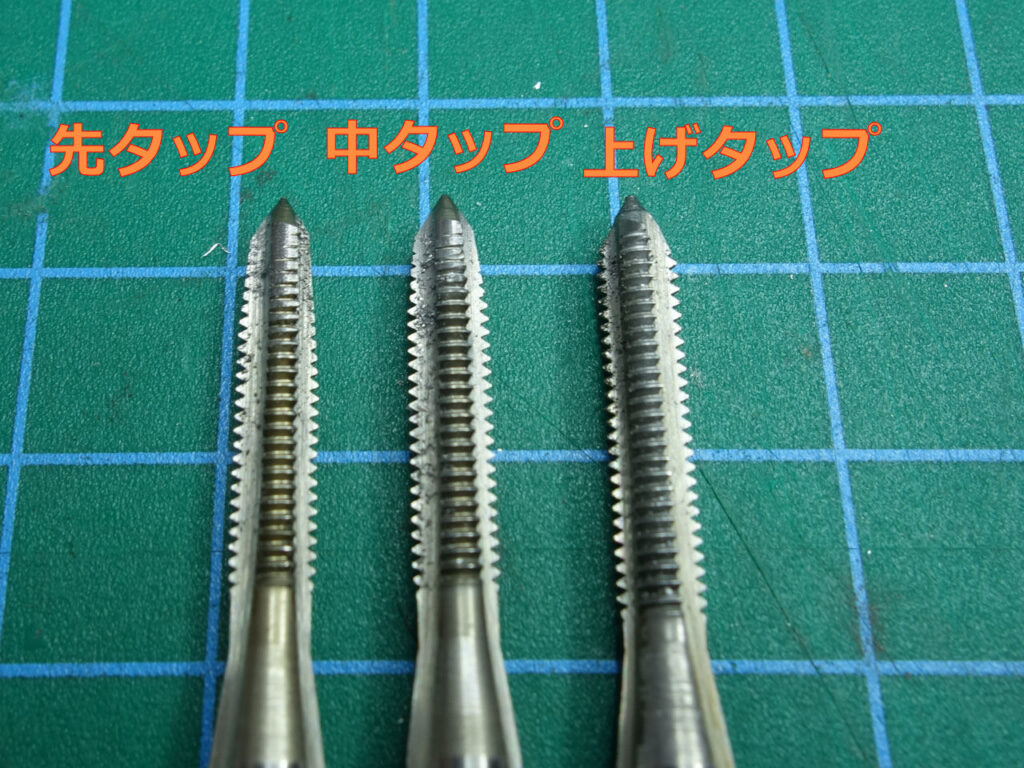
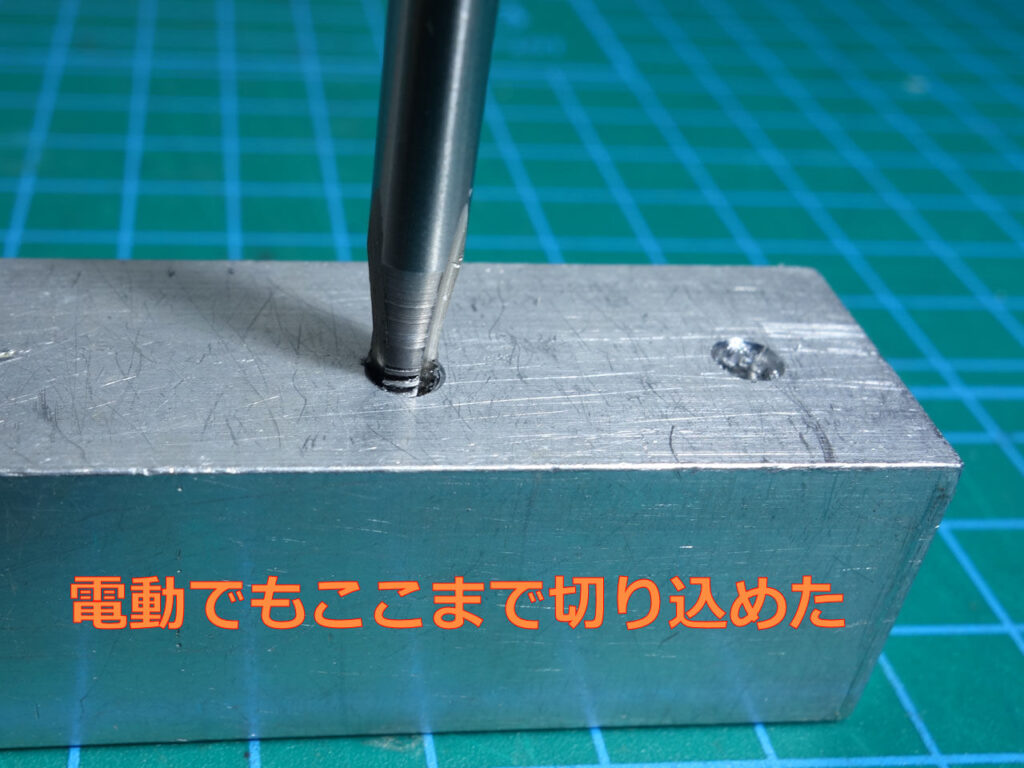
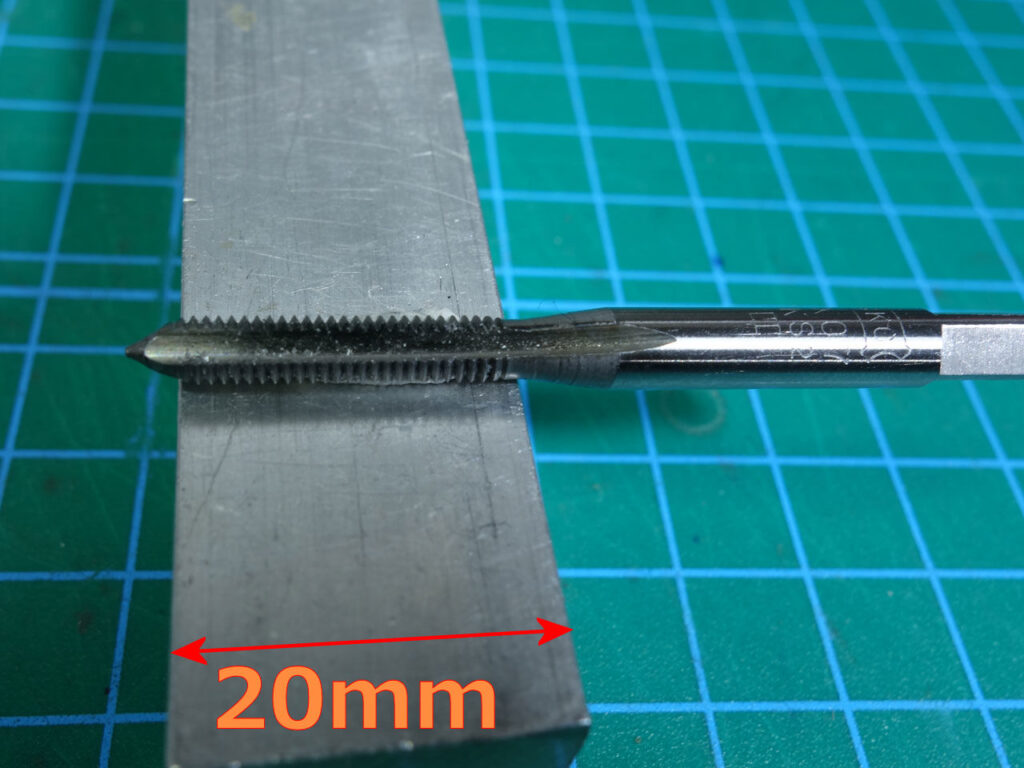

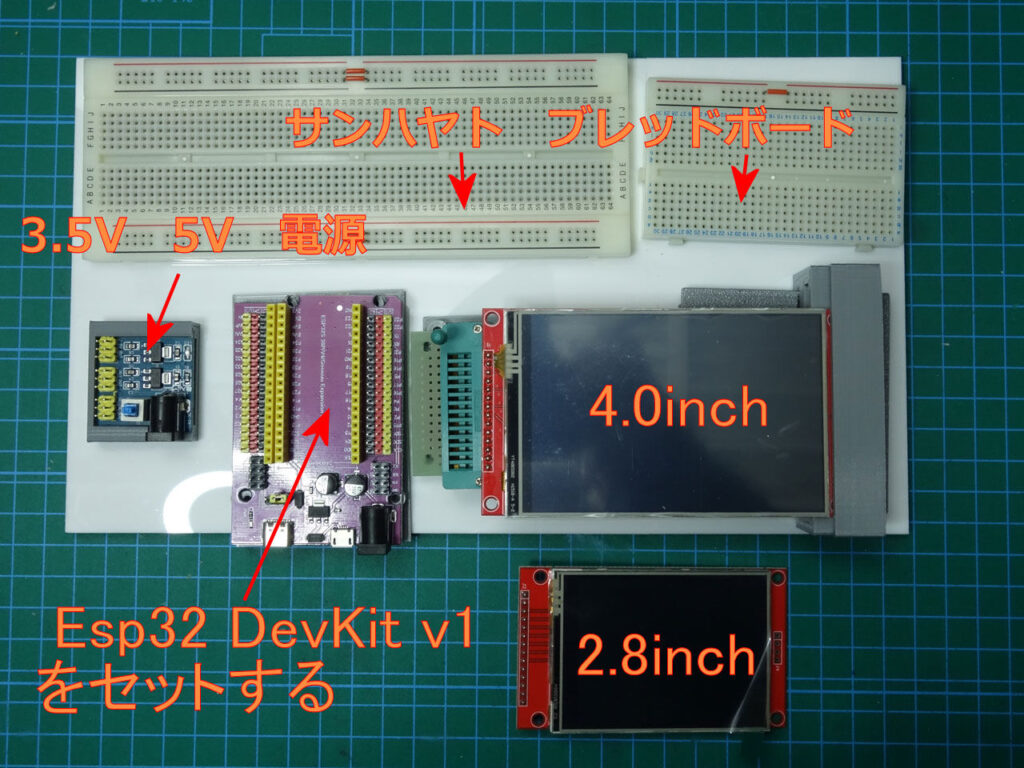
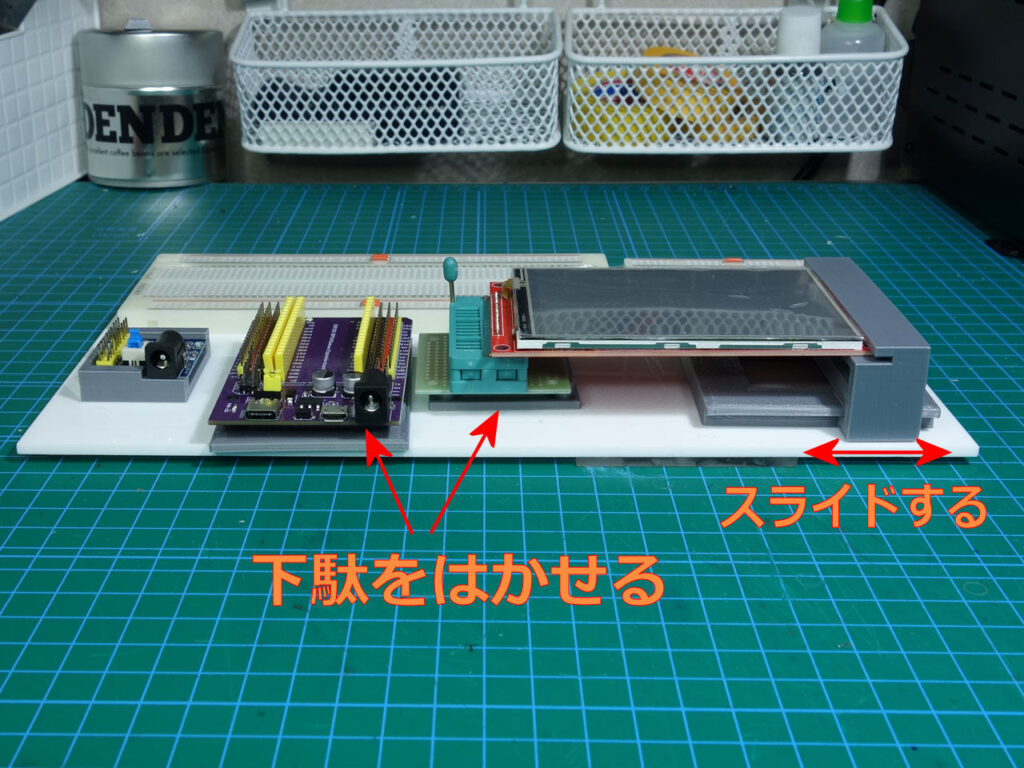
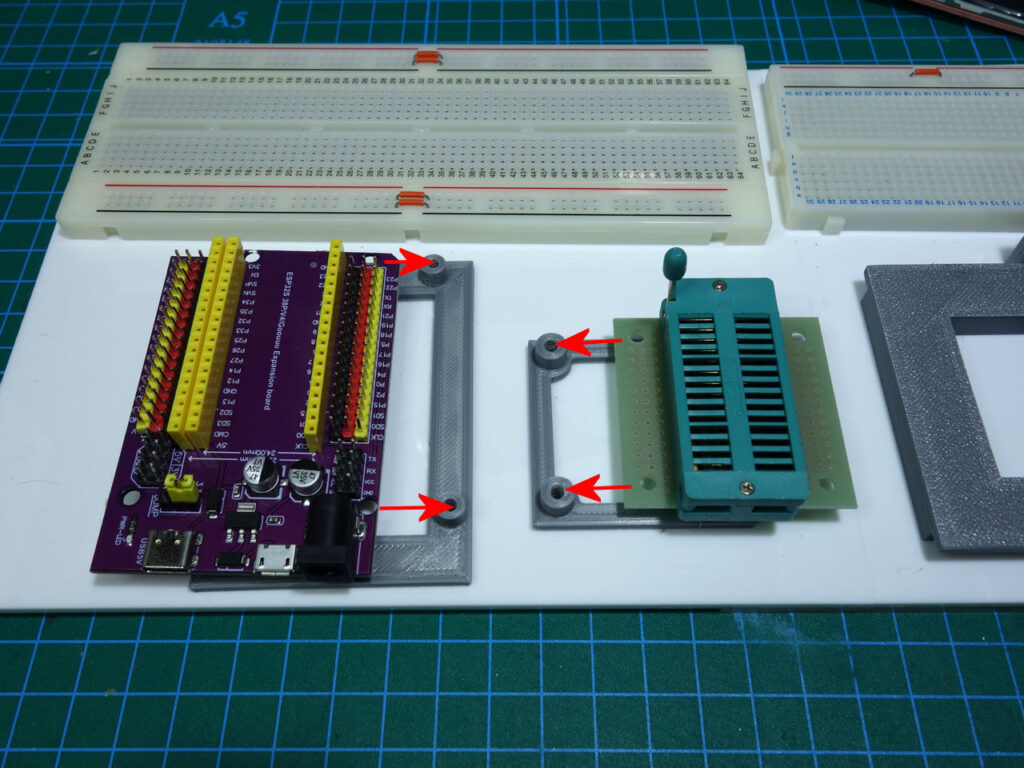
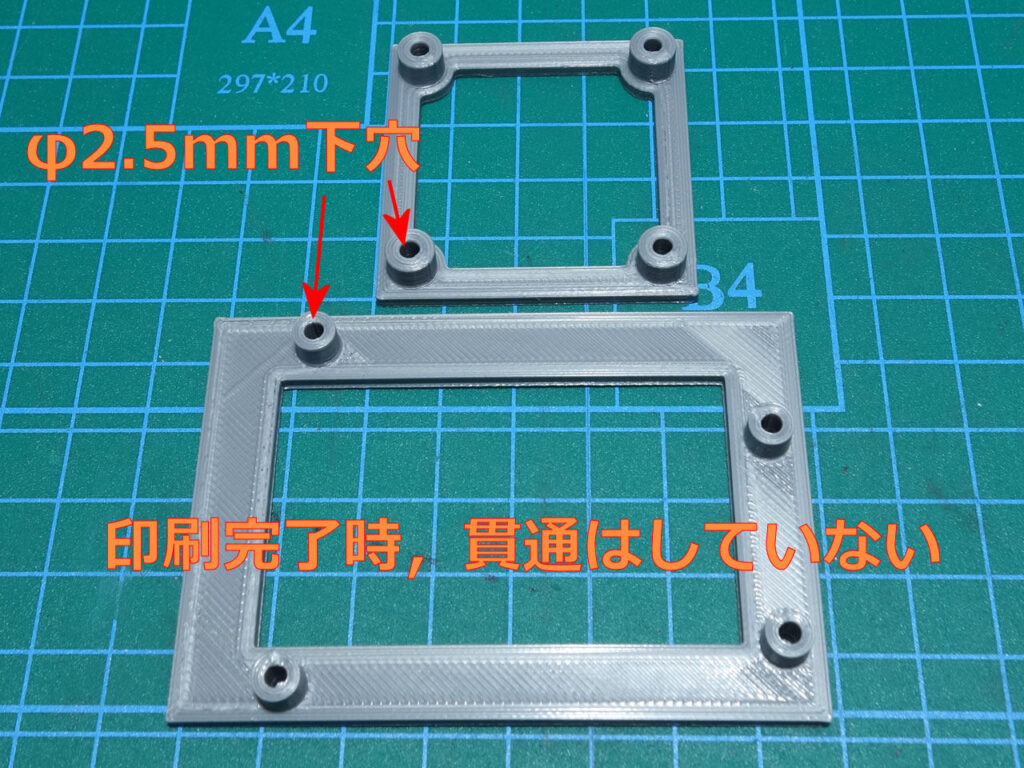
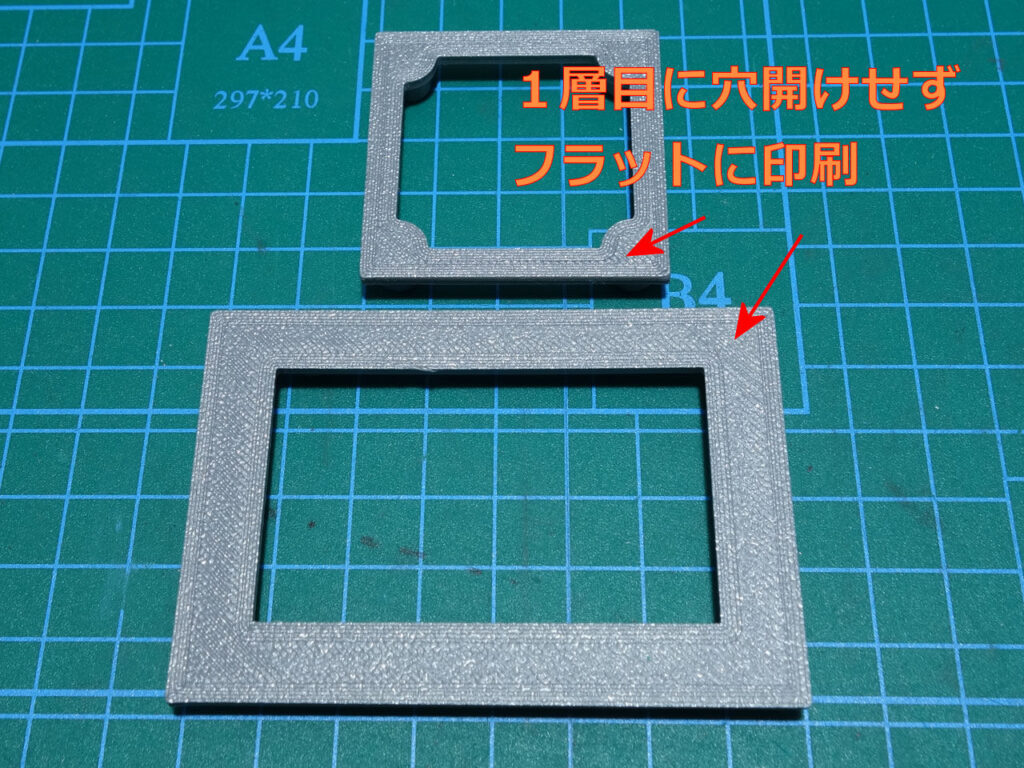
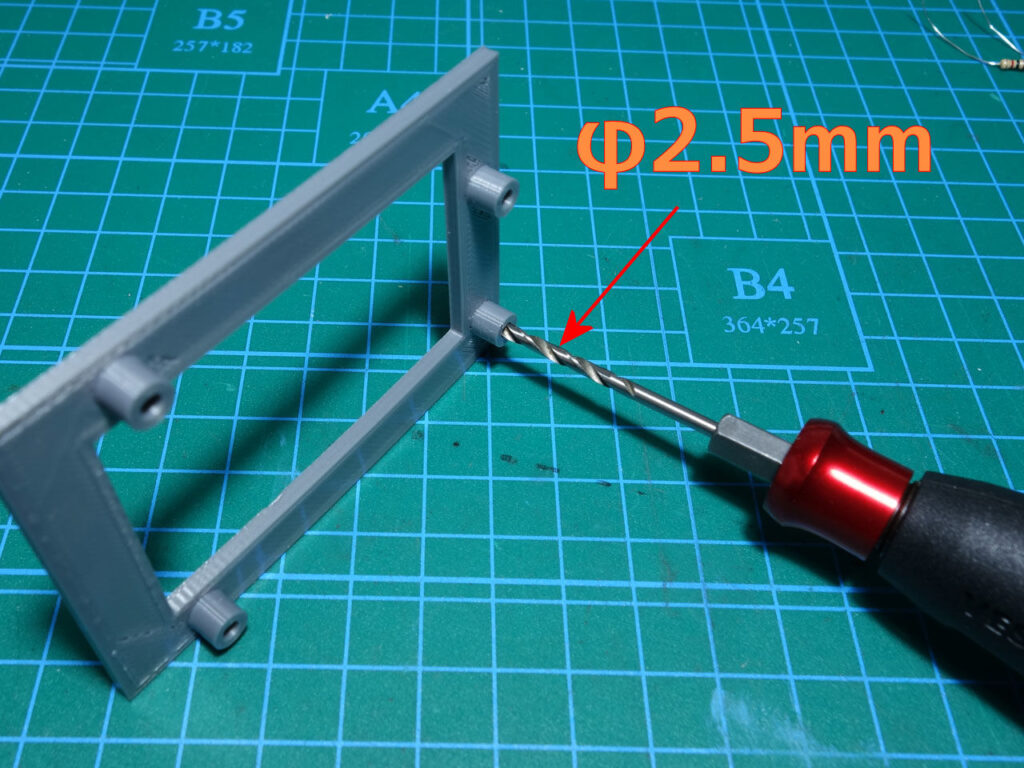
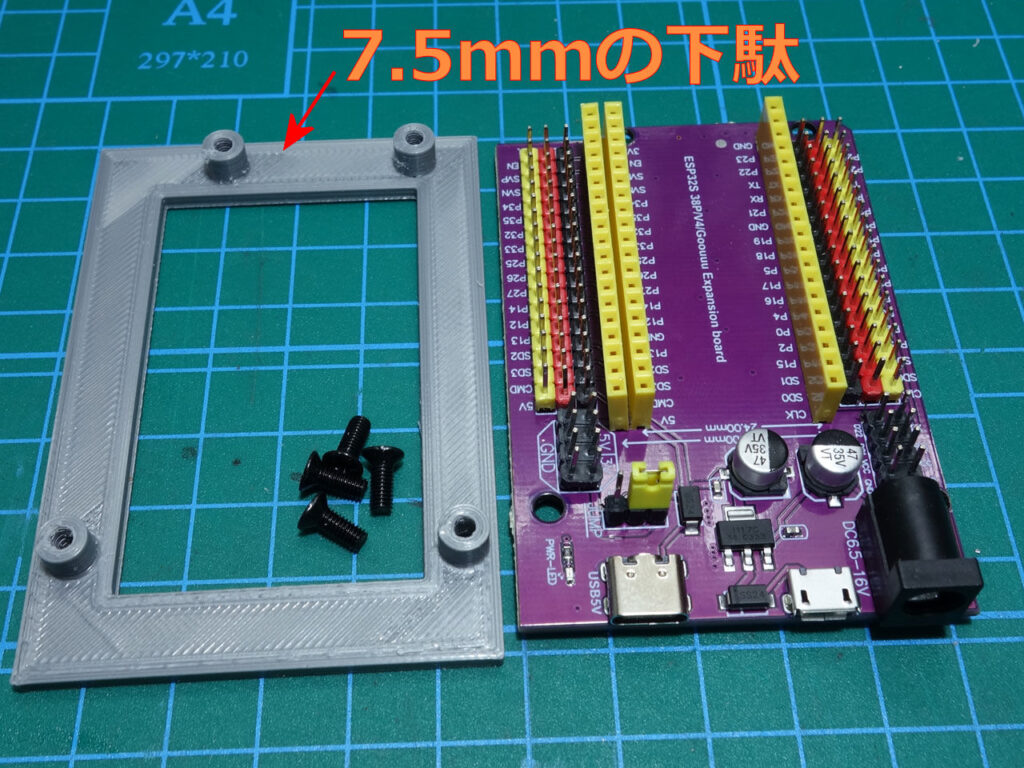
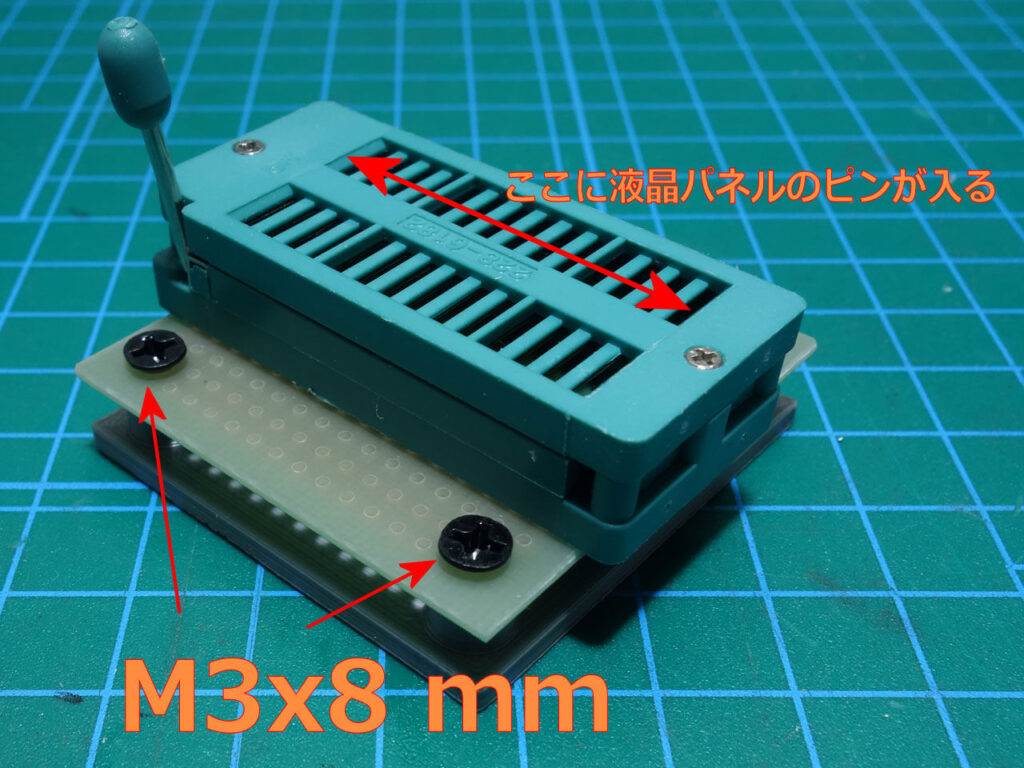
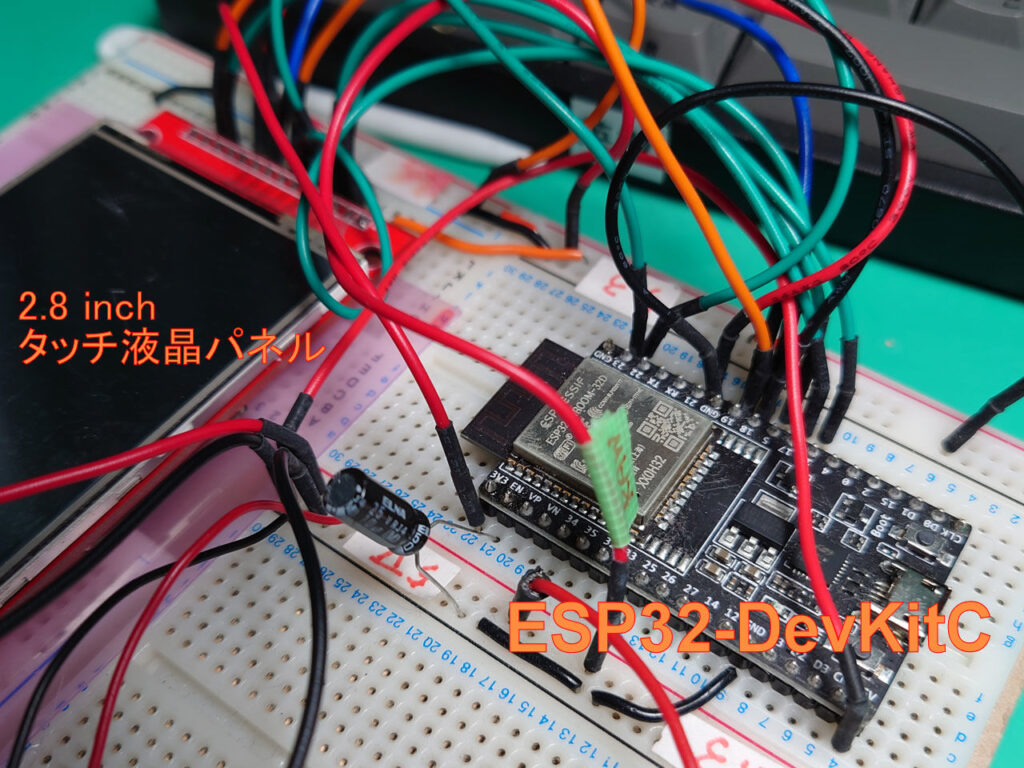
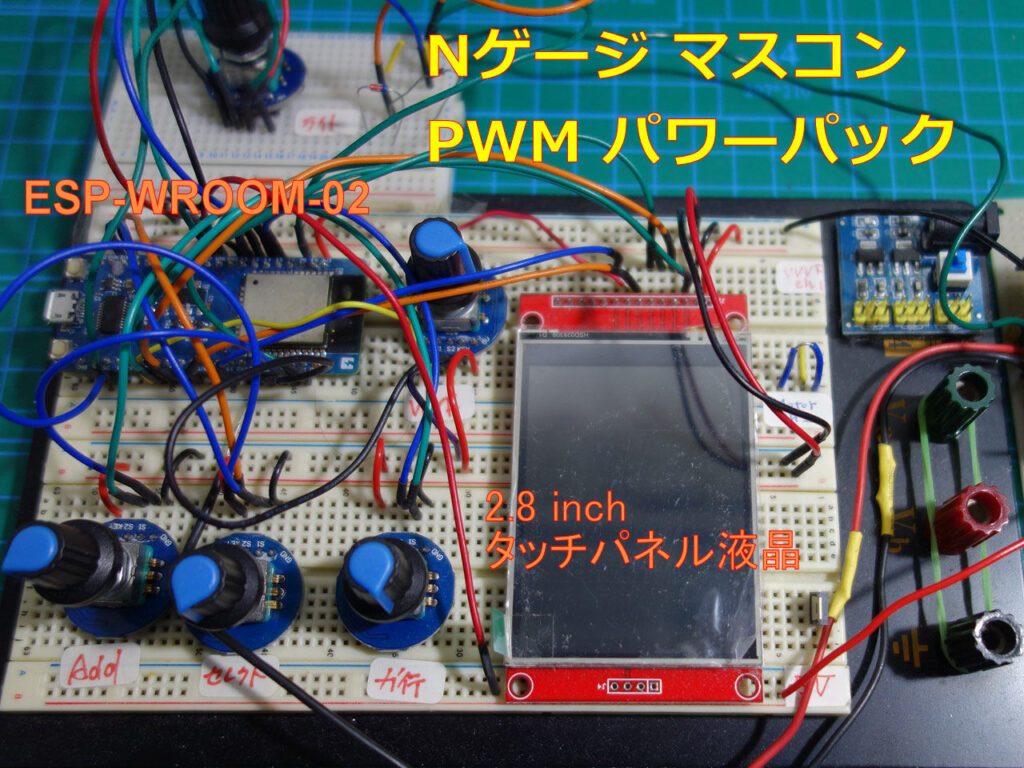
電動タップスタンドに使用した3Dプリントパーツをダウンロードできます
ファイル形式は 3MFです.2次配布は禁止とします
ご利用は自己責任で!