- 当工房で一番多用するnano工作機械である
- 金属加工を伴う工作に,穴あけは必須である.以前は卓上ボール盤を使用していたが,重くて収容時の場所を取ることから別の穴あけ手段を模索した
- そこで,ドリルスタンドとボッシュのAC100V使用の電気ドリルを組み合わせたボール盤を組み立てた.ベルト駆動であることの多い,卓上ボール盤よりトルクがあると感じている.現在もドリル径が6mmを超える穴あけにはこれを使用している.こちらのサイトで紹介されたものを大いに参考にさせていただいた
- フットペダルスイッチと秋月電子のトライアック万能調光器キットを組み合わせて,回転数制御と,ON/OFF スイッチングを行っている.アルミボックスに入れ,赤いアルミ製ノブをVRにつけた.なかなかかっこいいのだが,前面パネルのレタリングがシールなので,いずれシルク印刷にトライしようと思っている
- しかし,実際の穴あけはφ6mm以下であることがほとんどであるため,さらなる小型軽量のボール盤が欲しくなった
- いつものようにAmazonサーフィンしていると,手のひらに乗っかるボール盤を発見.しかもドリルチャックは6mmまで対応.これしかないと思ったが,これまたいつものようにAlliexpressで同等品を探してみた.画像多めで,改造プランがたてやすかった.Amazonだとこれと同じと思われる
- この手の商品によく使用される電源は,評判が芳しくなく,別商品付属のものを実際使ってみて,発煙させたトラウマがあるので,電源レスを購入した..
- そして,当工房の電源システムで運用する.このシステムはフットべダルでモーターのON/OFFを行う.突入電流対策として自動車電装用リレーを用いている.当然過電流対策のヒューズを内蔵している.中華製電源の最大の欠点はヒューズがなく,過電流時(モーター過負荷時)にMOSFET?が焼損してしまうことである
- 煙が出て壊れた時に,内部を見たらMOSFET?が黒焦げであった.それ以来nano工作機械の電源は自前のものを使うようになった
- Aliexpressから到着後,実際に使ってみた.サイズ感は思った通りで満足.穴あけ能力も概ね良好である
- nano旋盤の刃物台を製作するときに,穴あけ加工がたくさんあったが問題なくこなしてくれた.10mmアルミ板4枚重ねにφ5.1mmで穴を開けるというこのサイズのボール盤には過酷と思える作業であったが結果OKであった
- しかし,3枚目を穿孔するあたりからはハンドルに力を入れて押し下げないといけないので注油しながら下げていくと,モーター音が変わり明らかに回転数が落ちている
- モーターのパワー不足と,ハンドルの剛性と長さ不足が原因であるのは明白である
- そこで,今回の改造は,より強力な895モーターへの換装と,ハンドルの改造を行っていく.それに伴う各所の補強等も必要となった
- Aliexpressから商品到着後すぐに,プチ改造行った.ベースが小さく不安定なのでジャンクボックスをあさり使えそうなものを見つけ出した.以前木工用ルーターテーブルを作製しようとAmazonから購入したルーターテーブルインサートプレートを利用することにした.本来の目的には使えないほどに平面が出ていなかったもの
- ねじ止めして,滑り止めのゴムシートを貼り付けてある.大きくなった分安定し,クランプで作業テーブルに固定しやすくなった
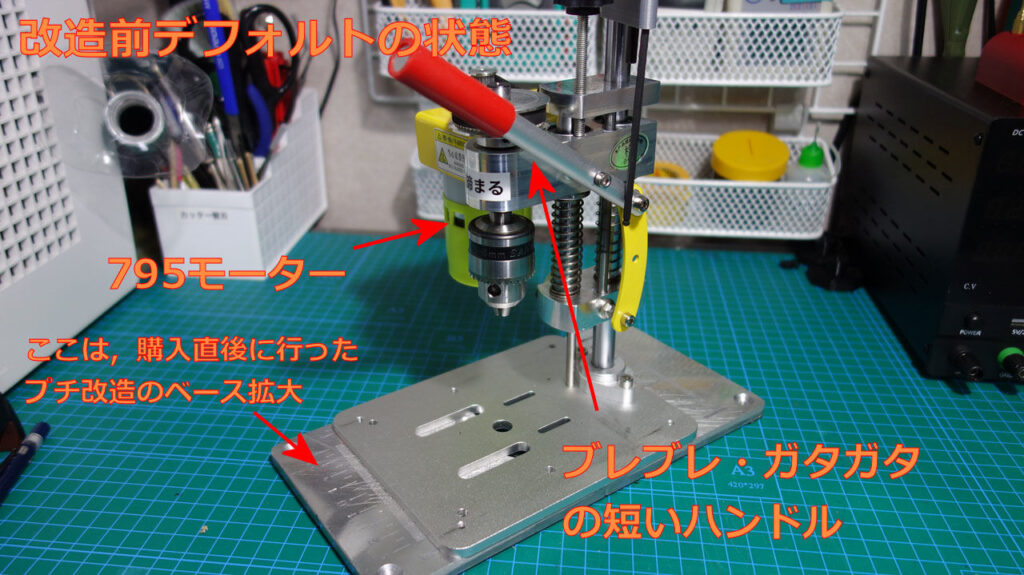
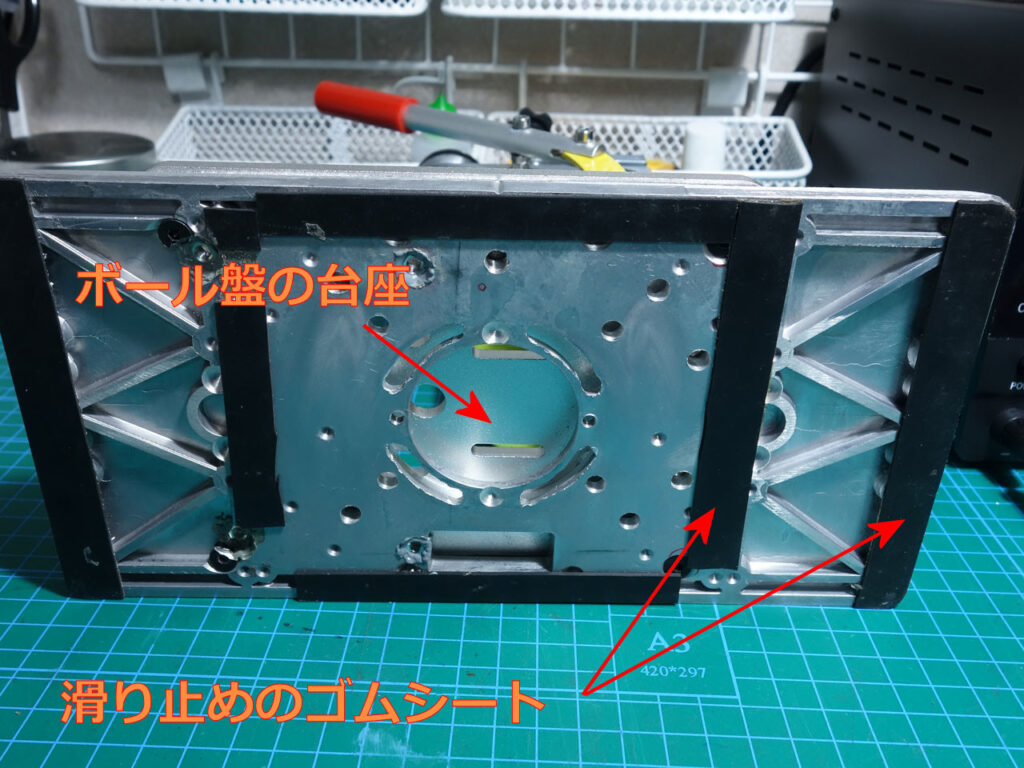
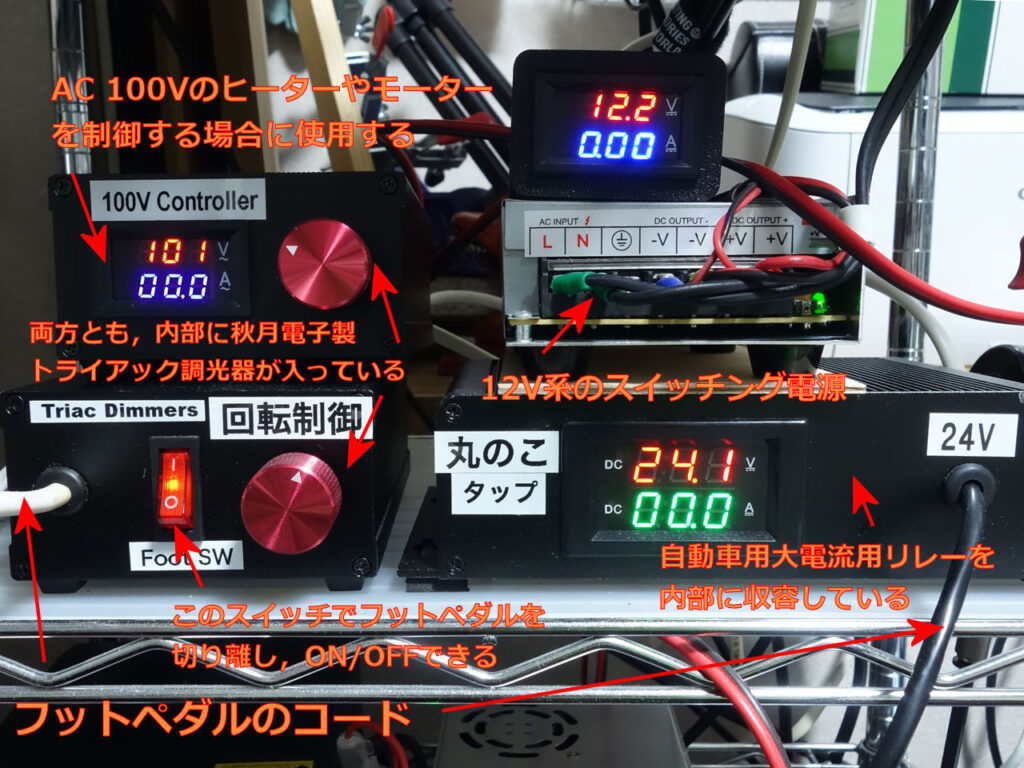
- デフォルトのモーターは24V 795 モーターである.モーターの回転数は明記されていなかったので,24Vの電源につないでボール盤主軸の回転数を計測した
- 方法は,非接触式レーザー測定タコメーターを使用.2年ぐらい前にAmazonで購入したもの.付属の反射テープをチャックに貼り付け,ボタンを押してレーザー光を照射する
- 安定化電源を使用して,ジャスト24Vを印加する
- ボール盤主軸の回転数はMAX 3259 r.p.m であった
- 歯数を数えてみるとモーターのタイミングプーリーは15歯,主軸プーリーは28歯
- 以上から推察すると.モーター回転数は 3259 x (28/15)≒6000 r.p.m/24V とハイトルクタイプのようである
- 24V 795 モーターには,そのほかに 8000,12000,16000r.p.m などいろいろなバリエーションがある
- しばらく使ってみて問題なかったのだが,nano旋盤のオリジナル刃物台を製作する過程で10mm厚アルミ板に穴あけした時に,もう少しパワーがあればなと考えた.この時に穴あけ条件は,10mm厚アルミ板を4枚重ねた状態で貫通させるというもの.ドリルの刃長が長いため穴あけが進めば進むほど,接触抵抗が大きくなってくるのでこのサイズのボール盤では過負荷かもしれない
- 中華製モーターのラインナップでは,795の次にハイパワーのものは895となる
- nanoテーブルソー,nanoベルトサンダーもこのモーターを使用している
- 実際手に持ってみると,両者の大きさの違いにちょっとびっくりした.かなりでかくて重い
- 当然消費電力も大きく,トルクもでかい.したがって,過電流とならないよう電気回路の許容電流を再考したり,力がかかる部分の補強が必要となるので,実施した改造点を紹介する
- ここで,モーターの直径が数値上は入ることはわかっていたが,念のため仮に装着してみた.クリアランスはギリギリであった.これで,改造作業が進められる
- 何はともあれ,本体からモータを外すことからになる.モーター,電源スイッチとDC電源ジャックが取り付けられている黄色いパーツを取り外す.M4のプラスネジで締結されている.ワッシャ&スプリングワッシャでゆるみ止めされているが,ネジロック材はなかったが,緩めるのに結構な力をくわえたので,ネジ山が一部つぶれてしまった.ちなみにこの黄色のパーツは,2mm厚の鉄製である
- 取り外してから,本体側のメネジを確認した.十分な長さでねじが切ってあるのでキャップボルトで強力に締結できそうで安心した
- まずは電気的な改善.回転を開始・停止するスイッチはAC125V/10Aの波動スイッチが用いられているが,360Wを想定している回路においては問題があると考えられる.24Vで動作させるということは電流は15Aということである.このスイッチでは今回の改造では使えない
- なぜ360Wかというと,ミニテーブルソーを購入した時に付属していたスイッチング電源が360Wであったからである.このミニテーブルソーはモーターが895で動作する.直流モーターは起動時に突入電流が流れるため余裕をもって電源は考えないといけない.実際に丸鋸でいろいろなものを切断しても,順調に切断している間は電流は3Aぐらいで切れているのだが負荷がかかったときは電流は一瞬で増加している
- このテーブルソーが気に入って,もっと小さなテーブルソーを購入した.これには電源アダプターが付属しているのだが,過負荷(ちょっと厚めの木材を切断時)になったときに,アダプターから煙が出てその後使えなくなった.ヒューズさえも内蔵していない.中を開けると3端子の半導体(MOSFET?)が焼損していた.
- これ以後,電源システムを構築する必要を感じた.おかげで快適なシステムができあがったのである
- しかし,nano工作機械はnanoボール盤を含めて電源のON/OFFはフットペダルスイッチを用いる,したがってnanoボール盤本体に電源スイッチは不要なのである.いやついていると,むしろ邪魔なのである
- 電源スイッチにしろDC電源ジャックにしろ,コードが795モーター用としてもちょっと細い気がする.許容電流は守られているとは思うが,安全率を十分とっていないと感じる
- ということで,モーターは電源ジャックと直結とした.電線は安心のエーモン製自動車配線用のコードを使用,24V/400Wと想定する電流をカバーしている.固くてはんだ付けや取り回しが大変だが安全第一である
- この配線コードは太いためはんだ付け時に熱を持っていかれて少し難しい.そこで,はんだごてのこて先温度を通常の電子回路で使用する設定温度の370℃ではなく420℃へ変更する
- フラックスは必ず必要.無洗浄タイプを使う.モーター電極と配線コードにたっぷりつけておく.フラックスは無洗浄タイプといってもやはり洗浄が望ましいとされるよう.パーツクリーナーが有効という情報もあるが,私はそのまんま放置である
- モーターの電極にはんだごてをしばらく当てて,温度を上げておく.配線コードは太くて硬いのを利用してモーター電極の穴に通して,固定しておく.銅線部分にこてを当てて予熱しはんだを当てて溶かしながら,電極にはんだ付けする.こてを当てておくと,フラックスの作用で馴染んで線束中に溶け込んでいく.はんだの表面にテカリがで出るのを見計らいこてを離してしばらく保持しておく.熱いが我慢!
- ハンダは鉛入りがおススメ.断然はんだ付けがやりやすい.煙を吸わないように注意すること
- ノイズキラーは,0.1uFセラミックコンデンサを使用.安心の村田製作所製である
- できるだけ電極近くに,できるだけ足を短く取り付ける.モーター缶へのはんだ付けはひと手間かける.モーター缶表面をやすりやカッターの刃なので荒らしてから,フラックスを塗布してから予備半田を行っておく.コンデンサの足をマスキングテープで仮固定しておくとやりやすい.カプトンテープを出してくるのが面倒だったのでマスキングテープで代用したが,問題なかった
- たまたまこのモーターには,くぼみがあったので,そこへコンデンサをはめ込んだ
- あと電気回路としては,DC電源ジャックがある.これも今回の仕様では不安なので,Aliexpressで購入しておいた大きめのものに変えておいた
- 穴拡大処理が完了したら,DCジャックを取り付ける.電線が太いので苦労した.絶縁として簡単なのは熱収縮チューブなのだが,電線が直角近く曲げないといけない状態であったので,曲げに強いPVCキャップを使用した.ストックしておくと何かと便利である
- 取り付けネジはキャップボルトを使いたかったが,近くのDIY店にはM5 10mmは無く,プラスネジしかなかった.スプリングワッシャでゆるみ止め対策とした
- ショート,断線防止のためお約束の収縮チューブで処理する.ポリオレフィン系のものが安価でバリエーションがあるが,収縮がなかなか難しい.はんだごてや,ホットガンなど一通り試したが,ポケトーチが一番やりやすく安定している.そうそう焦げたり溶けたりはしない.
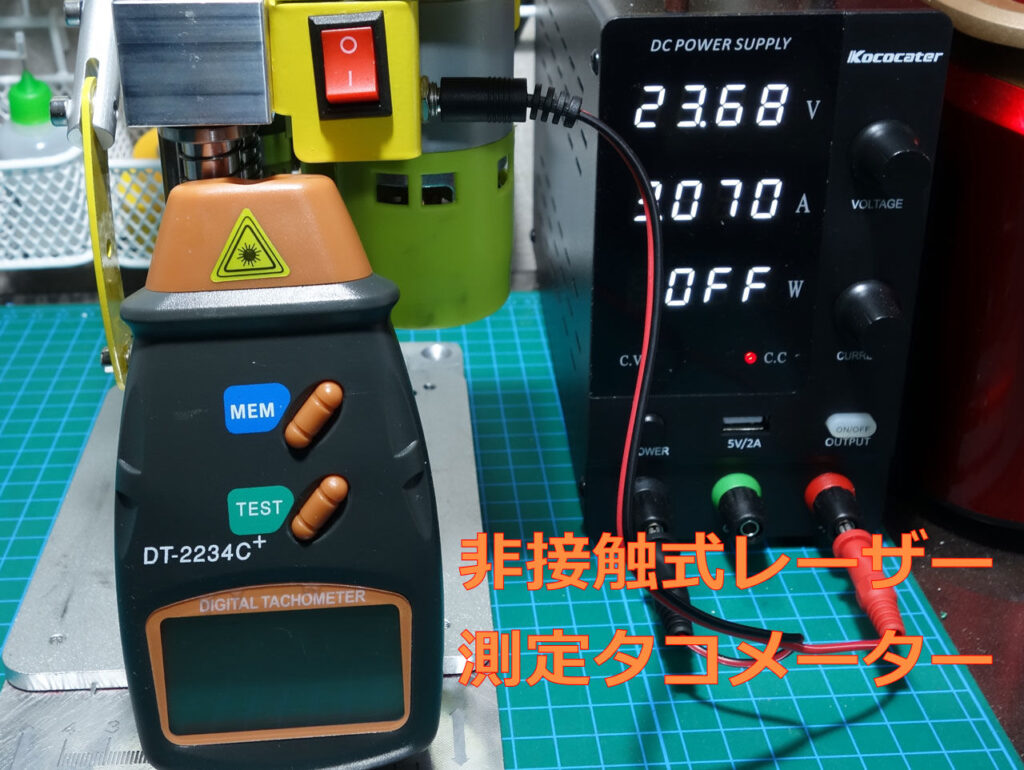
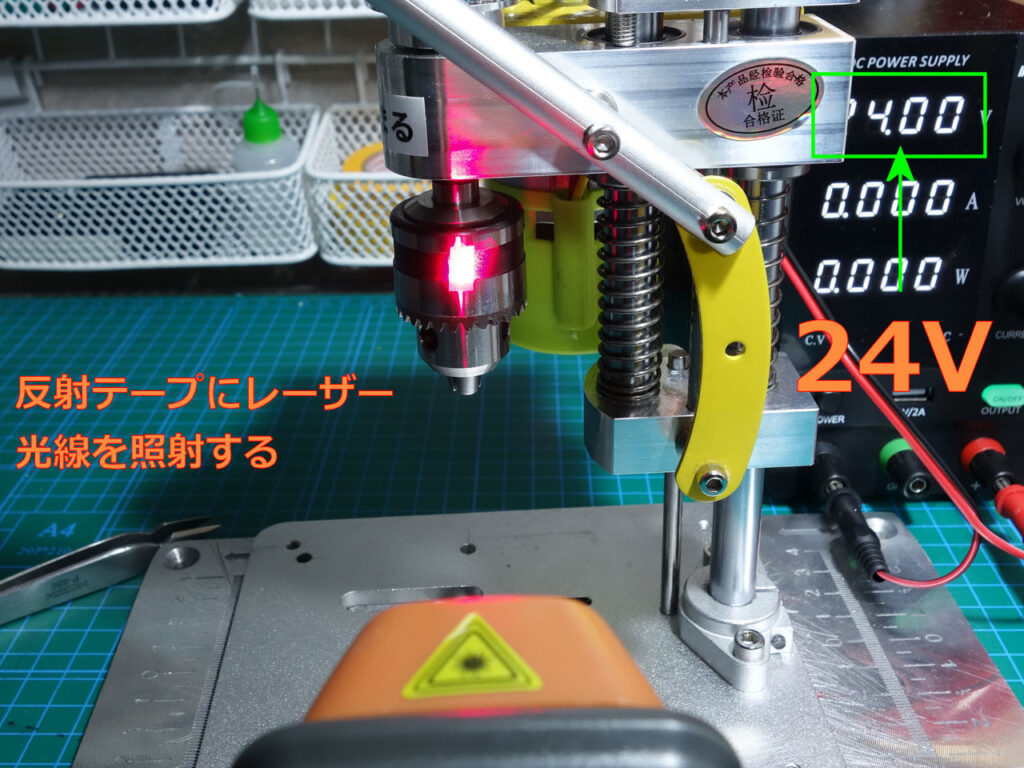
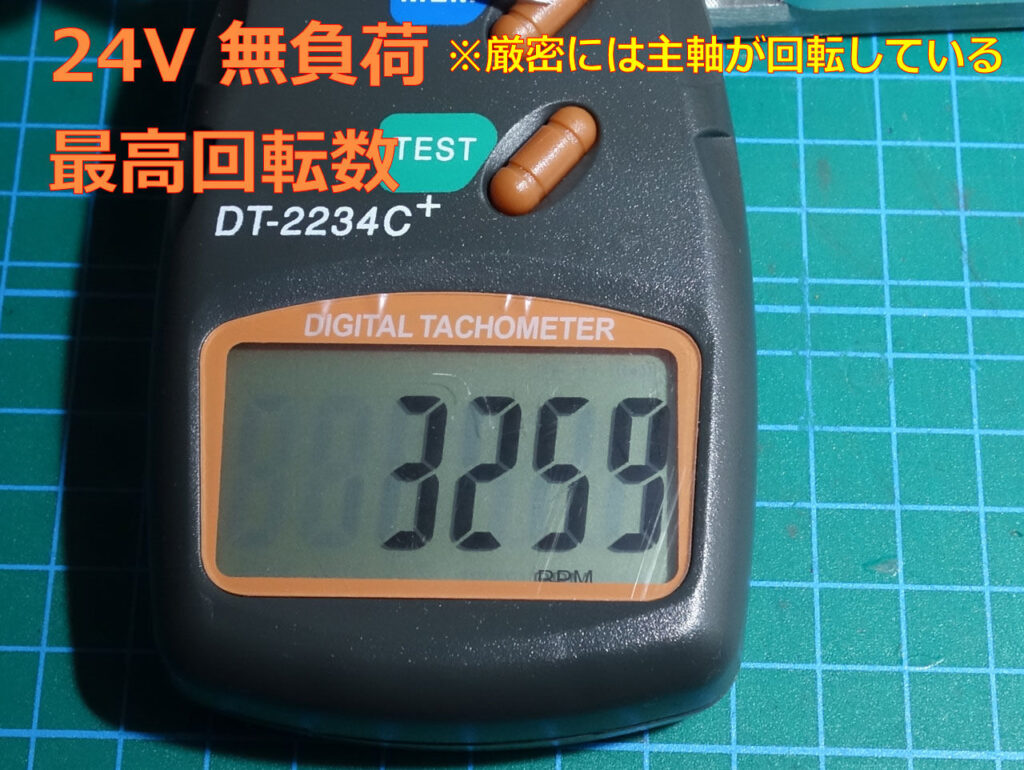
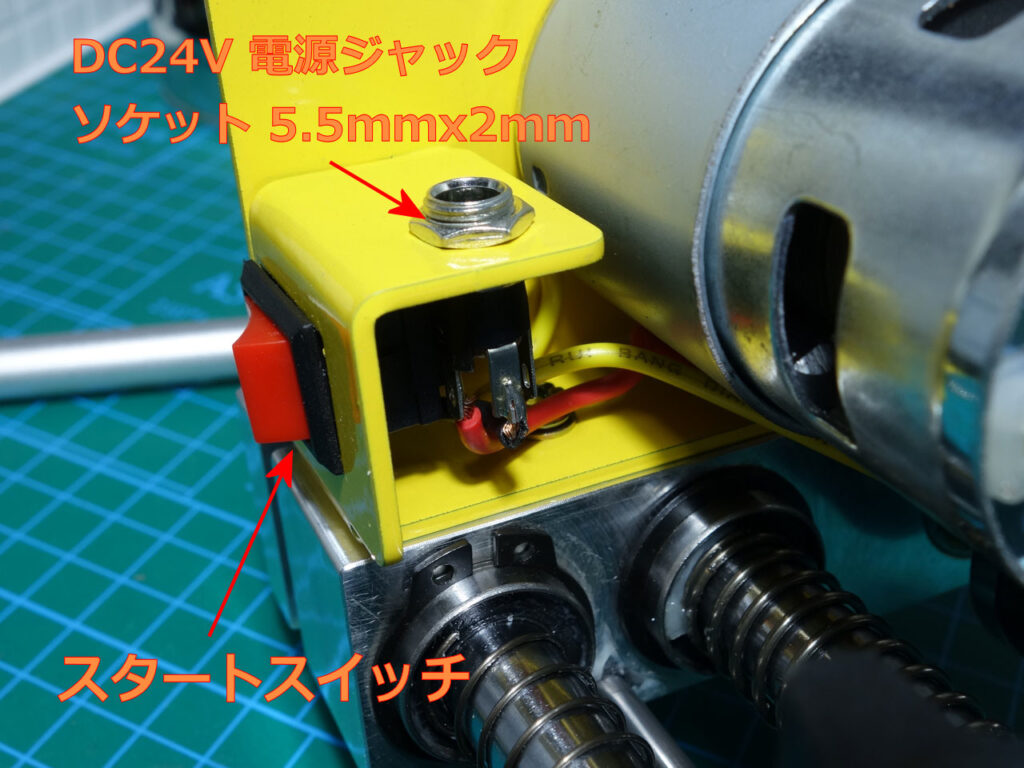
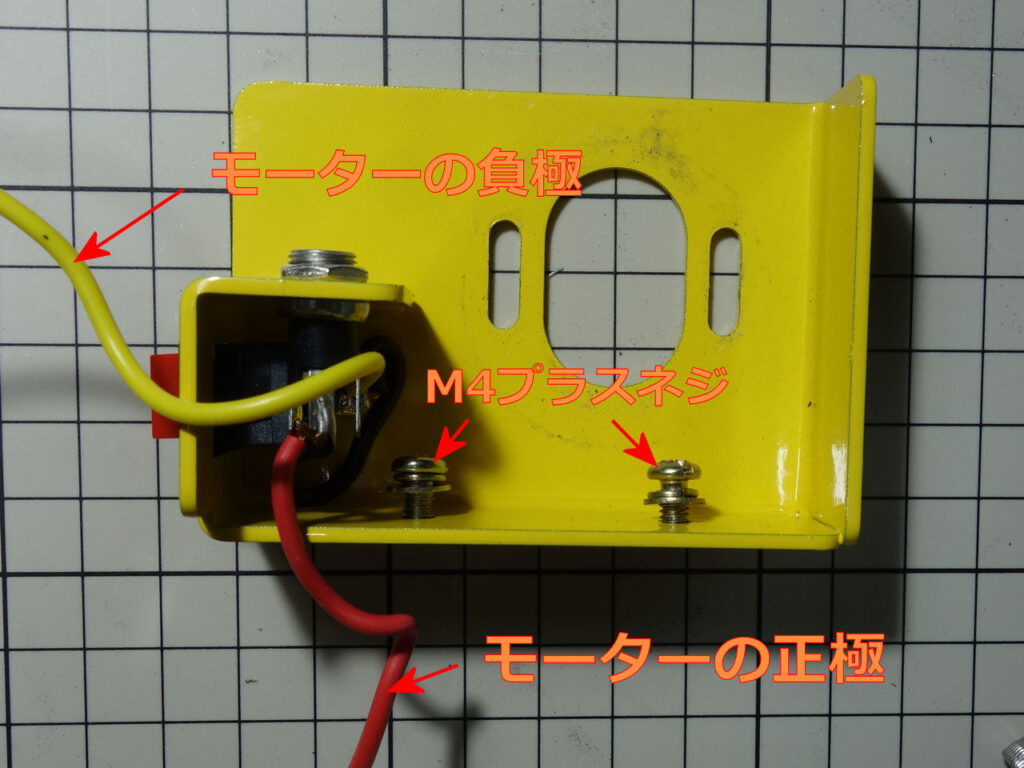
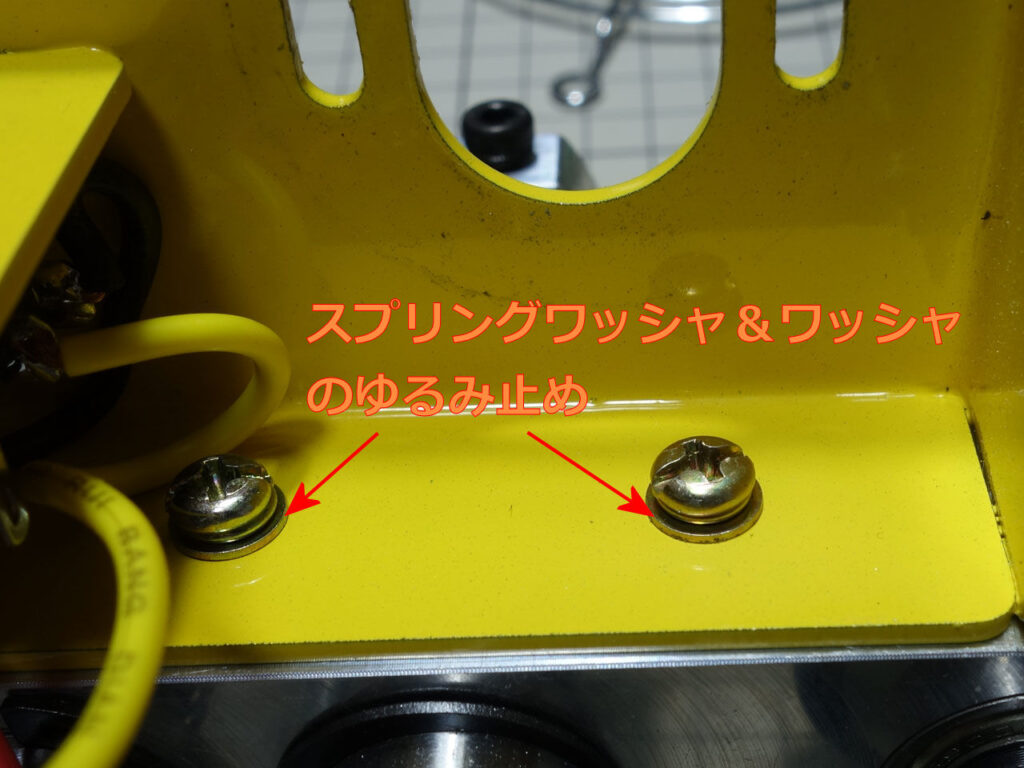
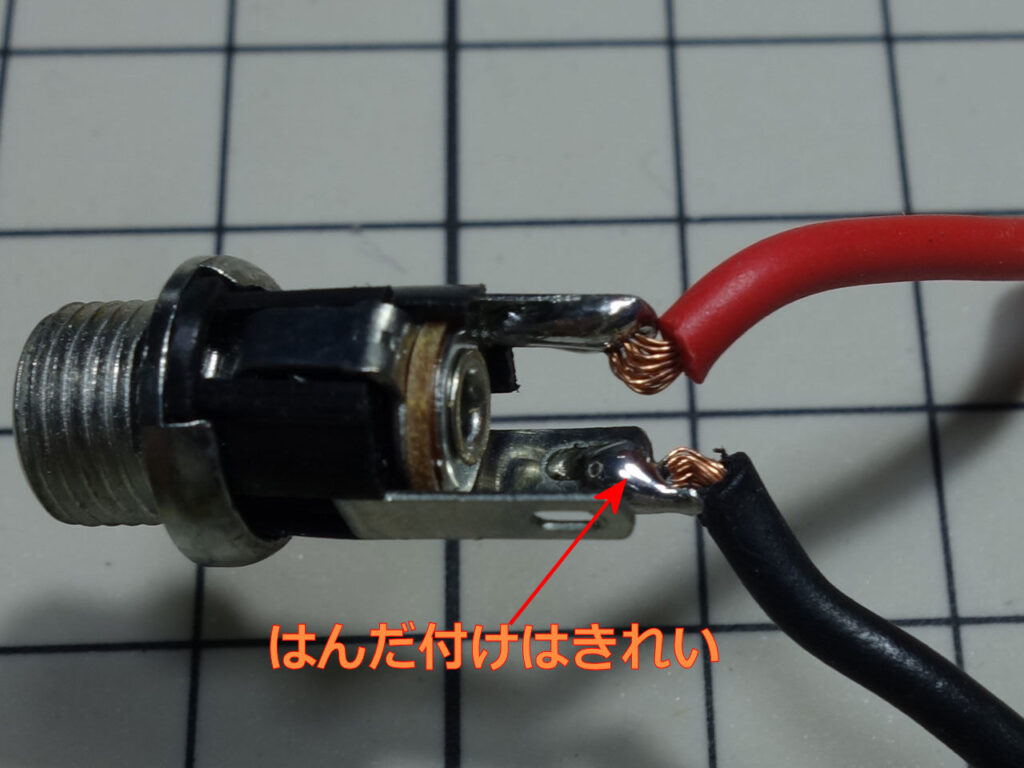
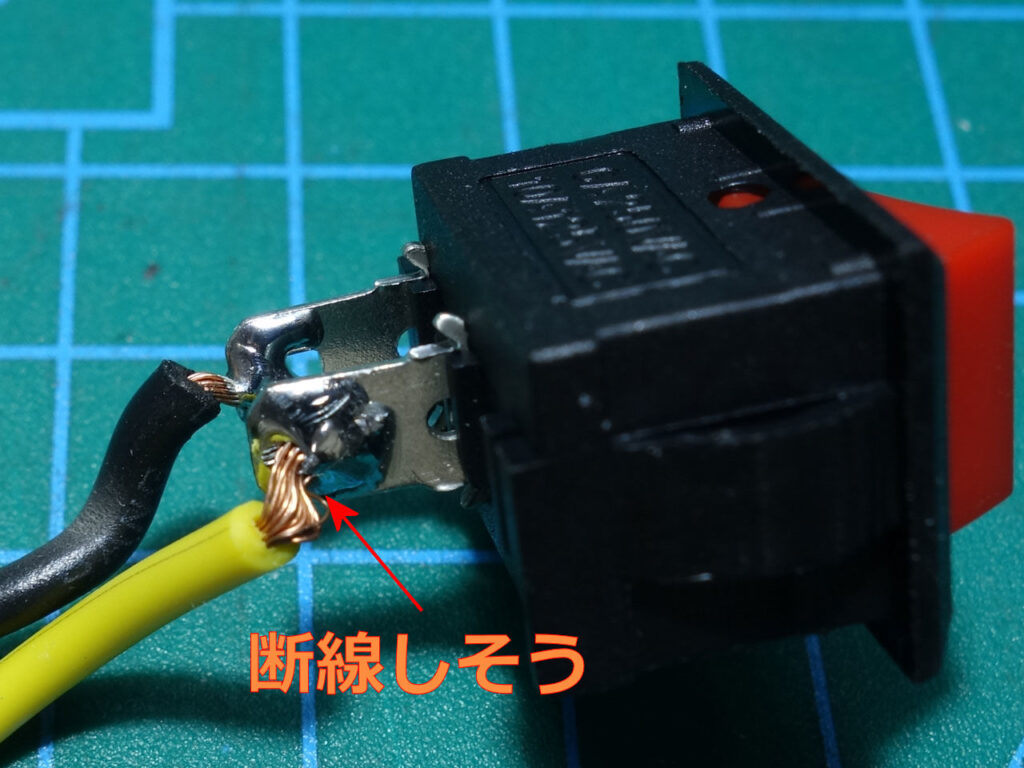
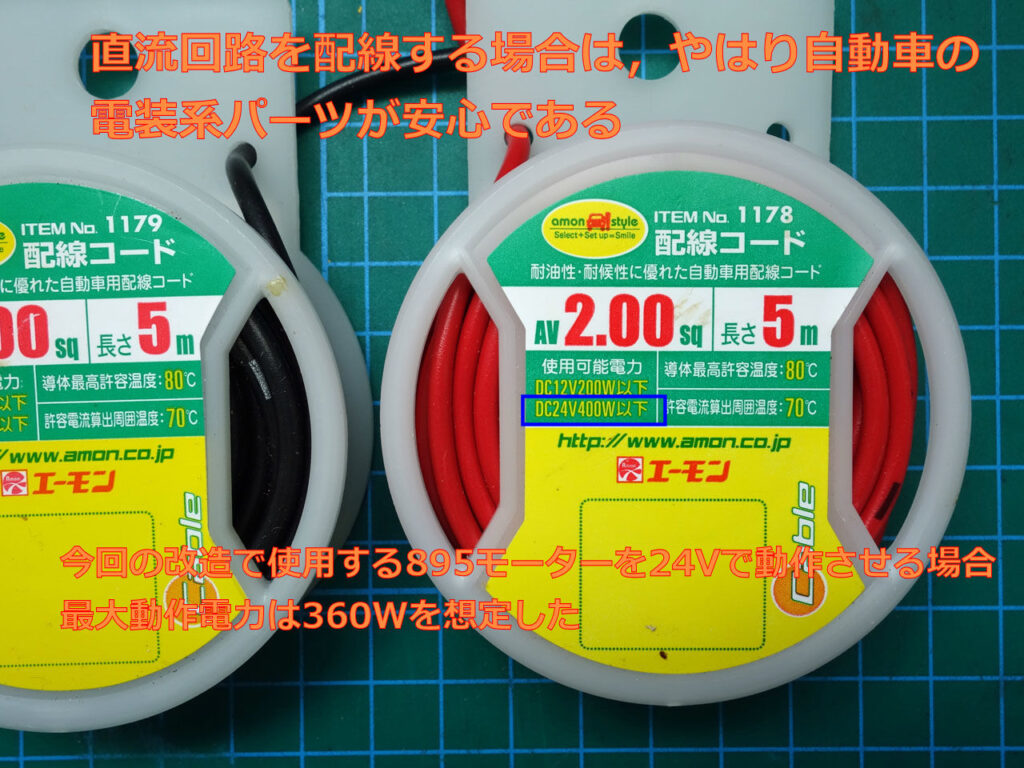
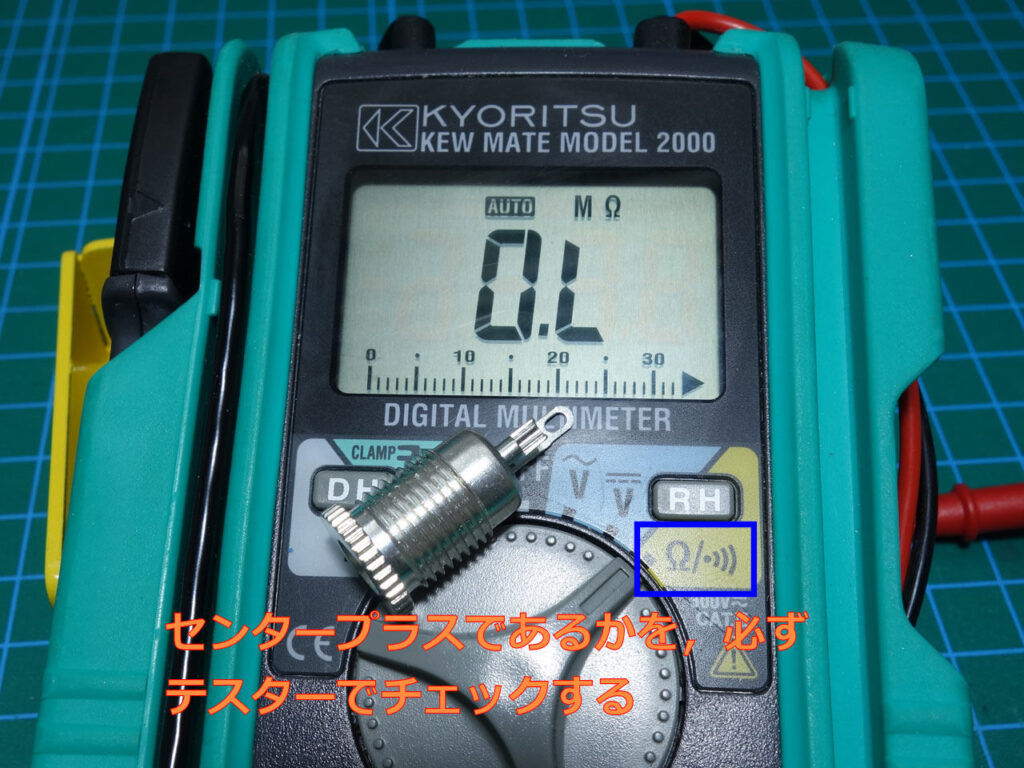
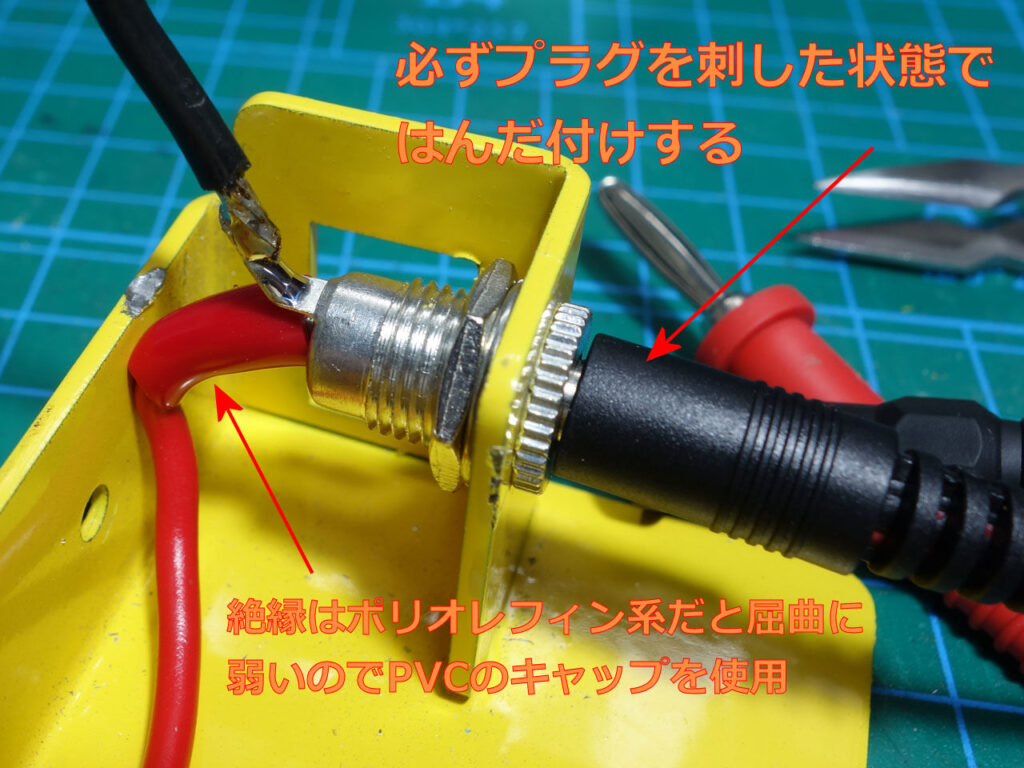
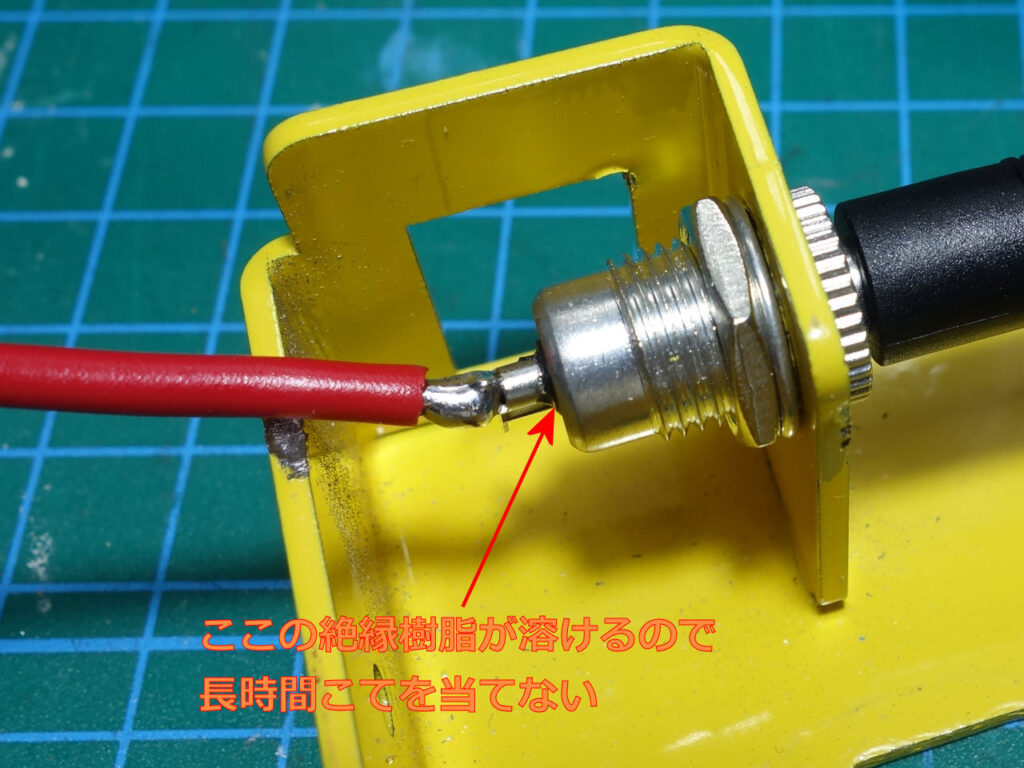
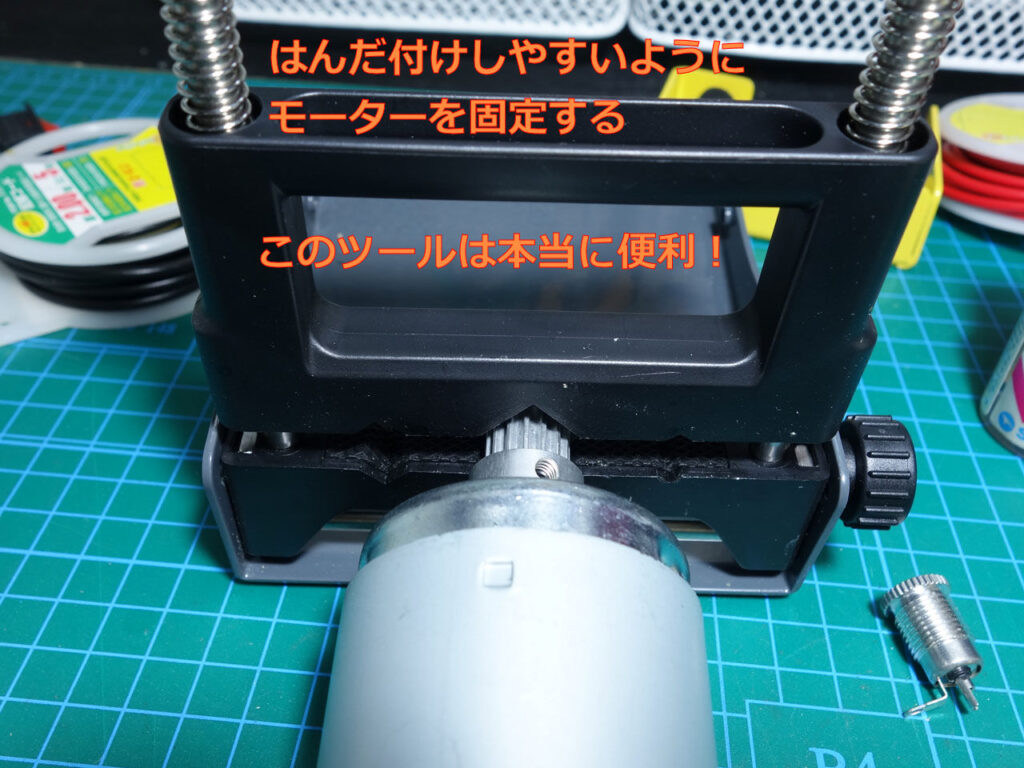
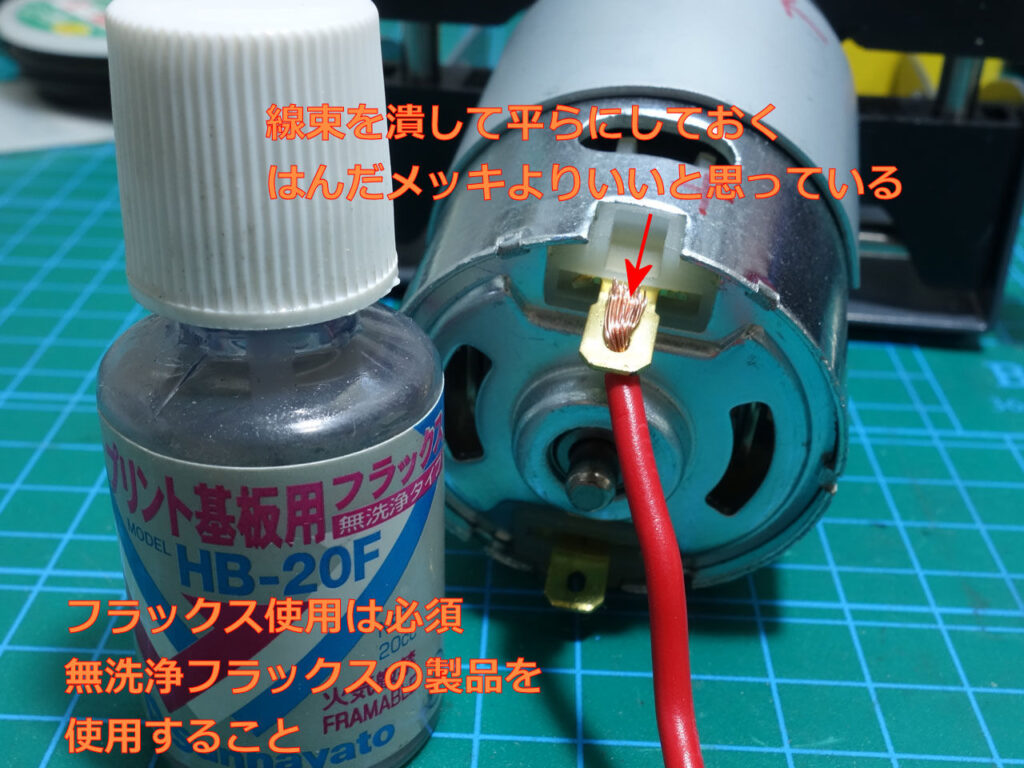
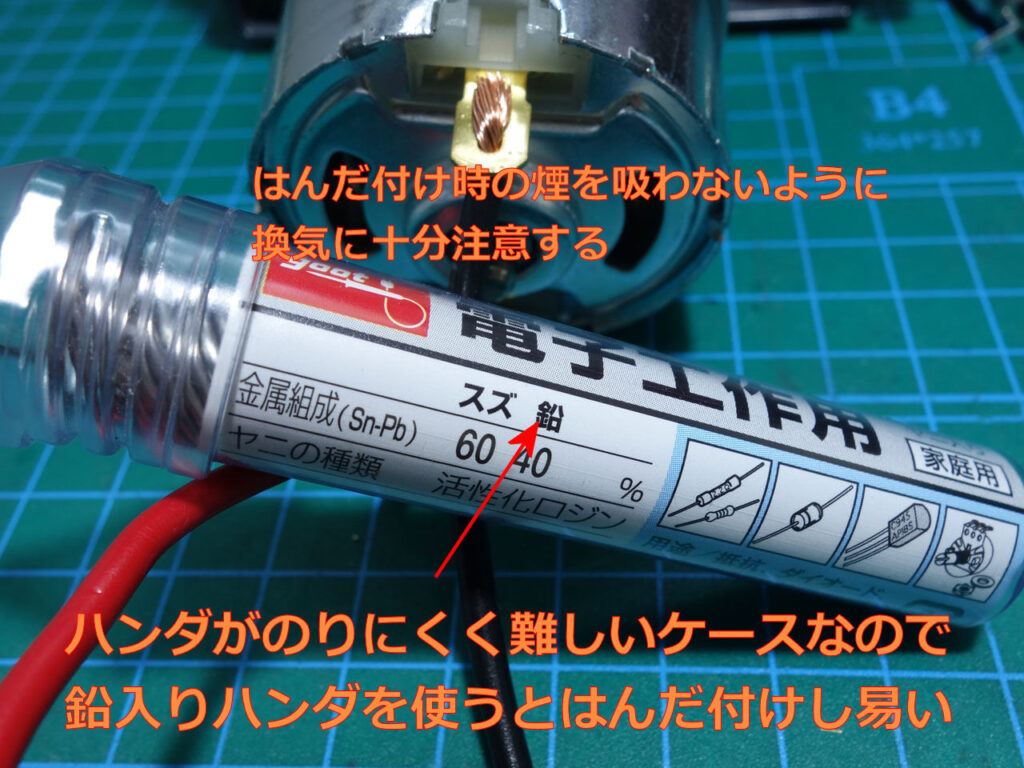
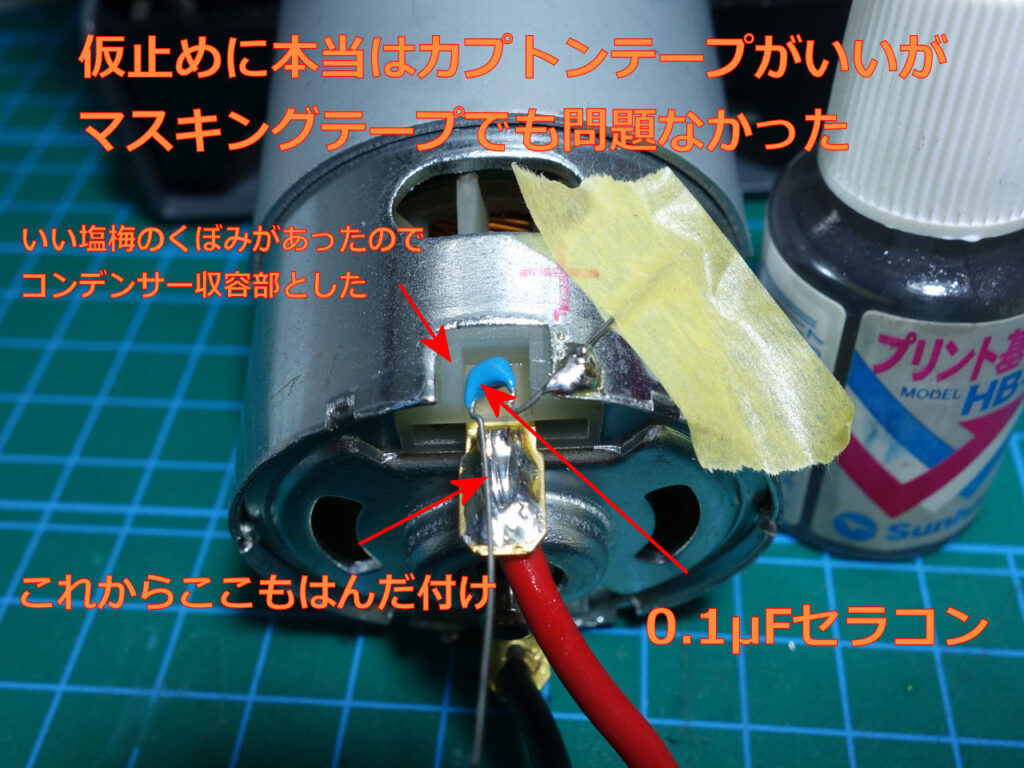
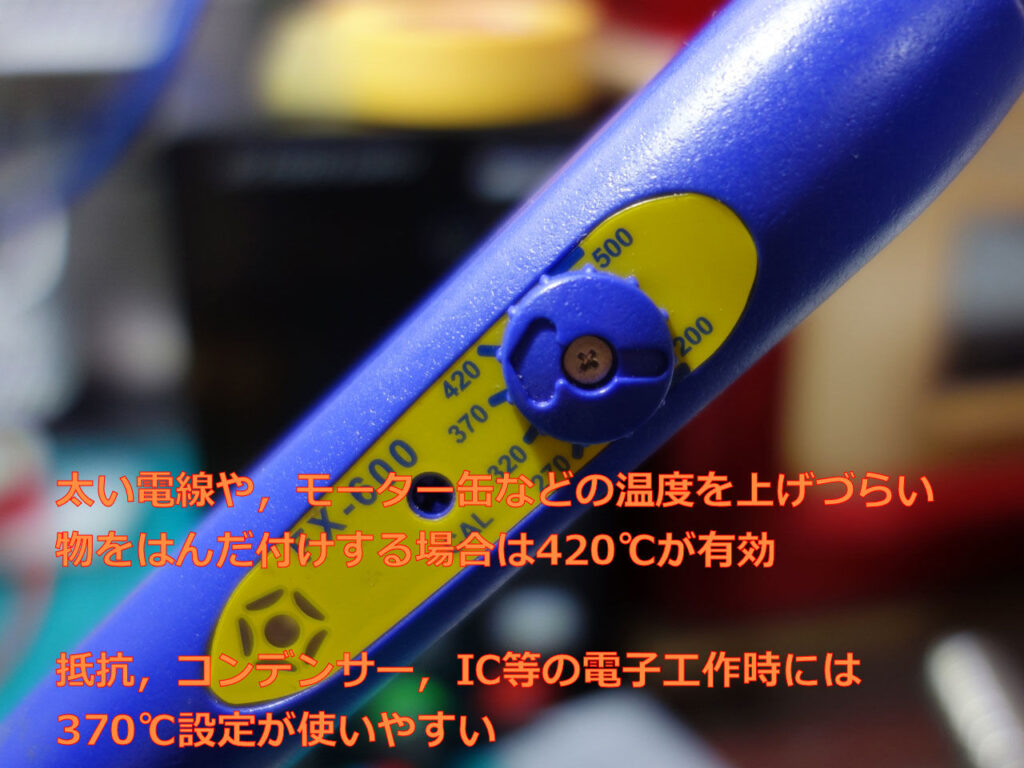
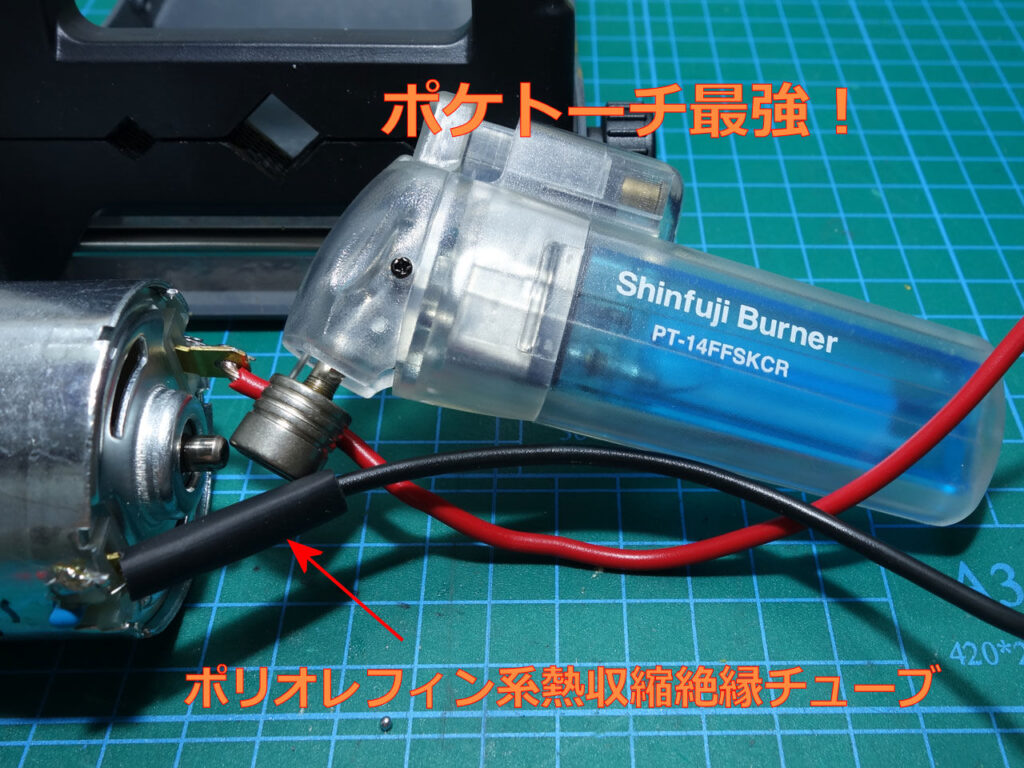
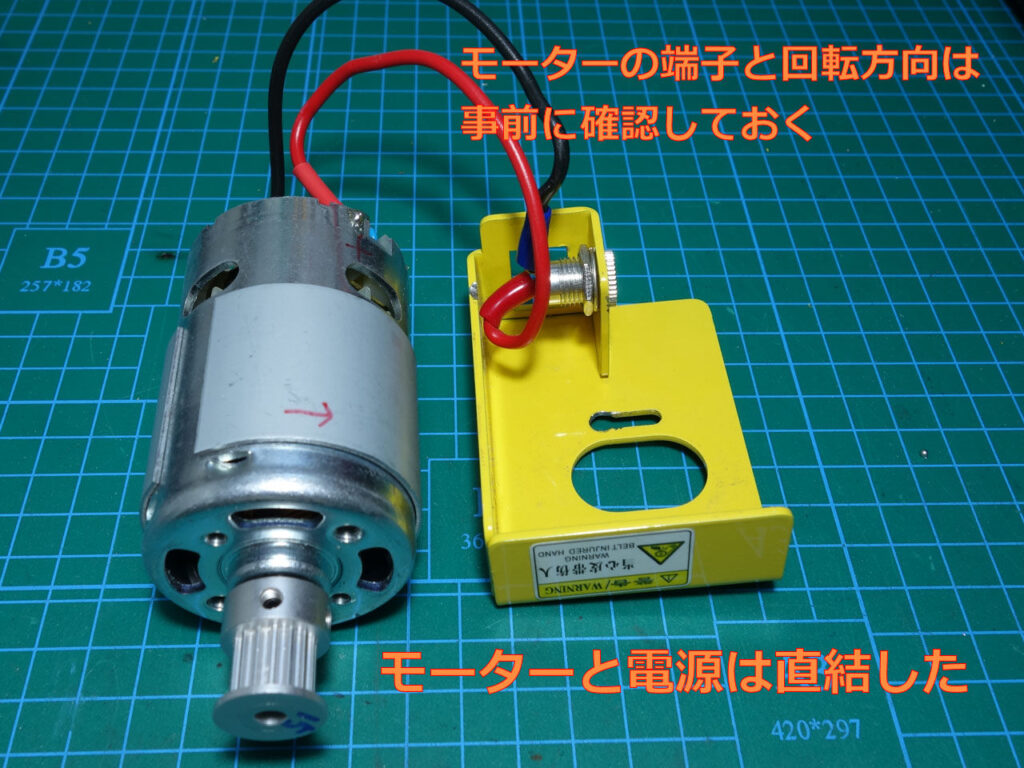
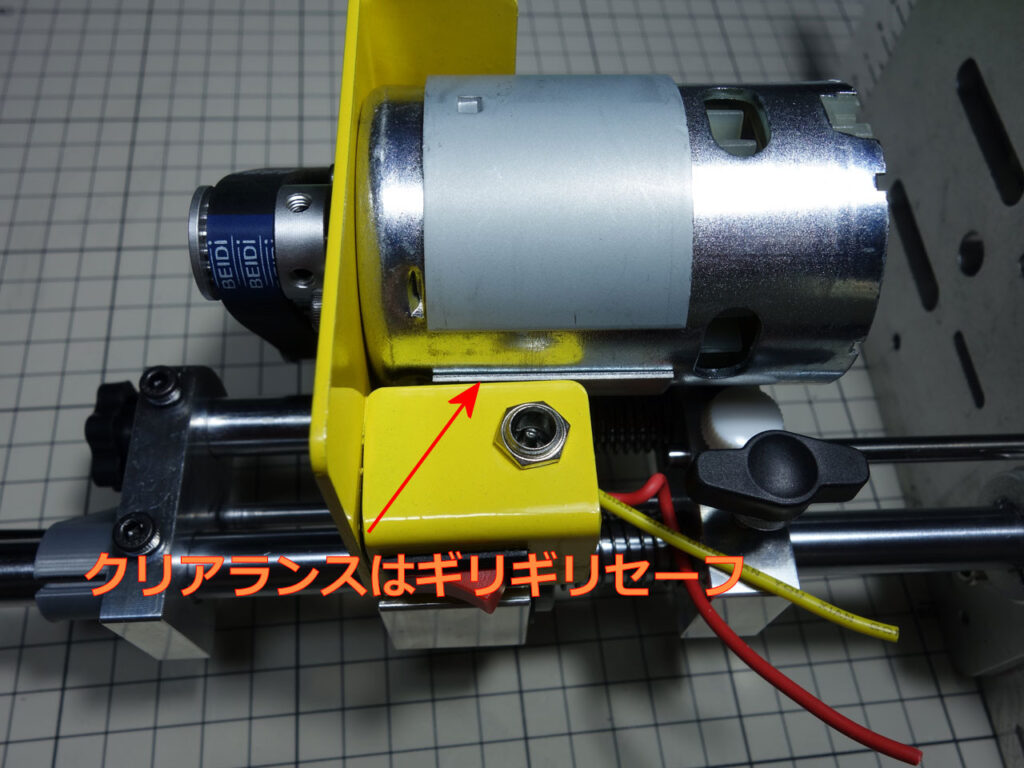
- モータには取付用のビス穴が2種類開いている.M4メネジとM5メネジである.当然M5で取り付けることにするのだが,それが面倒なことになった
- 795モーターはM4のみなので,ボール盤側取り付け部にはM4用の溝がある.この溝の幅ではM5ネジが入らない.入らないだけでなくタイミングベルトを試適してみると張りすぎの状態となってしまう.そこで,溝部をリューターで削っては合わせてを繰り返した.結構な切粉がでる.導電性の金属粉なのでマスキングテープで養生した.こういう時には100mm幅のものが便利である
- そして便利なのが,ハンディクリーナー.はっきり言って吸引力は強くないが,そこが利点の一つ.いらん物は吸い込まない.粉物が得意である.おススメ!
- リューターで溝の対角部分にあたるところをM5ネジが入る状態まで拡大.この状態で仮着してタイミングベルトを試適したが,パンパンに張った状態となっていたのでやり直し
- モーター取り付けパーツの諸加工が完了したら,本体に取り付ける.デフォルトではM4 プラスネジであるが強固に締結するために,キャップボルトを用いることにした.思い切り締め付けて,ネジロック材を流し完了のはずであったが画像で右側のネジの頭がモーターに干渉するのが発覚
- 手持ちの六角穴付き極低頭ボルトで何とか収まった.今回のようにネジの頭が高いと干渉することは多々あるのでストックしておくと便利である
- DCジャックは許容電流が大きい分(Aliexpress商品サイトによれば10A)取り付け穴も大きい.そのためφ11mmの穴あけ加工が必要となる.奇数サイズがあるステップドリルには11mmがあるので,これを使用した
- 穴開けを進めていくと先端が突き当たってしまったので,斜めにして加工したため傷がついてしまった.目立たない場所とはいえ,ショックであった
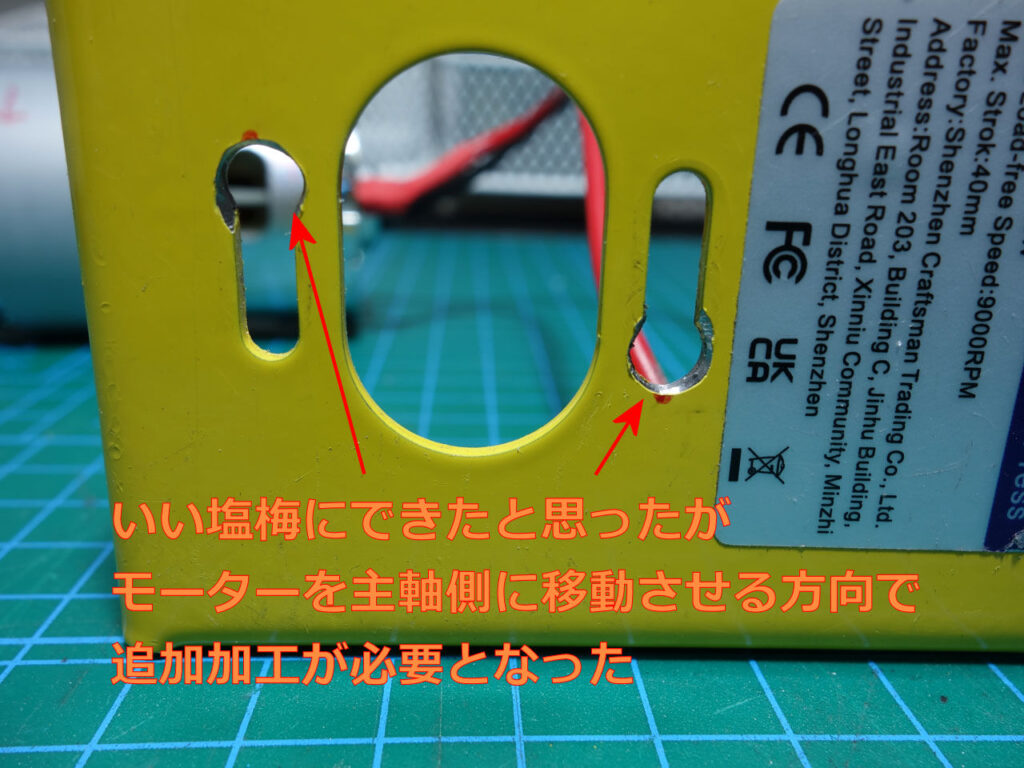
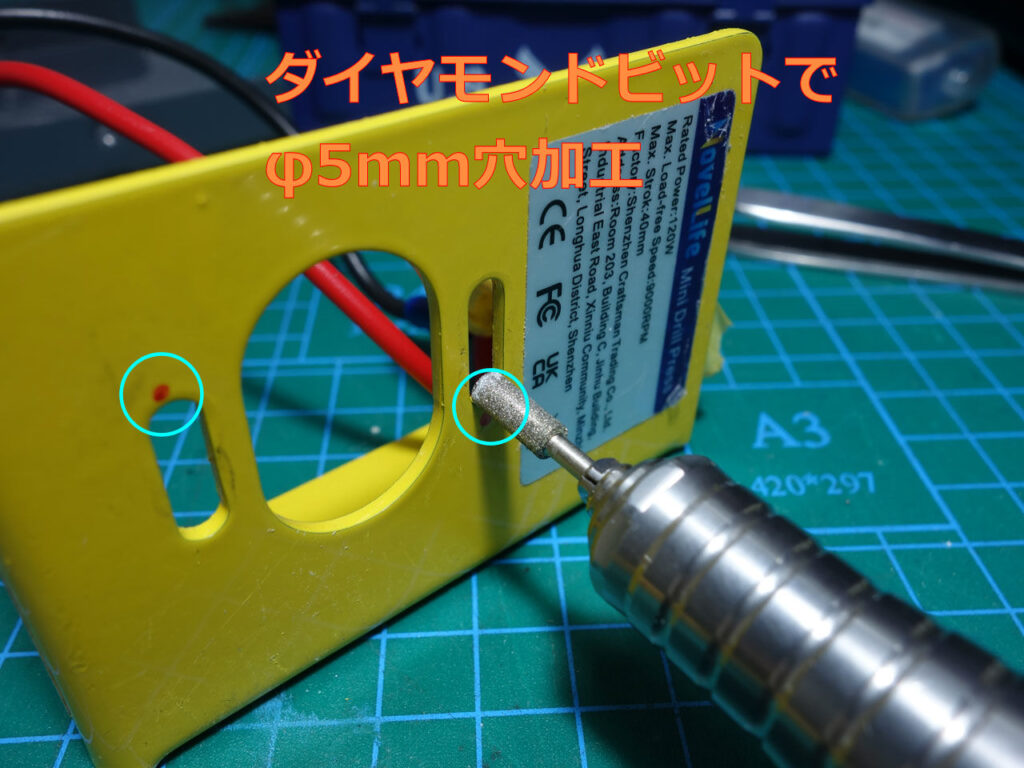
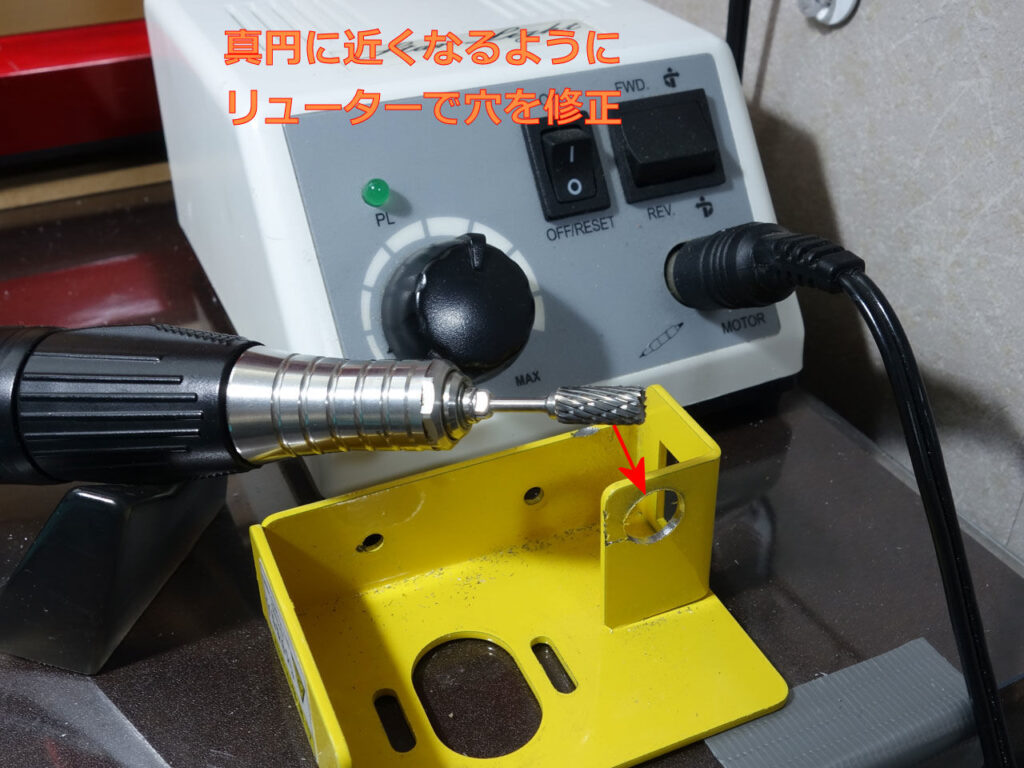
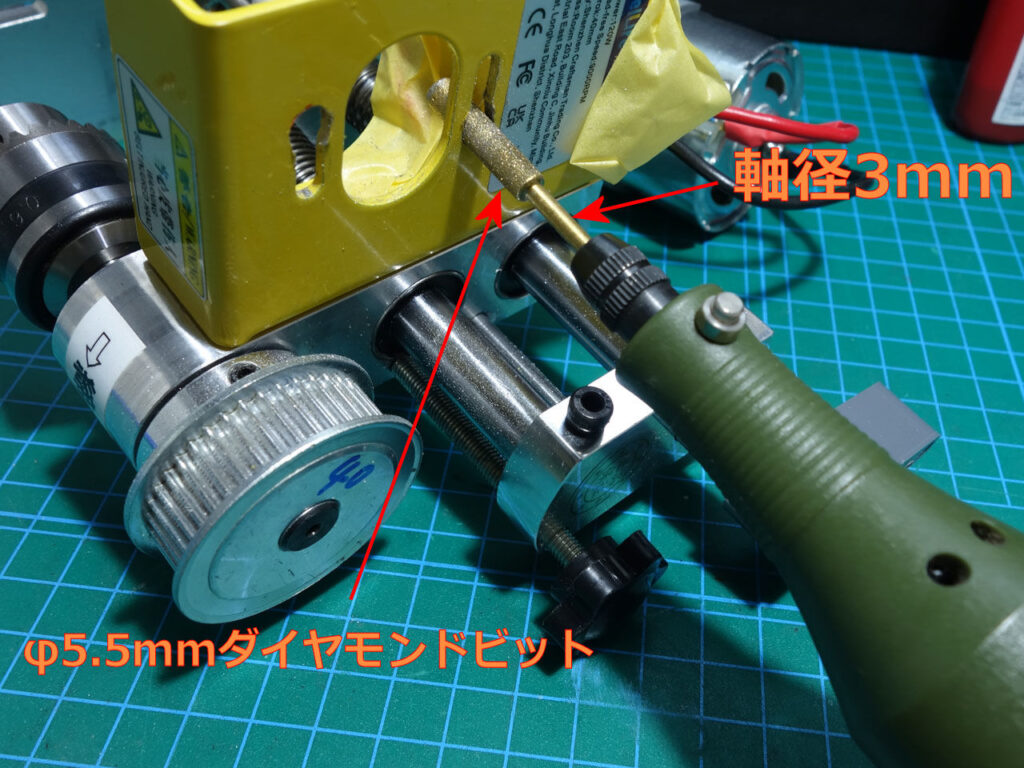
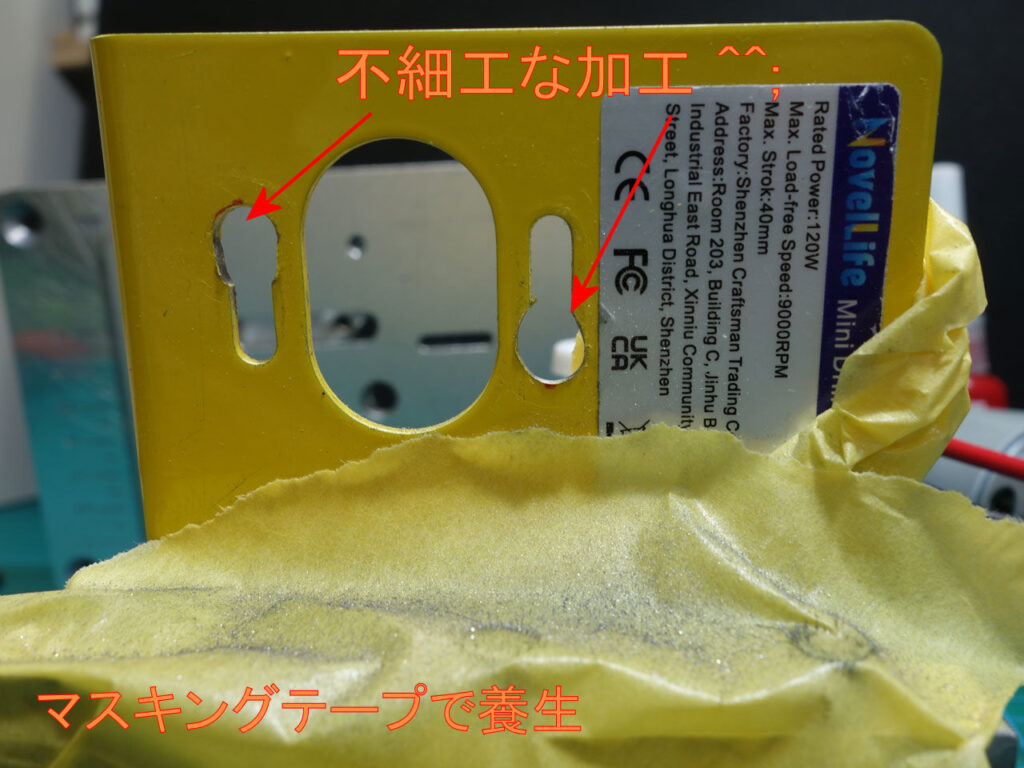
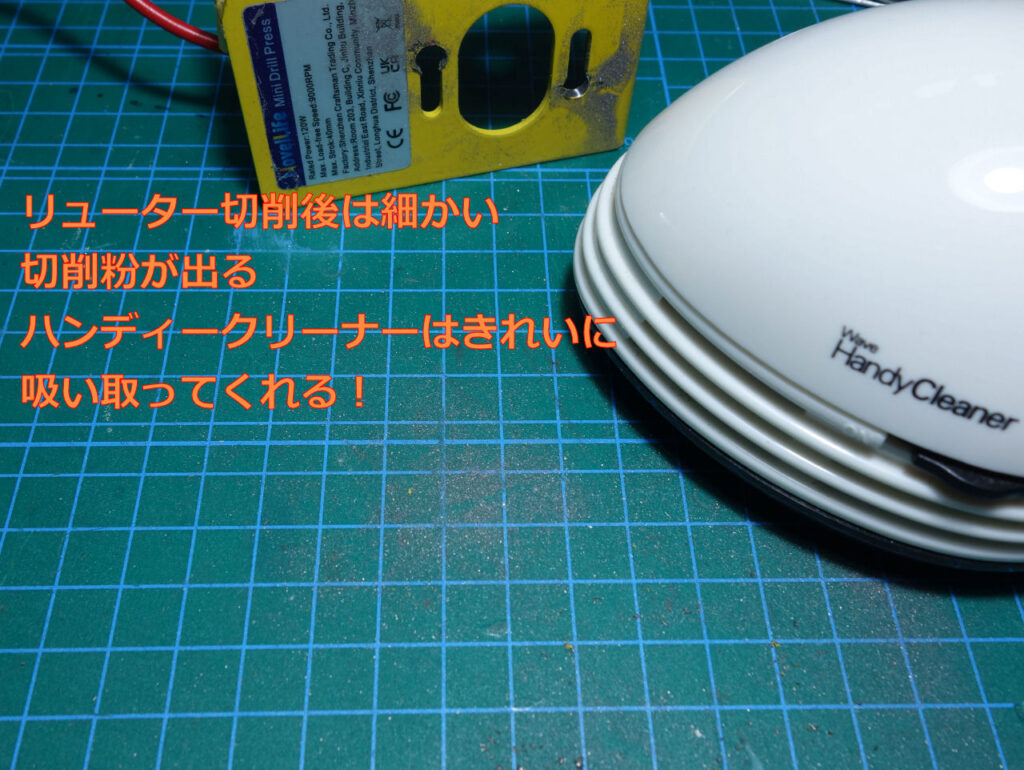
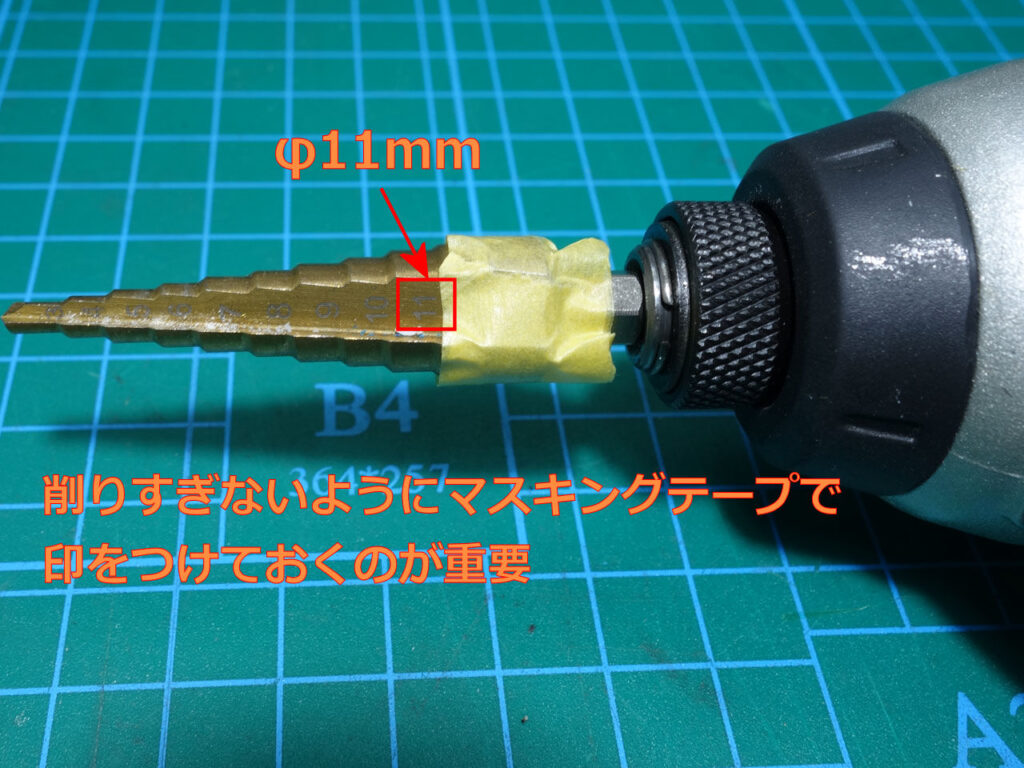
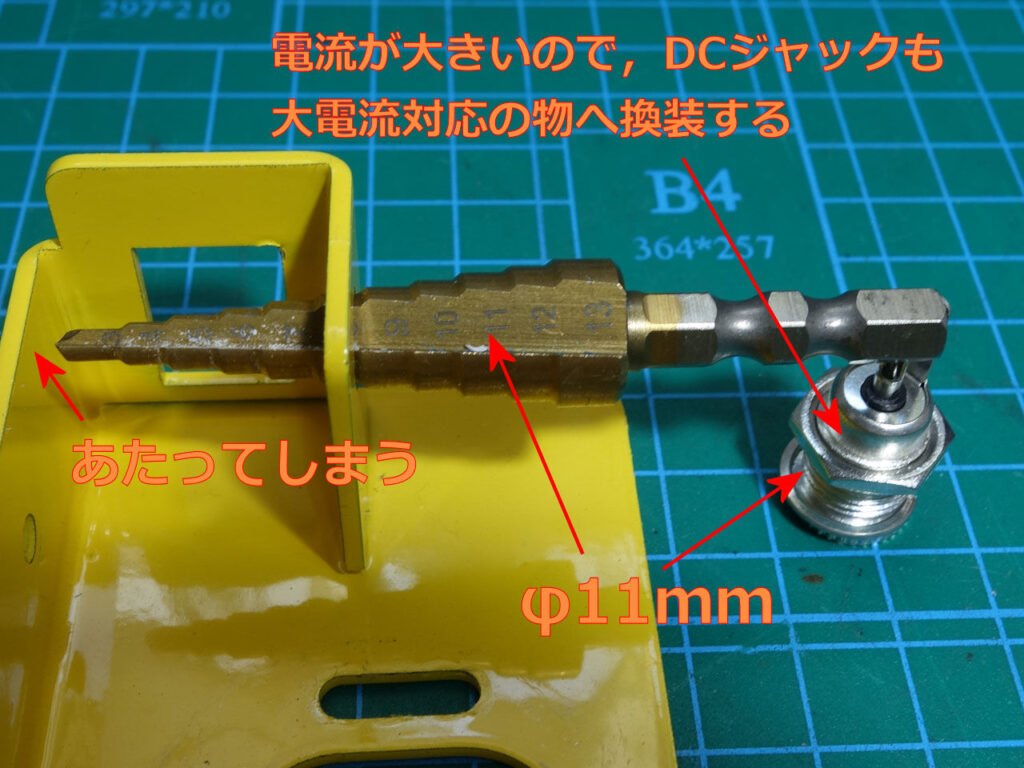
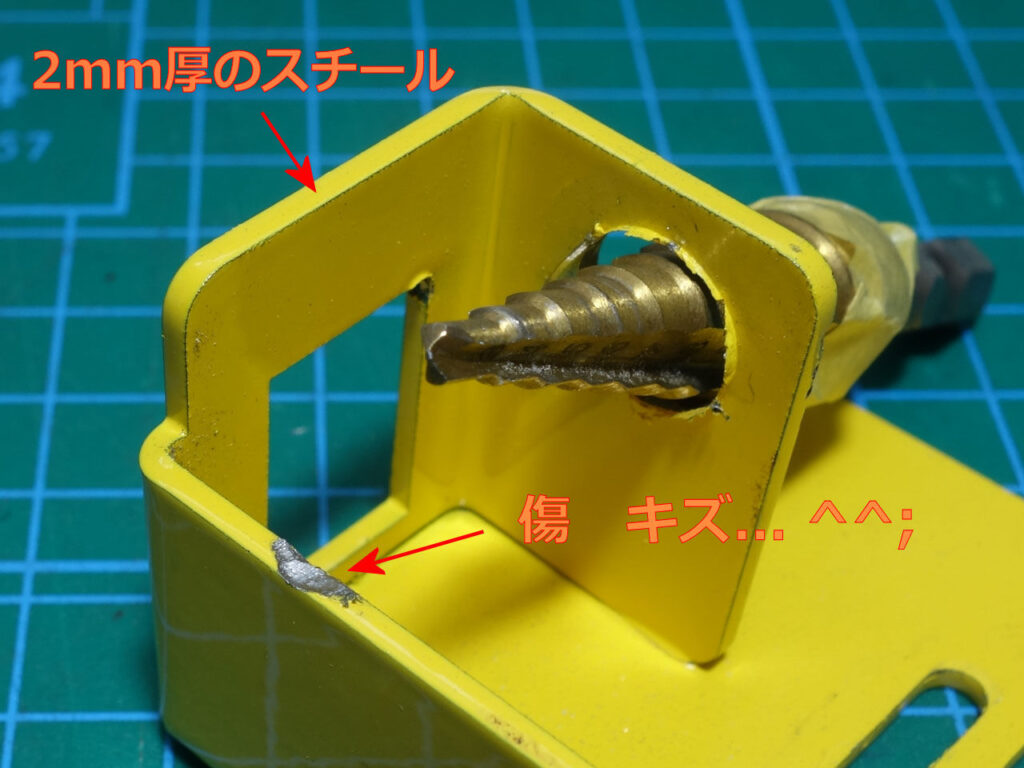
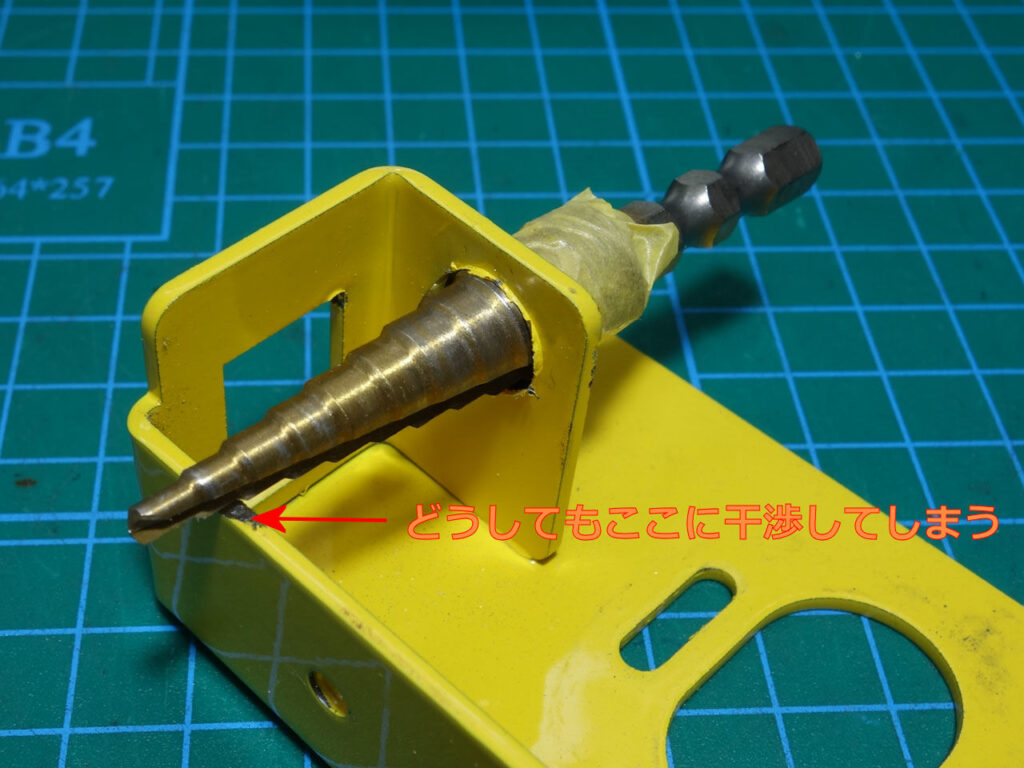
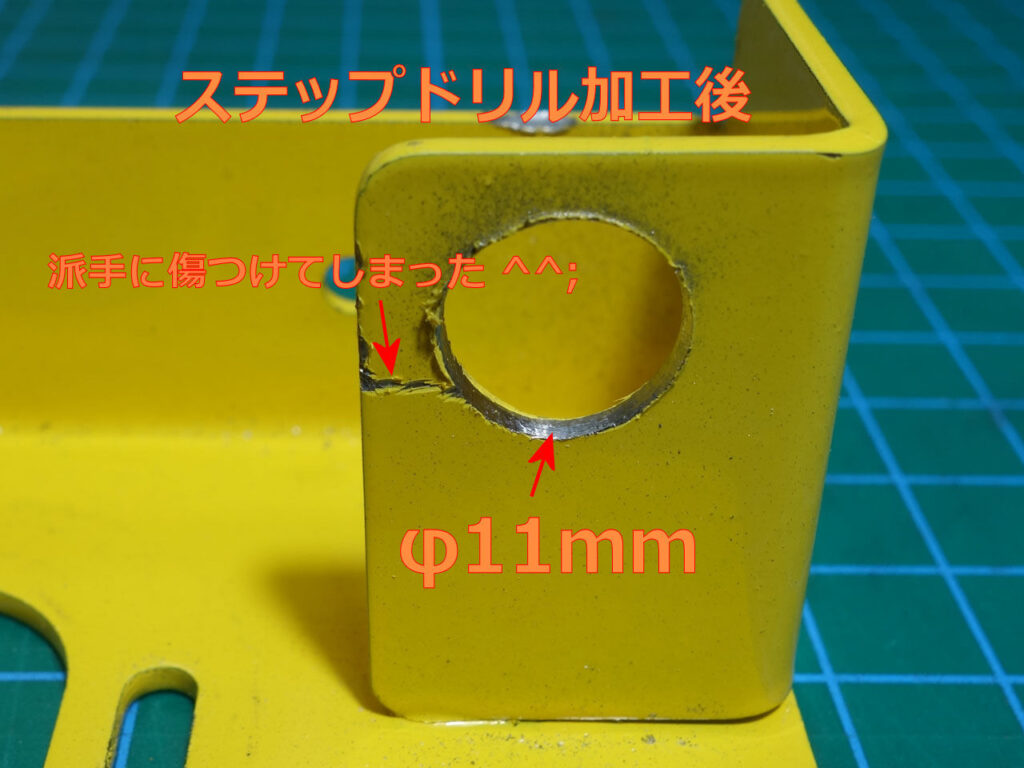
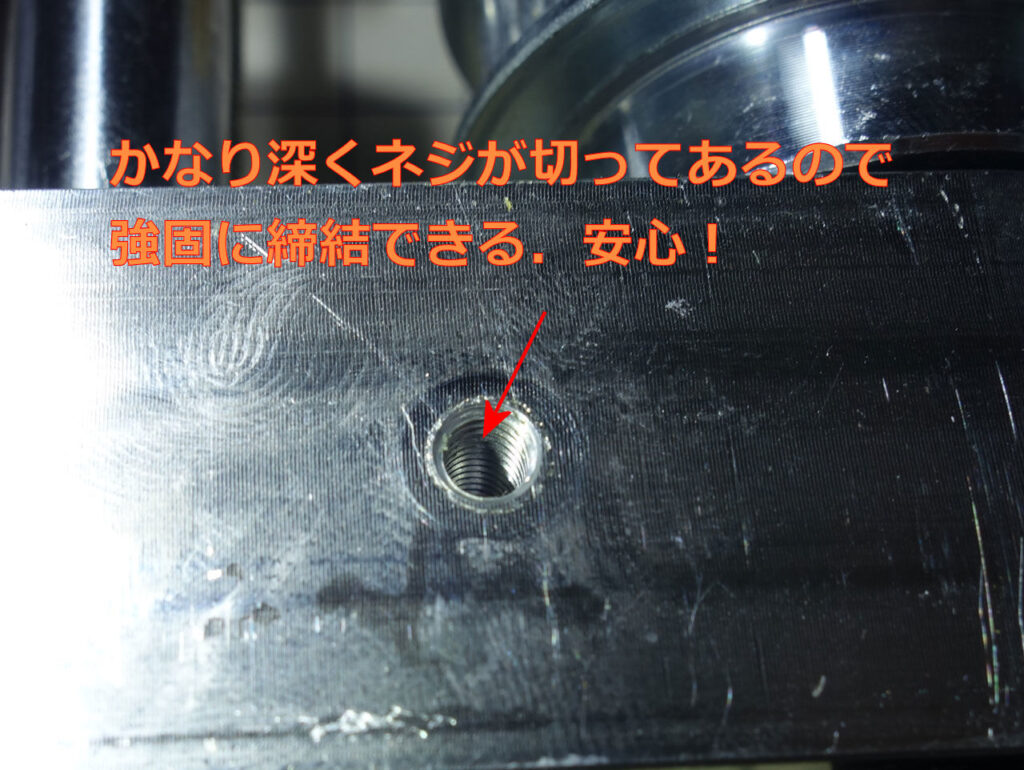
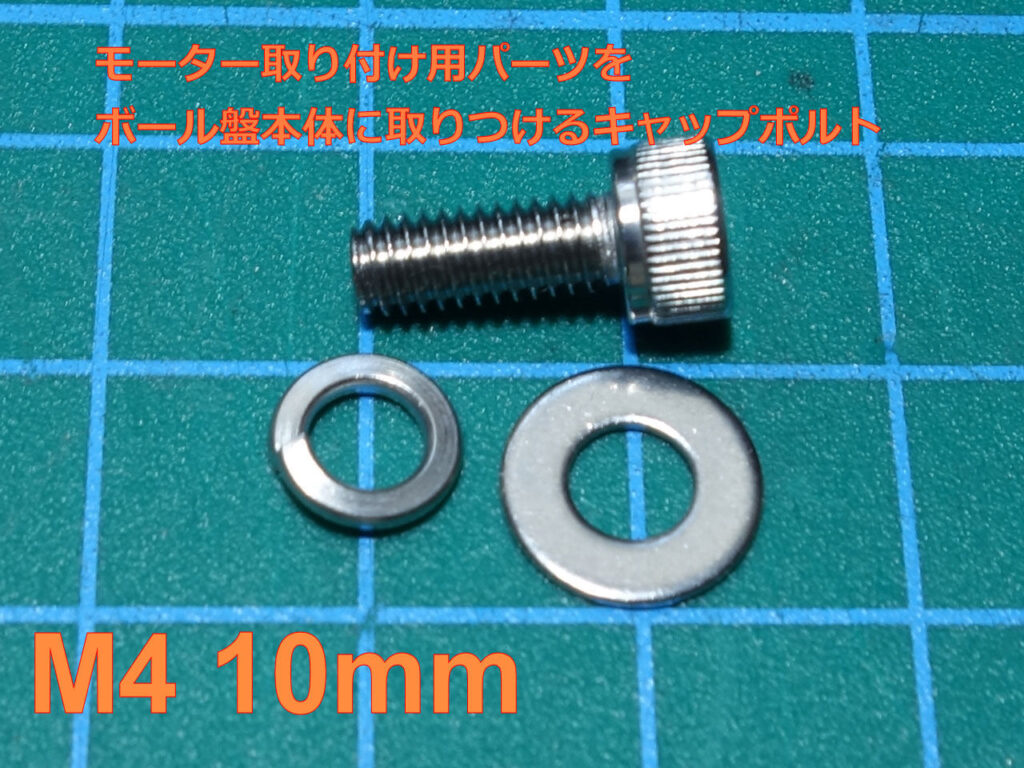
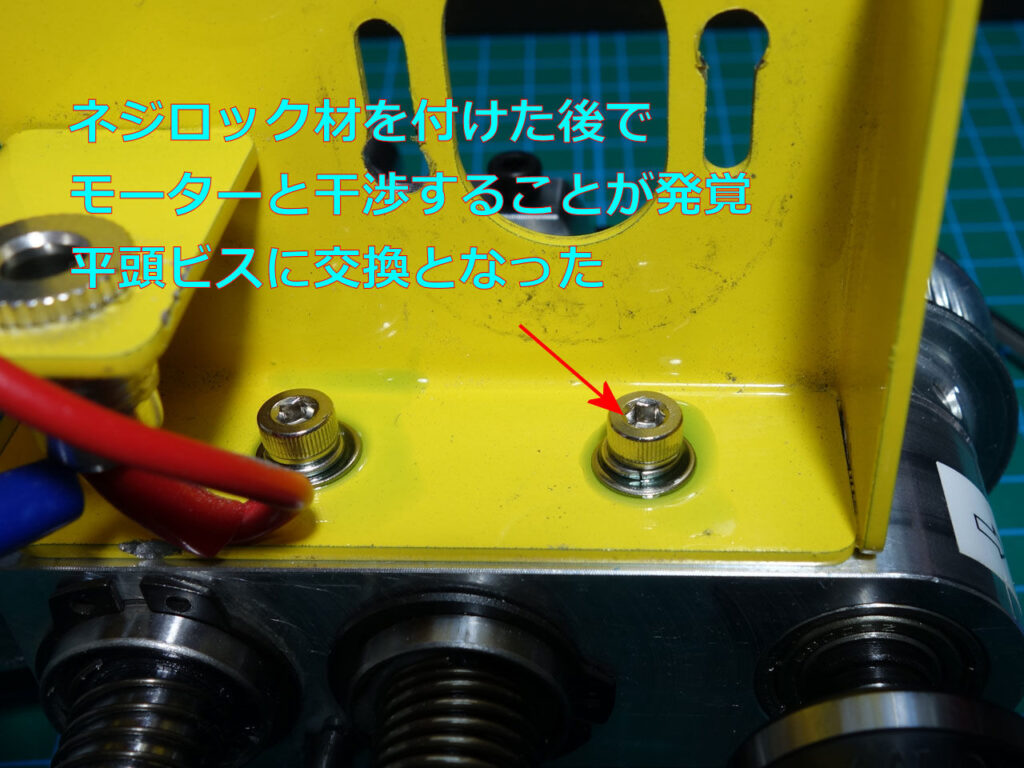
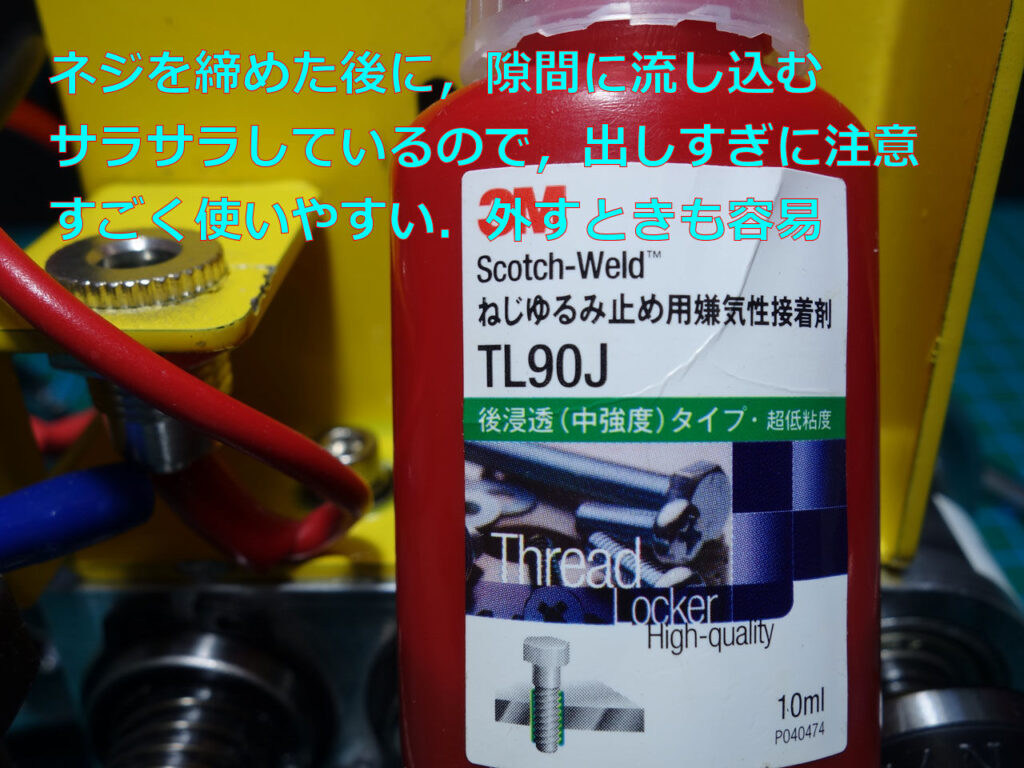
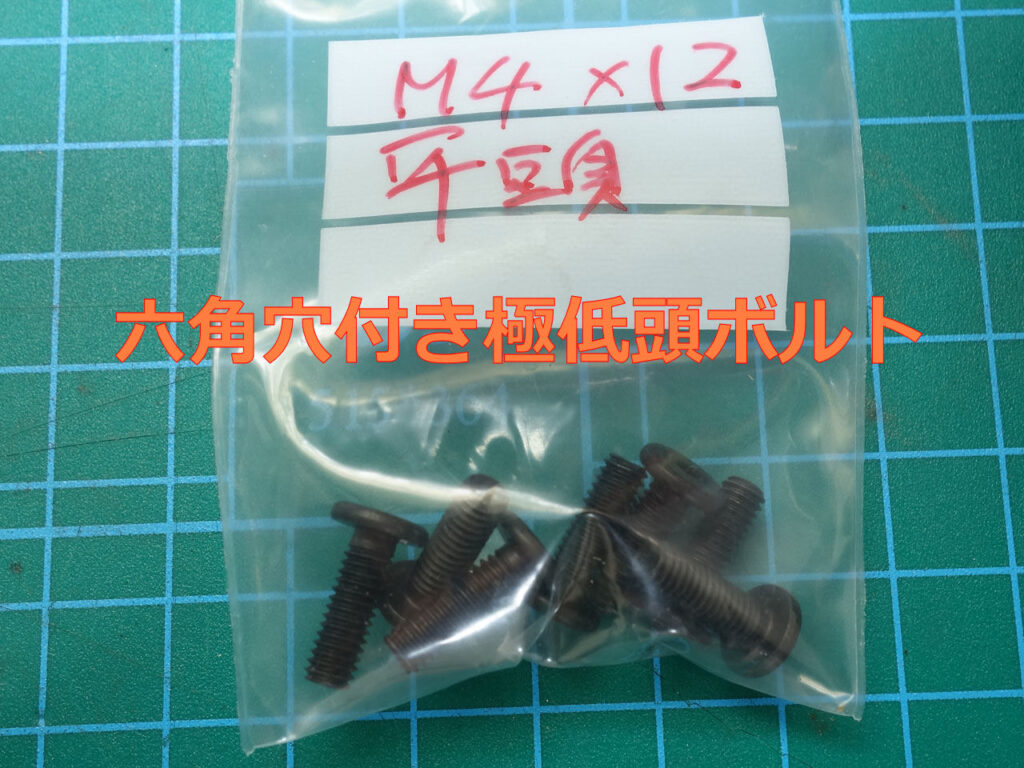
- 主軸を上下するハンドルはアルミ丸棒である.本体とはM4キャップボルトで連結される.丸棒に開いている穴にキャップボルトが通され,本体に固定されるのだがこの穴がキャップボルト径よりかなり大きくガタが大きい.さらに丸棒の曲面と締結されるため,ボルトとは線で接触するため極めて安定が悪い
- そこで,丸棒の代わりにアルミフラットバーを使い,キャップボルトとは面で接触するように改造した.基本的な機構はそのままである
- フラットバーの先端は,弧状のスチールのプレートを挟み込む形でボルト止めする.ガタの出ないようにかつきつすぎないようにM4のキャップボルトとフランジナットで調整する
- 改造前の丸棒の先端は幅3mm程度のスリットがあり,そこに0.5mm厚の2枚のワッシャを介して弧状スチールプレートが止められている.ここでも,ガタがある.やはり丸棒曲面とキャップボルトの固定だからである
- フランジナットは,日本製と思しきものをホームセンターで調達した
- ハンドルの長さは,オリジナルのものは少し短いと感じていたので25mm延長した.弧状スチールプレートの厚みは1.9mmなので,幅15mm,2mm厚のアルミフラットバーを3mm厚のアルミフラットバーでサンドイッチにする構造とした
- nanoテーブルソーにアルミ製クロスカットスレッドをセットして,部材を切り出す
- これら3枚のアルミフラットバーはM3x8mmの皿ネジ固定とした.フラットバーの合計厚みは8mmなのでちょうどいい.ちなみに皿ネジの長さ(呼び長さ)は,皿平面部からネジ部先端までを指す.したがって皿穴加工すればぴったりとなるはずである.Amazonで購入したが,150個入りなのでお得である.3Dプリンターで作製した箱ものに蓋を取りつけるときにもよく使っている.
- 皿穴加工は,手持ちの面取りカッターを使用したが,モノタロウの製品が抜群に良かった.皿穴加工とは銘打っていないので仕方ないか・・・
- そこで穴あけと,皿穴加工を同時にできるドリルカッターを購入したのだが,よくよく考えると穴にはネジを切らないといけないので使えないことに気づいた
- 3枚のアルミフラットバーは,瞬間接着剤で仮着してφ2.5mmのドリルで貫通穴を開け,そこにM3でタップを切るのでドリルカッター付属のφ3mmドリルは使えないのである
- まずはアオニスを塗り,ノギスのジョウでケガキ線を入れる.15mm幅のフラットバーなので,ノギスを7.5mmで固定して慎重に,アルミ自体にキズを入れないようケガく
- あとは,図面通り端から穴あけ位置にケガキ線を入れていく
- できるだけ正確な位置にポンチ穴を開けるため,2本のオートポンチを使う.先端が細く,ケガキのクロス位置に正確に針をおけるペンタイプオートセンターポンチで1回目のポンチ穴を開ける.次いでオートセンターポンチでポンチを打つが,最弱の位置で問題ない
- 画像から正確に打てているのがわかると思う
- さらに,正確に穴あけを行うためにセンタードリルを使用する.穴あけ,皿穴加工は当然nanoボール盤を使用した.この時点でモーター換装は完了しているので,快適に作業を行うことができた.これでハンドルが完成すれば完璧である
- 穴あけ後は,軽く面取りをしておく.いつものモノタロウ製を使用した.その後,3本を固定するためのM3皿ネジ用のタップを切っているが,タップが進んでいくと瞬間接着剤を使用していても,はがすような力が加わるためバイスプライヤーでしっかり固定しておく必要がある.その際,傷つけない養生が必須である
- タップも正確に,垂直に立てなければならない.当然電動タップスタンドを使い垂直を出してタップ先端を食い込ませる.その後タップハンドルを使用してタップを切った
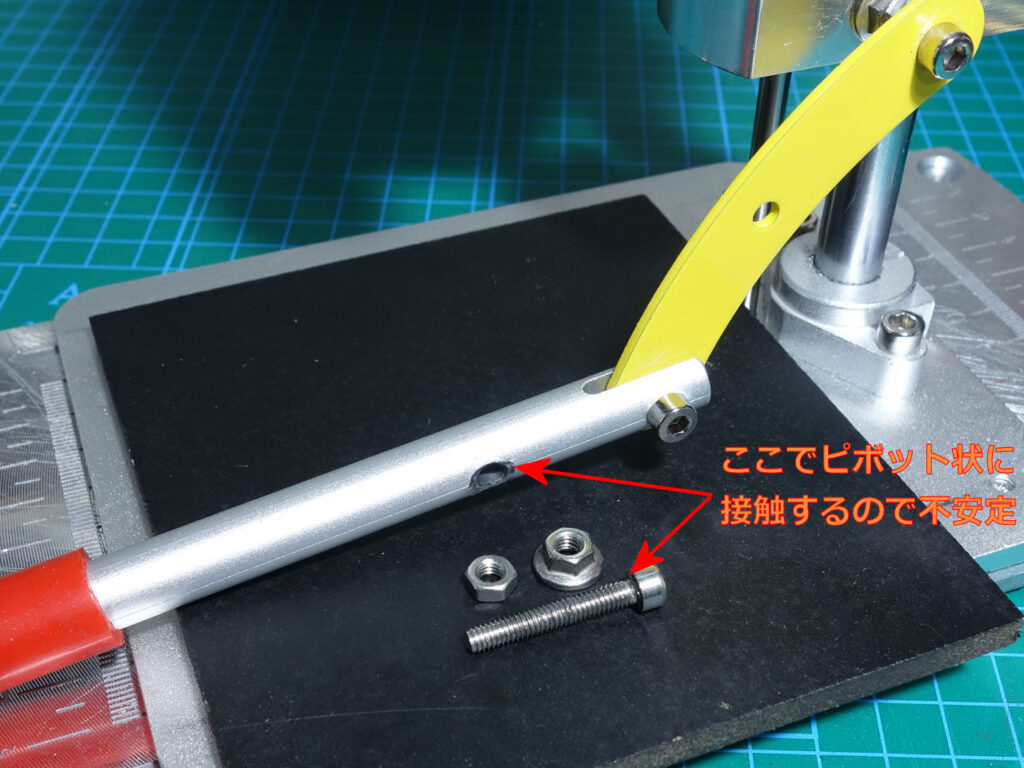
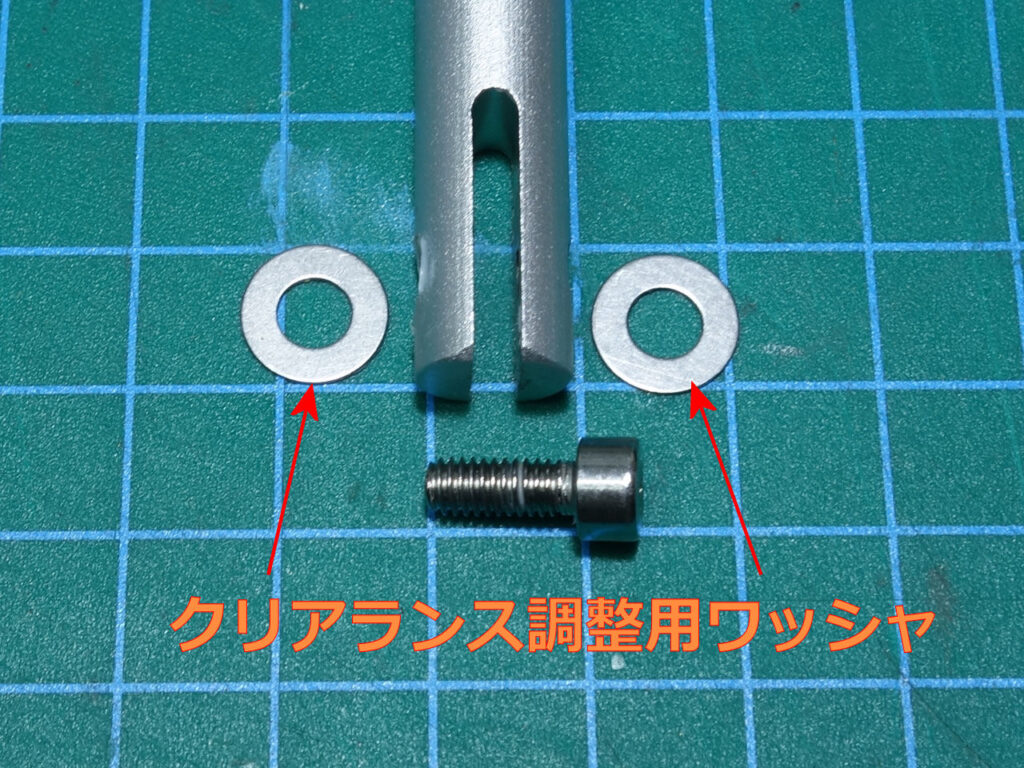
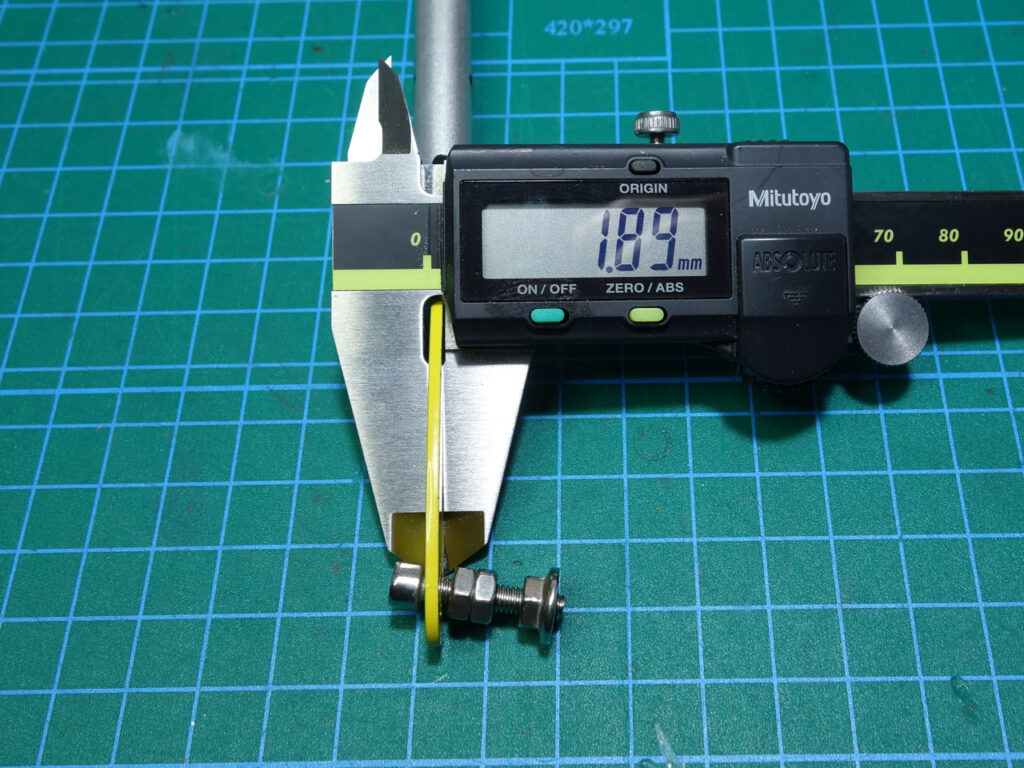
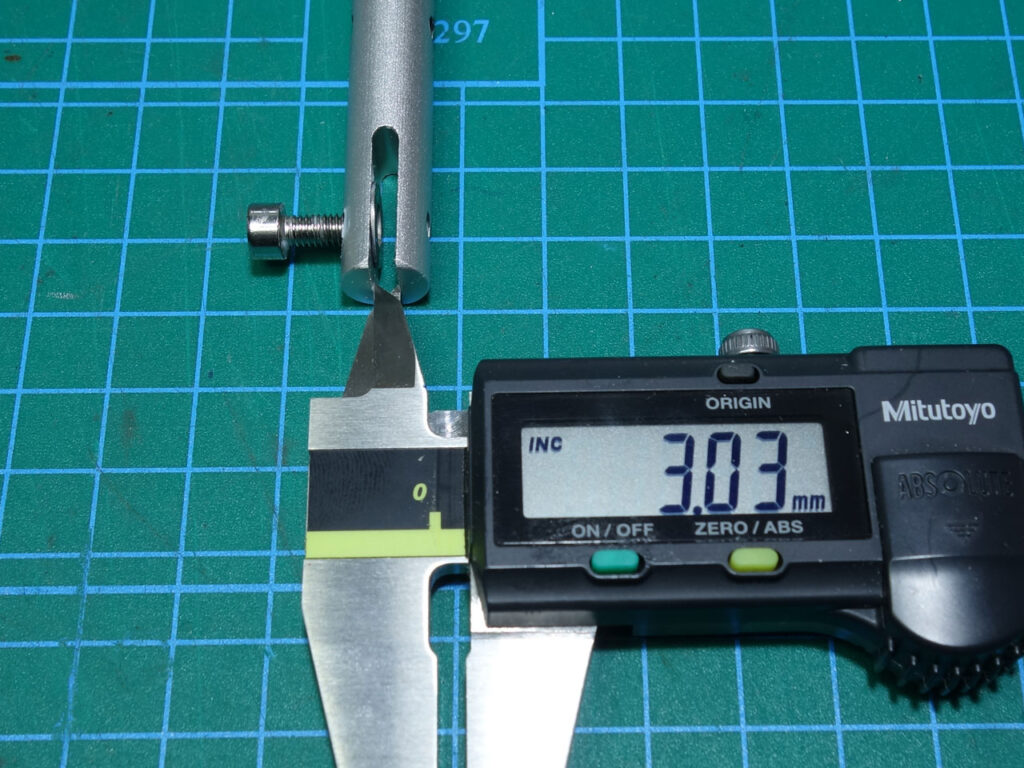
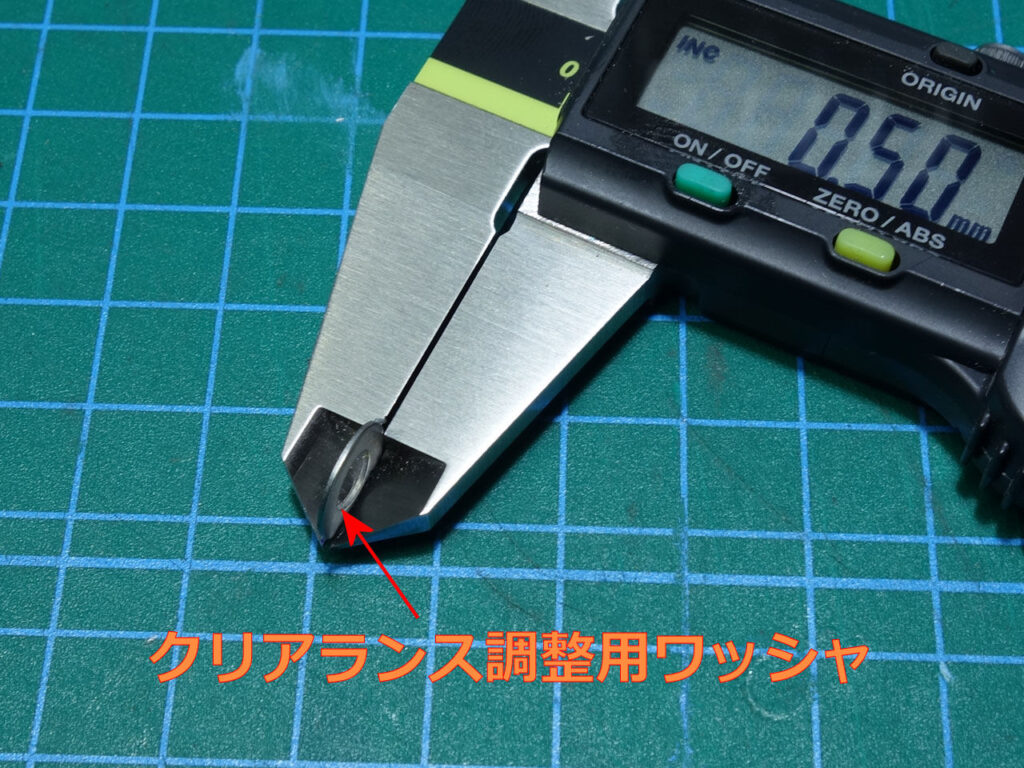
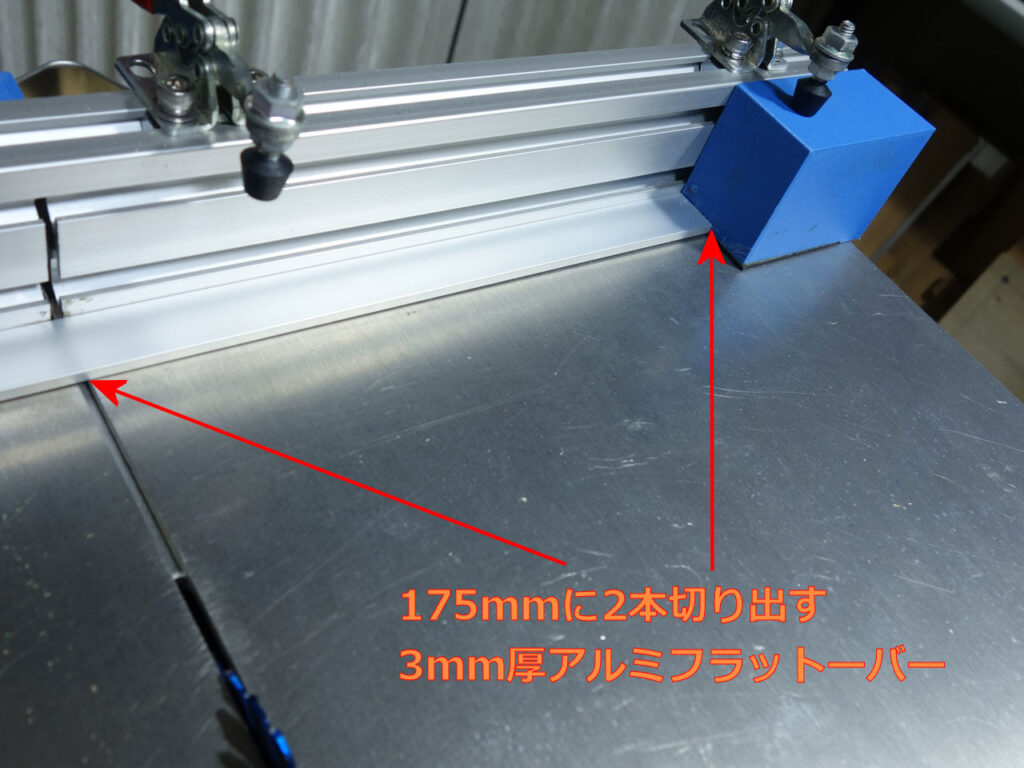
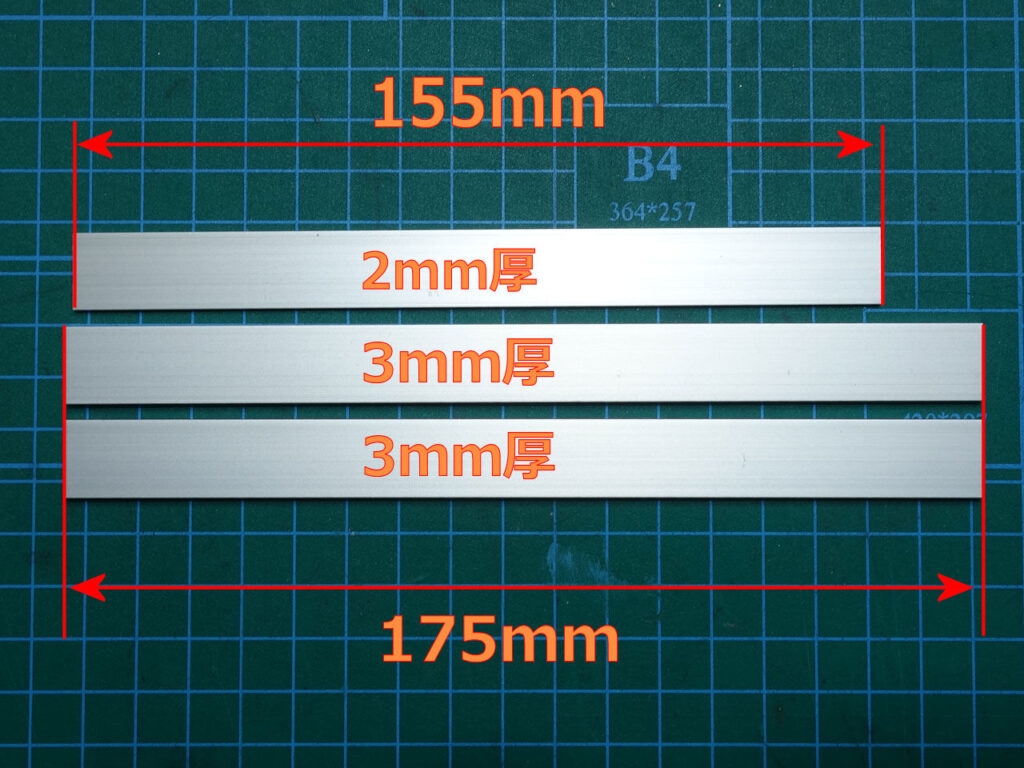
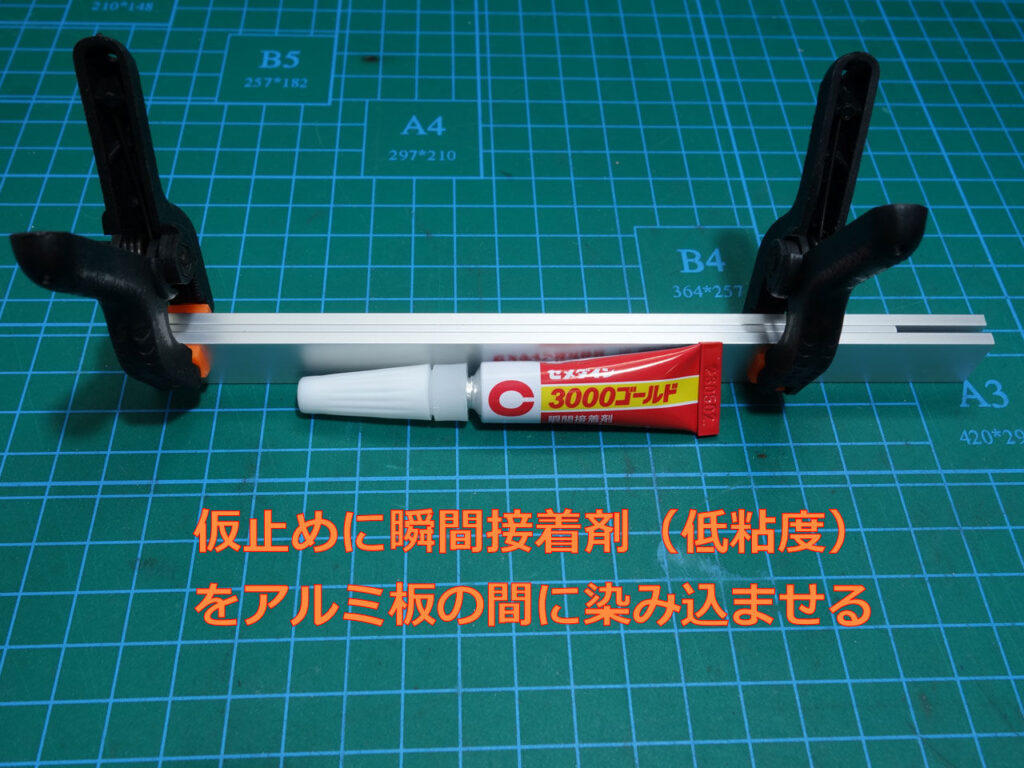
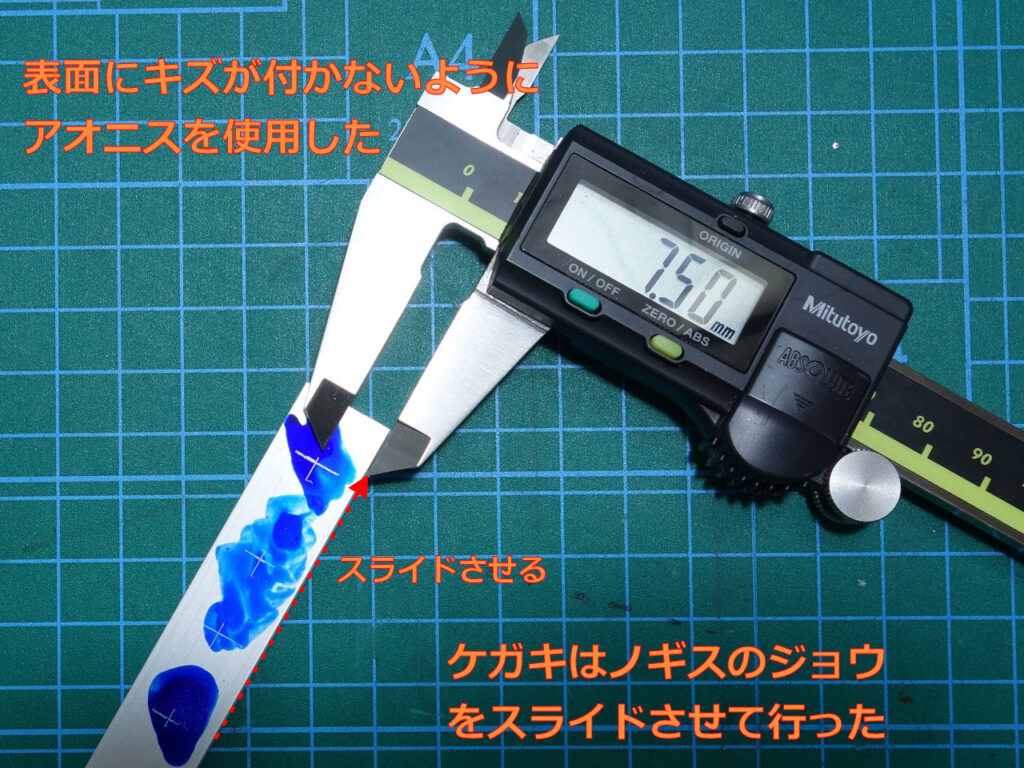
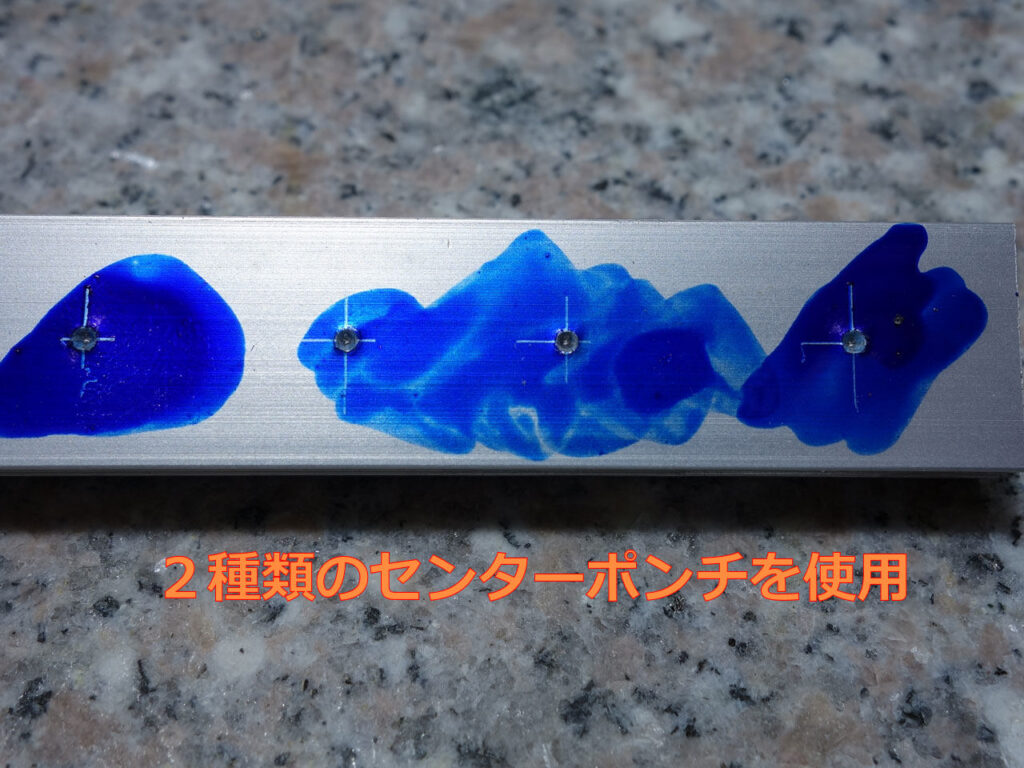
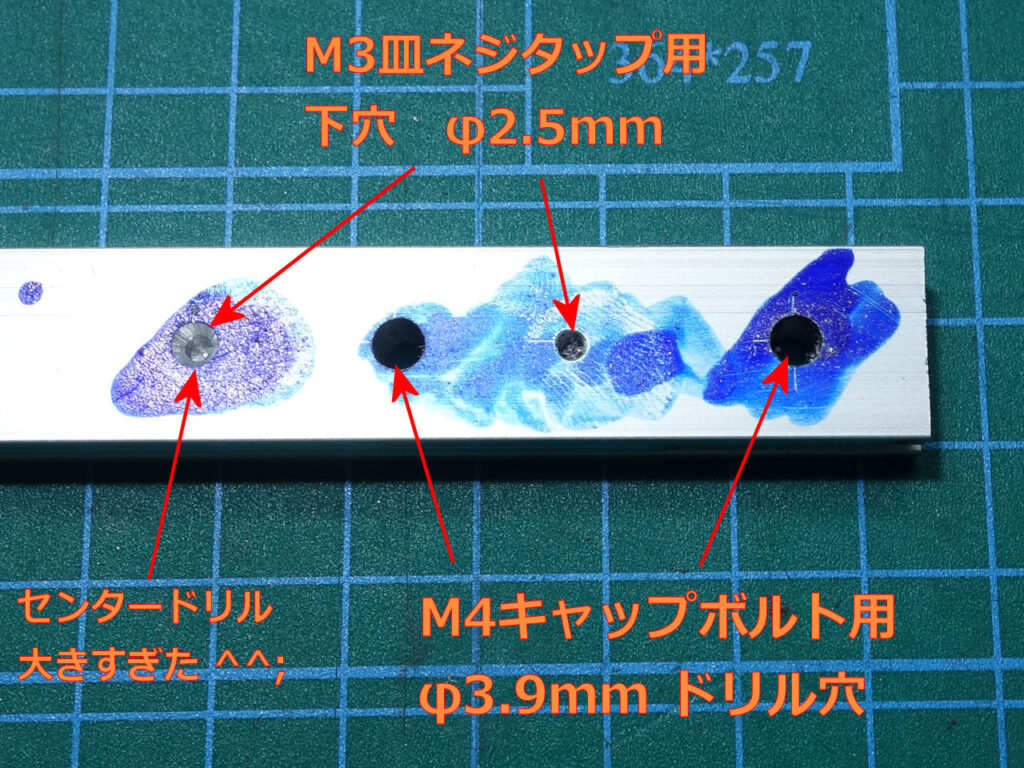
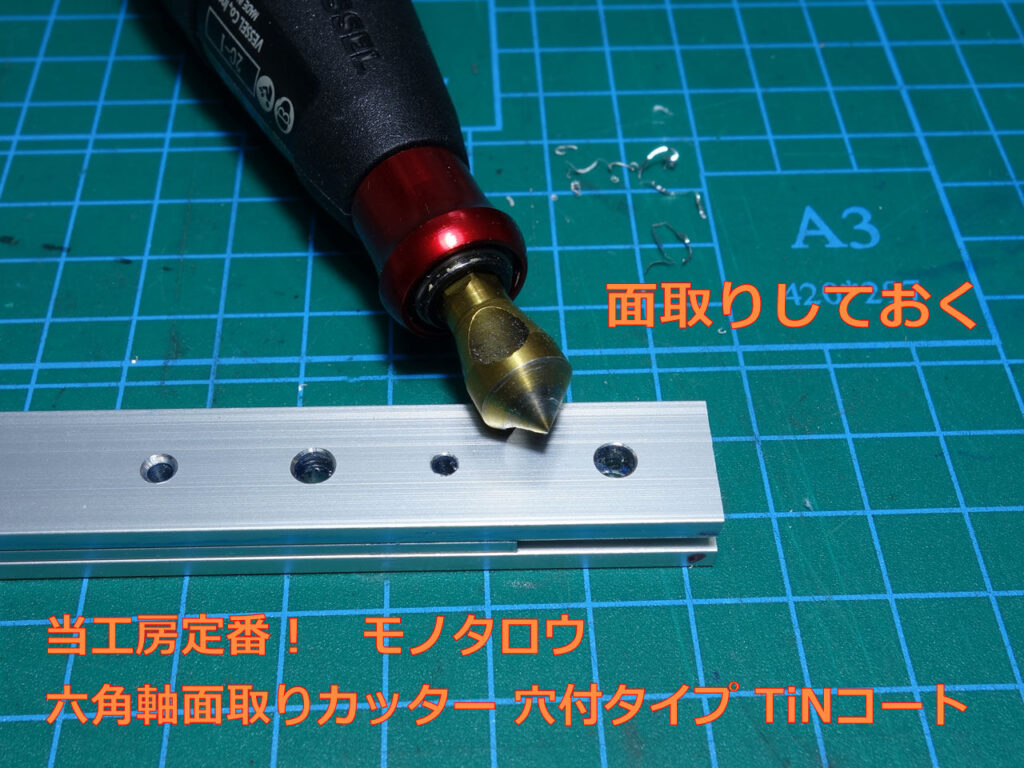
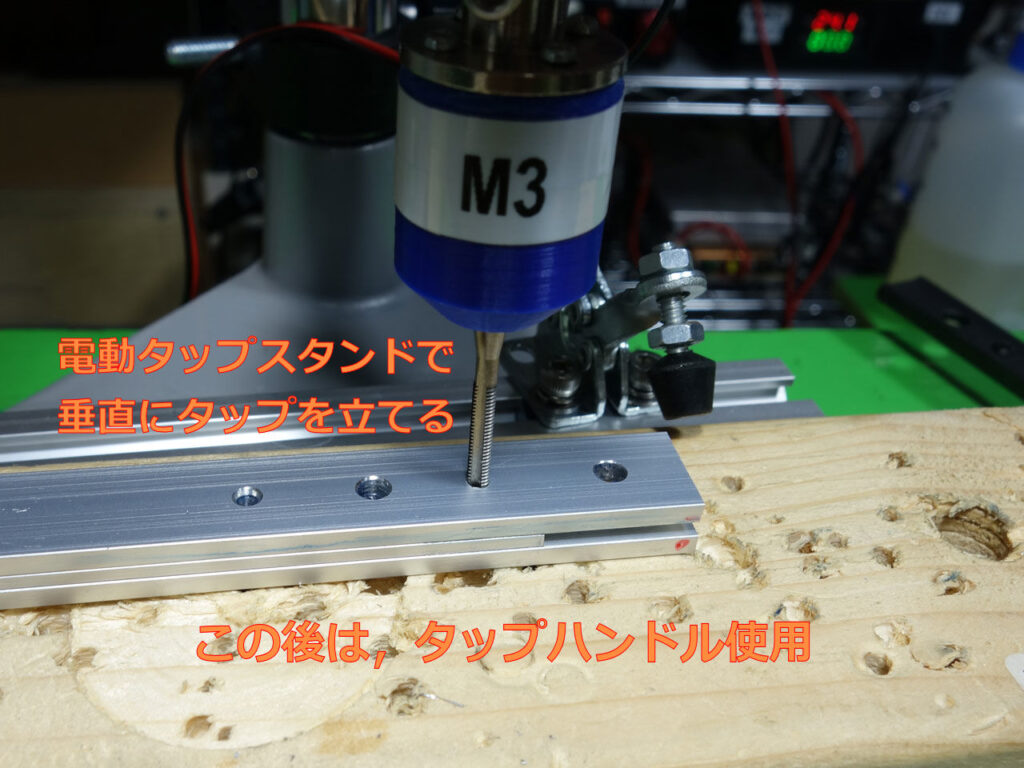
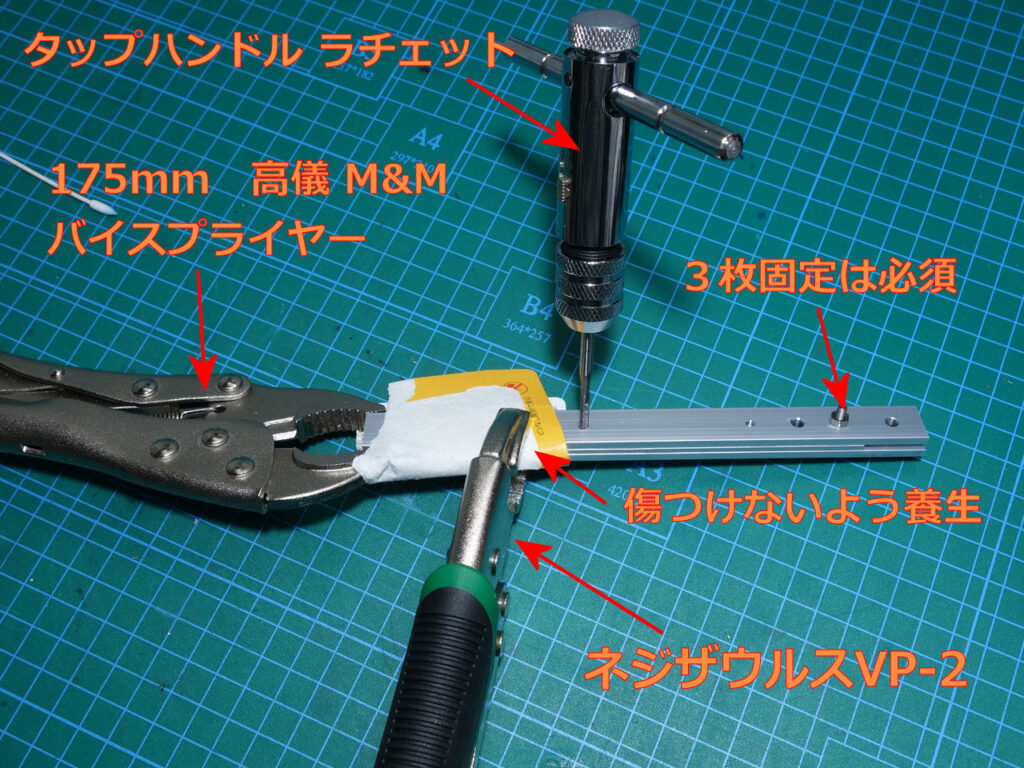
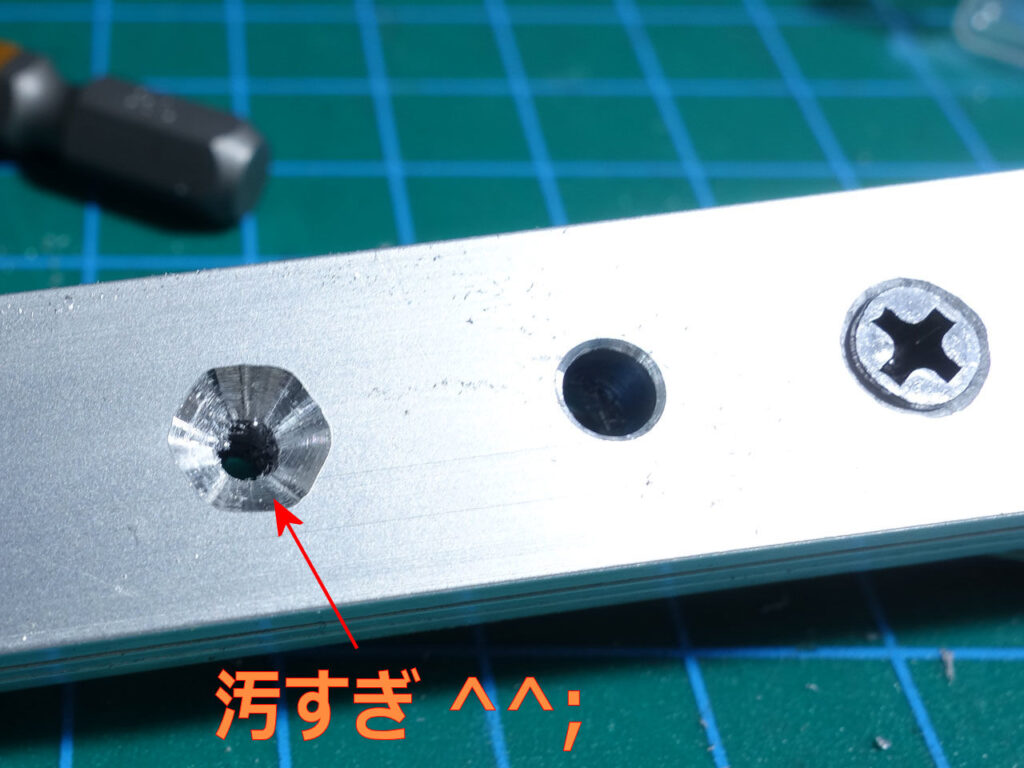
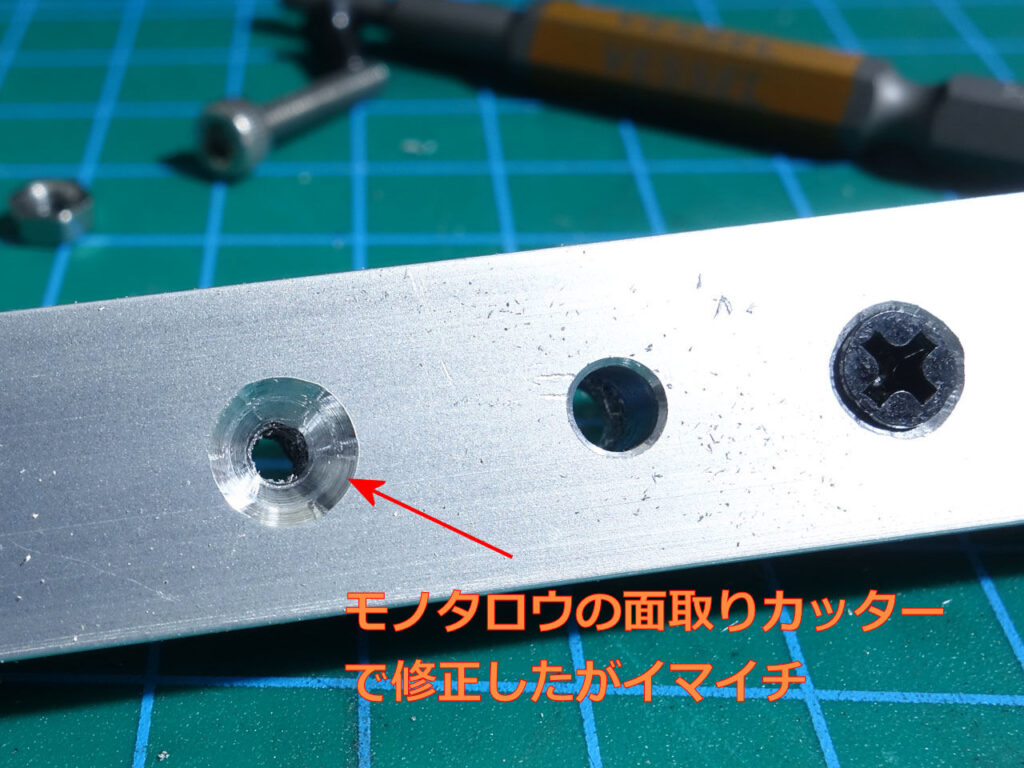
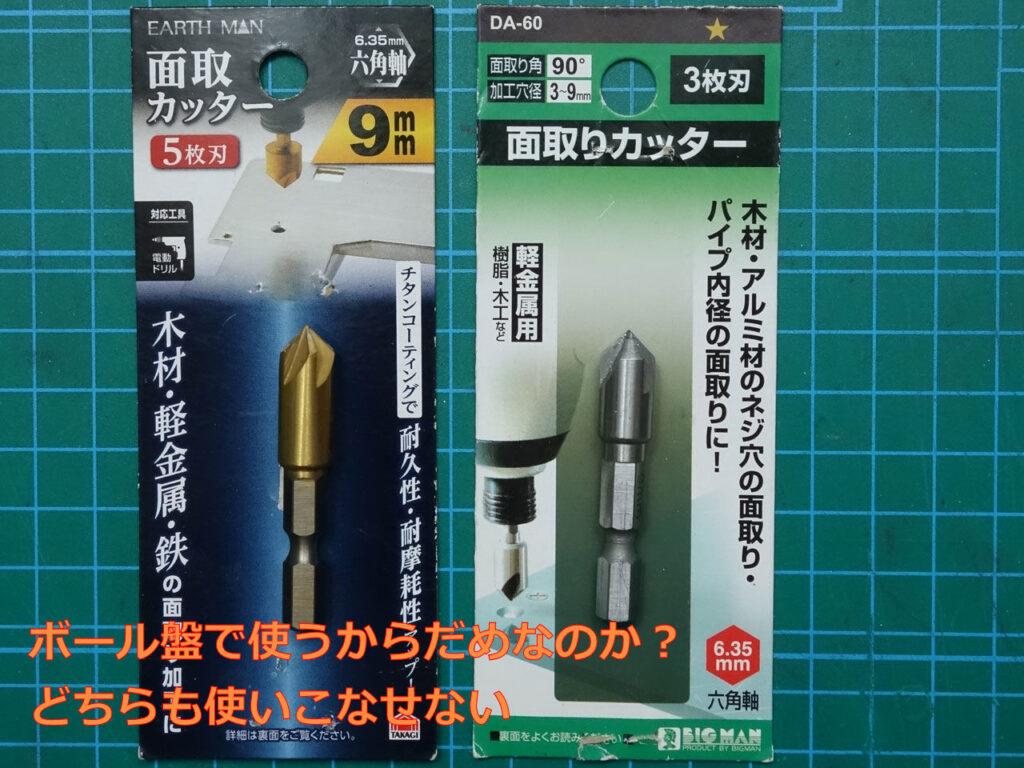
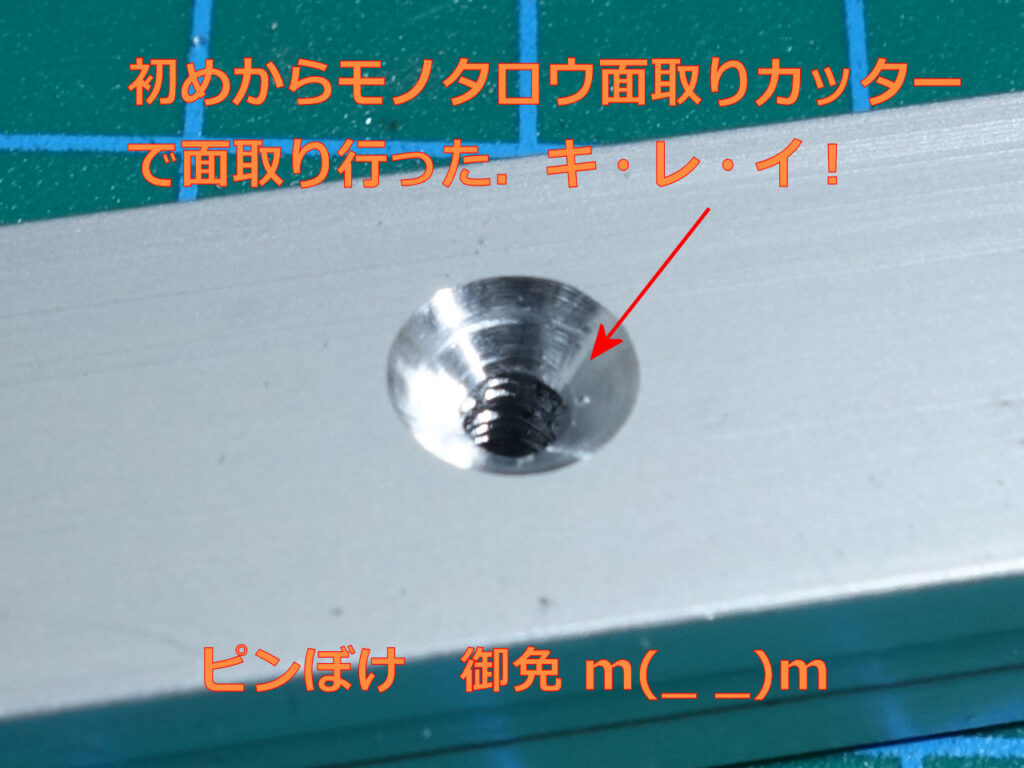
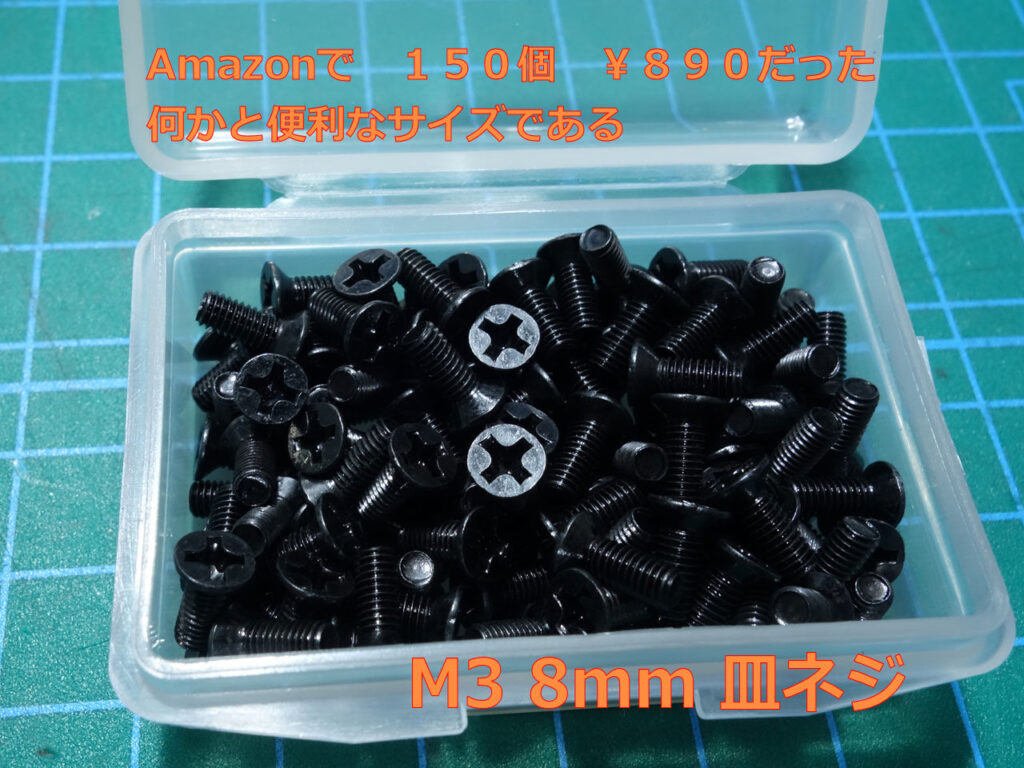
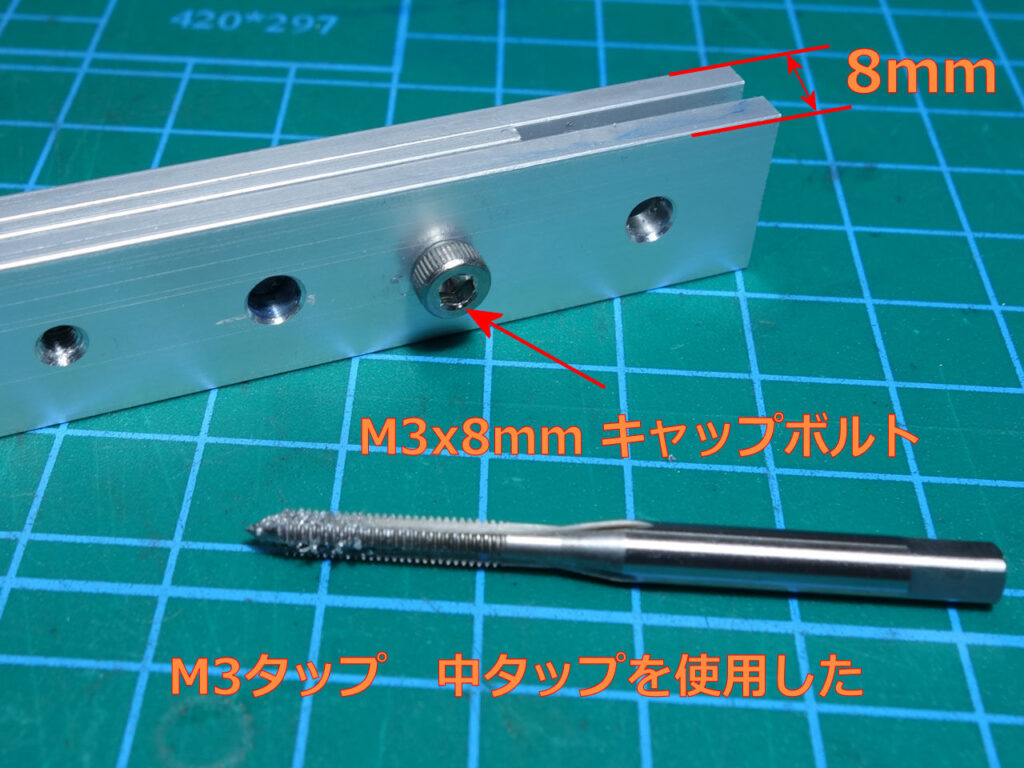
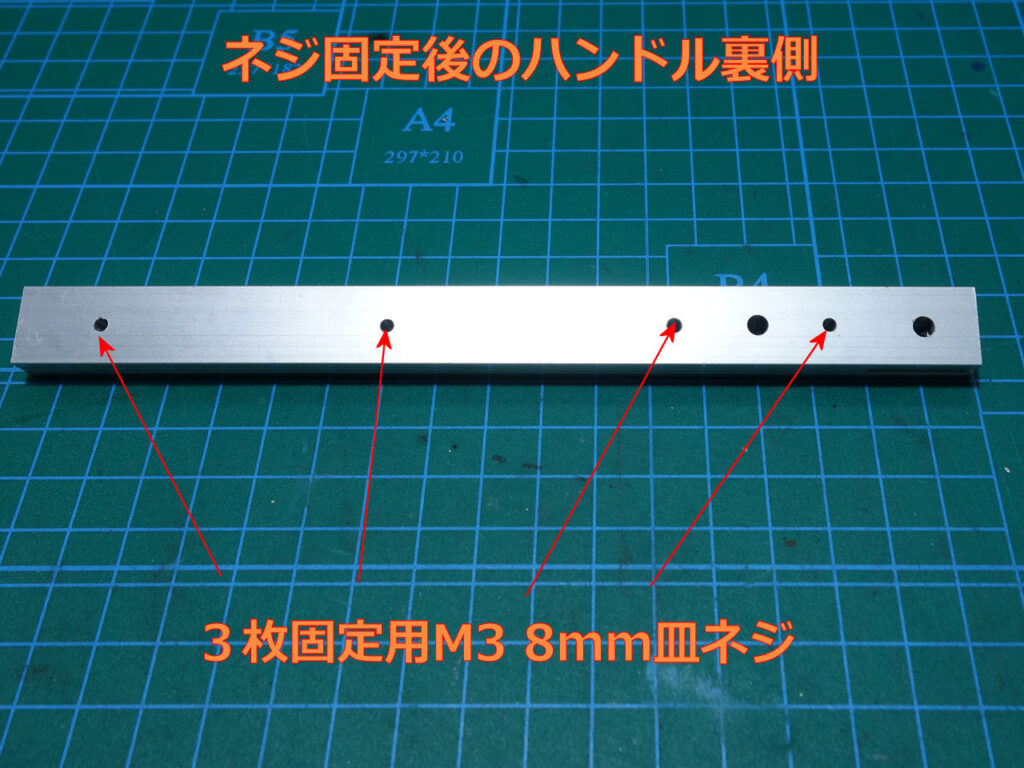
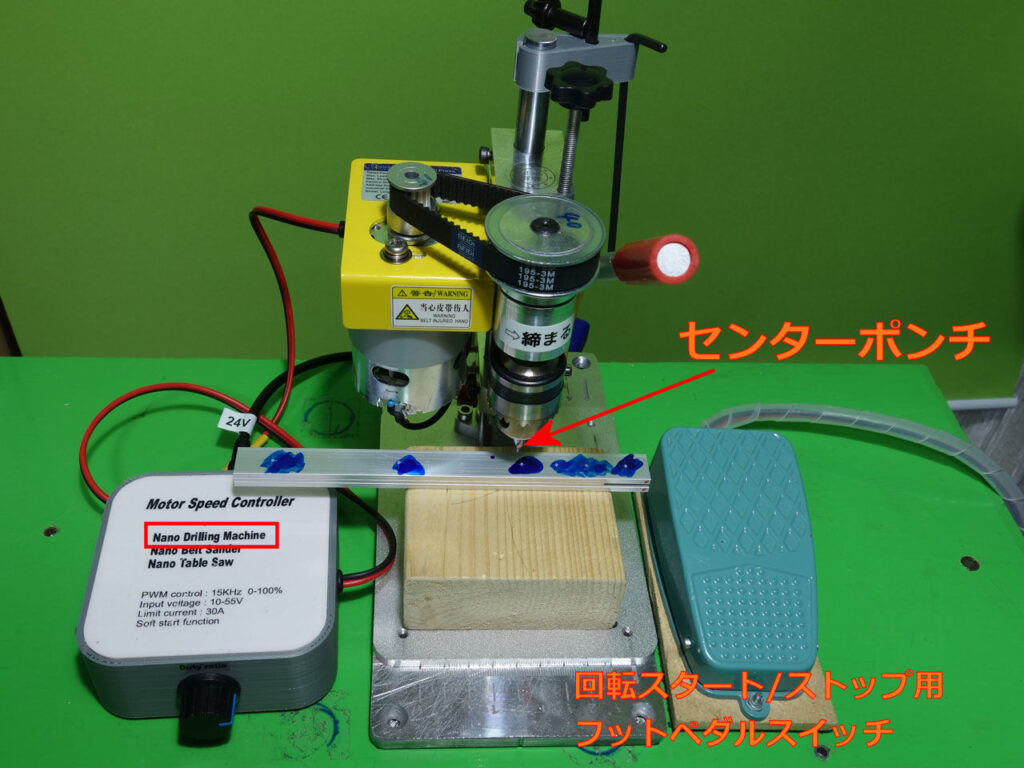
- ねじ止めが終わったハンドルを本体上部に取り付けていく.取り付けはM4キャップボルトとフランジナットを使用するために,ハンドルには取付用の穴を開けておく.M4キャップボルトのネジ部直径は3.8mmちょっとある.そのためφ3.9mmの穴を開けるのだが,非常に中途半端なサイズではあるが,M4前後のドリルサイズは0.1mm刻みで販売されている
- テストで事前にアルミフラットバー端材に,φ3.9mm穴を開けてM4キャップボルトを通してみた.ガタもなく適当なクリアランスがあり問題ないことを確認した
- 本体取付用キャップボルトは,ホームセンターで購入した日本製と思しき,M4 25mm キャップボルトである.それをフランジナットに通してから本体上部取付メネジに締めこんでいく.ちなみにフランジナット日本製.デフォルトのものより頭部のネジが対角8mmと大きい
- フランジナットはドリル本体上部に締め付け・固定し,ステンレスナットを2つ使用して弧状スチールプレートを取り付ける.この2つのナットはダブルナットでゆるみ止めにする役目と,スチールプレートと本題の間に間隔を確保する役目がある.こうしないと,プレートが本体側の主軸タイミングプーリーにあたってしまう
- さらにがたつき防止のために,ワッシャをプレートの両側に取り付けた.この状態で2つのナットでハンドルがガタなくスムーズに動くよう調整する.この時プレートとフランジナットとの間隔が狭いので,締めつけには苦労したのだが,SK11のスパナセットを購入して少しは楽になった.スパナの厚みがあと1mm薄かったら,完璧であったのだが
- 次は,ハンドル下端をドリル本体下部に取り付ける.ここは,ハンドル両端の3mm厚アルミフラットバーでサンドイッチにした状態で,M4キャップボルト,フランジナットで取り付ける.隙間は0.1mmなのだがちょうどよかった
- ねじ止め各所にはネジロック材をつけておいた
- 4方向から見た外観画像を載せておく
- 仕上げとして,ハンドルにTPUで印刷したグリップを取りつけて,ハンドルの完成とした
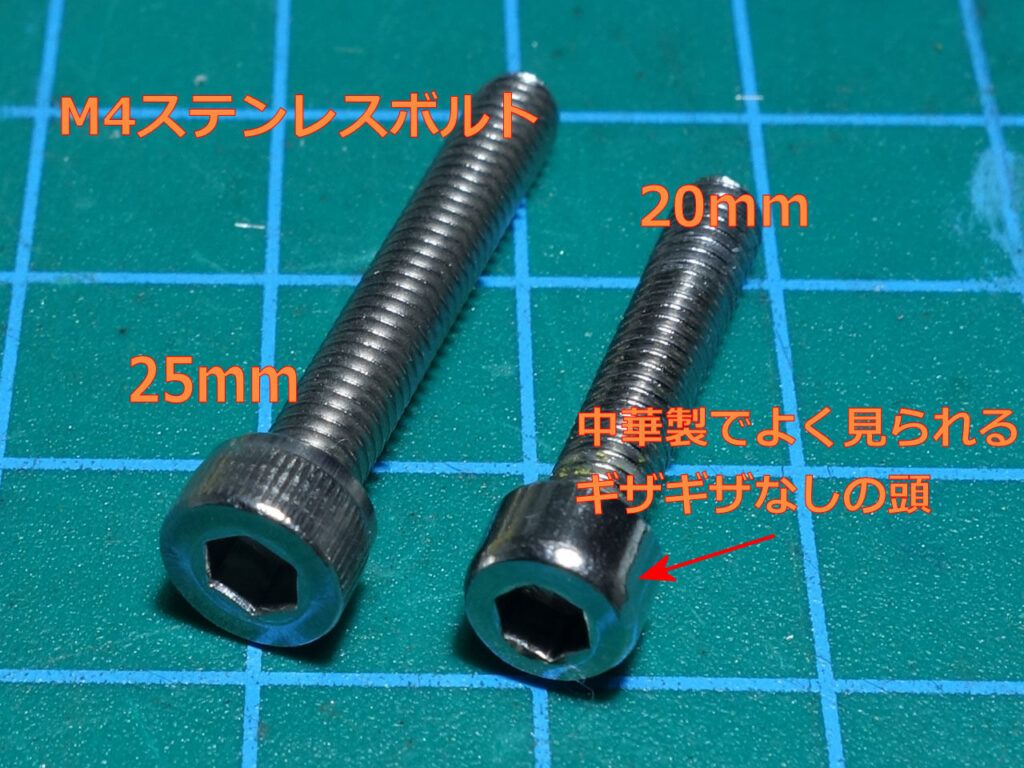
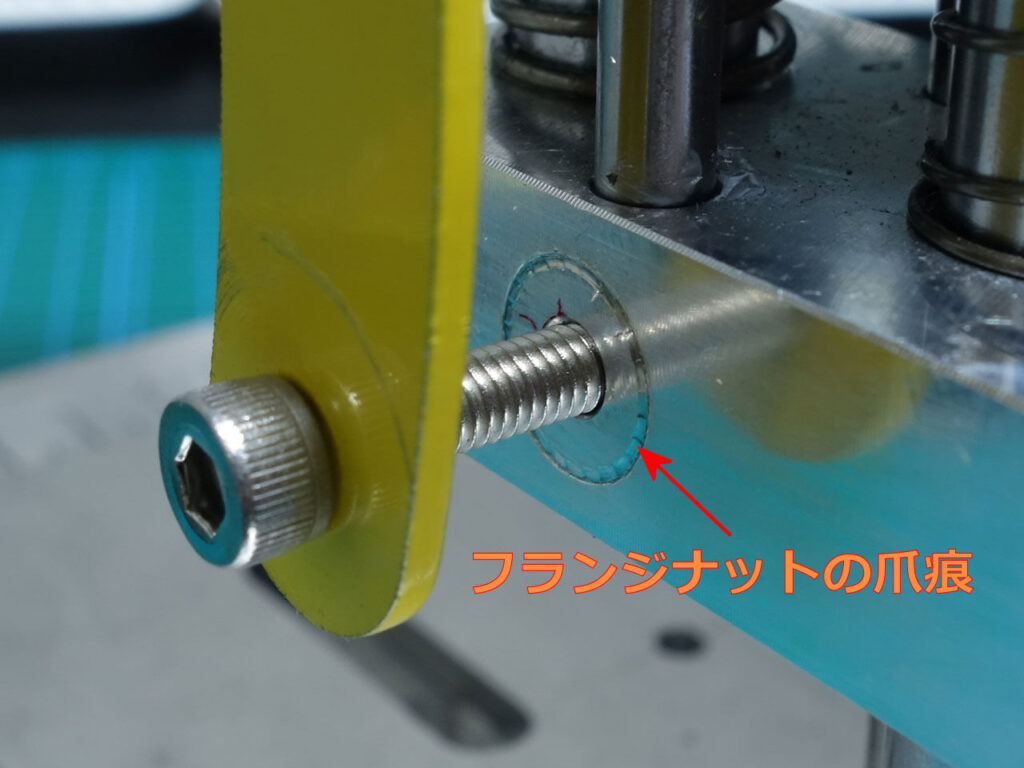
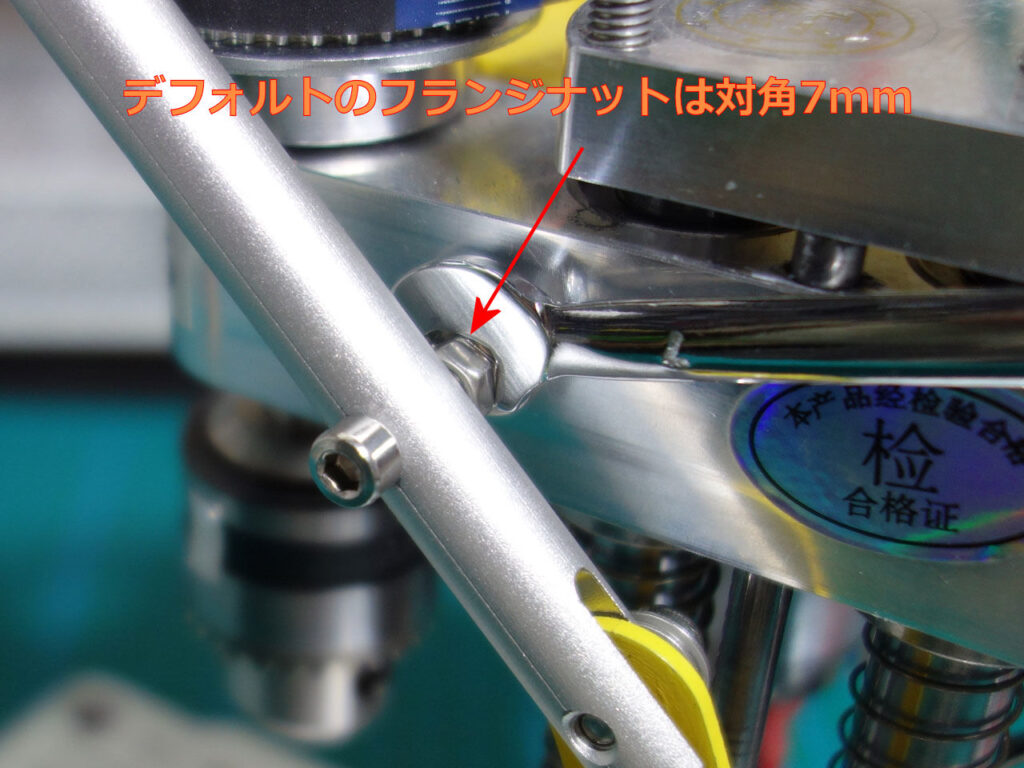
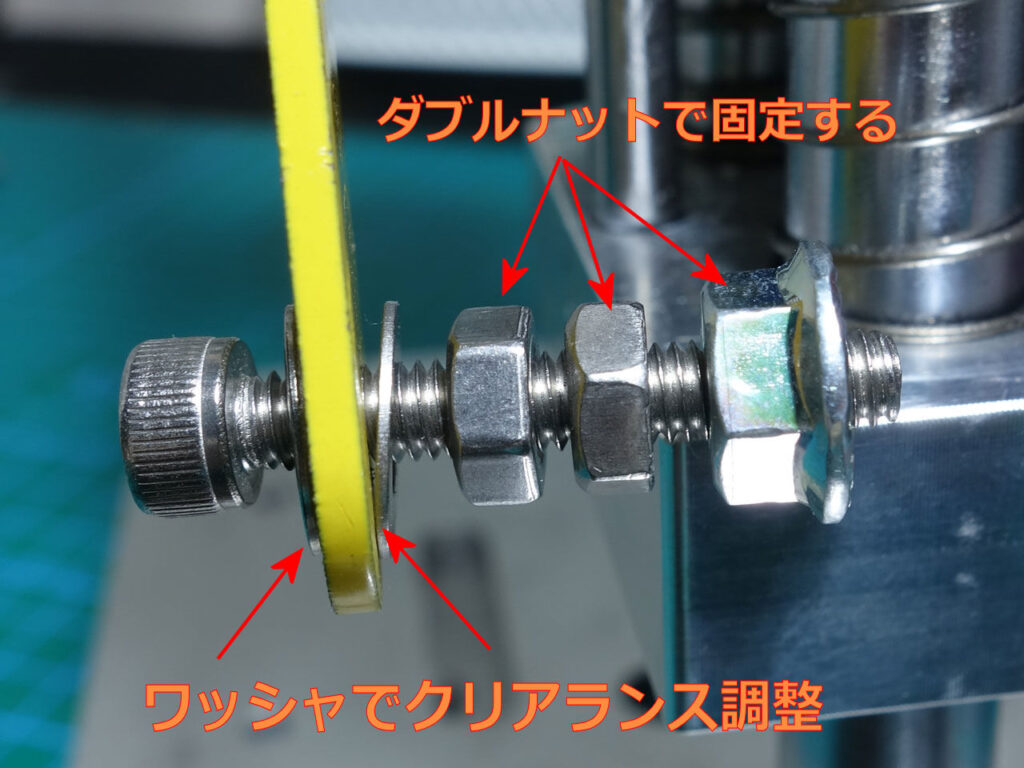
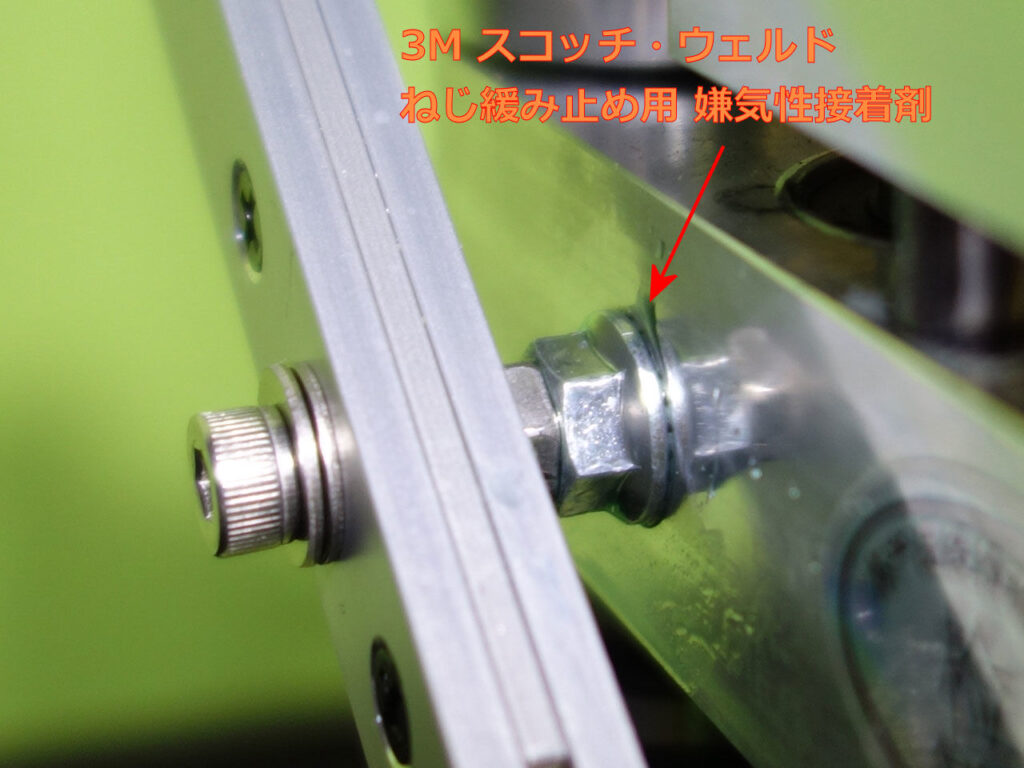
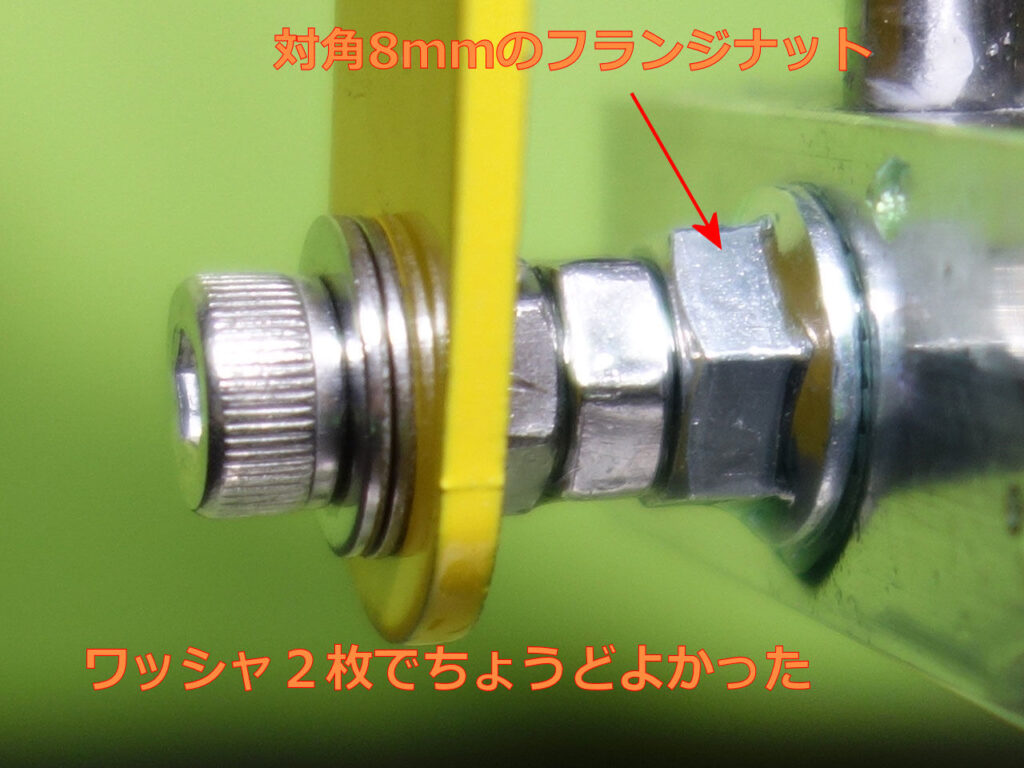
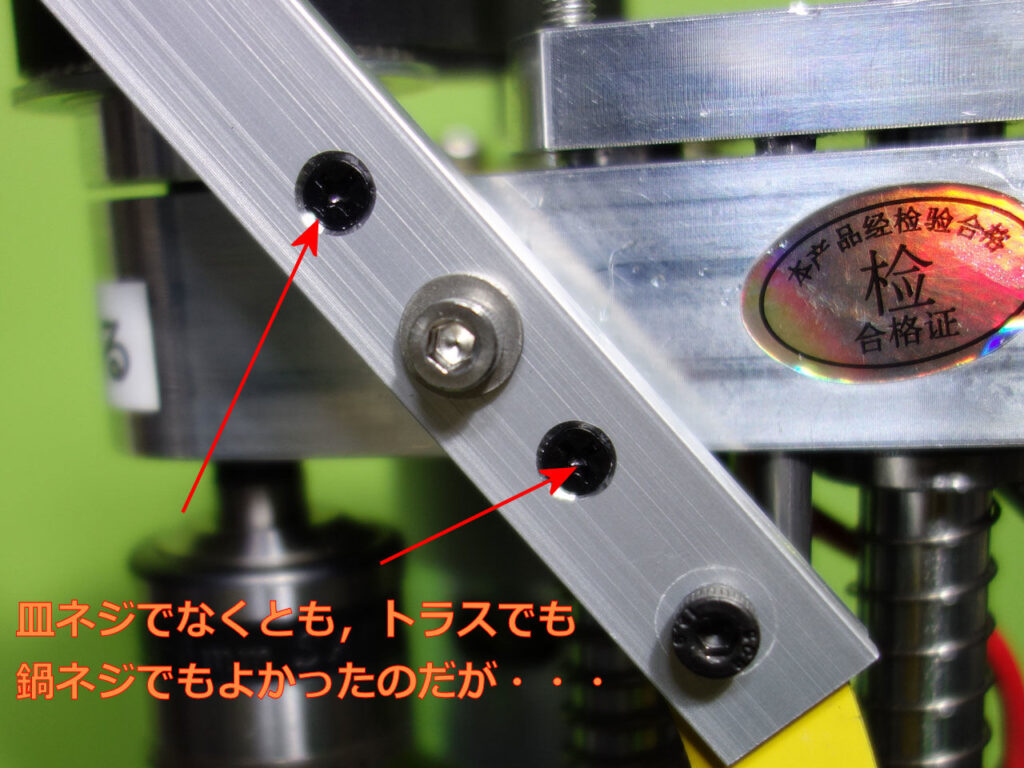
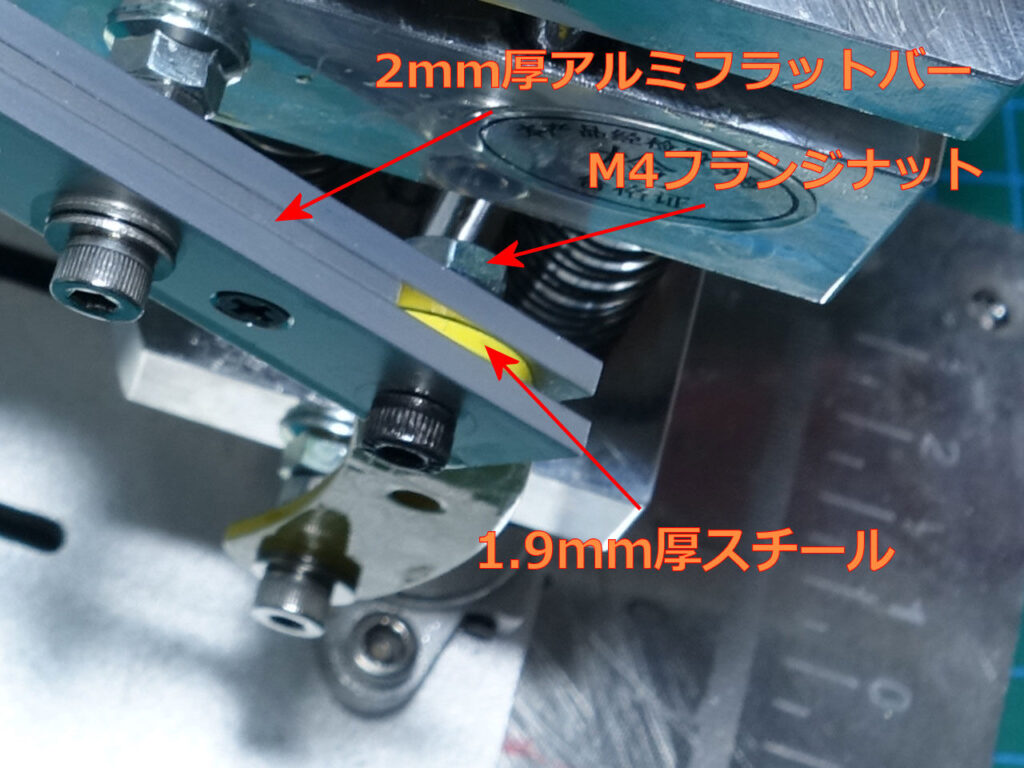

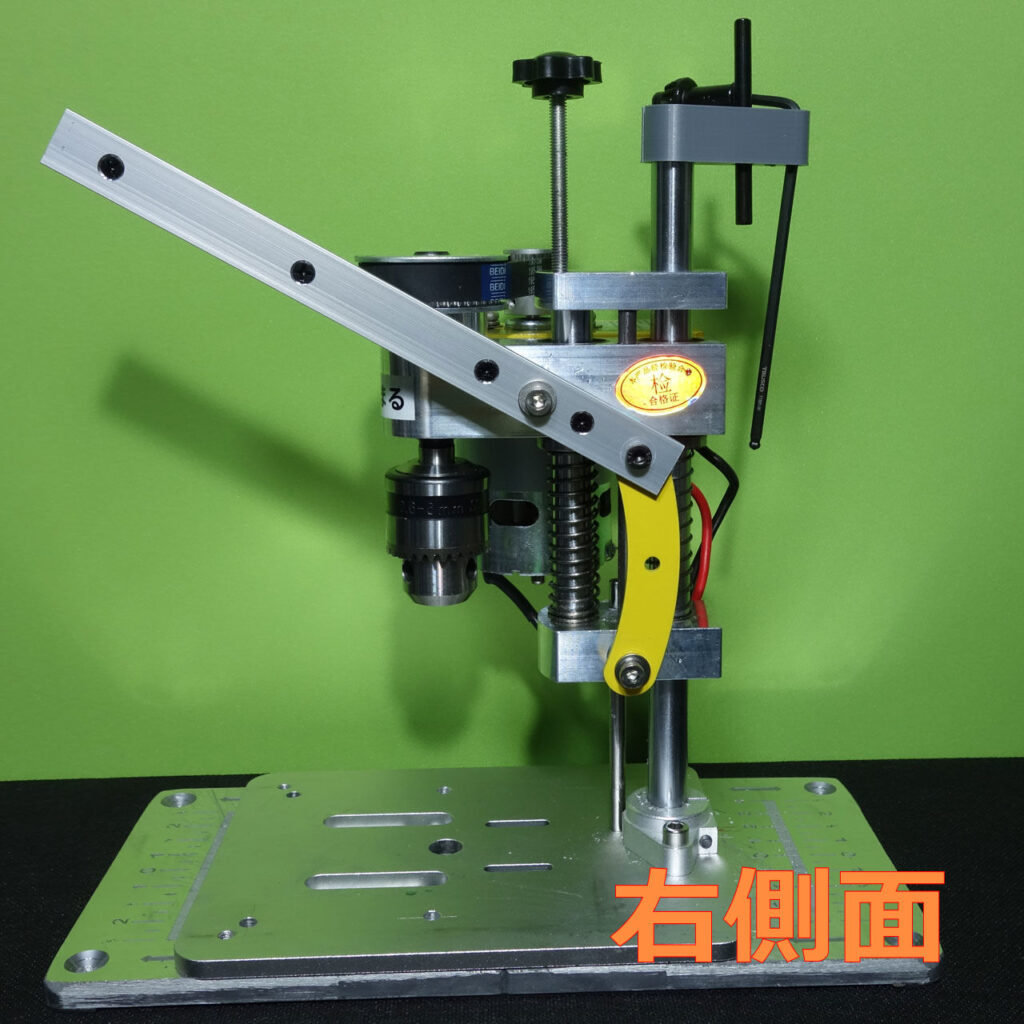
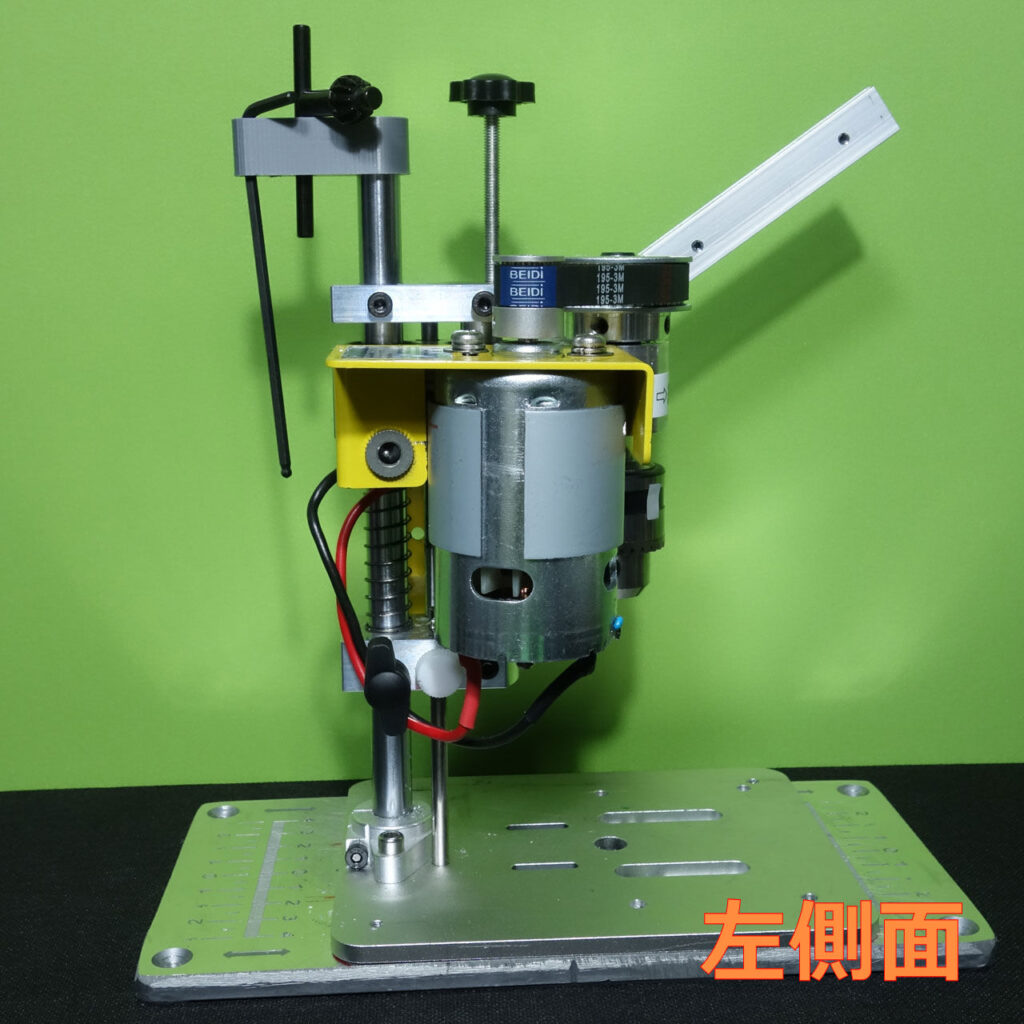
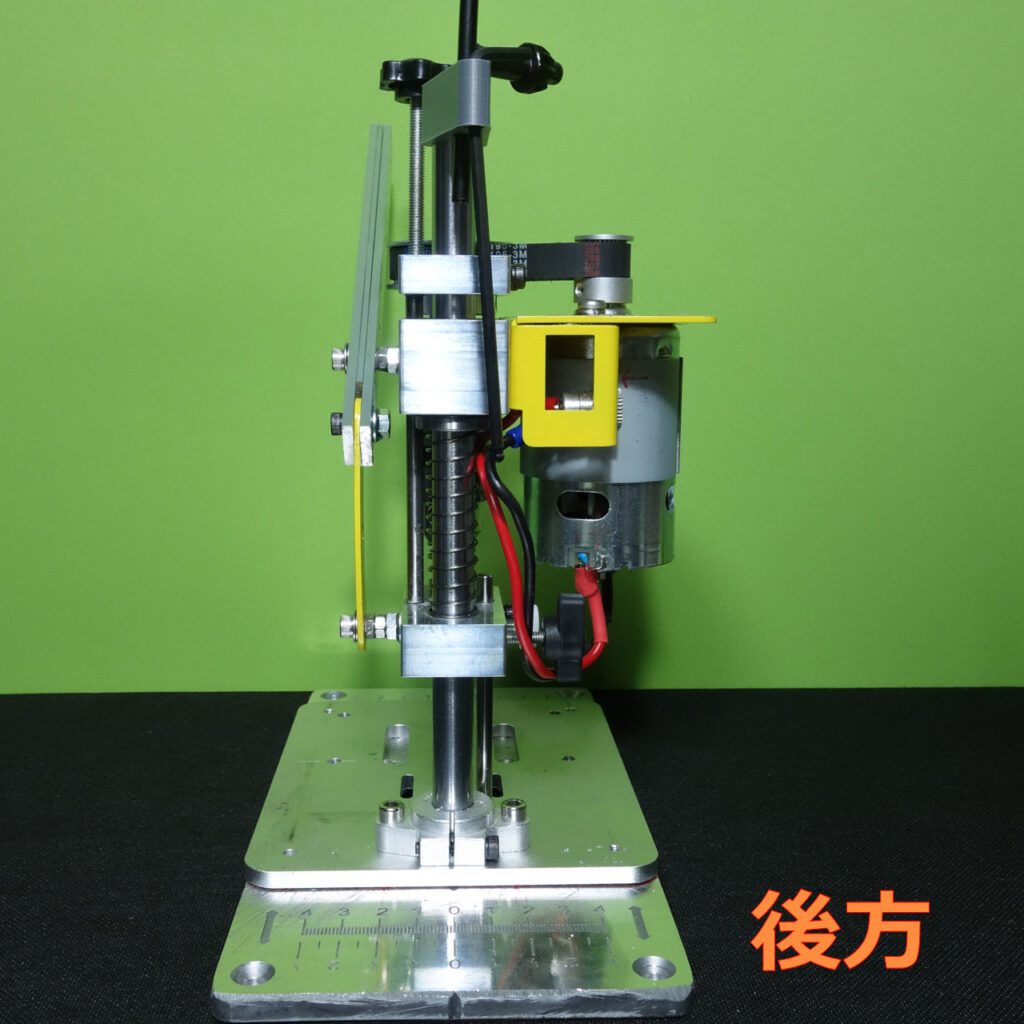
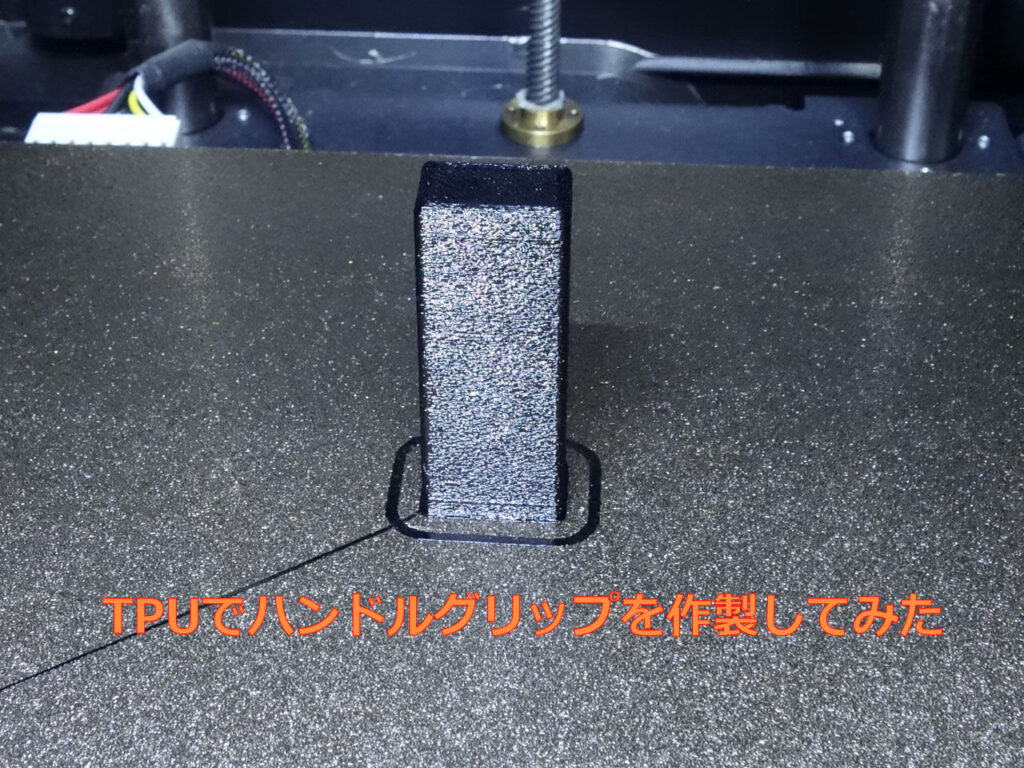
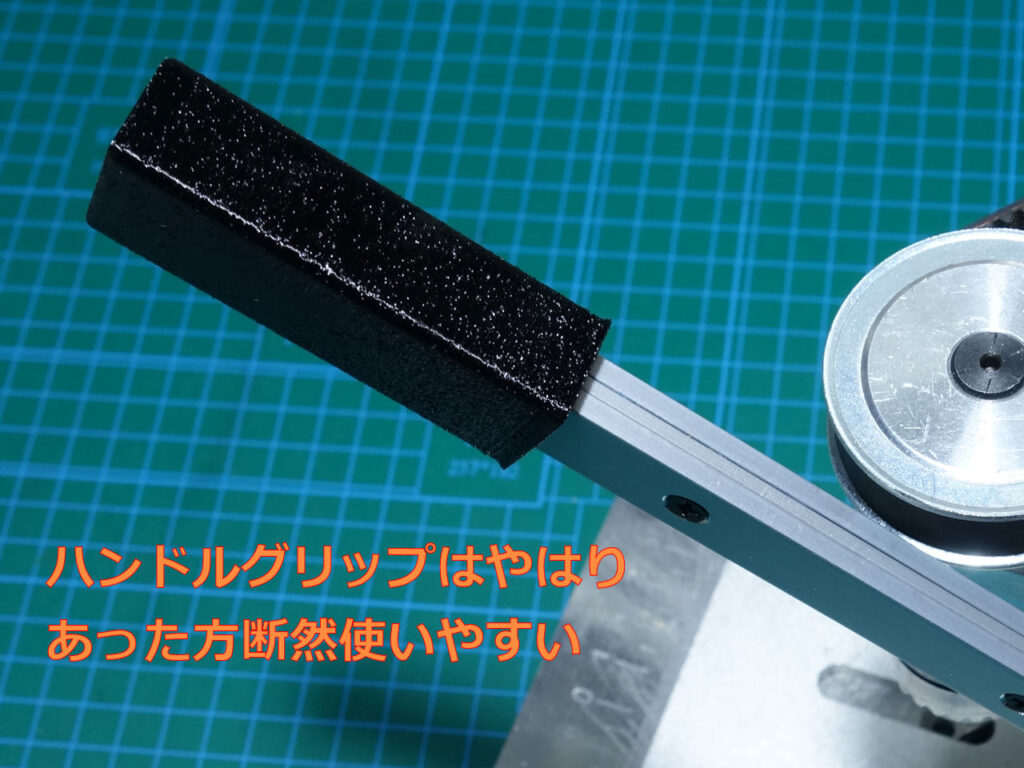
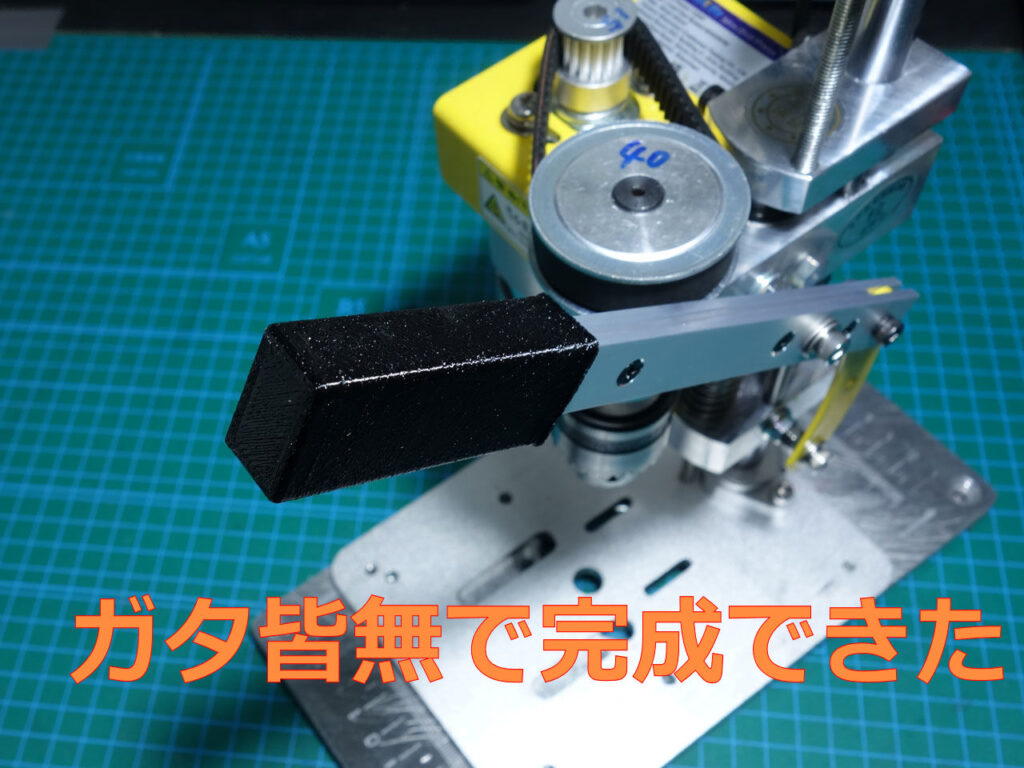
- モーター換装にあたり,最初に考えたのは主軸回転数をどうするかである.それにはデフォルト状態での無負荷回転数を計測しておくことが必要である
- 記事冒頭で説明した通り,回転数は3259 r.p.m であったので,改造後回転数もそれに近い値を想定した
- Aliexpressで24V 895 モーターを探してみた.この手のモーターは,Amazonより圧倒的にAliexpressの掲載が多い.そこで見つけたのが,24V 10000r.p.m 895 モーターである
- 895モーター10000 r.p.mの回転数は,795(推定6000 r.p.m)と比べて負荷は大きくなっているはず.さすがに895とはいえ過負荷となるのではと考えた.負荷の低減策としてギヤ比を小さくすることを考えた
- それには,モータープーリーの歯数を減らか主軸プーリーの歯数を増やすことになる
- そこで,主軸のプーリーの歯数を増やして40歯のものを選定した.ギヤ比が上がるのでトルクも増加する.これが正解かどうかは全く不明である.
- 45歯のプーリーも見つけたのだが,45歯では径が大きくボール盤のハンドルに干渉するため断念した
- また,モータープーリーも目的の回転数近傍となるように2種類準備する
モータープーリーを12歯,主軸プーリーを40歯で計算すると・・・
→10000 x (12/40)=3000 r.p.m
モータープーリーを15歯,主軸プーリーを40歯で計算すると・・・
→10000 x (15/40)=3750 r.p.m - 上記の組み合わせがあったが,3750 r.p.m が望ましいと考え,モータープーリーを15歯を選択した
- モーターのパワーを上げたため,タイミングベルトの強化も図った.HTD 3M規格ベルトでプーリー幅は10mm とした.デフォルトもHTD 3M規格であったが,感覚でちょっと頼りない気がしたため
- 軸間距離を55mm(実測値)として,ベルト長は192mm,195mm を購入したが,取付穴の位置から195mmを使用した
- ベルト長の計算は,こちらのサイトを参考にさせていただいた.感謝m(_ _)m
- 歯数は40歯に決めた主軸プーリーであるが,主軸直径は10mmであるので Bore 10mmを選択する
- 購入した15歯モータープーリーは,モーターシャフト径がφ5mmなので Bore 5mmを選択する
- 購入した195mmタイミングベルトは,幅10mm を選択する
- モーターを黄色のフレームに取る付ける際,モータにはM4とM5mのネジ穴が開いている.どう考えてもこのモーターは享禄だから,M5と使えと製作側は言っている気がする.M5 10mmのキャップボルトを使いたかったのだが,近所のホームセンターにはおいていなかった.まあ,締め付けすぎはよくないと考え,購入できたプラスビスとした
- 前記の通り穴あけ加工した黄色のフレームに,M5 10mm のプラスビスで固定.ゆるみ止めはワッシャ&スプリングワッシャとねじ緩み止め用 嫌気性接着剤を併用して,万全を期した
- 主軸にはストッパー?がついていて,ベアリングの内輪と接して止まるような構造になっている
- 主軸を本体ベアリングに下から通して,上からプーリーを挿入する.ベアリング内輪は少し突出しているのでそのまま上下のガタがなくなる位置で,プーリーをイモネジ2本で固定する
- 本体への黄色のフレームの取り付けは,上記のとおりである
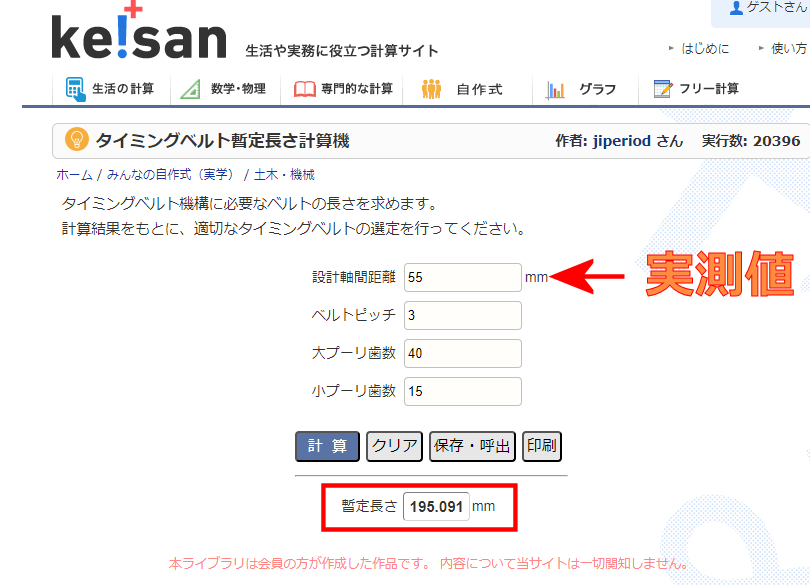
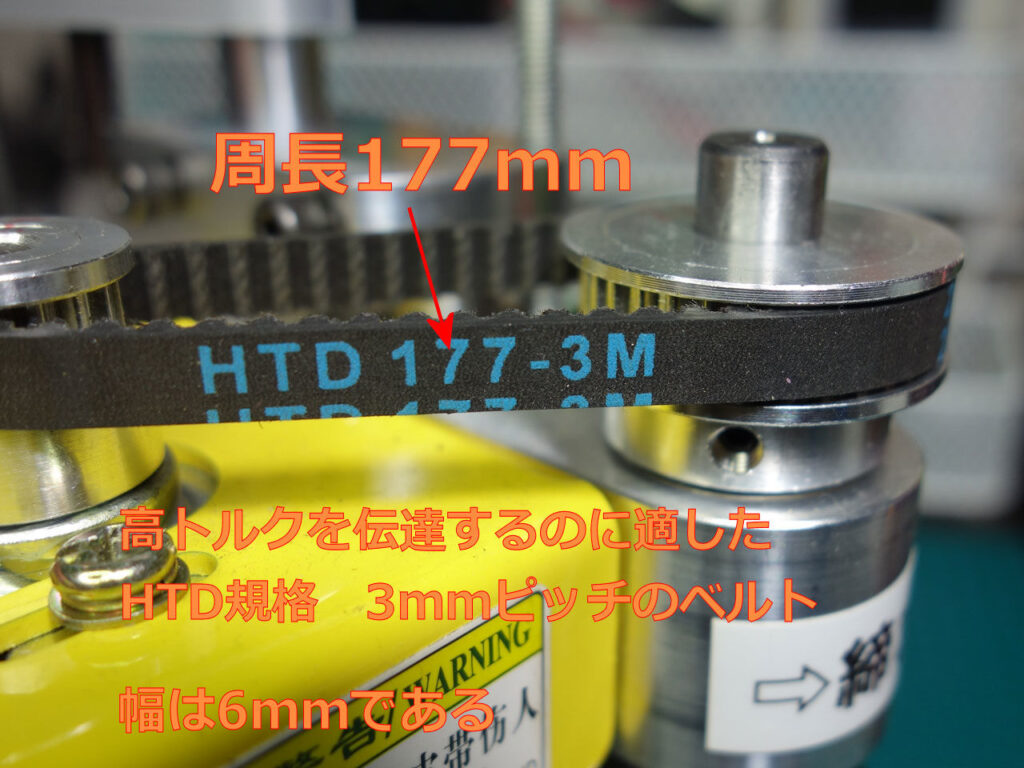
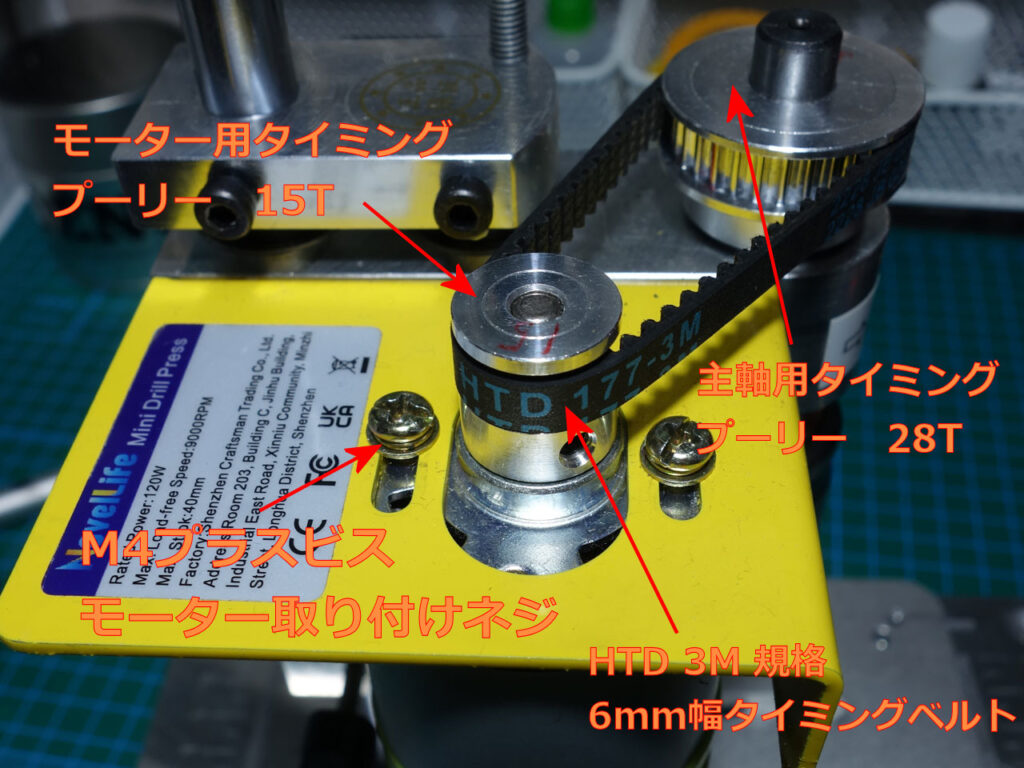
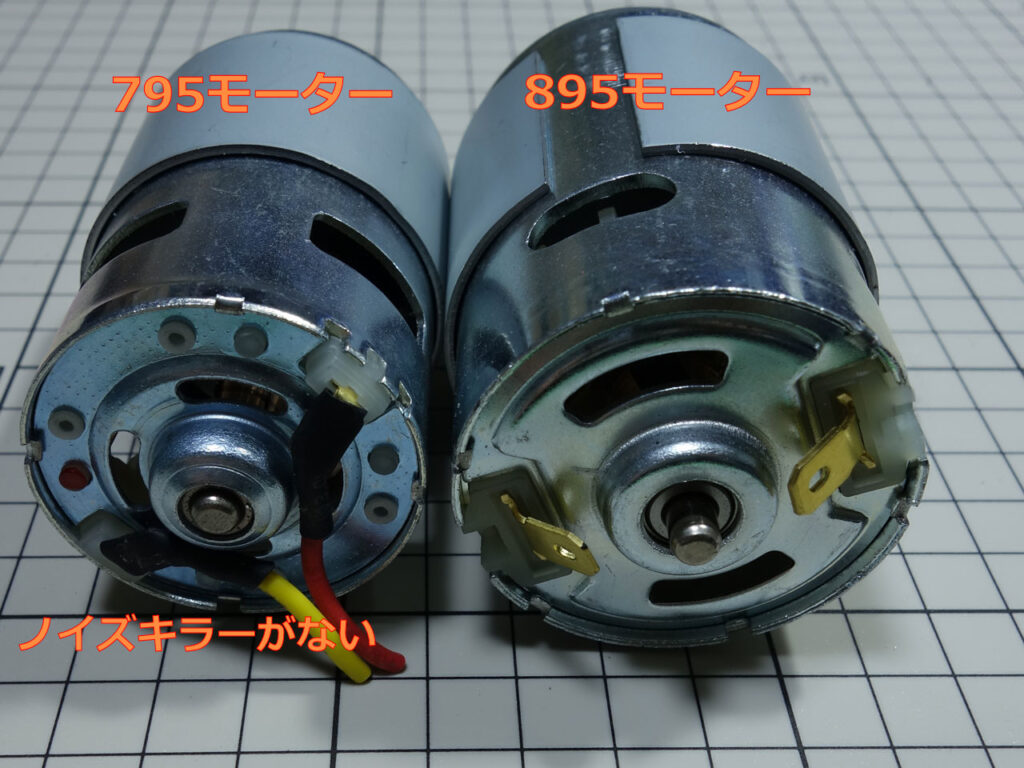
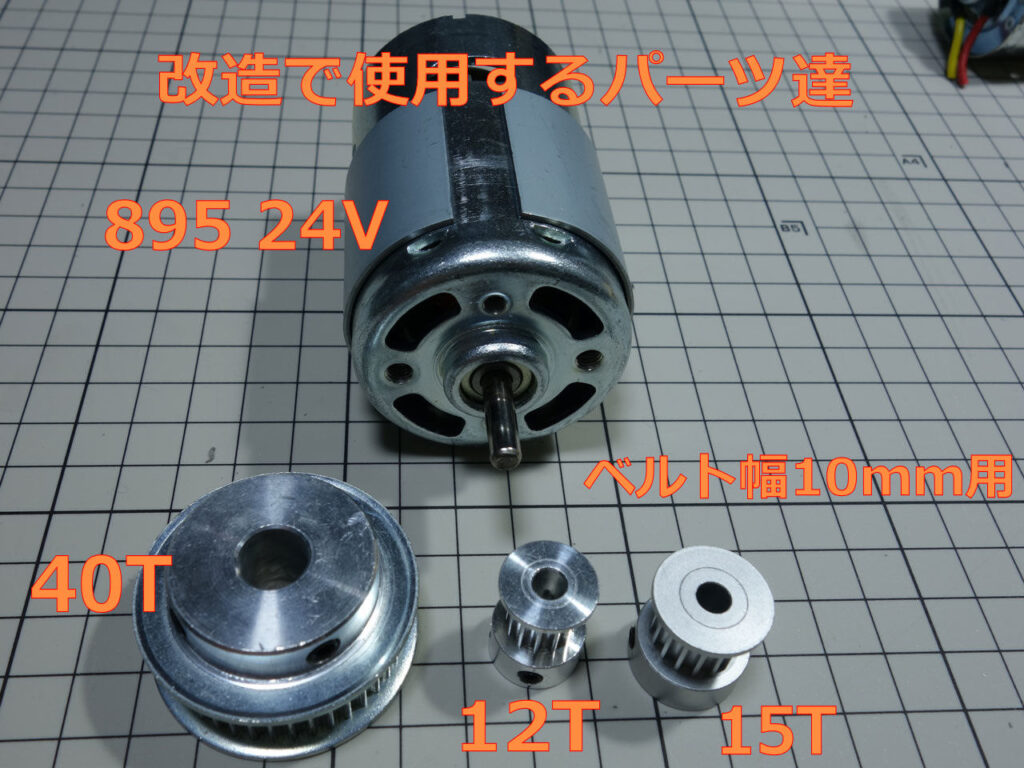
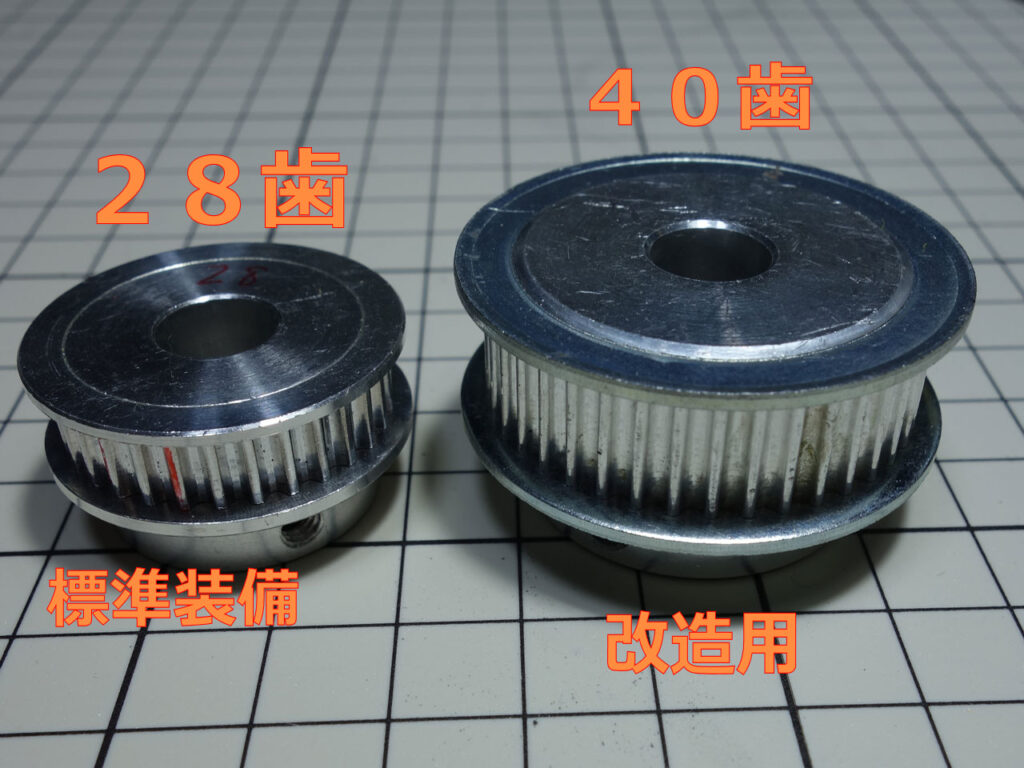
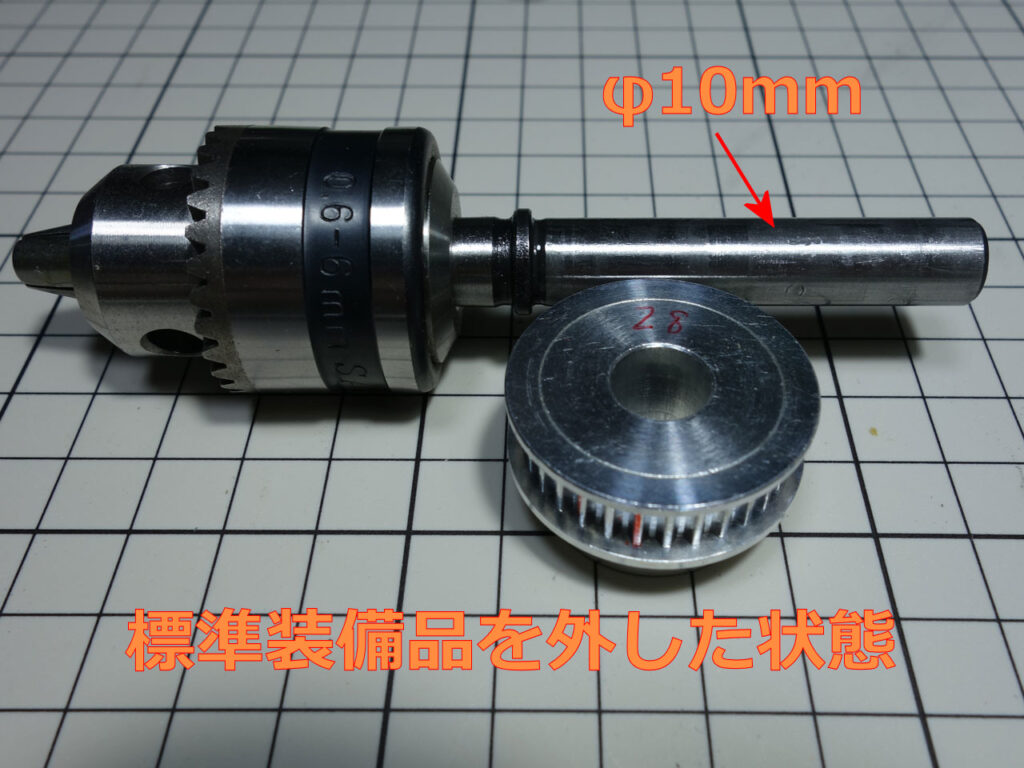
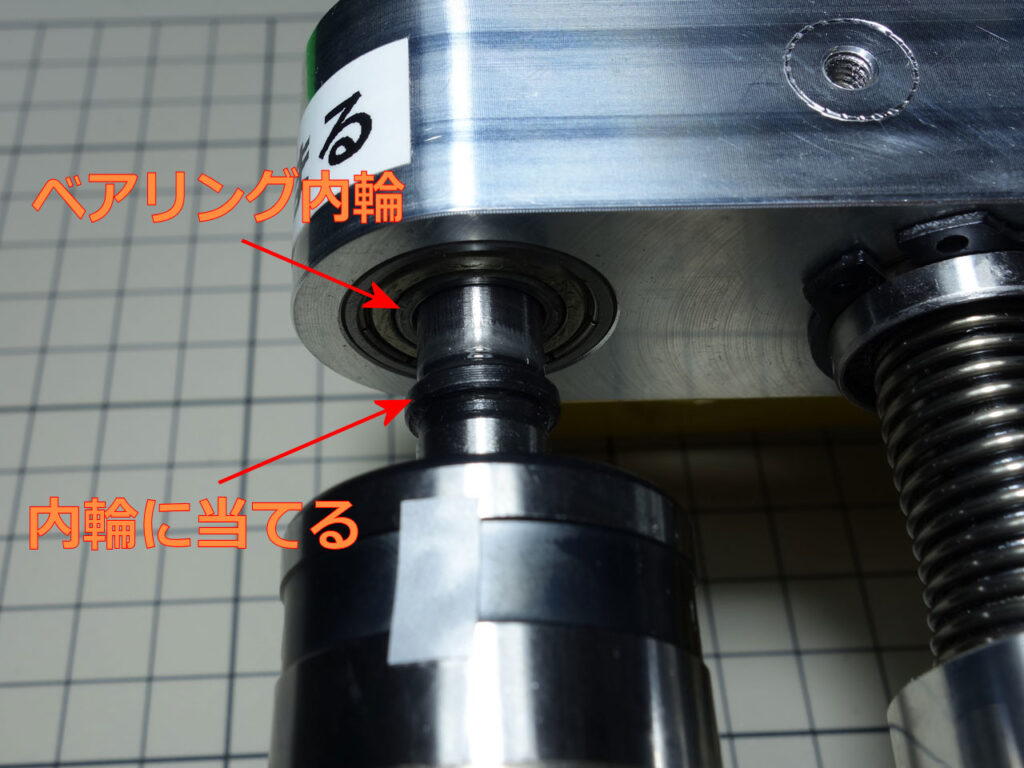
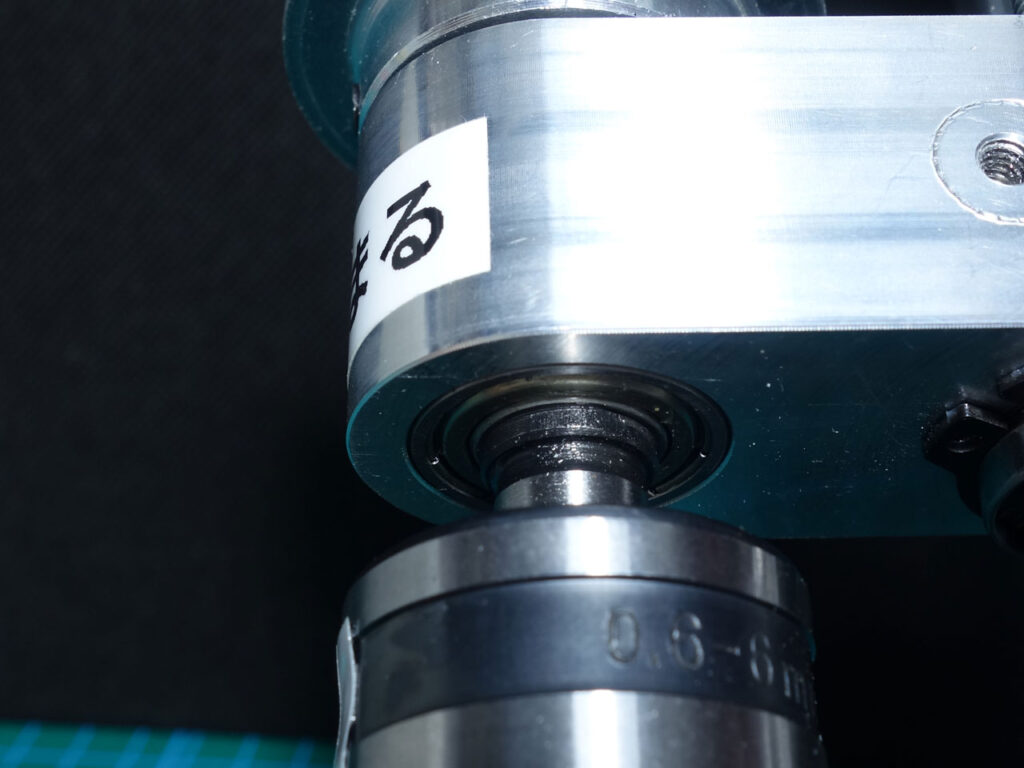
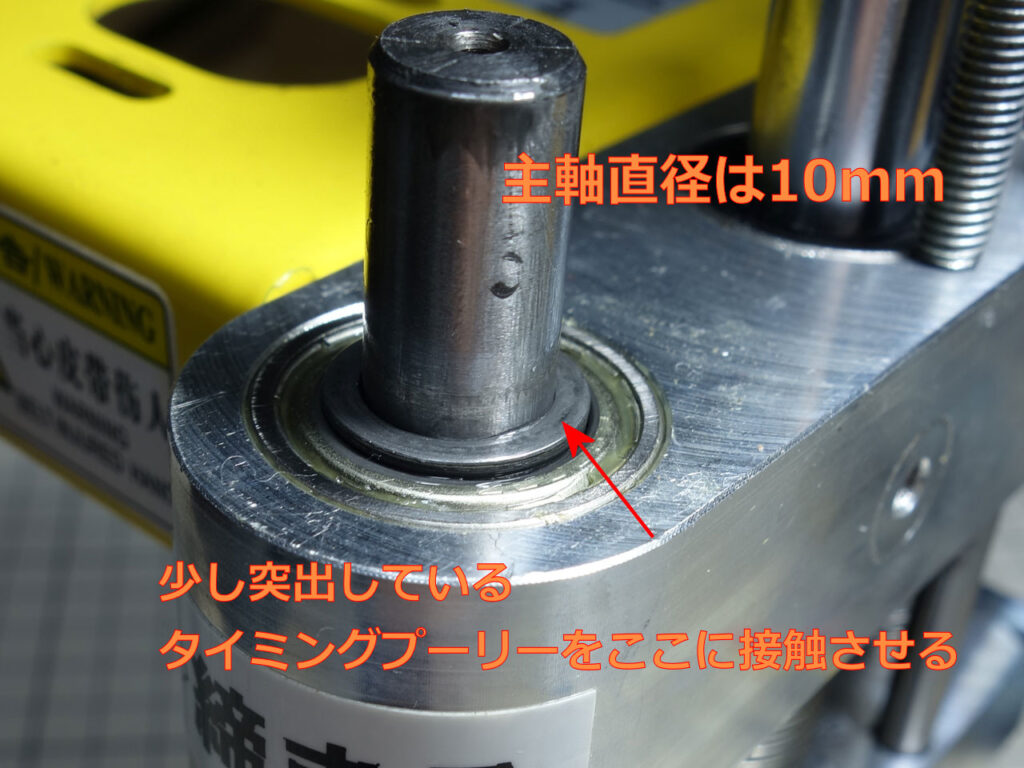
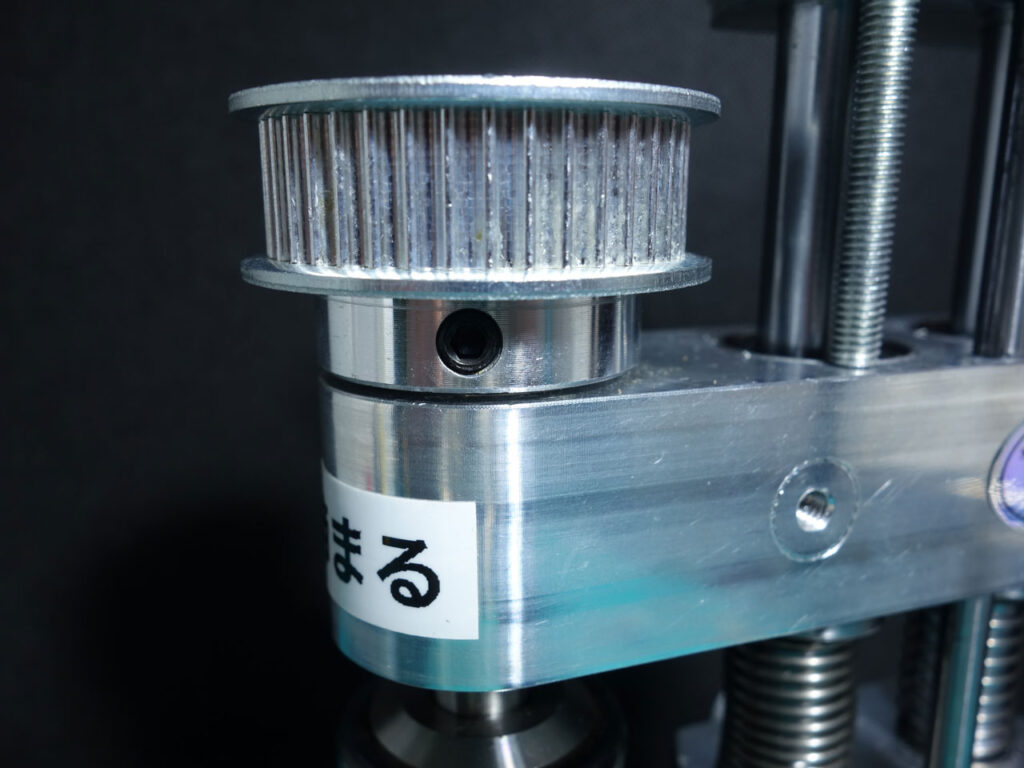
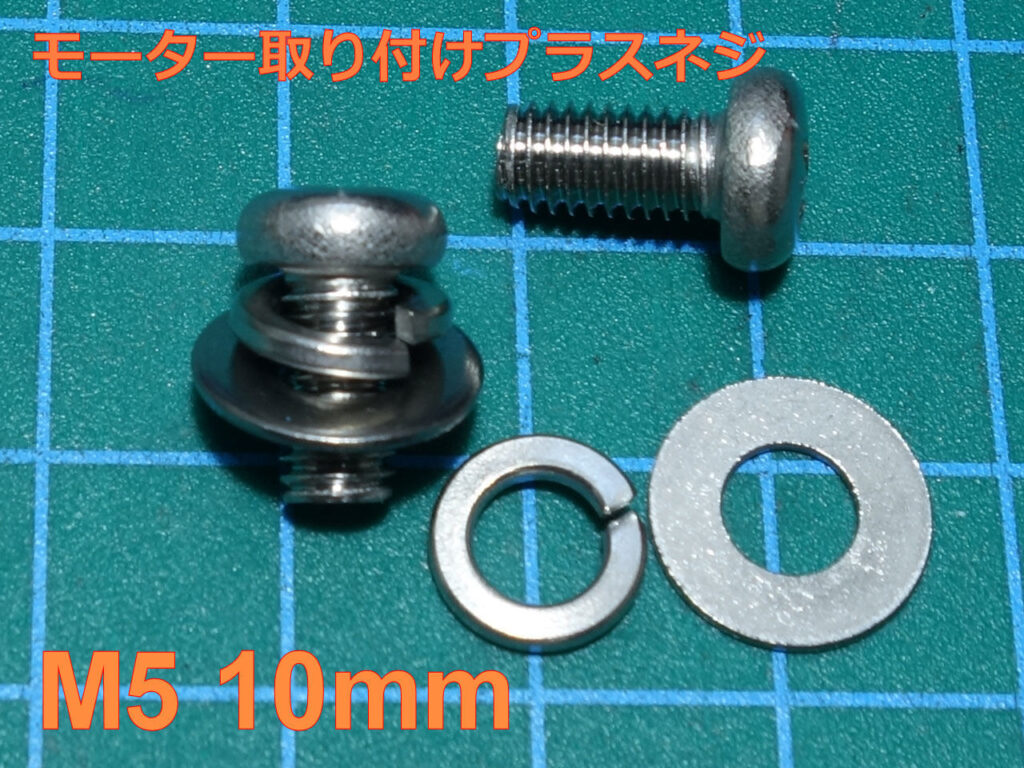
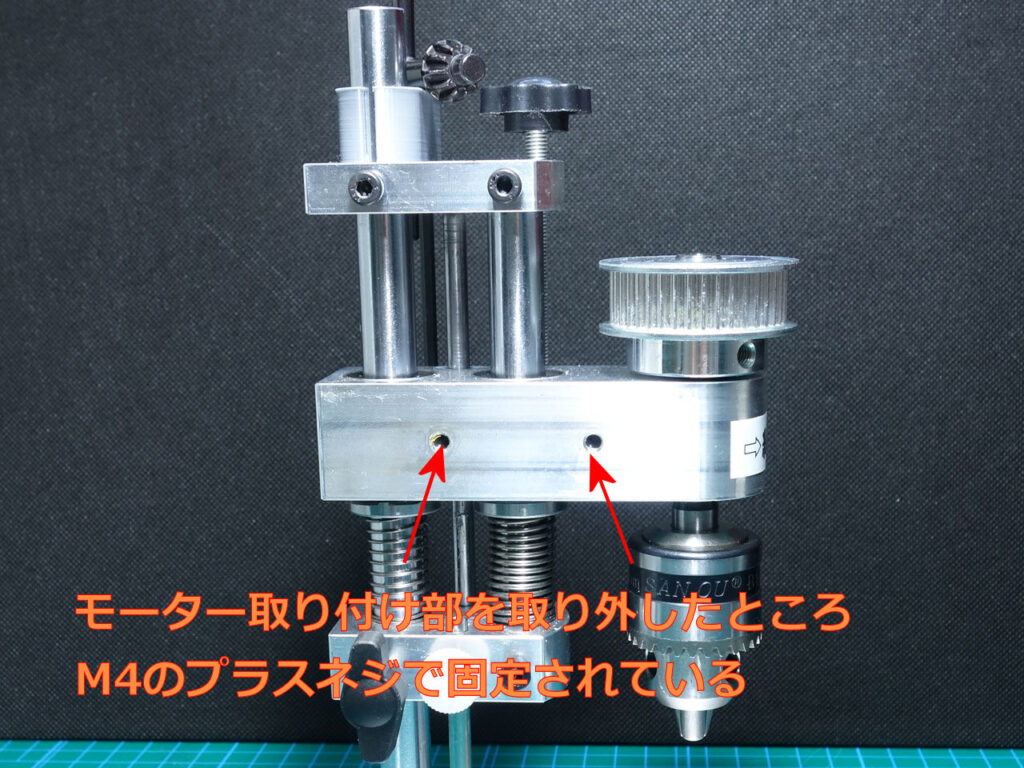
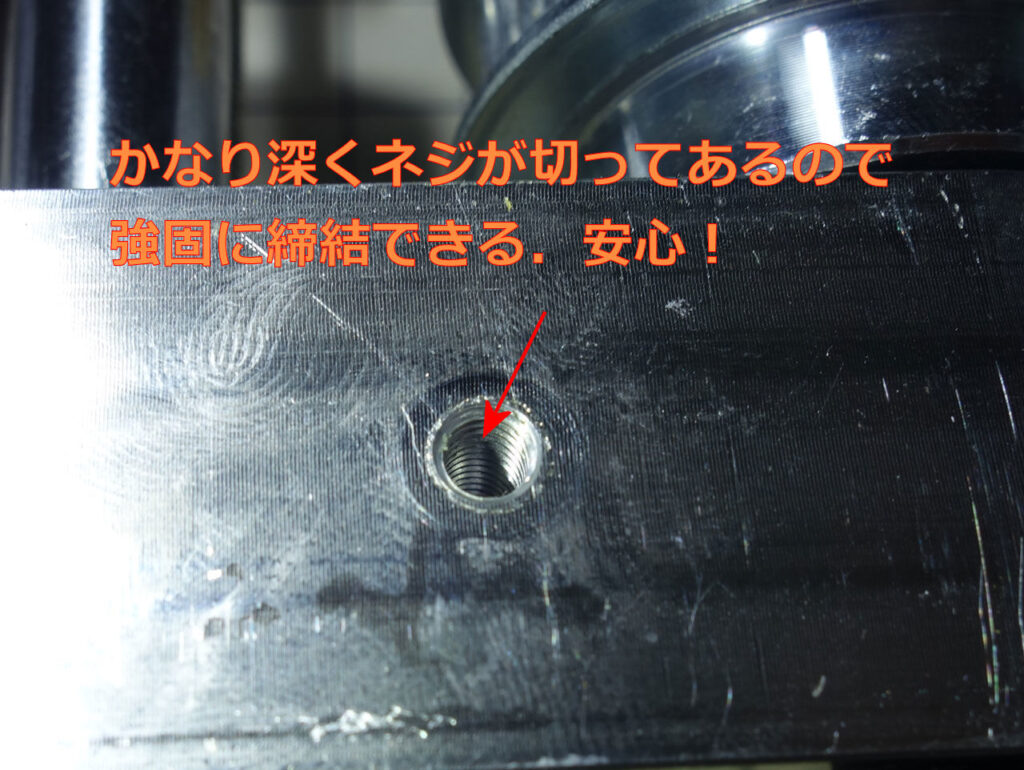
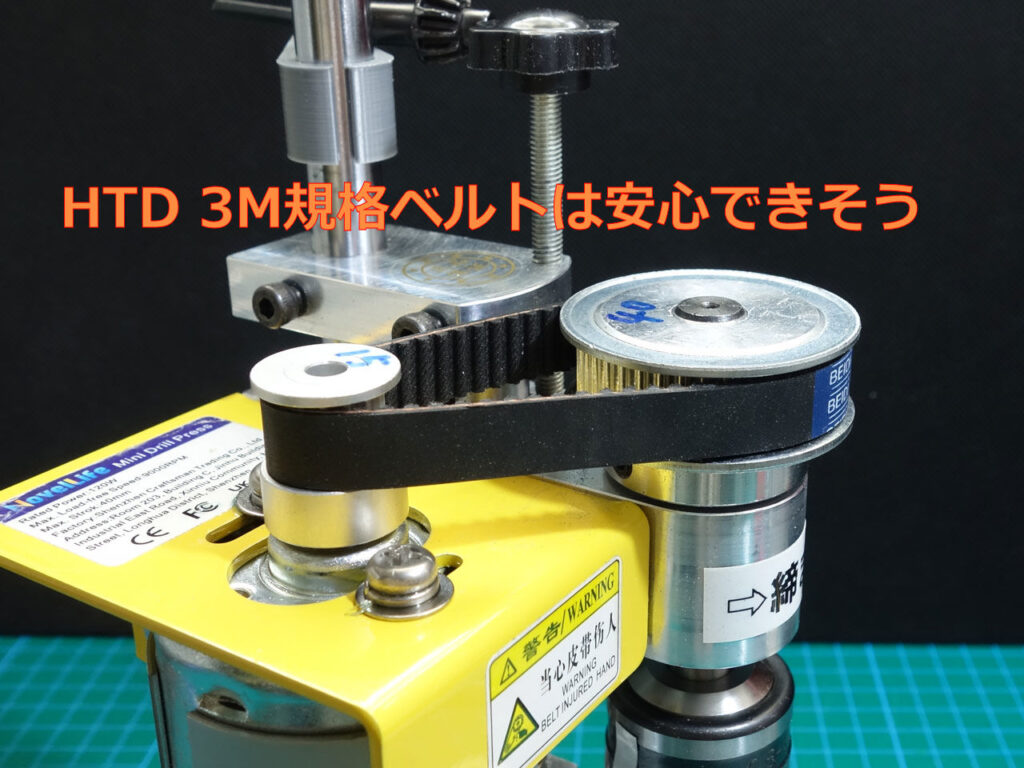
- ドリルチャックは0.6mm~6mmのものが付属していた.別バージョンで10mmまでのものもあるようだがさすがに10mmでは荷が重いだろう
- nano旋盤で使用したチャックと同じメーカーの SAN OU 製である.若干の心ブレがあるので将来的にはいいものがあれば交換を行いたい
- ドリルをチャックにくわえさせるときに,最初は手で大まかな締め込みを行うが,ドリルチャックレンチだと回転方向は間違えることはないが,手回しだとどっちに回したらいいかすぐに忘れてしまう.そこでシールを貼っておいた.すごく便利.忘れる人にはおススメ
- その,ドリルチャックレンチであるが,これもすぐにどっかに行ってしまう.ボール盤あるあるである.そこでホルダーを3Dプリンターで作製した.これもなかなかイケてる
- ドリル主軸を上下させるには,2か所のネジを緩める.上のキャップボルトと,下側のツマミ付きボルトの2か所を緩める.いい高さになったら,まずは下側のツマミで固定する.それから,L字6角レンチでしっかりと締める.この時に使用したレンチもすぐに,どっかに行ってしまうので,先に紹介したホルダーにさしておく
- 当然支柱を中心に回転するのだが,これを規制する仕組みも備わっている.台座に穴が開いていて,そこにロッドを差し込んでおく.この時ユリアねじは緩めておく
- このロッドをユリアねじで固定すれば,これ以上下げたくないという位置で止めるリミッターとしても利用できる.このユリアねじはもともとはキャップボルトなのだが,いちいちレンチで回すのは面倒なので交換した.それほど強く締めこむところではないので,問題ない.ちなみにこの場合,主軸を支柱を軸にすこし回転させて穴の位置から少しずらして固定する
- 主軸プーリー近くに,ノブ付きの長いボルトがある.これ以上主軸を上げたくないという位置で止める場合のリミッターとして使ったり,主軸の上下位置を微調整する場合に使える.ネットでは台座部分にXYクロステーブルを取り付けてドリルの代わりにエンドミルをくわえさせ,フライス盤のように使用している例も見受けられた.この時の主軸を少しずつ下げるのに便利らしい
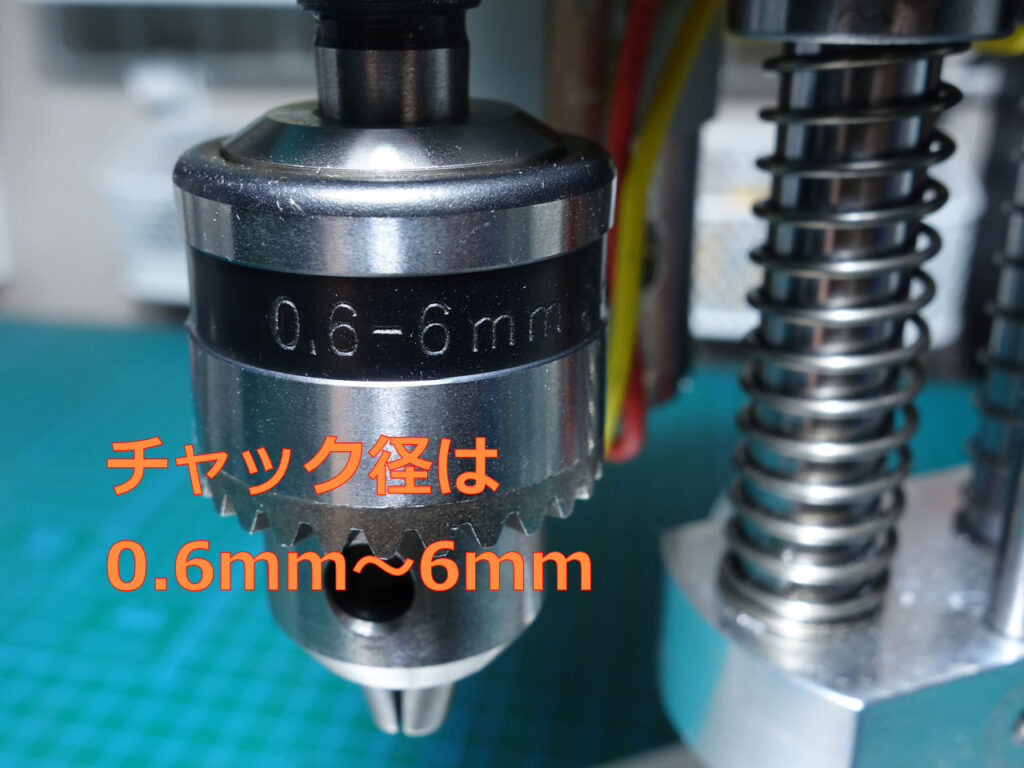
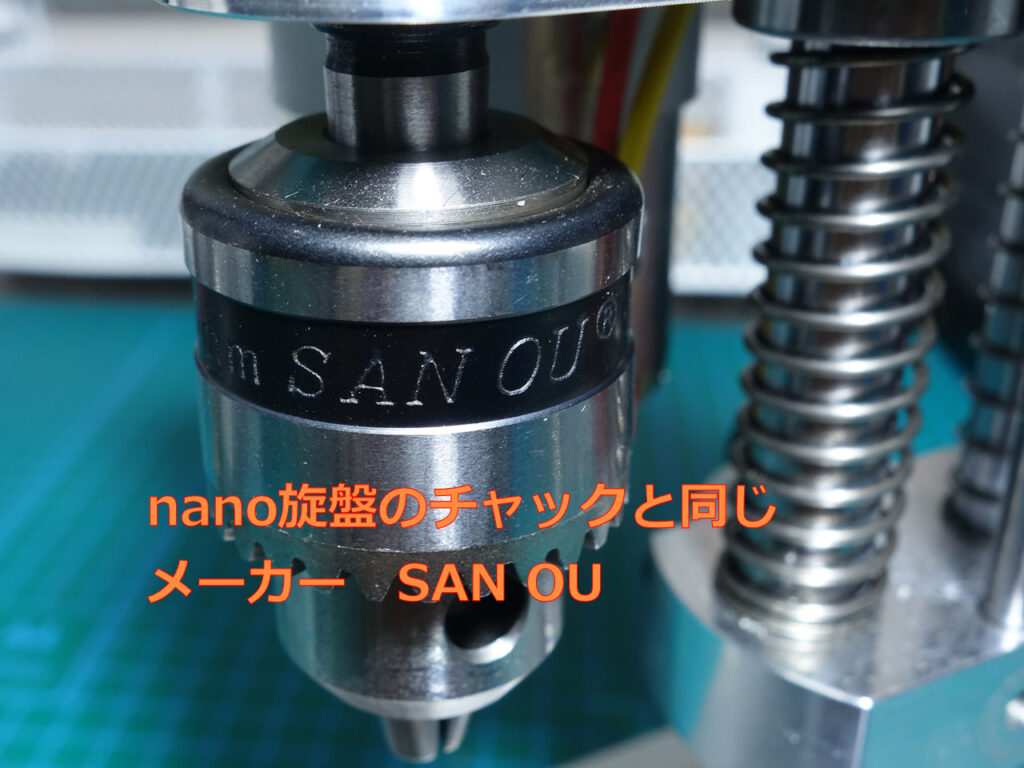
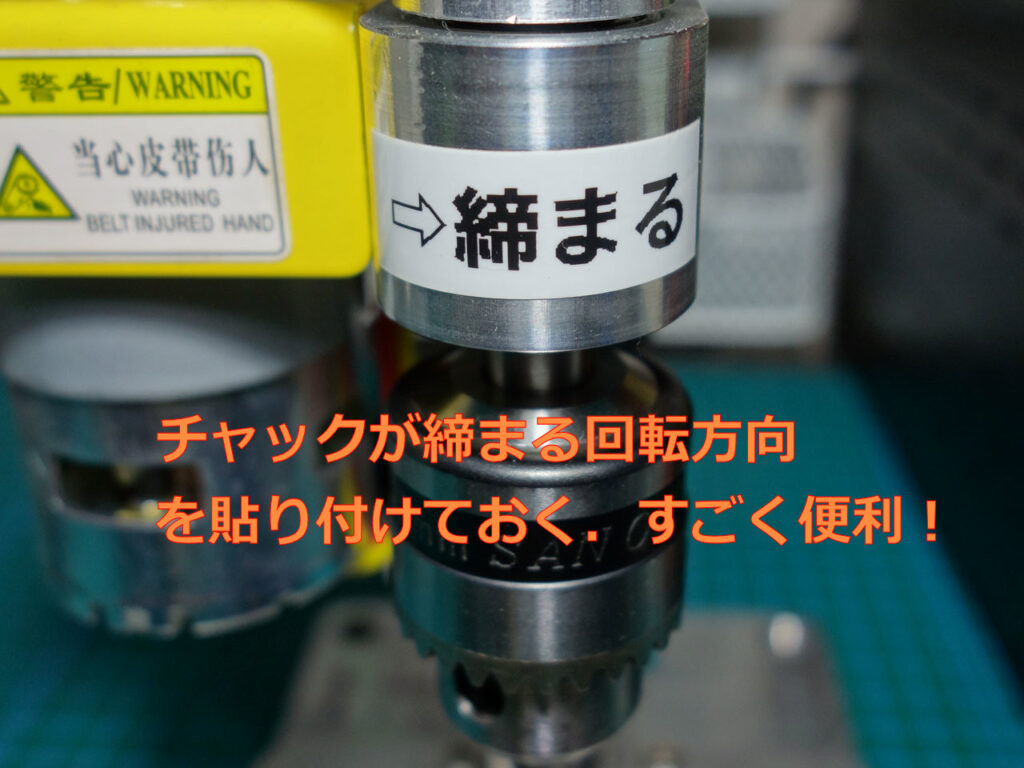
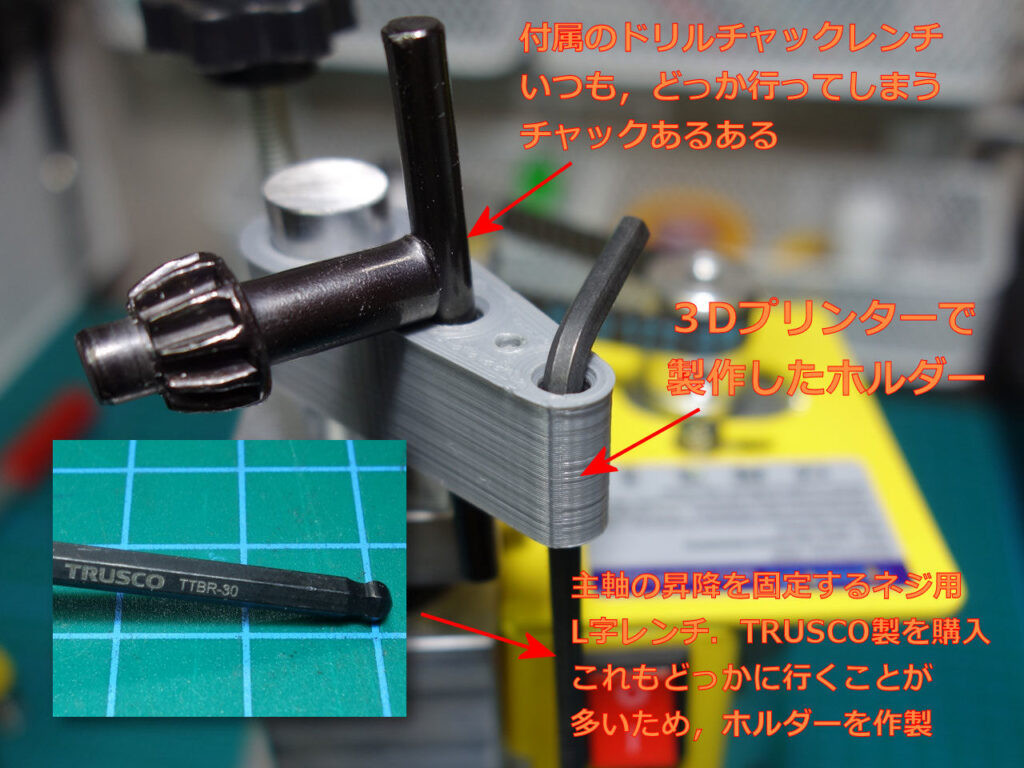
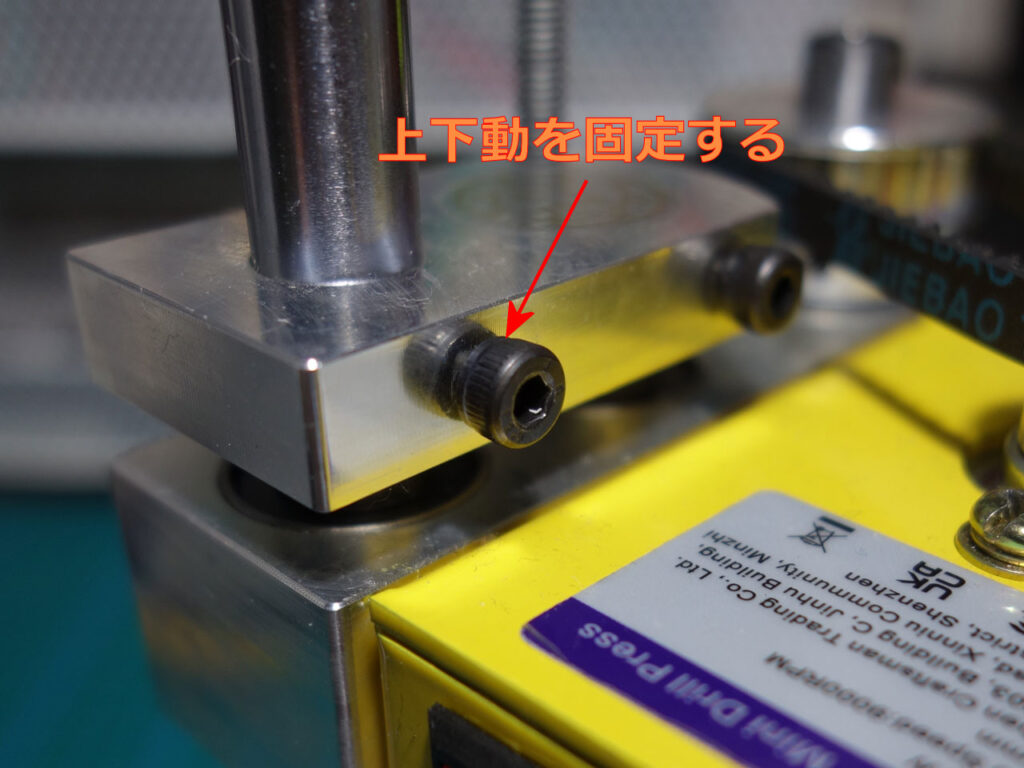
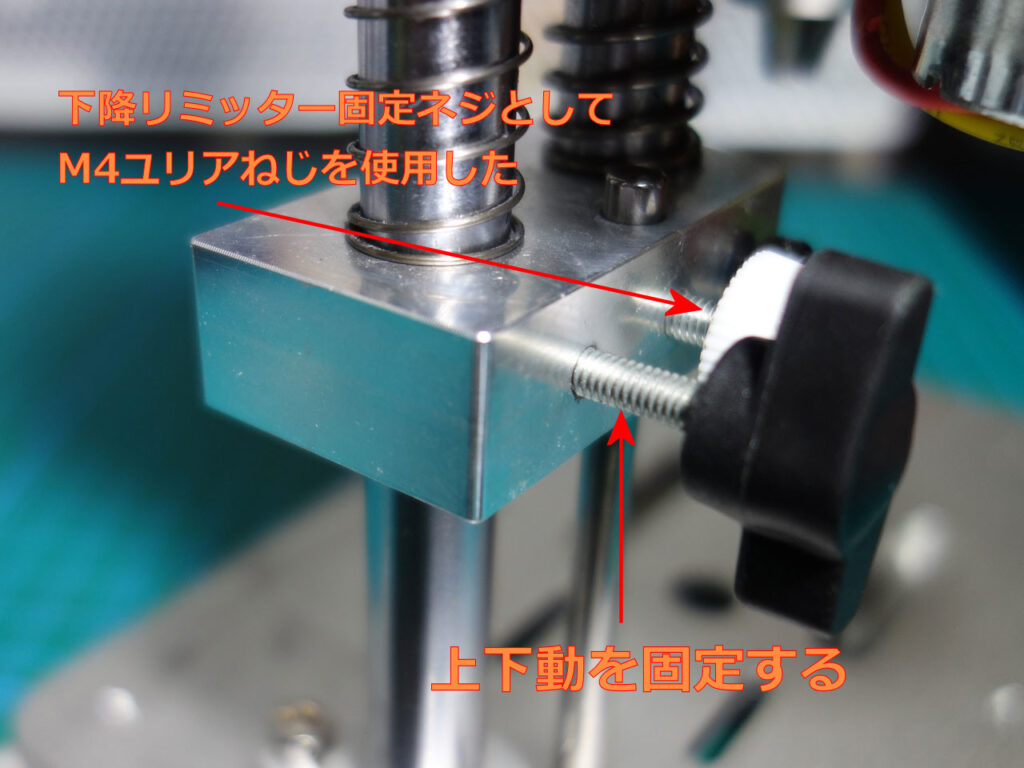
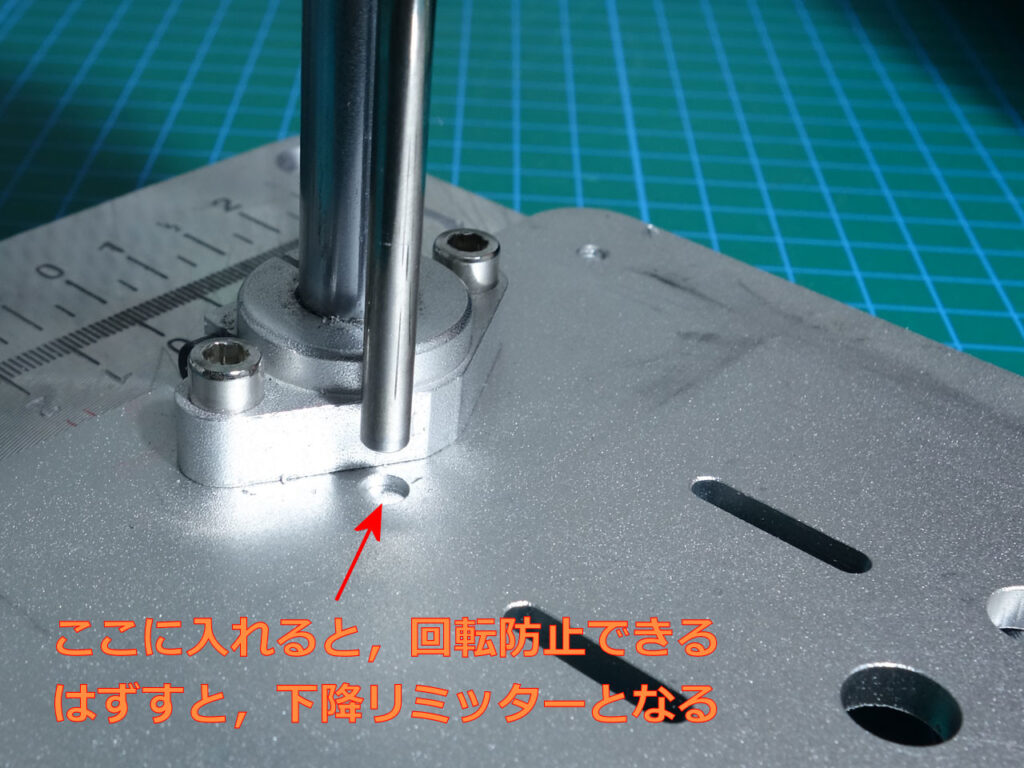
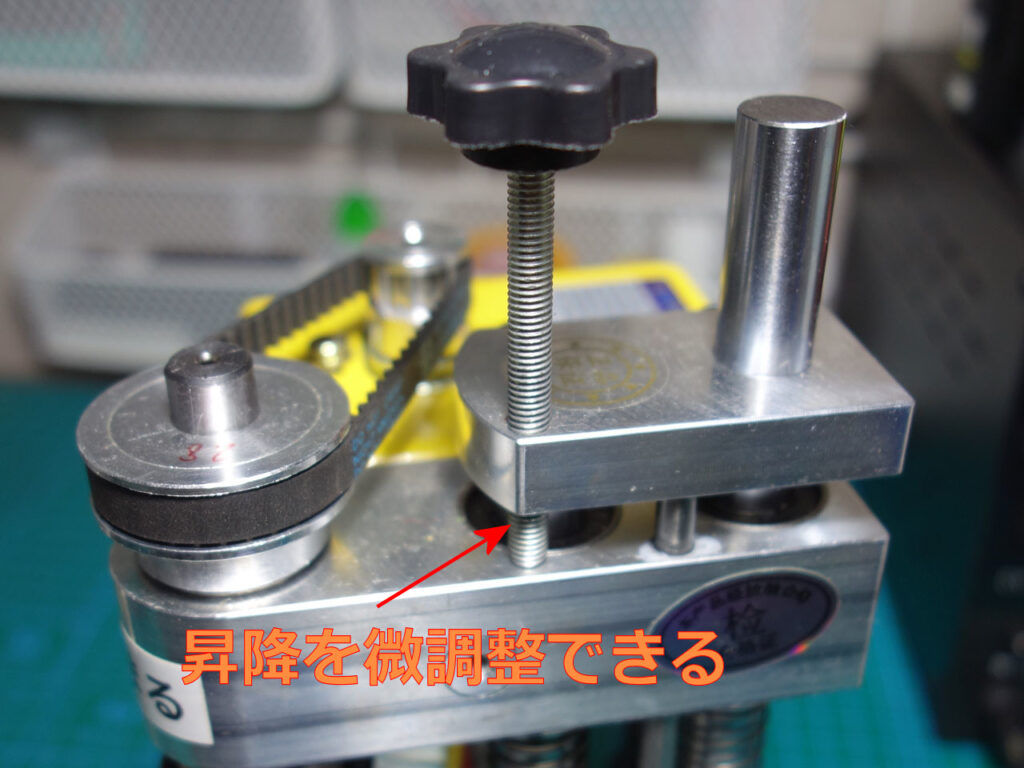
- 電源装置に接続して,電圧を6Vから24Vまで変化させて無負荷主軸回転数を計測した
- モータへ加える電圧と主軸の回転数の関係はきれいな直線となった
- 穴を開ける対象物の材質あるいは使用するドリルにより,適した回転数がある
- 例えば,アクリルでは発熱を避けるため低回転で穴あけする必要がある.アクリル専用ドリルビットは,最大回転数は3000r.p.m 以下と指定されている
- 通常のドリルを使う場合は,新品ではなく使い古した切れないぐらいのもの,あるいは先を加工たドリルで,切削油をさして低速回転で使用する
- アクリルの穴あけについては,こちらのサイトが参考になる
- nanoボール盤のドリルチャックは最大6mmまでなので,φ6mmの穴あけ時には1800r.p.mで加工する必要があることがわかる
- 下記の計測データから,電源装置で12Vの電圧を印加してφ6mmの穴あけを行うのが望ましいことがわかる
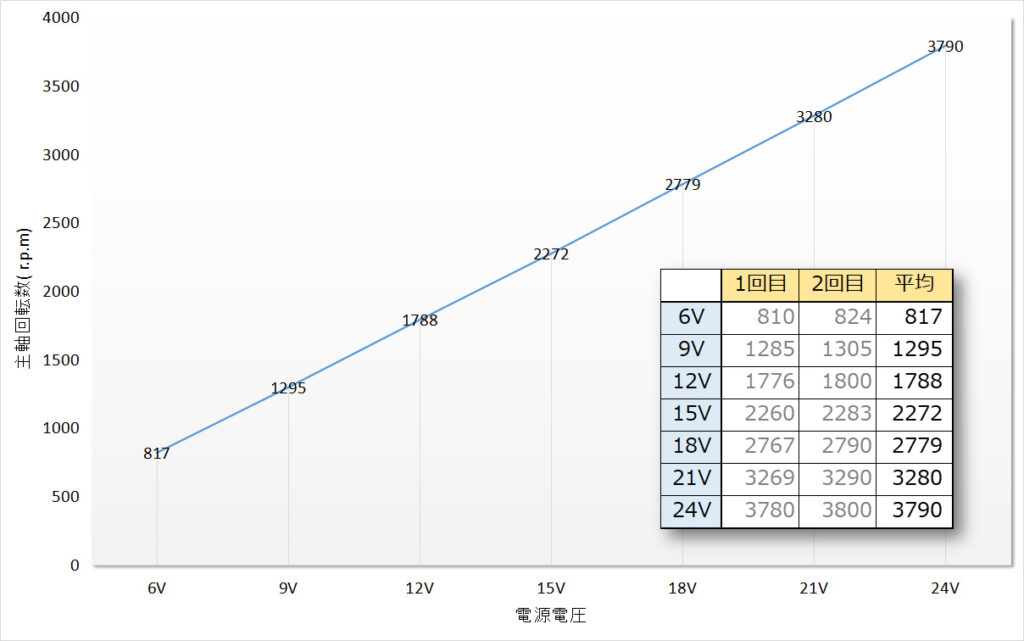