本記事で製作したパーツの3Dプリンターデータファイルはダウンロードセンターにあります
- インサートナットを使用する際,精度よく圧入したいときは,インサートナット圧入スタンドを使用しているが,そこまでではない時はハンダごてを手に持ってフリーハンドで圧入している.何度やっても難しい
- そこでもう少しお手軽&お気軽に圧入できるツールを作ってみることにした
- インサートナット圧入スタンドは便利に使っているのだが,如何せん大きい!もっといえば収納時邪魔なのである.狭い工房の棚に収納するには,いささかでかい!
- 更に欠点として,ボール盤等で言うところの”フトコロ”が小さい.スタンドのテーブル上に載らない物には使用できない.高さも然りである
- インサートナット圧入スタンドだとワークをベースの上にのせて圧入するので,必然的に鉛直方向に圧入することになる.ワークを横倒しにできない場合は,ワークの側面(水平方向)にも圧入できれば便利である
- 圧入時ある程度の高さとフトコロを確保すると,スタンドタイプではそれなりの大ささとなってしまう.収納スペースをくうし,重いし,作業スペース確保も必要だし,出し入れも面倒だしと,”だし”の連発となってしまう
- これらの問題点を解決すべくハンディーインサートナット圧入ツール製作プロジェクトを開始した
- Amazonをみると,ハンダごてにセットする先端の交換式インサートチップがたくさん見られようになったことも,本プロジェクト開始のモチベーションとなった.トレンドなのだろう.しかもあのgoot もラインナップしてきたのである
『PX-280 インサートナット挿入用こて先』 - 今回のプロジェクトではこのインサートチップを使ってみることにした.インサートナット圧入スタンドではチップをnano旋盤で削り出して作っていたが,M2 M2.5 M3 M4 M5 M6 M8用の先端チップが付属しているこの商品で簡単に各種サイズが手に入るので,どんなもんか試してみたくなった.削り出して作ったものは,汎用品と比べ専用品に勝るものはないわけで,先端部の長さや太さを自由に設定できるので,出番がなくなったわけではない
- アダプタと呼ぶロッド状のパーツをハンダごてにとりつける.ロッドの先端には雄ネジがきってあり,そこへ各種サイズの先端チップを取り付けて使用する商品である.メジャーなハンダごてには対応しているようである
- 問題点もある.インサートナット圧入時に,PLAなどのマテリアルが溶けてインサートナット内部に侵入して来る.貫通穴に圧入する場合はタップでさらってやればいいのだが,盲端の場合はかなり困るのである.これは,ナットの長さ(高さ)と同じ長さで先端部(ネジ穴に入る部分)のインサートチップがあれば解決する問題である.汎用品にバリエーションがあればいいのだが,今のところほとんど見つからない.この対策は考えてあるが上手くいくかは不明である
- 早速Fusionで設計にとりかかった.コンセプトはできるだけ小さく.当然使い勝手も良くないといけない.インサートナットの圧入時,インサートチップを抜く時の操作性を重視した.実際にフリーハンドで圧入をしてみると,圧入は案外簡単に入っていくが,インサートチップを抜き取るときにまっすぐ抜くのが難しい.圧入して間もなくだとPLA等のマテリアルが柔らかいので,ちょっと軸がずれるとチップが所定の位置からずれてしまう.つまり正確な圧入は,圧入時よりインサートチップを抜き取るときがキモである
- 当初はUSB充電式のハンダごてを用いるプランであったが,その方式ではインサートナットチップを十分に加熱することが出来ず,お蔵入りとなった.そこで100Vハンダごてを使用するプランに変更した.このハンダごてによるインサートナット圧入は問題なくできることはわかっているので,ツールとしての使い勝手や,圧入の出来映え向上に注力できる.本来のハンダごてとしての使用では問題はない
- インサートナットチップ部の改良を行い,何とか使えるものにしたいと思っている.機構部分は満足いくものができているので,このままお蔵入りは悲しいので
- 常用しているハンダごての,白光のFX-600を使用して製作する.温度調整機能がついておりチップの選択肢も多い.インサートナットの大きさは,例えばM2のものとM8の物では大きさが全く違う.いろいろなサイズのチップに熱容量が異なりそれぞれ適した温度があるはずである.その点で温度調整機能は便利である.この製品をお使いの方は多いと思うので,参考になれば幸いである
- 3Dプリンターで造形するパーツ,ステンレスロッド,押しバネが主な構成要素となる.パーツごとの製作,組み立てについて紹介する
- 今回使用したフィラメントはこちらのPLA
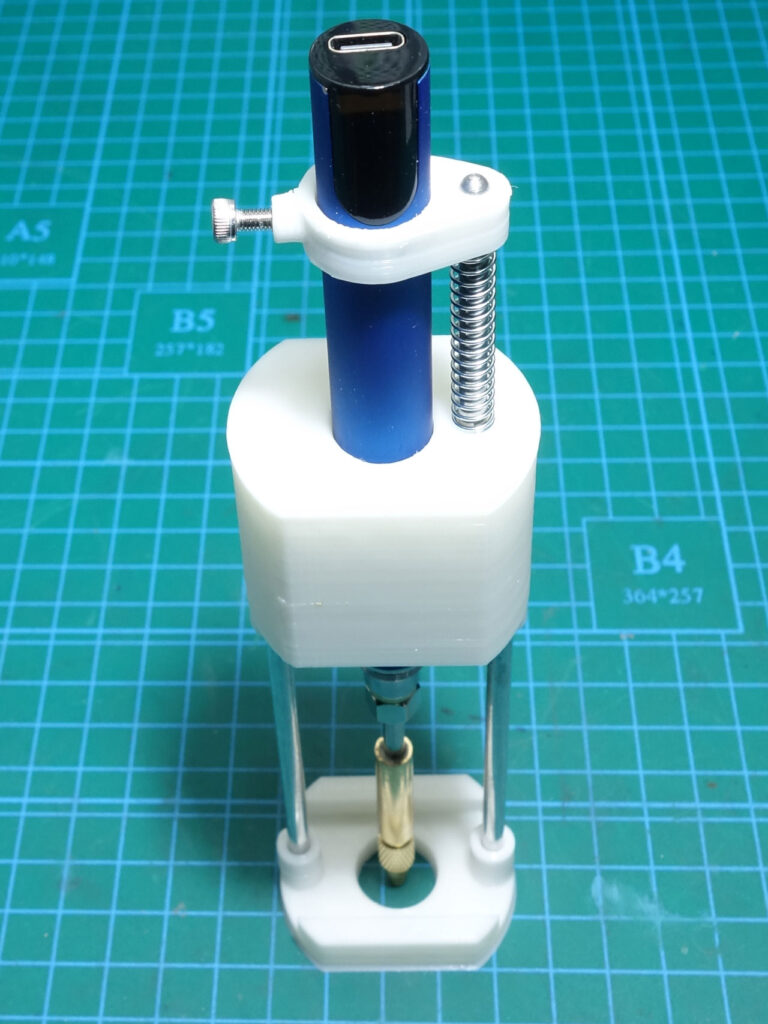
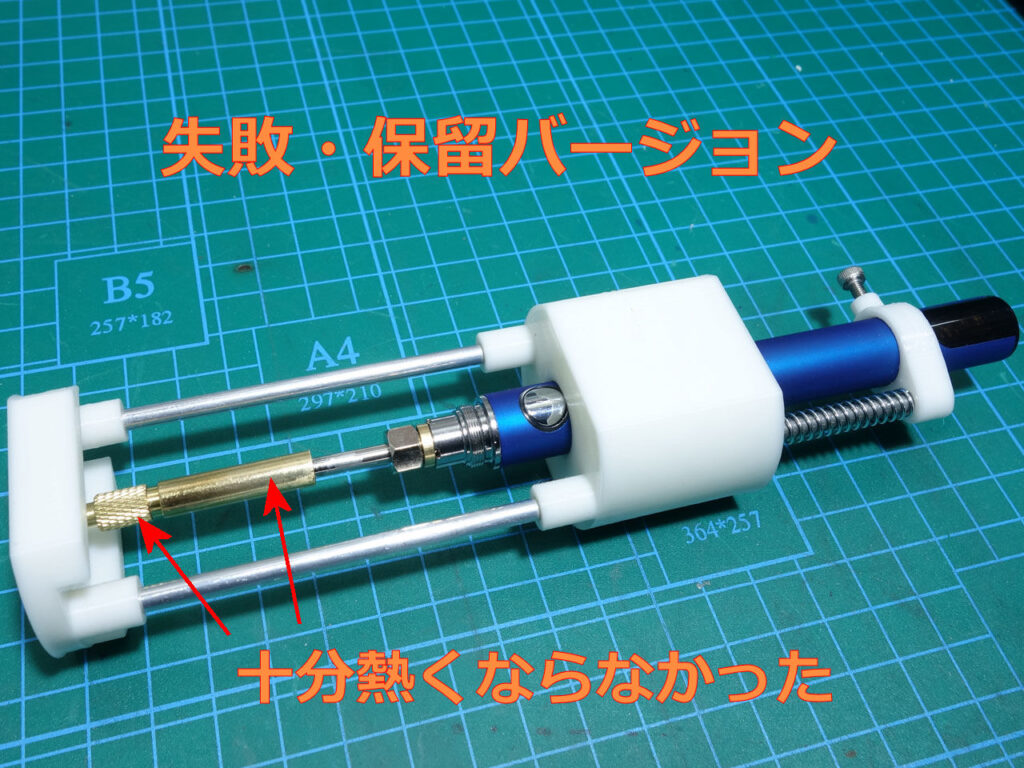
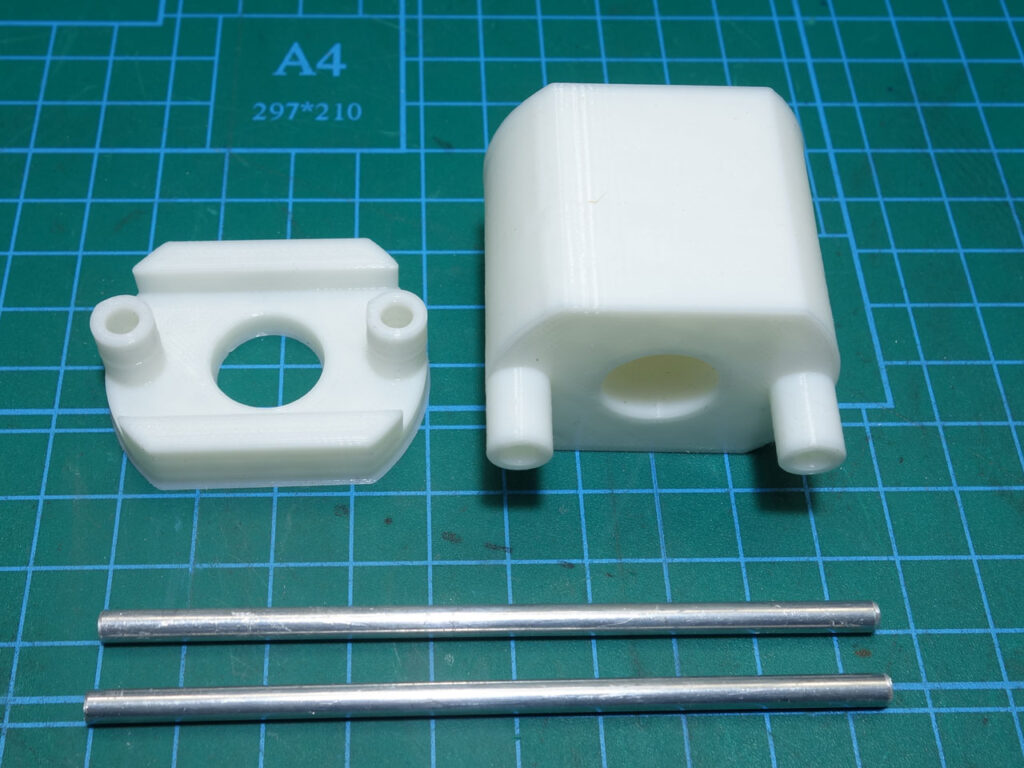
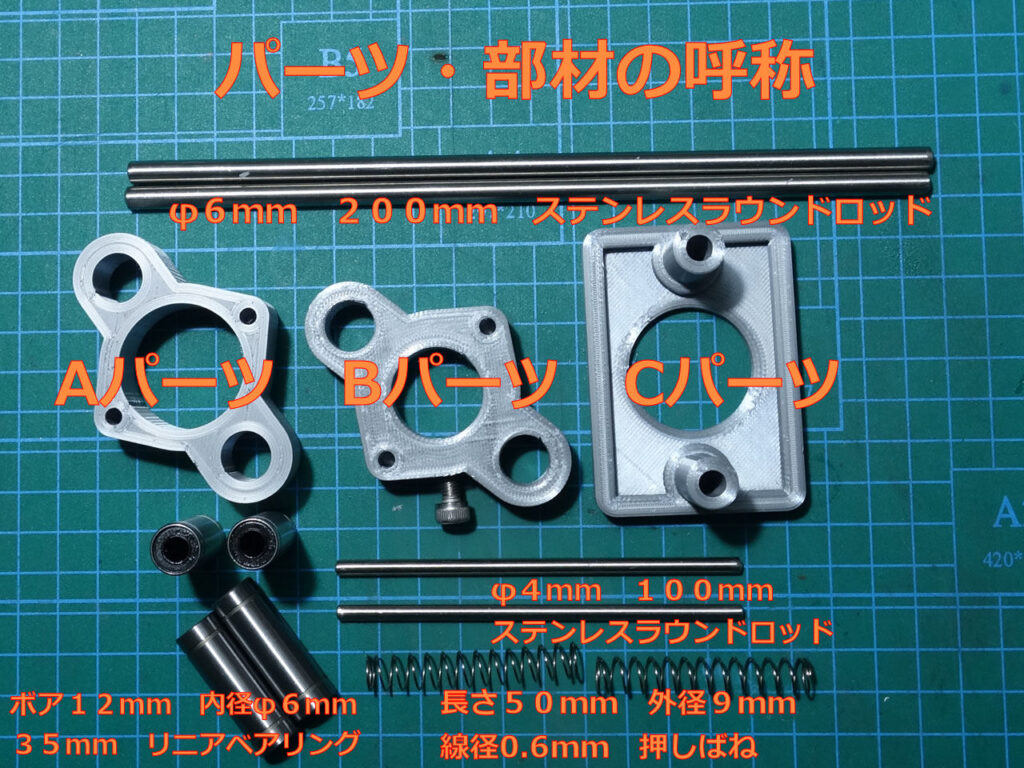
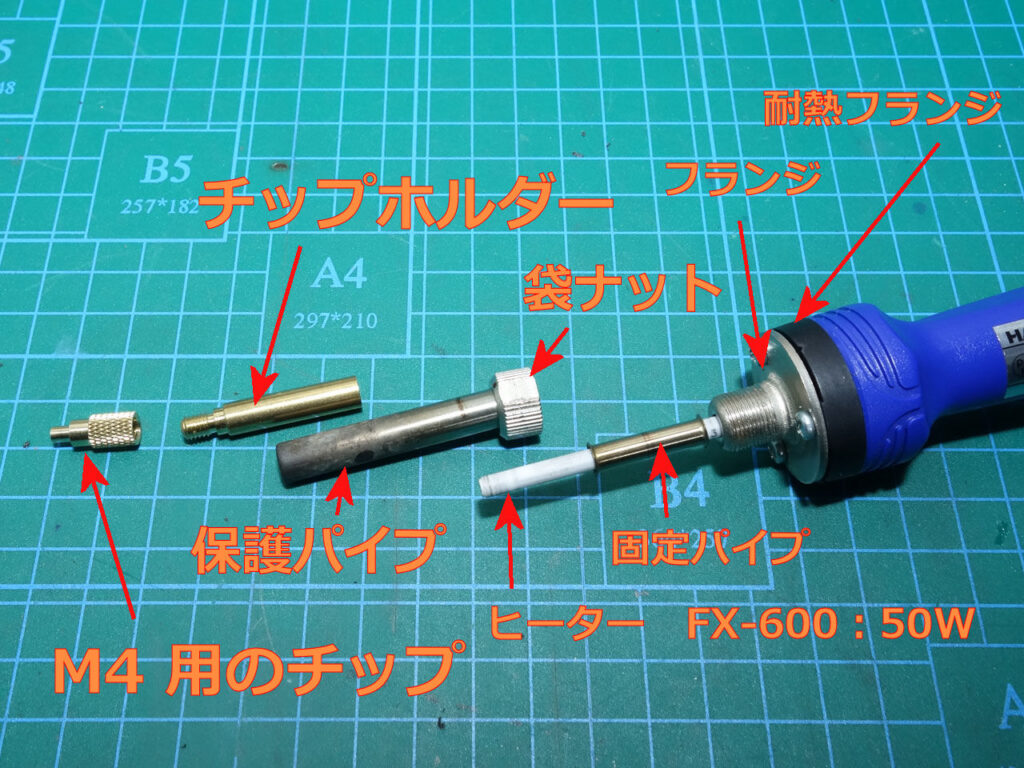
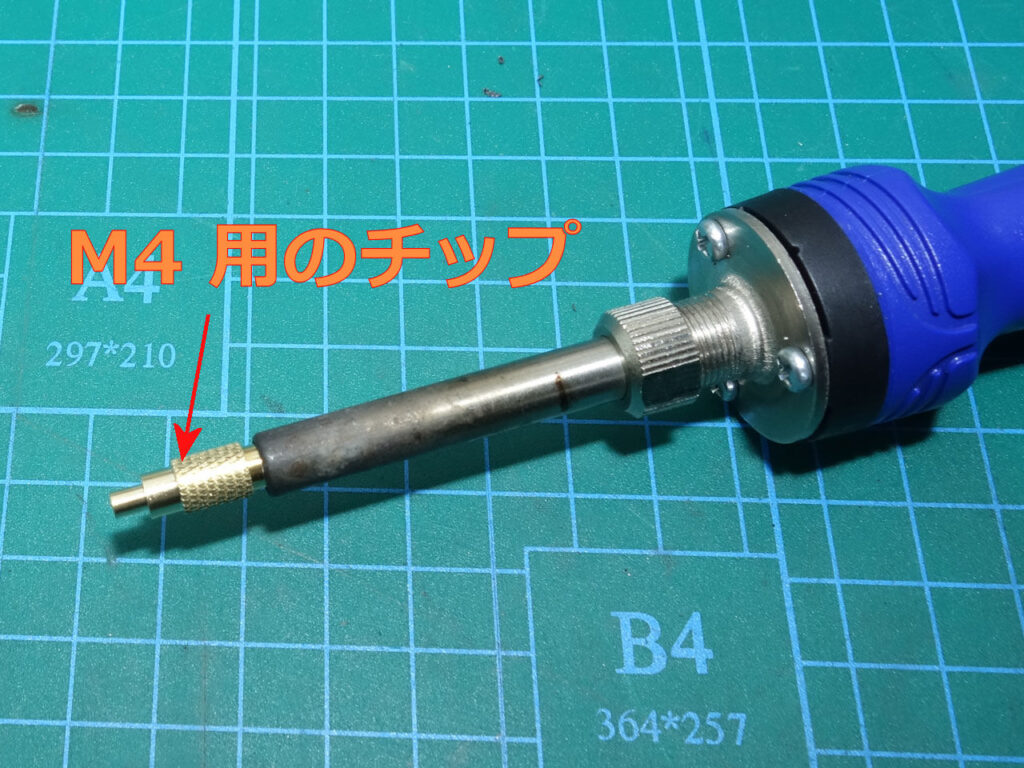
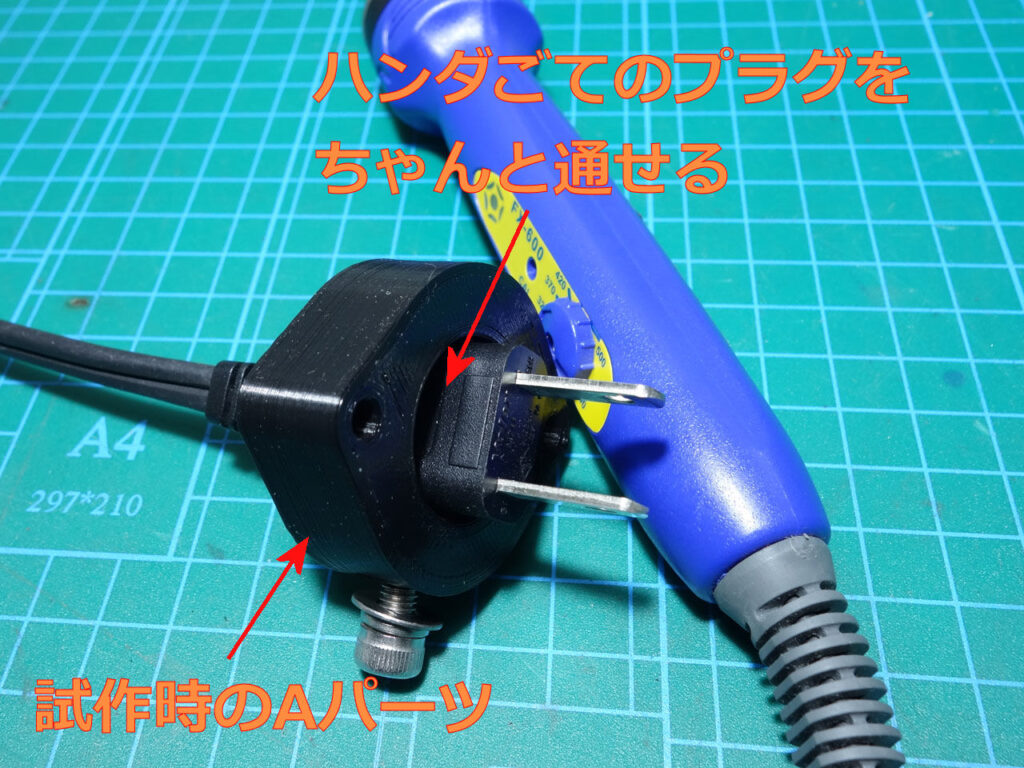
- ハンダごての上部?(コードの出ている方)を保持する部分で,Aパーツと呼ぶことにする
- ハンダごてのこの部分は,円柱状であるため,円筒形のパーツをPLAで印刷した.内径22mmで試作したのだが,いい塩梅であったのだが,PLAの製品によって微妙にきつくなったり,緩かったりする.普段使うことが多いeSUNのPLA+で造形すると,穴が設計通りに造形されるのだが,今回シルバーメタリックにしたかったので変更したら,わずかに穴が大きく造形された
- Aパーツはハンダごてにしっかりと固定するためにネジ止めとする.ハンダごての同部にはハンダごてを組み立て用にビス止め用のザグリ穴が開いている.それを利用することにした.Aパーツの側面にM5キャップボルト用のネジ穴を付与してキャップボルトをザグリ穴に向けて貫通させ締め込む.しっかりとロックできた
- M5タップを切るための下穴をドリルで開けるのだが,センターへ向けて正確に開けるたnanoボール盤で開けたのだが最低回転数で下穴を拡大したのだが,熱でPLAが溶けてしまった.その結果ドリル刃が固着してしまった.失敗だったが,ドリルの先がセンターに来ていたのがわかってよかった
- この横穴を造形すると,内面に穴の直径幅の帯状の隆起部分ができてしまう.これはFusionでの設計がまずいのか,スライサーの問題なのか不明である.内壁面まで貫通させないと回避できるようなのでタップの下穴はドリルで開けることにした
- AパーツにはBパーツと連結するためのφ4mmステンレスラウンドロッドを入れる穴も造形しておく.ガタは許されないので,3.7mmの下穴とした.これも使用するPLAによってきつさは変化するので,試作が必要である.きつめに造形して油圧プレスで圧入した.3.7mmは小さすぎに思えたが,今回使用したSilk PLA Pro シルク シルバーではこれぐらい小さめにしないと想定している状態には造形されなかった.最終的にはドリル,ハンドリーマーで仕上げるので小さめならそれほど気にしなくていいとはもう
- 試作1号ではスライド用のリニアベアリングはBパーツのみに取り付けたのだが,わずかだがAパーツとの位置関係がズレてしまう.そこでAパーツにもリニアベアリングを取り付けることにした
- ここでトラブルの話し.プロジェクト開始にあたりAmazonでリニアベアリングを購入したのだが,これが全く使えないレベルの粗悪品であった.φ6mmステンレスラウンドロッドを入れてスライドさせると,ゴロゴロ,シャラシャラと音や振動が感じられる.新品なのにオイル切れでもあるまい.というかそういうレベルではない.グリスをたっぷり入れて誤魔化そうかとも考えたが,全長が長いものを再度購入して試してみることにした
- 失敗購入品はボア(外径)12mm,全長19mmのもの.仕方がないのでAmazonで次の候補を物色しているとボア12mm,全長35mmの商品があった.ストアが同じであるため少し心配だった.国産有名メーカーのものは見たことも,もちろん使ったこともないので比較しようがないが問題ないと思う.4個入りなので余らせてももったいないので,Aパーツへの装着動機ともなった
- 着荷後まず試すのは,不具合のないリニアベアリングではどんなものか(スライド具合)と長くなった分ブレが抑えられるのではないかという点である.結論からいうと,両方とも期待通りであった.スライドは滑らかで,わざと垂直に上下スライドしないよう色んな方向ヘズラす力を加えてみたが,スムーズに転がるベアリングのボールが感じられる.求めていた感触である.グリスをしっかり塗って使うことにする
- リニアベアリングを固定する内径12mmの穴も造形した.同じ穴はBパーツにもあるので,そこで説明する
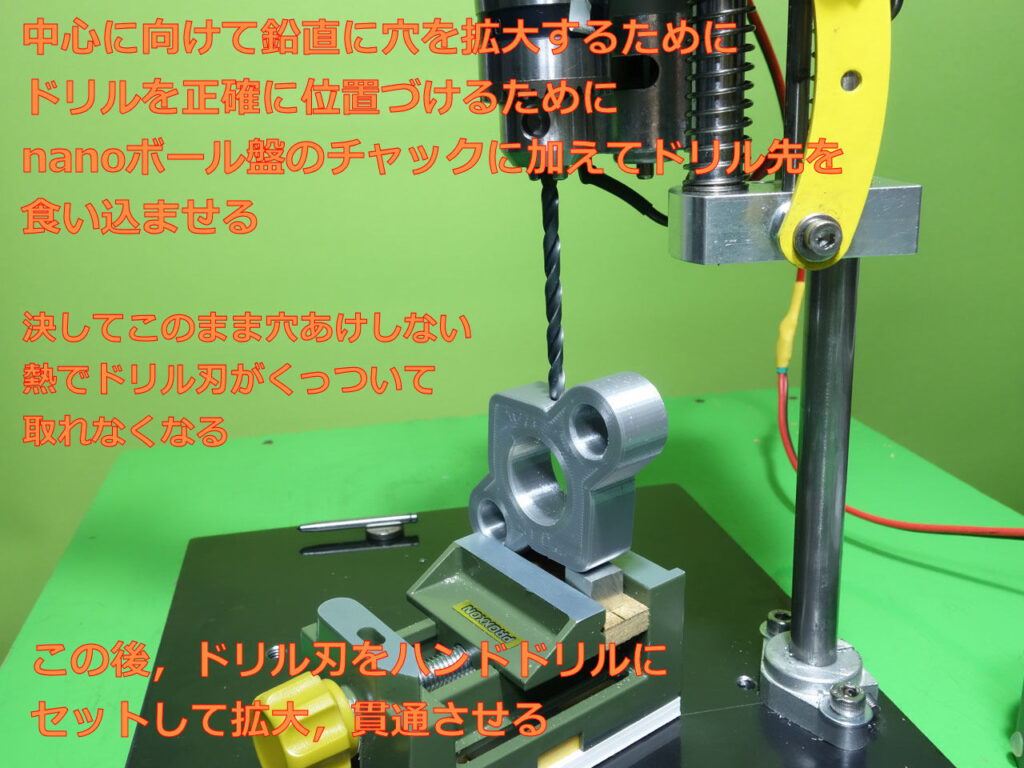
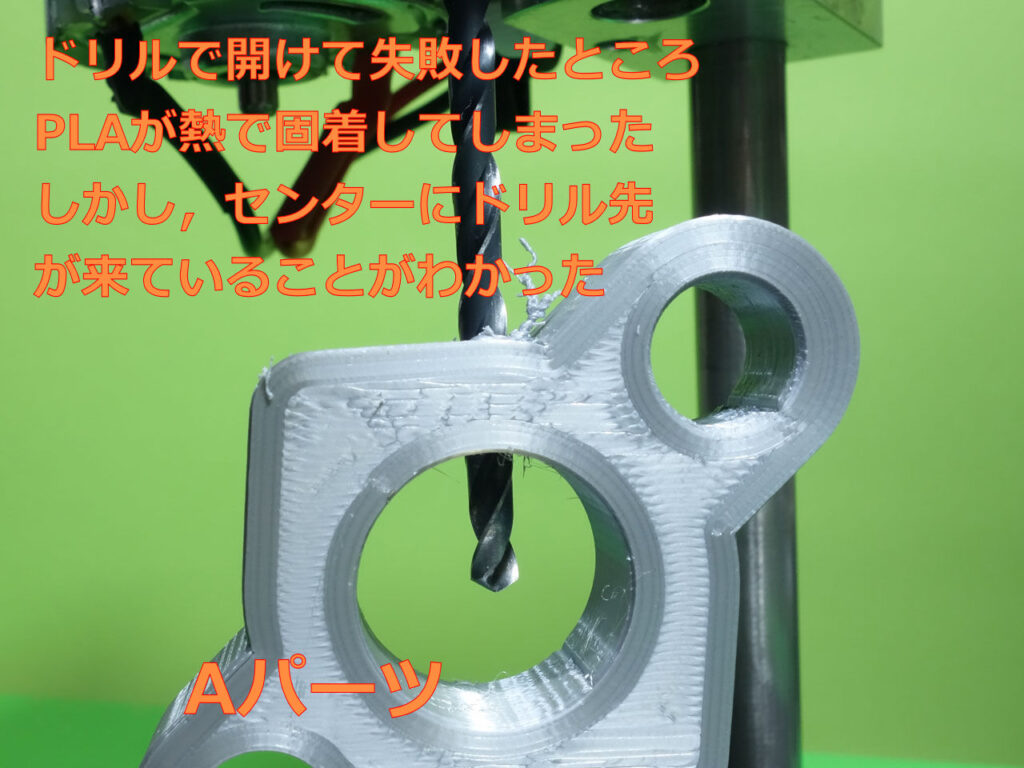
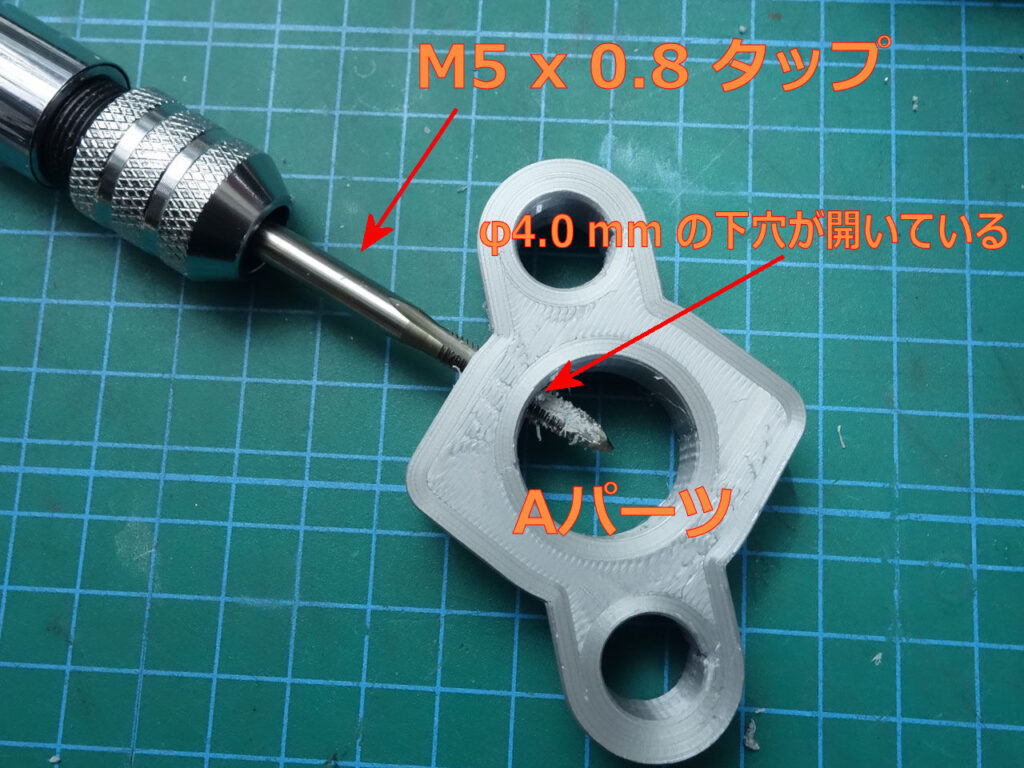
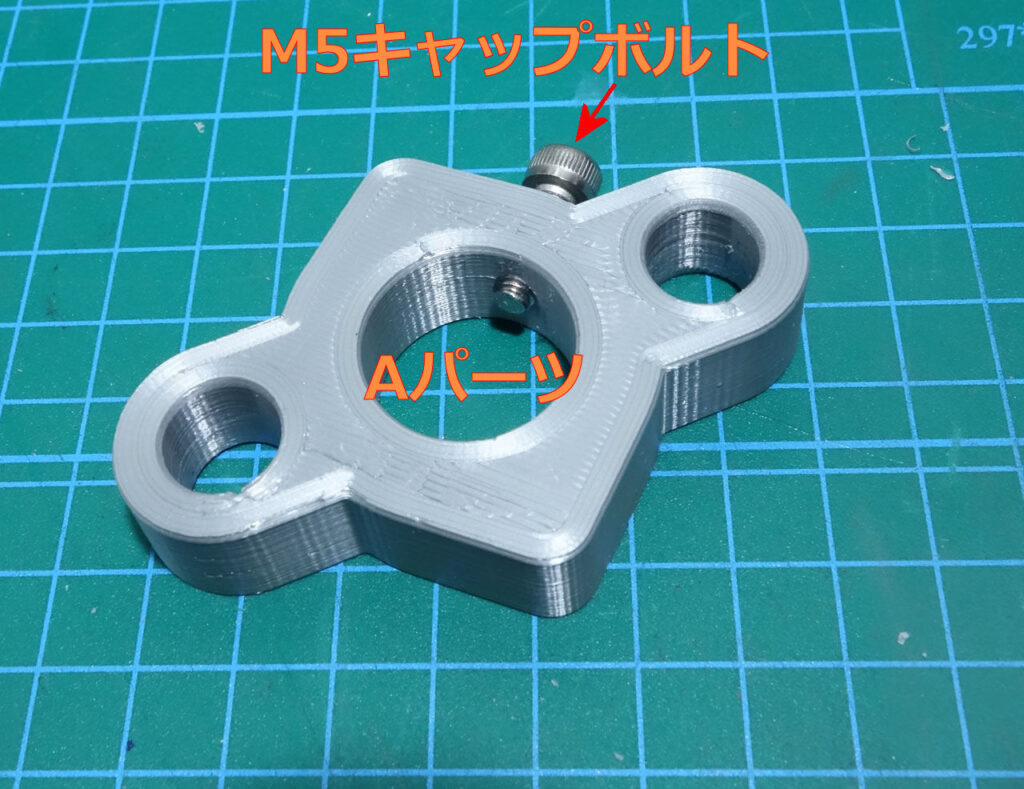
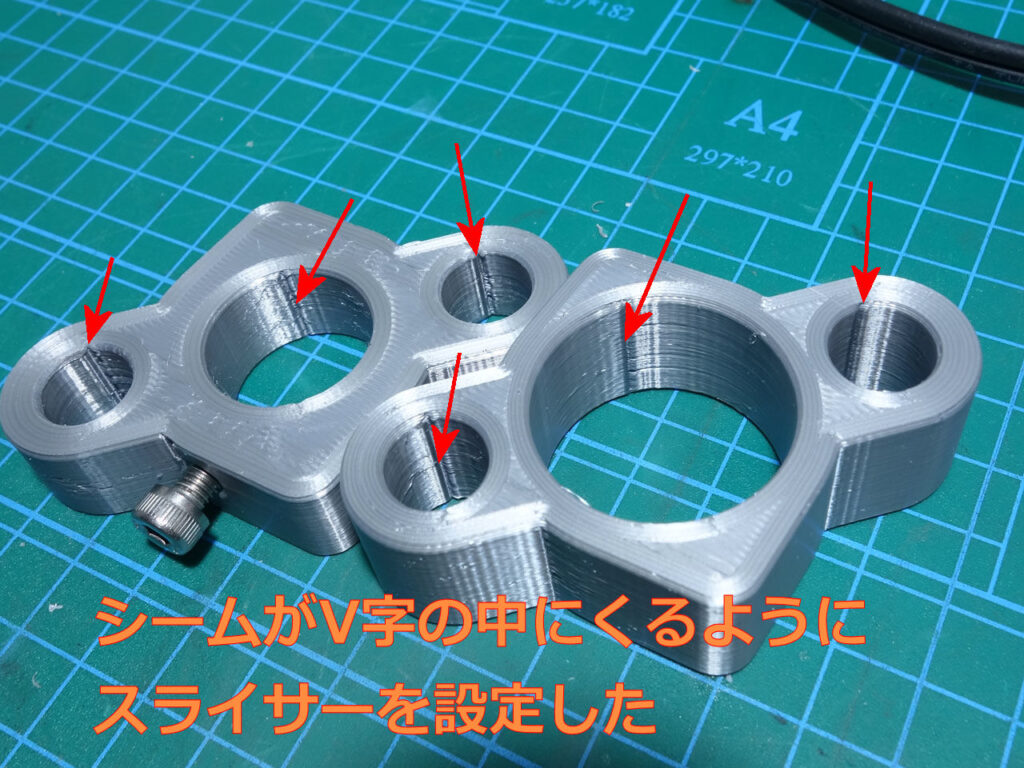
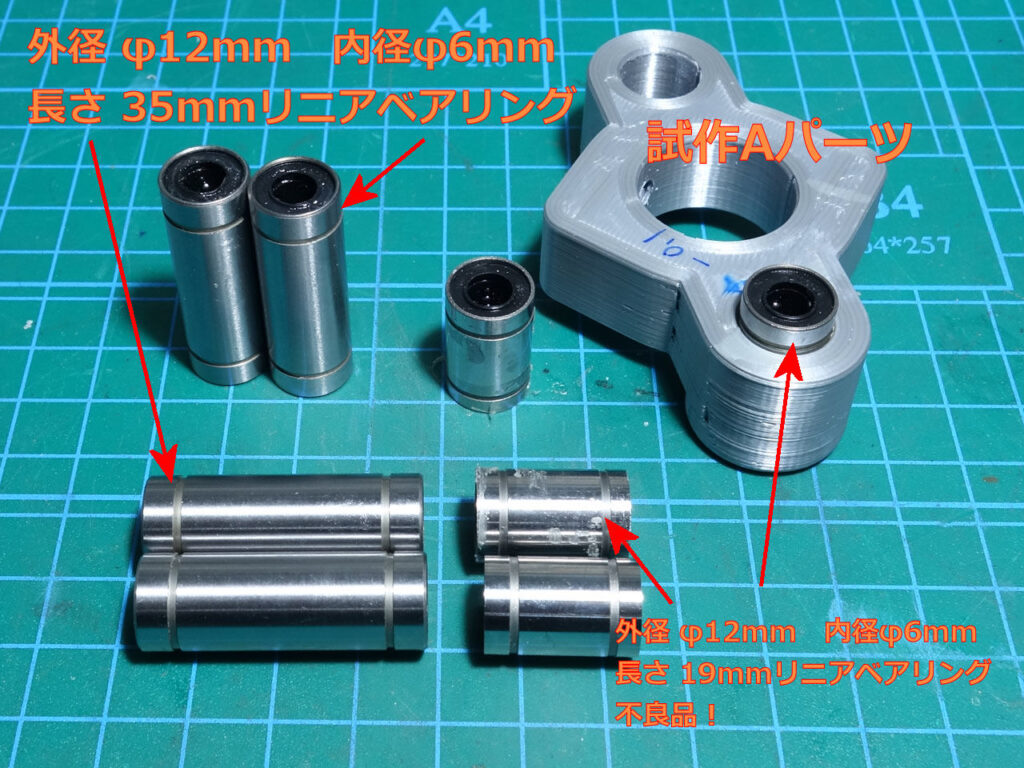
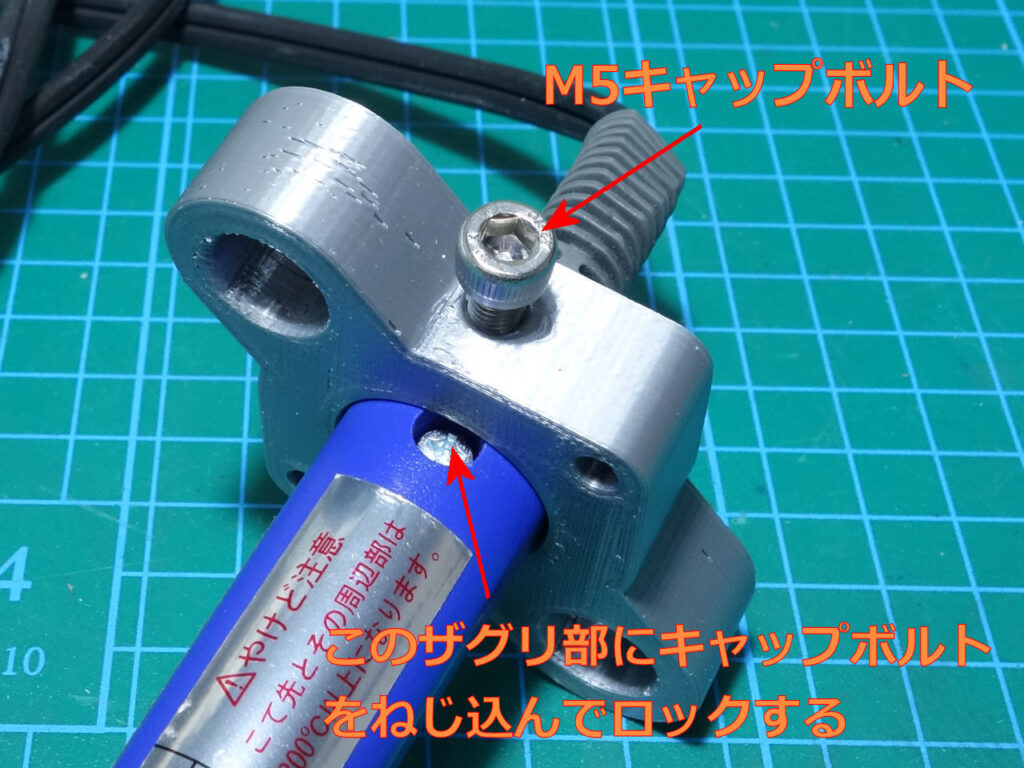
- ハンダごての中央部で持ち手(青いプラスチック部)をホールドするパーツで,Bパーツと呼ぶことにする
- Aパーツはしっかり固定だが,Bパーツはややルーズにハンダごてを保持するように造形する.着脱に軽い抵抗がある程度で,ガタは出来るだけなくす.あまりきついとAパーツとの位置関係に捻れが出てしまうと考えられる
- 筒状のワークを印刷すると内径面にシームが形成され,ハンダごてを入れるとシーム部では内径が小さくなるため,安定してはまらない.そういう場合はリューターでシーム部を削って調整していたが,今回はZシーム合わせという方法があることを学んだので試してみた.ただしスライサーがCURAあるいは ”CURA系”のお話しである.当然他のスライサーにも同じ機能がある.想定通りのシームレスの造形結果を得られた
- こちらのサイトを参考にさせて頂いた.分かりやすく素晴らしい解説である
- Aパーツと連結・固定する100mm長 φ4mmステンレスラウンドロッドを挿入する穴を造形する.Aパーツと同様である.挿入する長さ(深さ)を正確にするため貫通させない.1mmの厚さで”底壁”を残してある.PLAは圧縮強度はそこそこあるので,ロッドを叩き込んでも定位置で止まるはずである
- AパーツとBパーツを連結する時,捻れないように出来るだけ長い穴を造形した.ロッドがきついと組立て時に力が入って捻れそうなので要注意である
- ボア(外径)12mmのリニアベアリングを固定するための,内径12mmの穴を造形する.Aパーツのリニアベアリングと,Bパーツのリニアベアリング両方にφ6mmラウンドステンレスロッドが貫通する.さらに反対側にもリニアベアリング&ラウンドステンレスロッドが配置されるので,ハンダごて固定部の中心軸とリニアベアリングの中心は完全に平行である必要がある
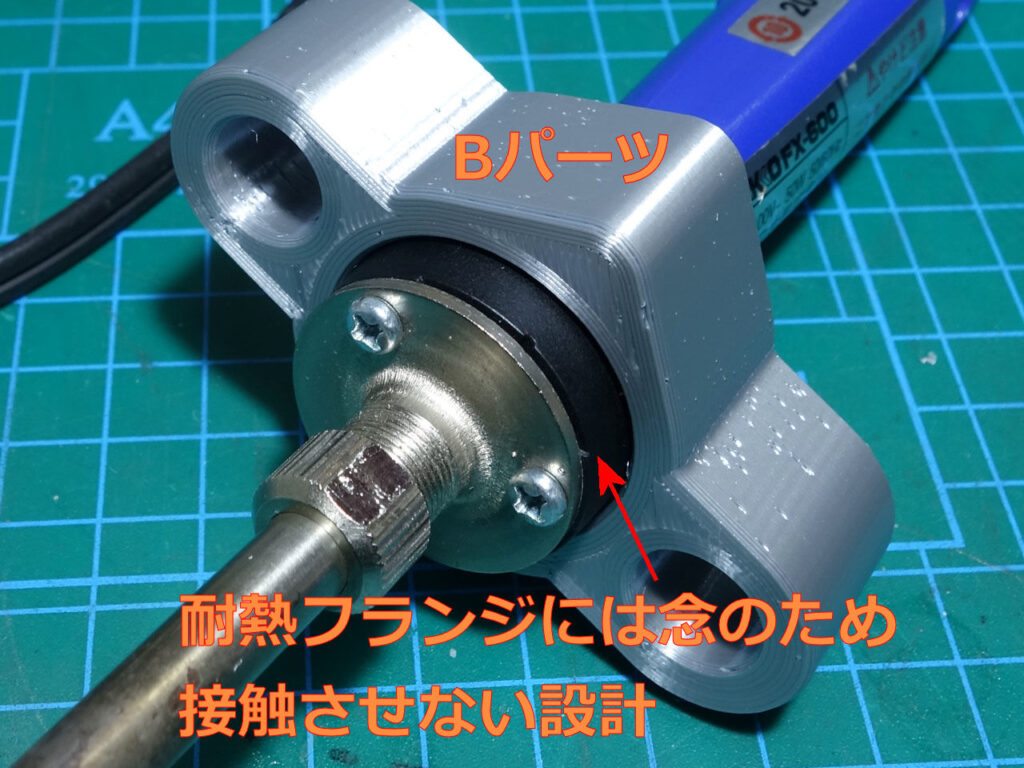
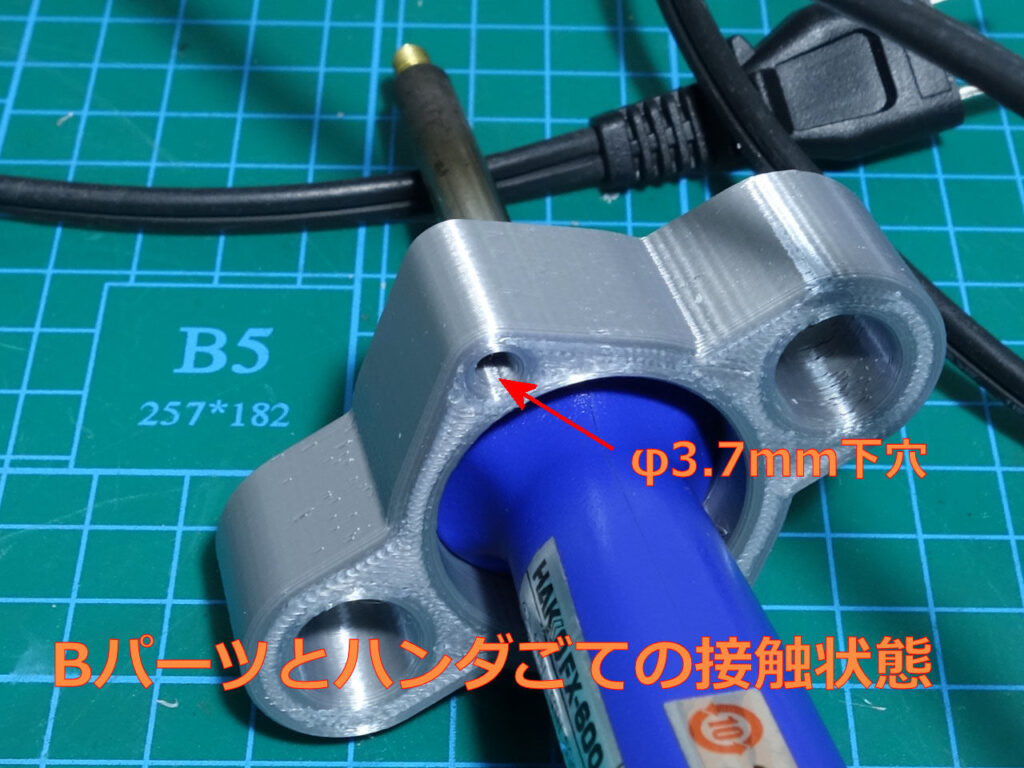
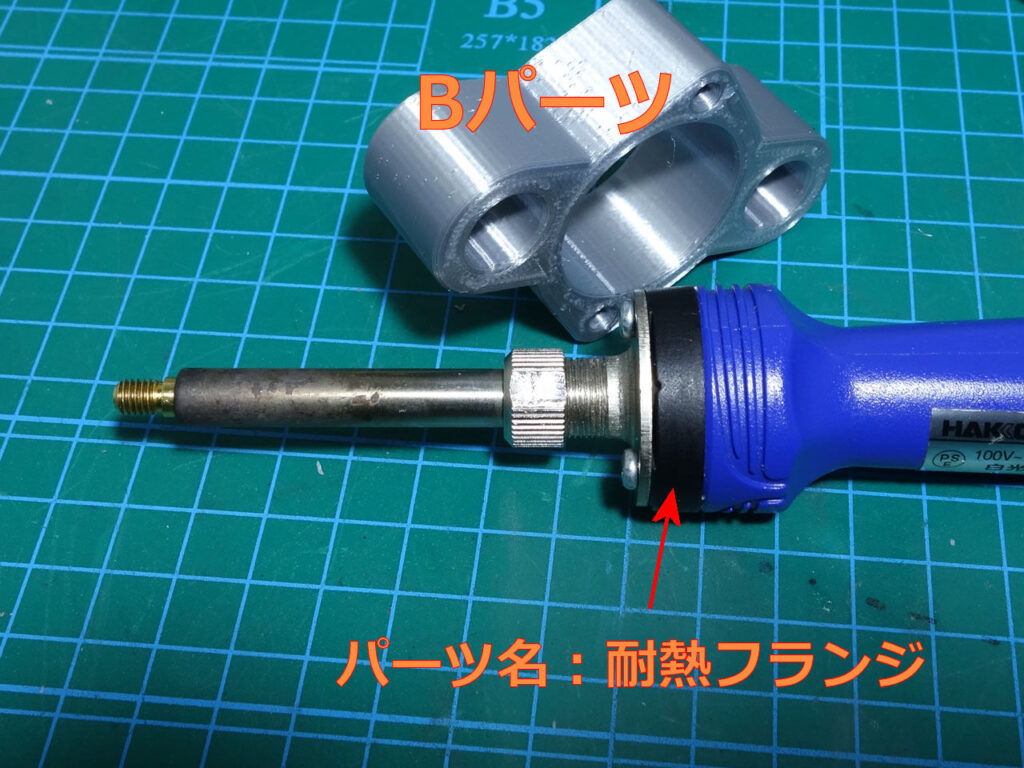
- ワーク上面に置いて,ハンダごてを垂直にサポートする部分で,Cパーツと呼ぶことにする.Cパーツは2種類製作した
- このパーツをデザインするにあたって考慮すべき点は多かった.まずは大きさをどうするかである.当然大きければ(広ければ)安定するが”ハンディー”でなくなってしまう
- まずは適当なサイズで作って使って修正することにする.デザイン変更は容易である
- 垂直にハンダごてをサポートし,かつスムーズに上下スライドさせる機構を考えてみた.一番簡単なのは,Aパーツ,Bパーツに同軸上の貫通穴を造形し,Cパーツに取り付けたロッドに通すというもの.この方法だとガタが避けられない.ロッドと貫通穴は摩擦があるため穴を大きめにあける必要がある.PLAとステンレスにおいてこの接触関係で摩擦は結構大きい.PLAに“粘り”があるためである.オイルやグリスはあまり効果はない
- そこでBパーツにリニアベアリングを付けて,Cパーツからのロッドを通す機構とすることにした.リニアベアリングとステンレスロッドはAmazonで入手できる.バリエーションも豊富である.前述の通り最初の商品は粗悪品であったが,次はまあまあ使えるものであったので予定通りプロジェクトを進める
- φ6mmのステンレスロッドの直径をマイクロメーターで実測してみた.わずかに小さい5.972mmであった.試作版でほんの少しガタ?ブレ?がある気がする.そんなにこだわる必要はないとはわかっているが,気になり出すと止まらない.金属削り出しのパーツならこだわる意味もあるが,PLAで作っている以上剛性不足は自明であるのであまりこだわるのは無意味だと思う.しかしAliexpressをみていたら公差Gと明記されているステンレスロッドが見つけてしまった.両方のロッドで2種類のCパーツを組んでみようと思う
- 2種類のうち一つは,インサートナットチップをCパーツの中心にセットするタイプである.中央にφ30mmの穴が開いている.圧入するワークの表面が平坦な場合有効である.Cパーツ基底面の一部が安定してのせることができればよく,全面接する必要はない.あくまでガイドとして使用する
- ここで穴加工について触れておくことにする.どんなに試行錯誤で印刷しても,ロッドと穴のはめあい具合を理想的な状態で安定して得ることは困難である.はめあい具合を左右するパラメータが多いからである.例えばロッドの外径,PLAの状態(製品,乾燥具合,ビルドプレートやノズルの温度,スライサーの水平穴精度)などなど沢山ある
- そこで専用工具が必要となるが,別の方法で製作することにする.今回使用したロッドの外径は4mm,6mmのものである.このサイズのドリル刃は容易に入手できるので,小さめに穴を造形して,ドリルで穴を修正するという方法をである.しかしやってみるてわかったが,ドリルの刃が粘りつく感じで良い感じではなかった.ツイストドリルなので仕方がない.ちなみに,PLA造形物のツイストドリルでの穴修正は,手回しで行う必要がある.ボール盤は絶対に使ってはいけない.摩擦熱でPLAが溶けてしまうのた.経験談^^;
- それでも使えないことはないのだが,穴をきれいに(真円に)加工するといえばリーマである.Amazonでなんともお買い得なリーマセットがあったので早速購入した.4 mm 6 mm 8 mm 10 mm 12 mm 5個セットである.今回のプロジェクトで使用する4 mm 6 mm 12 mmの3種類が含まれている.今後のDIYにも絶対に役立つはずである
- 以上穴あけに関してはA,B,Cパーツともに適用される
- もう一つは,インサートチップをCパーツのステンレスラウンドロッドの間ではあるが,ベースプレートの外側にセットするタイプのもの.この形態だと,Cパーツのベースプレートの下に物を置いて高さを調整すれば,ワークのインサートナットへのアクセスの自由度が増してくる.ベースプレート下面よりも下方に配置したインサートナットの圧入も可能になる
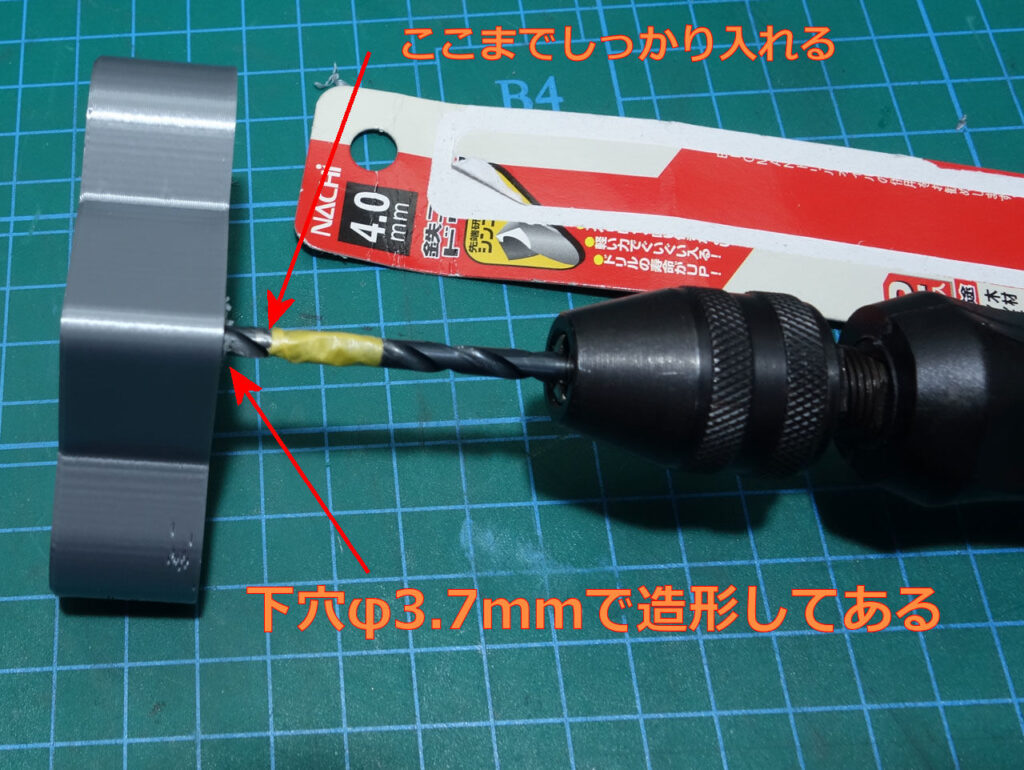
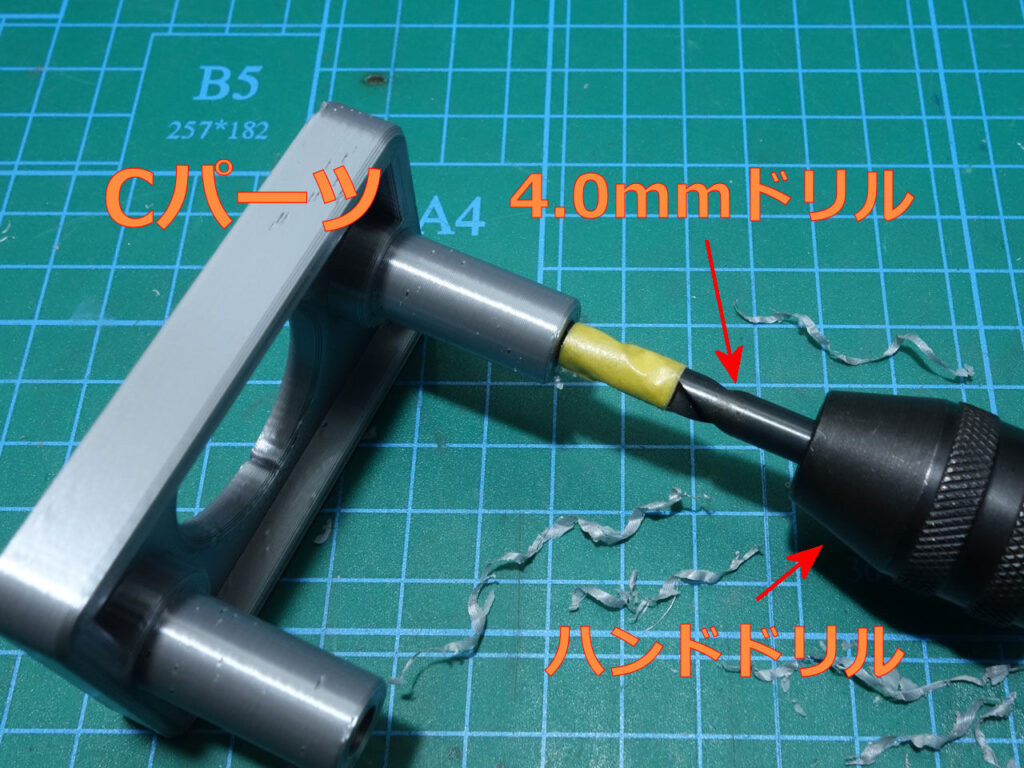
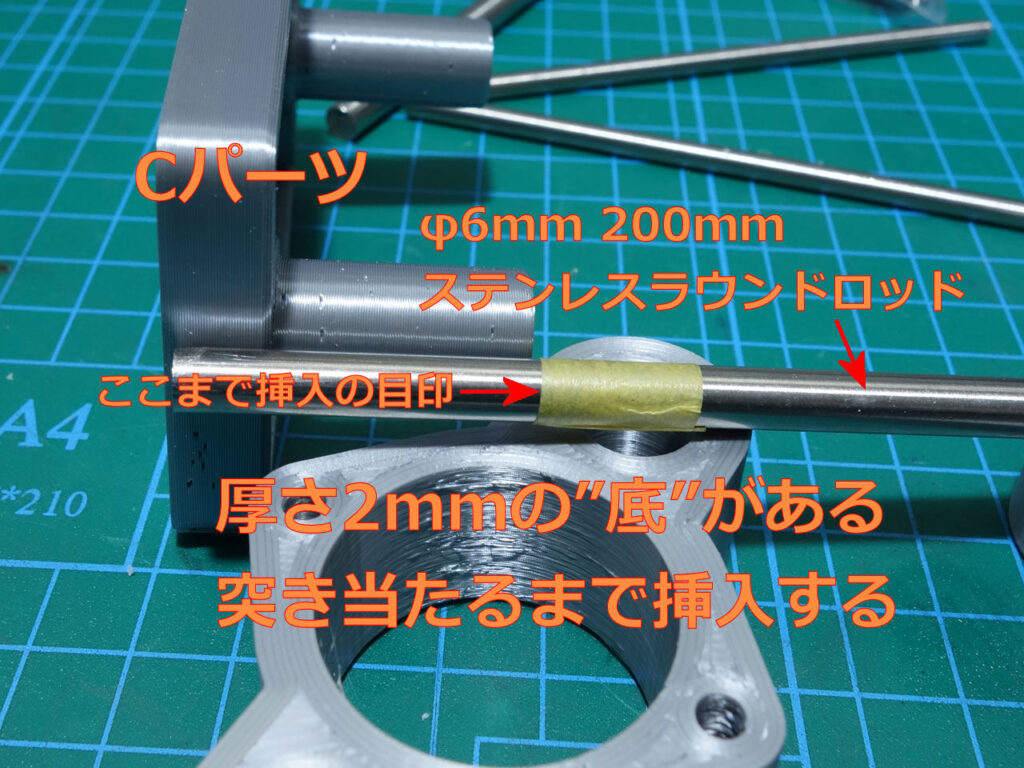
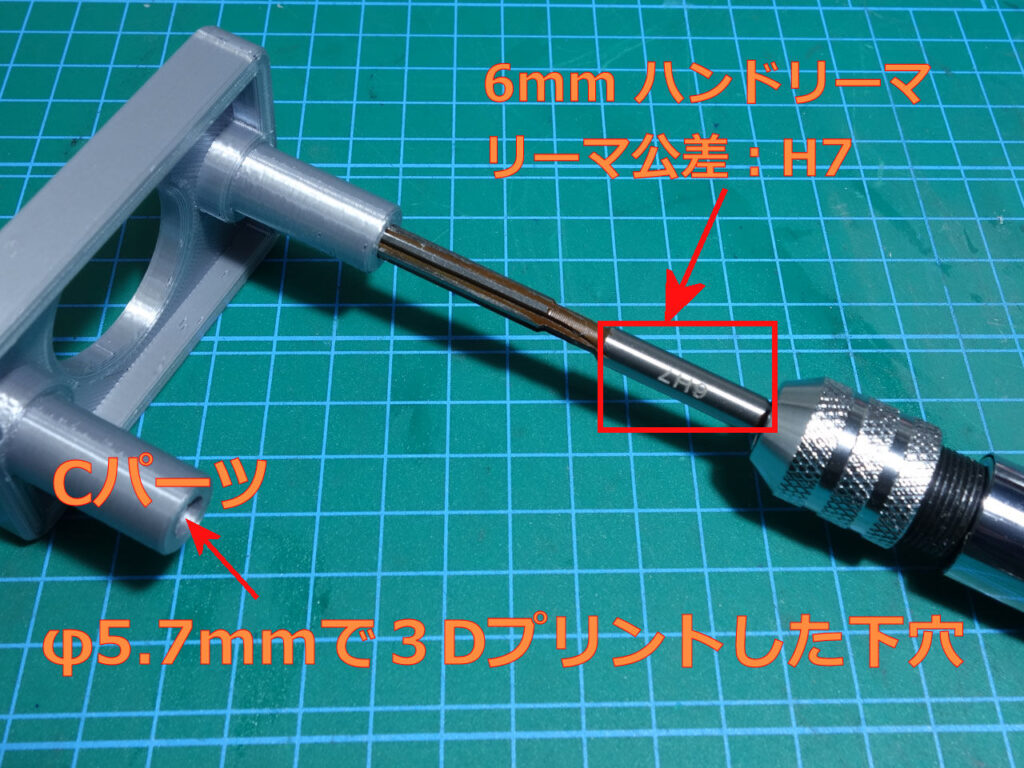
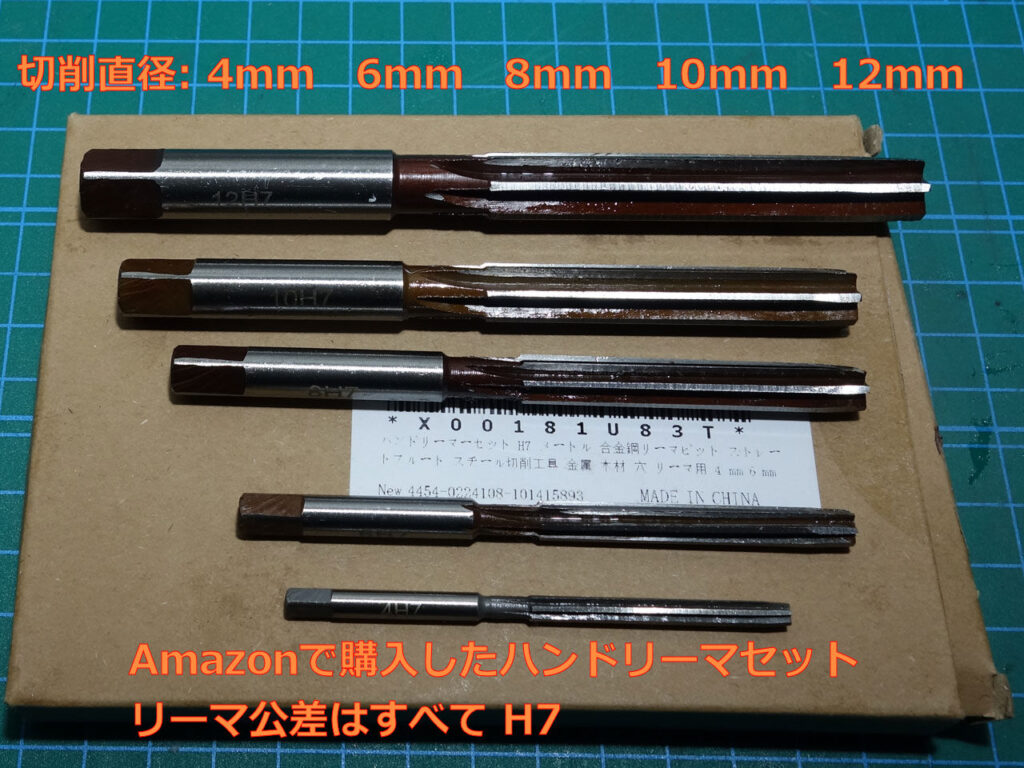
- AパーツとBパーツを連結するときに,捻れていないかをチェックするために治具を製作した.名パーツとは点(直線)で接するようにするた円弧状(断面が)とした.使用前に裏返して平面に置いた状態でガタがないことを確認した
- もっとお安いインサートチップセットはあったのだが,サイズの刻印がかっこよかったのでこれを購入.絶対なくしそうなので専用のスタンドを製作した
- ワークに置いたインサートナットと圧入用チップの位置付けを容易にするため,双方をできるだけ近づけてCパーツの位置を決定する必要がある.この時垂直的な位置を決たらその高さでA・Bパーツを固定できれば便利である.そのためのストッパー(位置固定)を製作した
- 圧入用チップの先端1mmぐらいならインサートナットに差し込んで置いても,PLAが軟化することはないので,その位置でストッパーを固定しても問題なかった
- 内径はφ6mmステンレスラウンドロッド径より大きくしてφ6.2mmで設計し,スライドさせやすくした.同径のドリルで整えた.固定用のネジはキャップボルトでもよかったのだが,何となくM4 12mmのローレットつまみネジを使ってみた.キャップボルトより頭部が長くて使いやすかった.ステンレスラウンドロッドに接するネジの底部は,点で接触するように調整された形態をしている.さすがに専用品である
- PLAは当然金属と比較してやわらかいので,スライドさせた時に引っかかりがでてスムーズに動いてくれない.そこでメタル製のφ6mmロッド用,長さ10mmのスペーサーをはめ込んだ.スライド動作はよくなった
- さらに反対側のロッドに入れて使うもう1つのストッパー(下限)も製作した.こちらはこれ以上降下させなくない位置にセットするものである.インサートナット上面をワークの上,面一,下と自由に設定できるので便利である
- 圧入後,圧入チップを上にスライドさせてナットから抜き抜くためのバネは,いろいろなパターンを用意したが結局下記の部材リストに載せた2種類となった.1本単独で使う場合,重ねて使う場合,ストッパーの位置を調整して使うことになる
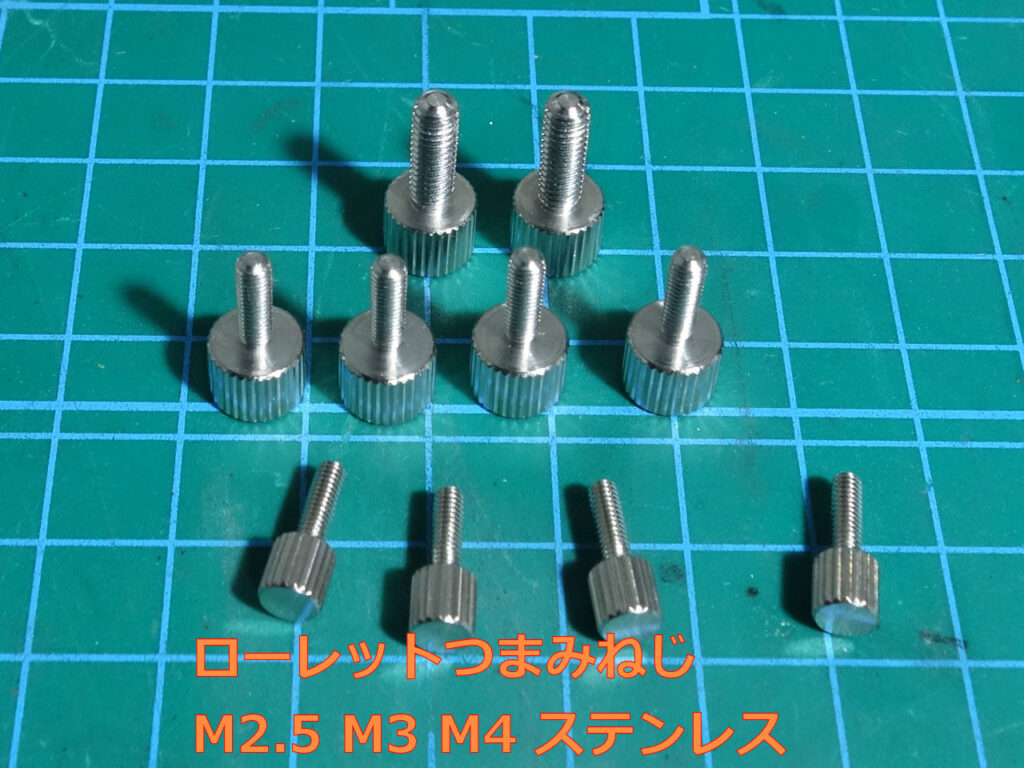
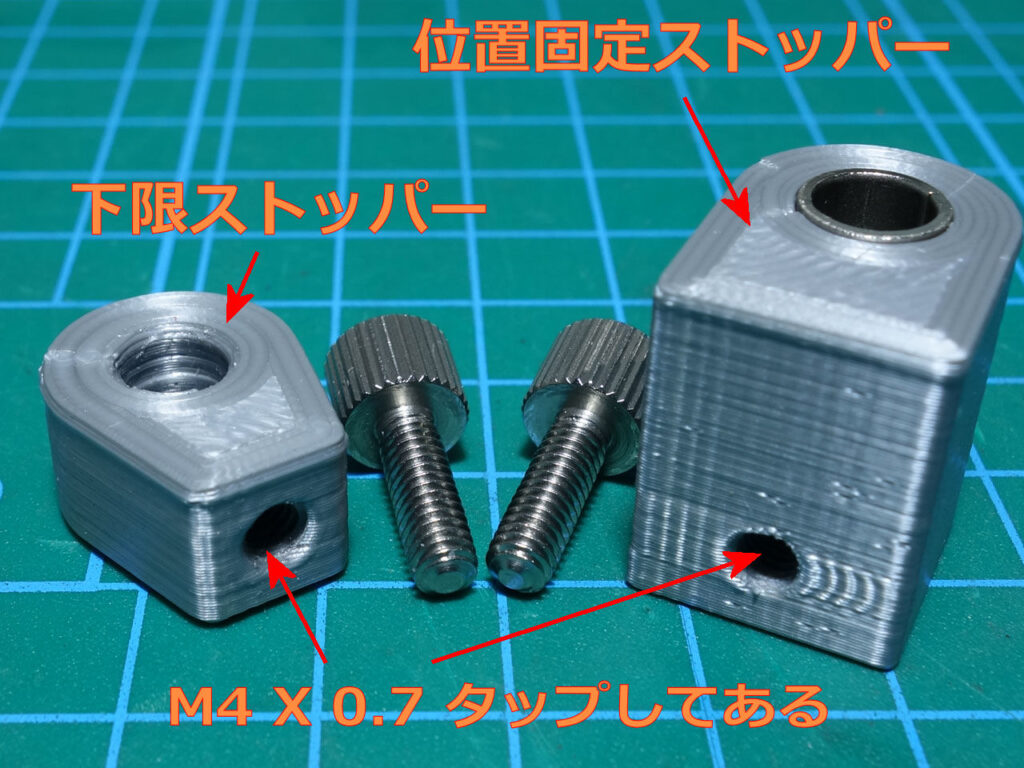
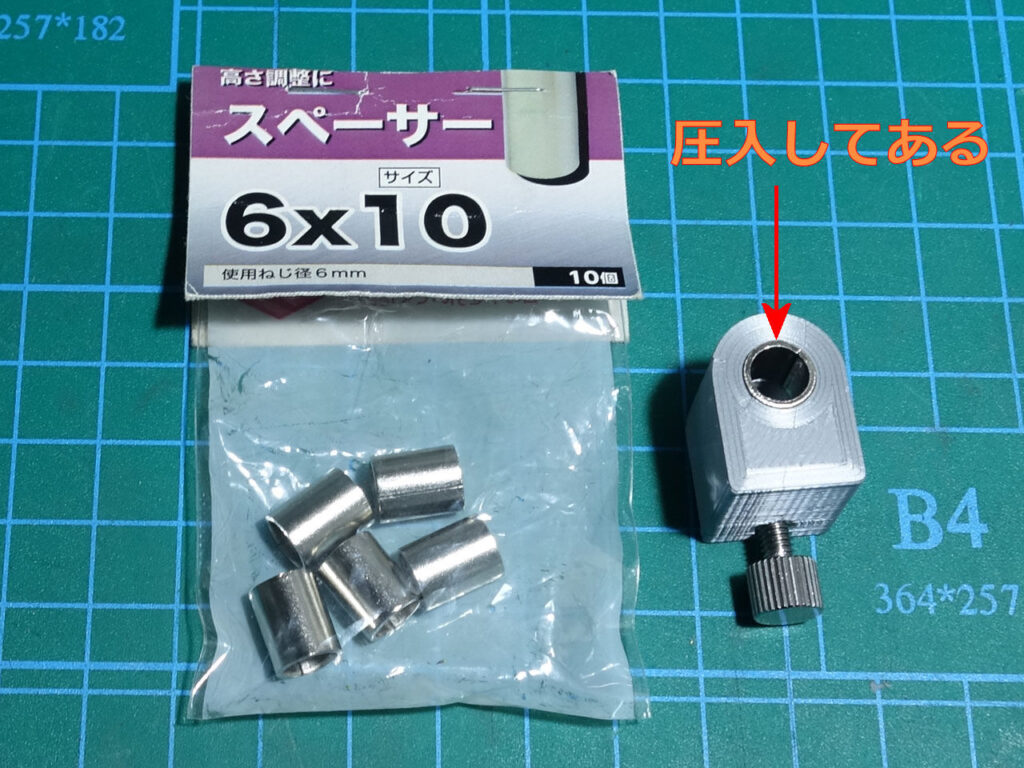
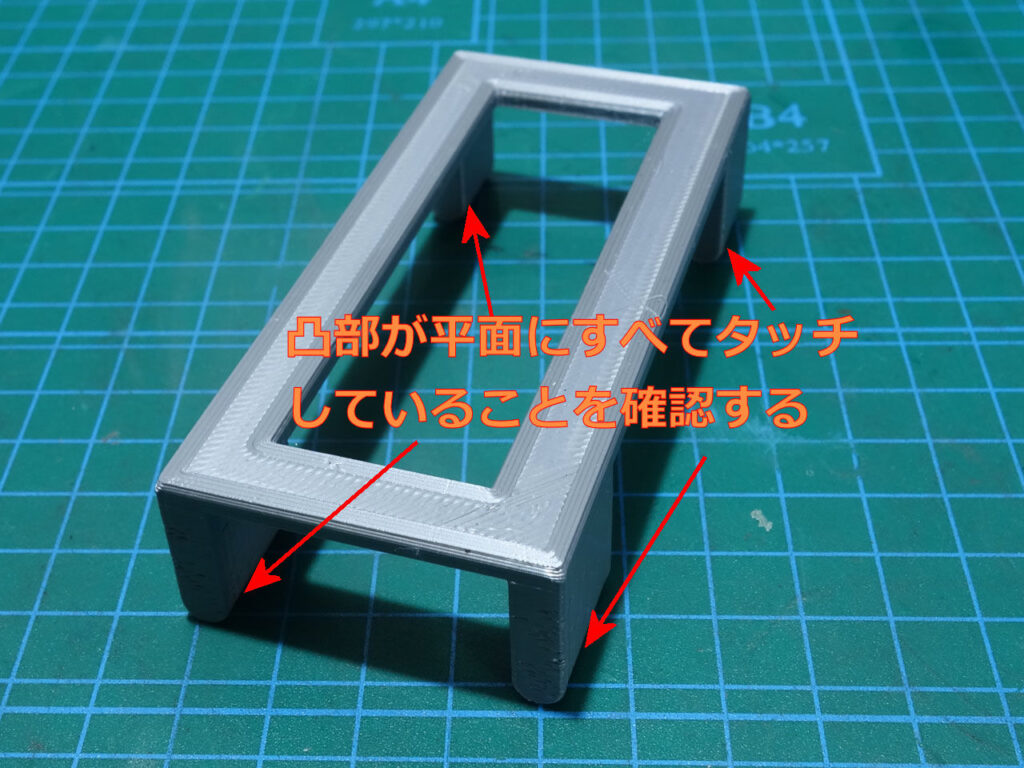
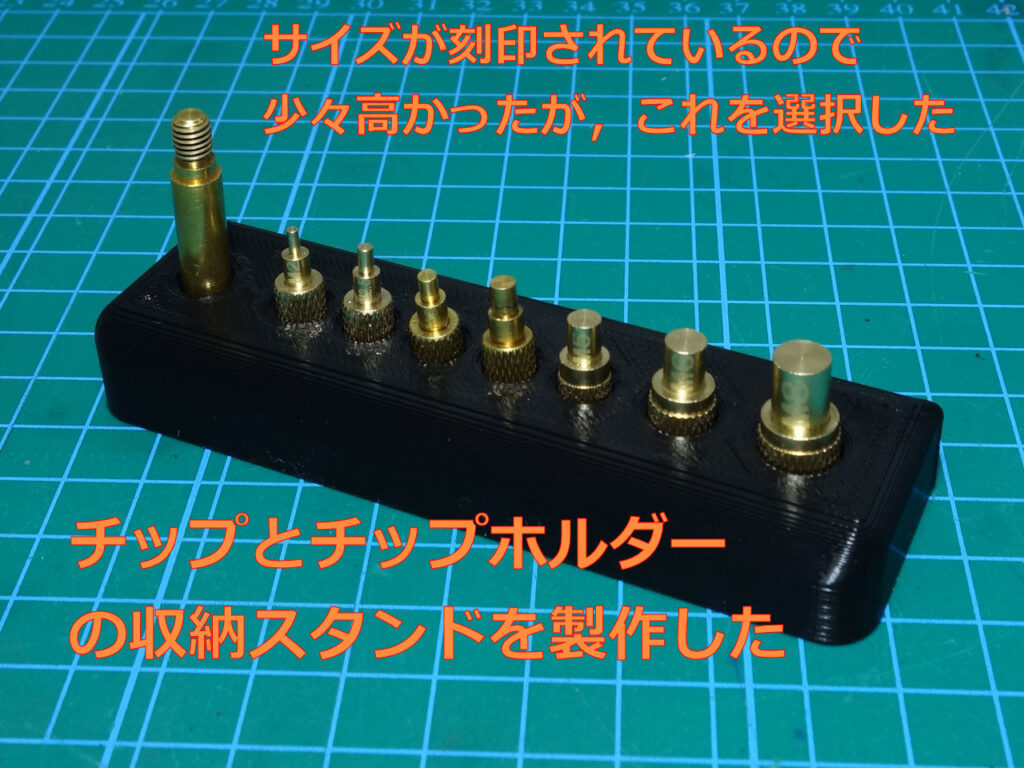
- まずはAパーツとBパーツの結合である.初めは外径φ4mm,内径3mmのアルミパイプを使用したが剛性が不足であったため,同サイズの真鍮パイプを使用した.これでやはりパイプということもありA,Bパーツを連結するとたわみが出たので,ステンレス丸棒とした.長さはアルミパイプの試作で100mmに決定していたので,Amazonでφ4mmで100mmのものをさがしたら見つかったので採用!
- φ4mm 100mmのステンレスラウンドロッドである.断端は面取りが必須である.少しでもバリがあれば,柔らかい素材であるPLAに食い込んで入らなくなってしまう.最初はφ4mm 60mm ダウエルピンが手元にあったのでこれを使おうと思っていたが,短かった.ダウエルピンであれば断端はラウンド加工や面取りされてきれいなのだが,そうでない丸棒の場合はほぼ切りっぱなしである
- 断端を面取りするのは以外に面倒で難しい.そこでnanoベルトサンダー用の治具を作った.面取りが任意の角度で行えるようなガイドを3Dプリンターで製作した.#320で削り,#1000 で研磨した.端面の平坦化にも有効.存外満足!
- よく使うφ4mm 5mm 6mm のラウンドロッドを対象としている.治具をnanoベルトサンダーのガイドテーブルにスプリングクランプで希望の角度をつけて固定する.滑らないように治具底面には0.5mm厚ゴムシートを貼り付けてある.ロッドを手で回転させてもいいのだが,電動ドライバーを使うと格段にきれいにできる.六角軸ドリルチャックを使いセットする.ベルトは下方に回転,ロッドの切削面は反対方向に動いていくような回転方向とするときれいにできる.結構熱くなるので,少しずつ行う
- 3Dプリンターの精度はあなどれない.かなりな精度で組み上げられる物ができる.造形された穴に入るところまで差し込んで,そこからは,レザークラフト用に購入したプレス機のALL-2000を使用して圧入した.ハンマーで叩き込んでもいいとは思うがせっかくなので使ってみた.圧入はスカッとして面白い
- 念のため組み上げ状態をチェックするための治具を作っておいた.その結果,わずかに捻れていることが判明した.手で修正して,重石をのせて(気休め)ネジロック剤で固定した.捻れを戻したのでロッドとパーツの穴にはわずかに隙間ができているはずなので,この嫌気性ネジロック剤を使ってみた.結果は良好である
- Aパーツ,Bパーツともに造形してあるリニアベアリング用の穴はシームレスとしたので内面に切り欠き(シームを強制的に作らせる凹部)はできてしまうが,内径は一定になるがやはりFDM方式なので積層痕が出来るので,滑らかではない.また糸引きもある.勿論と言っても過言ではないと思うが12mmぴったりではない
- そこでφ12mmのハンドリーマで修正した.精度としてH7なので十分過ぎると思う.ドリル切削用オイルをつけてゆっくりと内面を修正したのだが,PLAの場合オイルはない方が刃がしっかりPLAを引っ掻いてくれる.金属をリーミングする場合は必須なのであるが.公差についてはこちらのサイトがとても参考になった
- リニアベアリングの外径はわずかに12mmより小さいため,無理なく挿入できた.そしてφ6mmステンレスラウンドロッドを両ベアリング内に貫通させる.軸のズレもないようですんなりと通すことができた
- 再度治具にのせて,ロッドをスライドさせ,馴染んだところでリアベアリングとA,Bパーツとの隙間にネジロック剤のTL90Jを流し込む.プラスチック系には向かないと説明にあるが特に問題ない.PLAは石油由来ではないので勝手に大丈夫と思っている.サラサラの液状なので,毛管現象で吸い込まれていく感じ.問題出たら考えることにする
- Cパーツの組み立ては,φ6mmのステンレスラウンドロッドを挿入するだけなのだが,収納を考えてロッドはとりはずせるようにする.といってもハンドリーマで造形してある下穴を拡大・修正すればその状態となる.切削片が出なくなるまで,熱が出ないようゆっくりと回すだけである
- なお,強度確保のためベース部分の底部から2mmの所まで下穴は設計してあるので,同部までしっかりリーミングする.ツイストドリルの先端とちがってリーマは,フラットエンドであるので丁寧に回転させていればよい
- 初めは金属に使用する場合のように注油していたのだが,PLAは柔らかく粘りがあるので刃が滑って切削効率がわるく滑らかな切削面が得られないようである
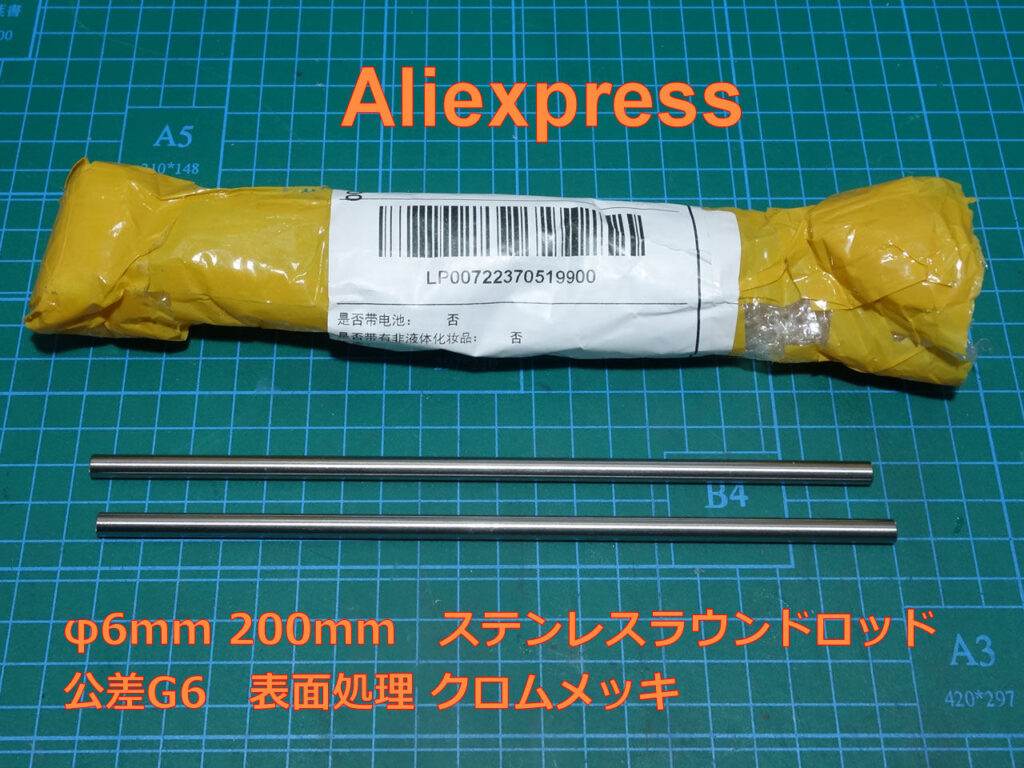
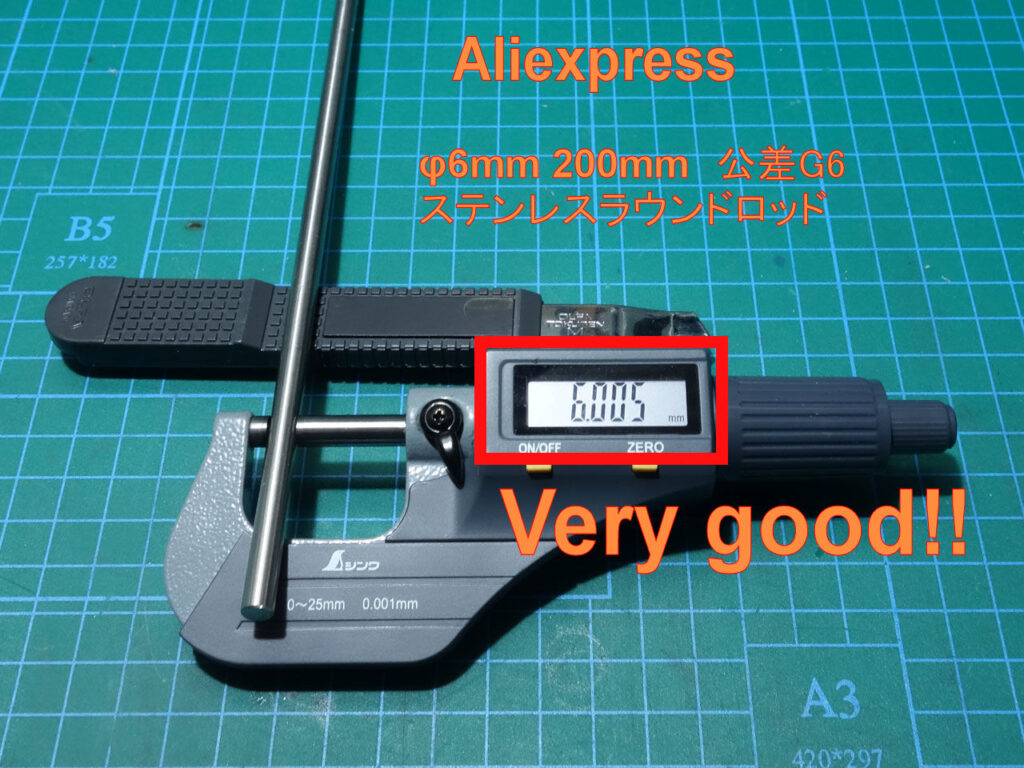
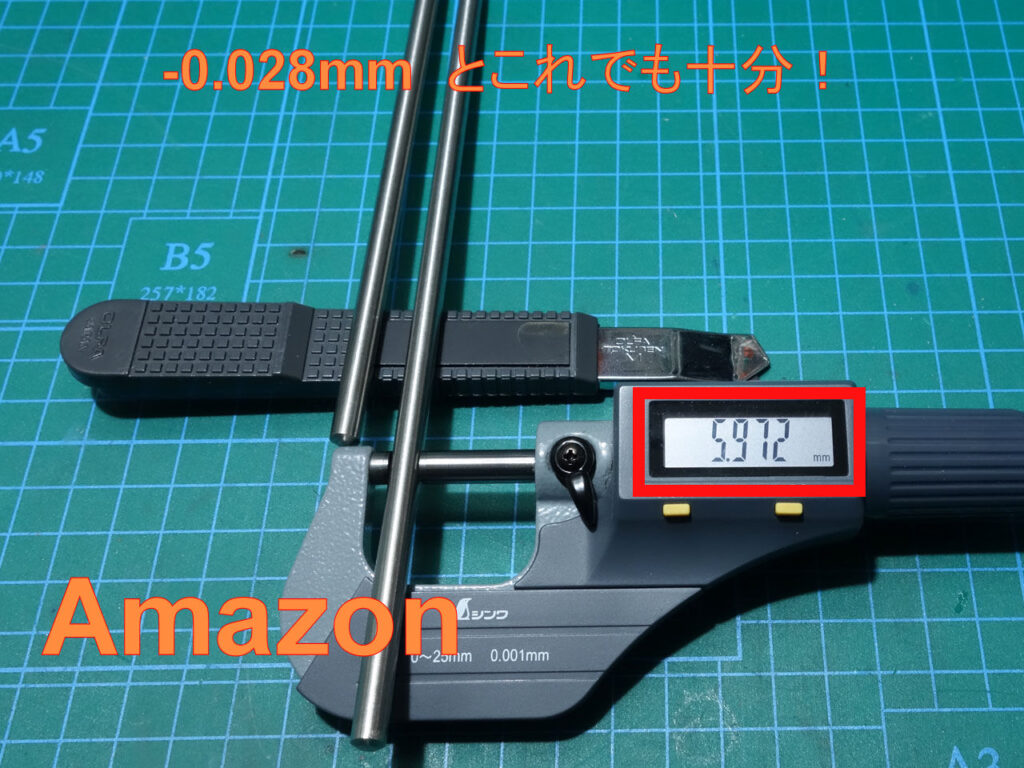
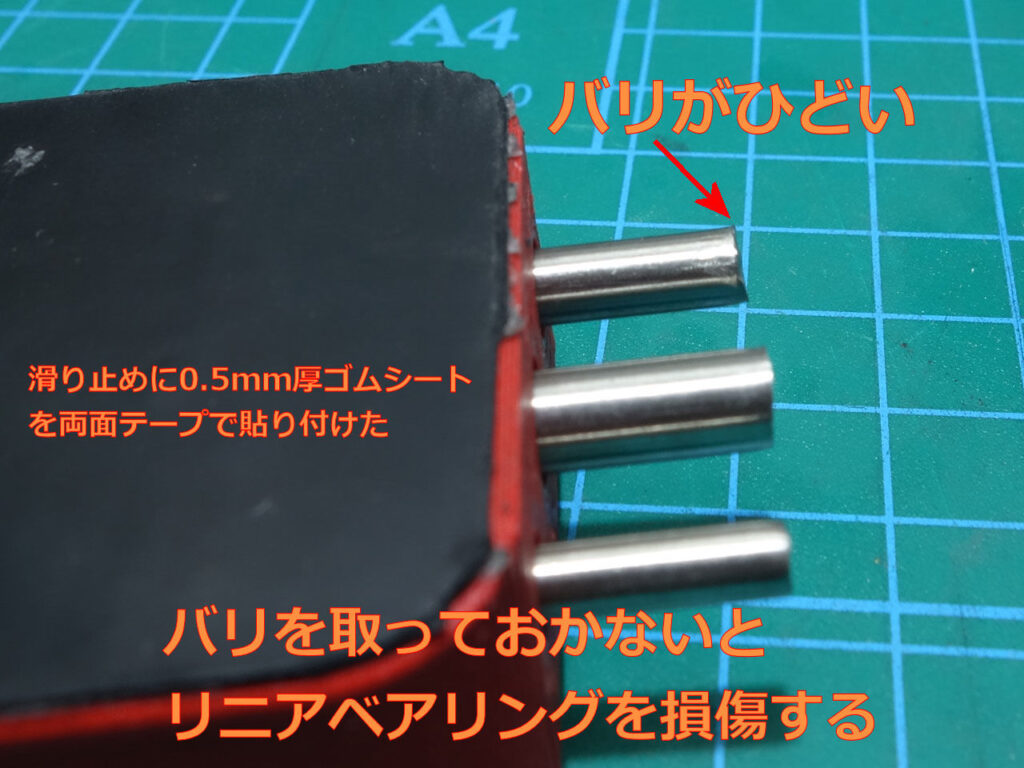
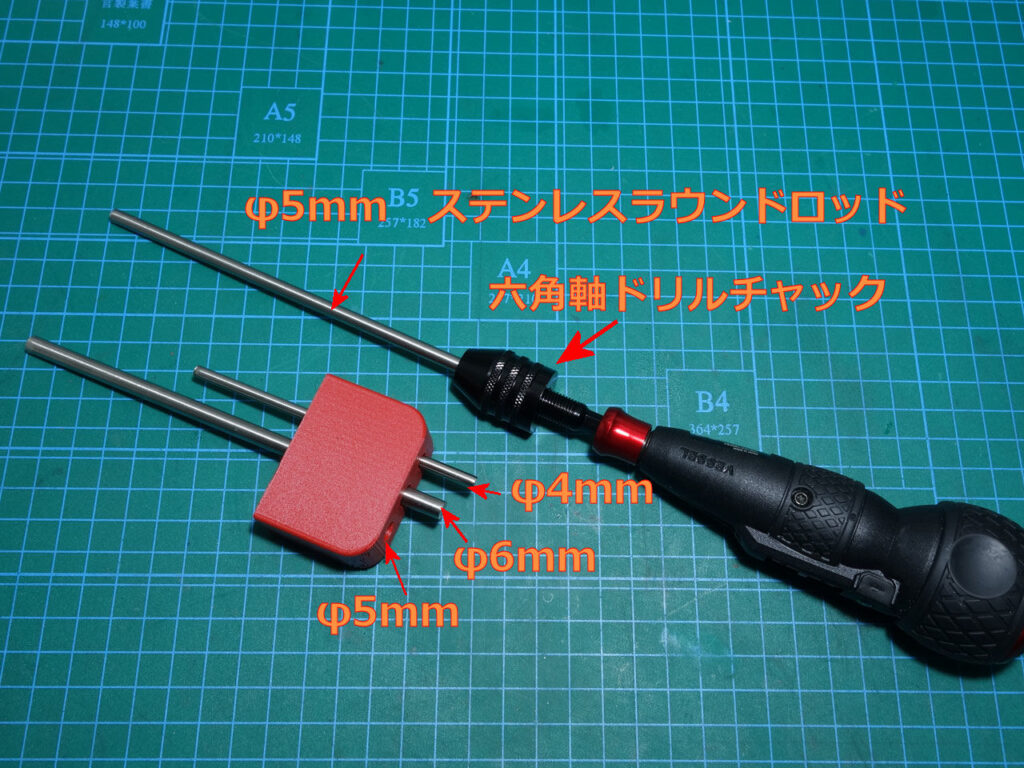
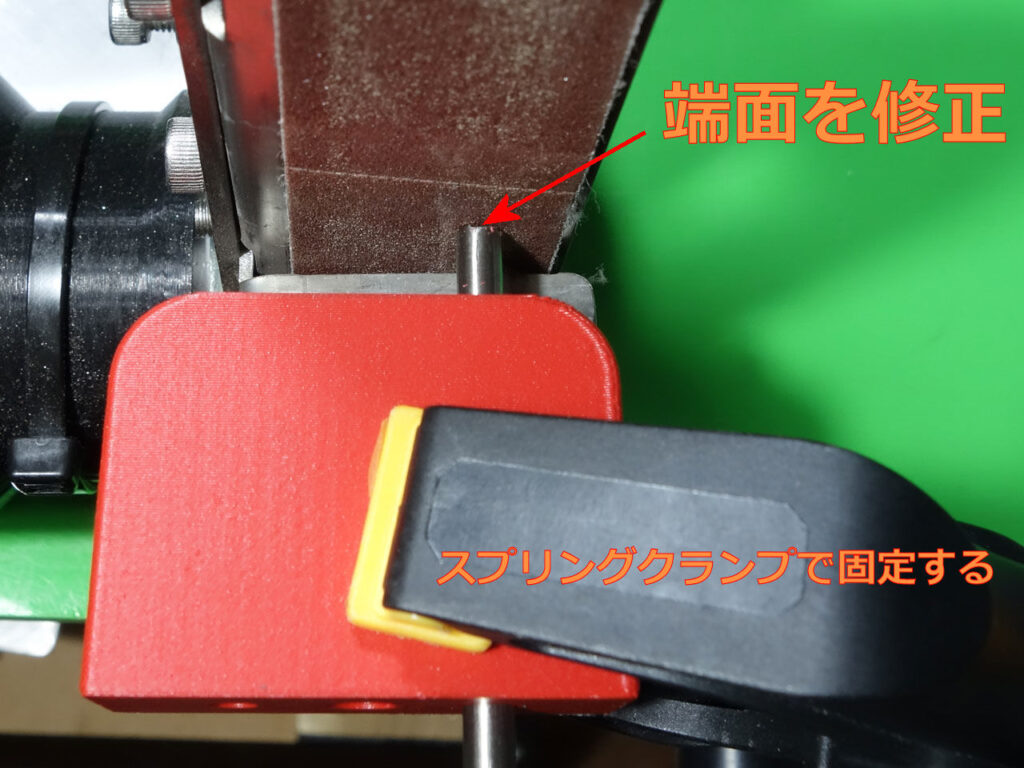
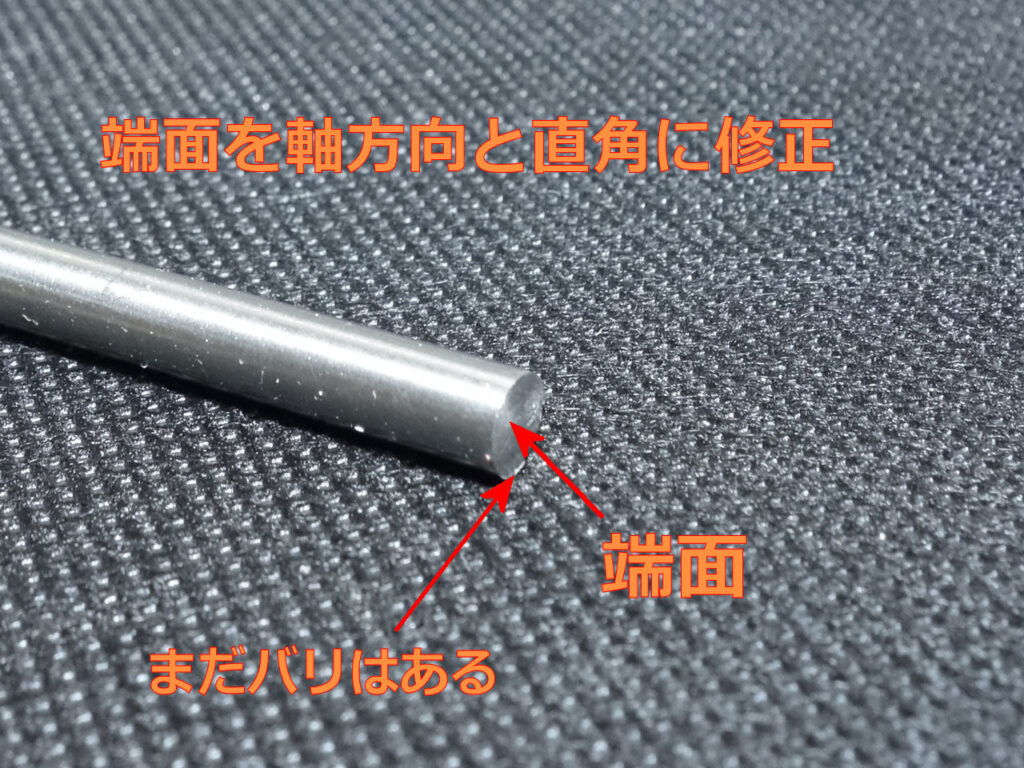
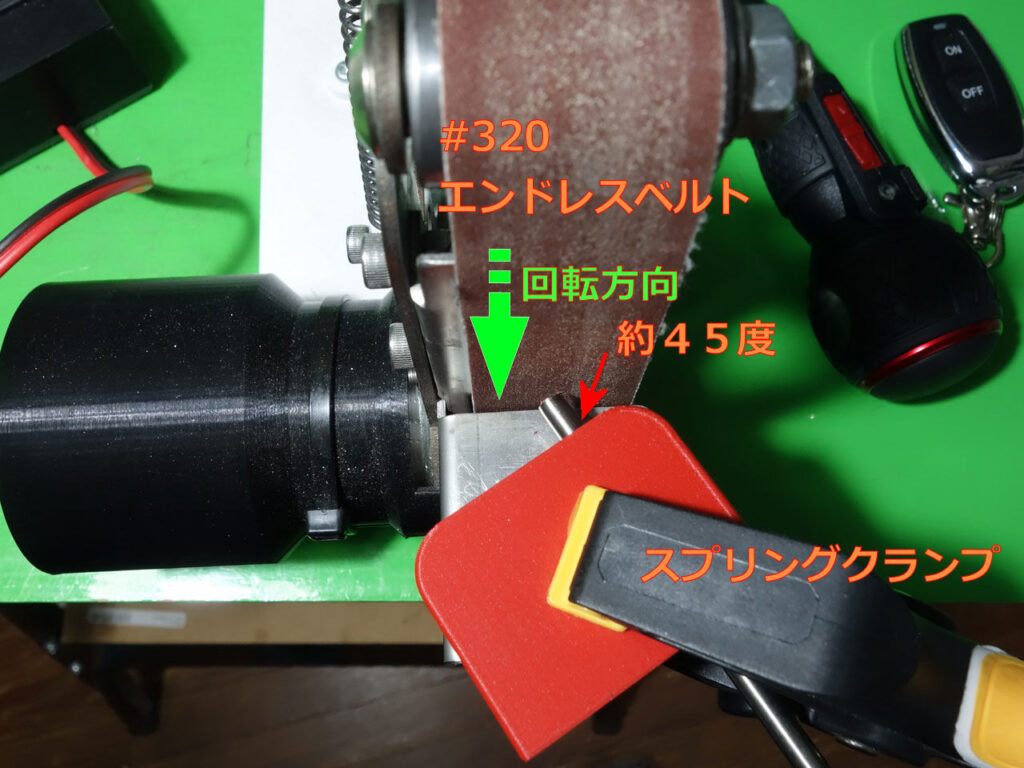
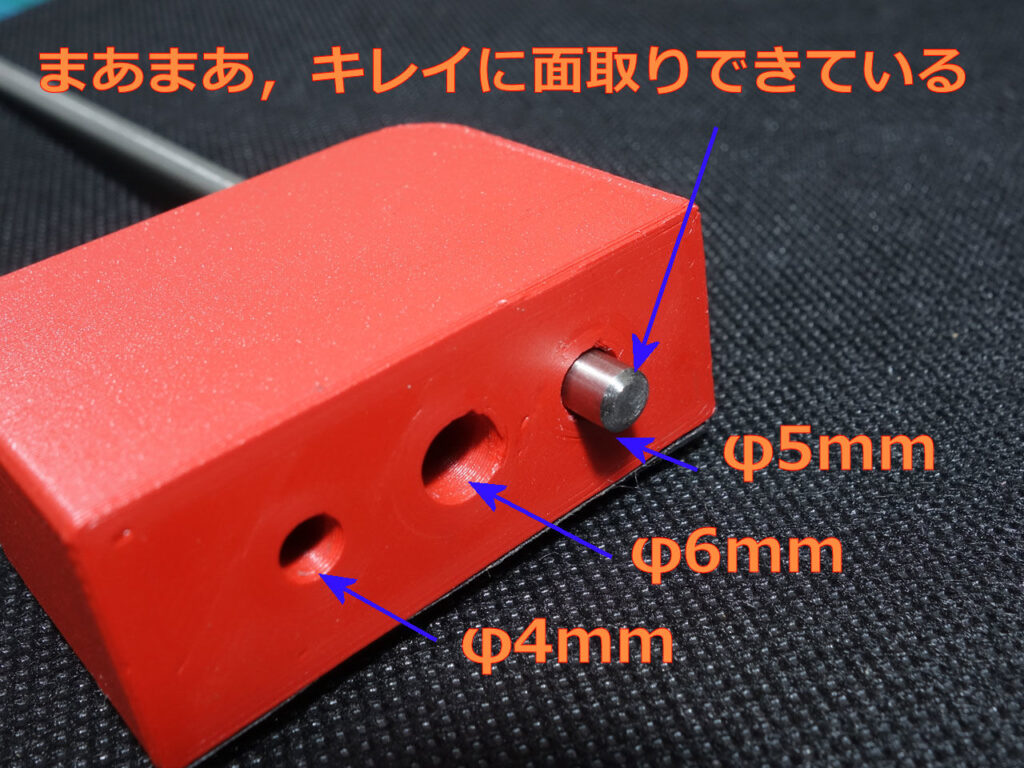
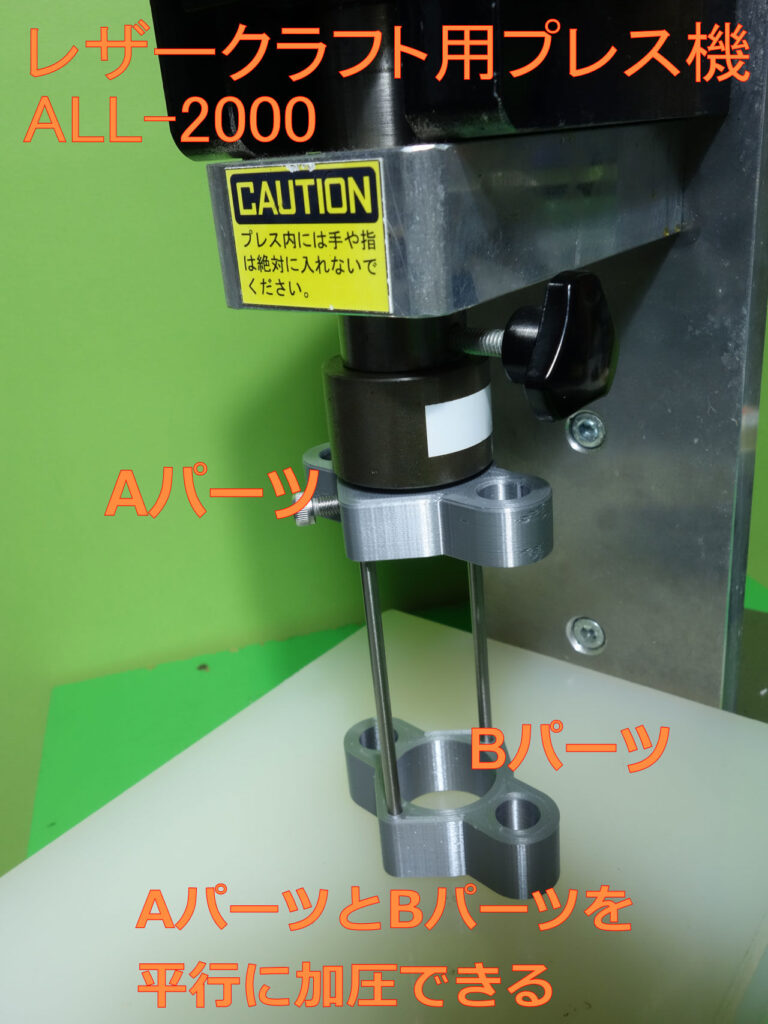
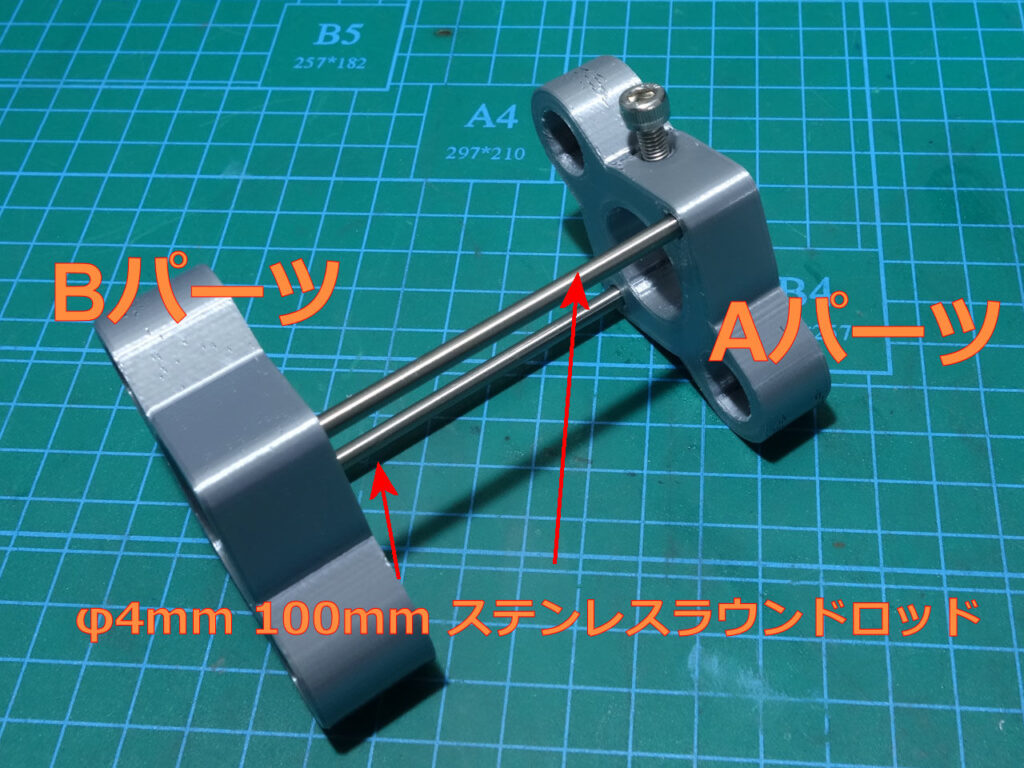
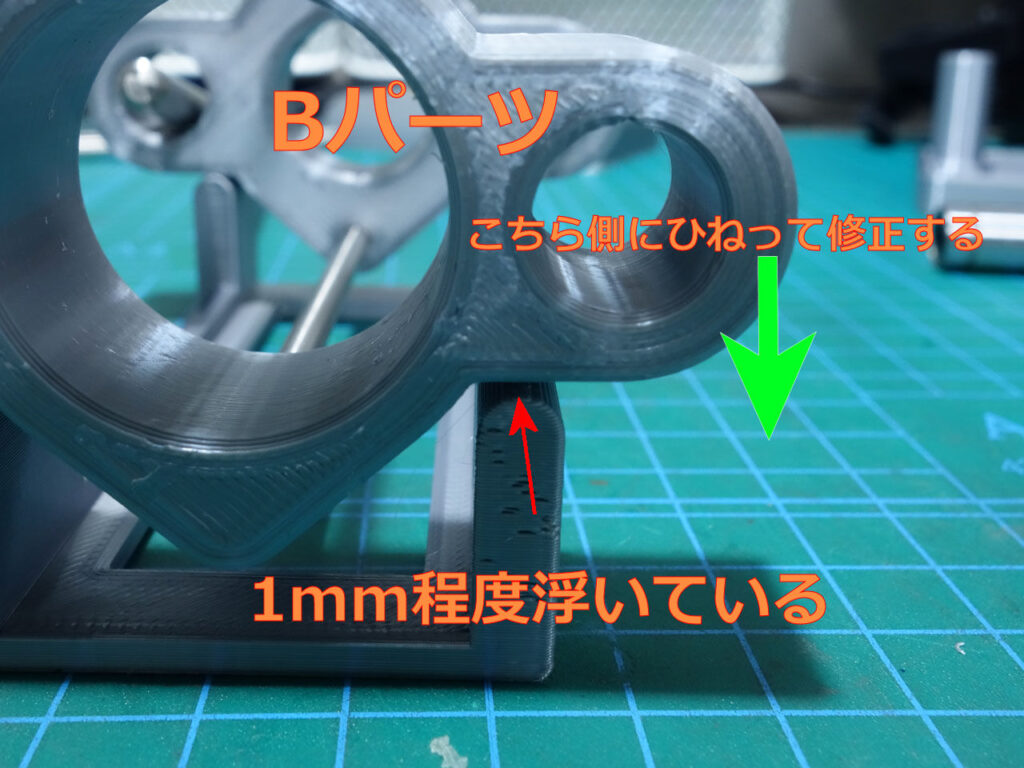
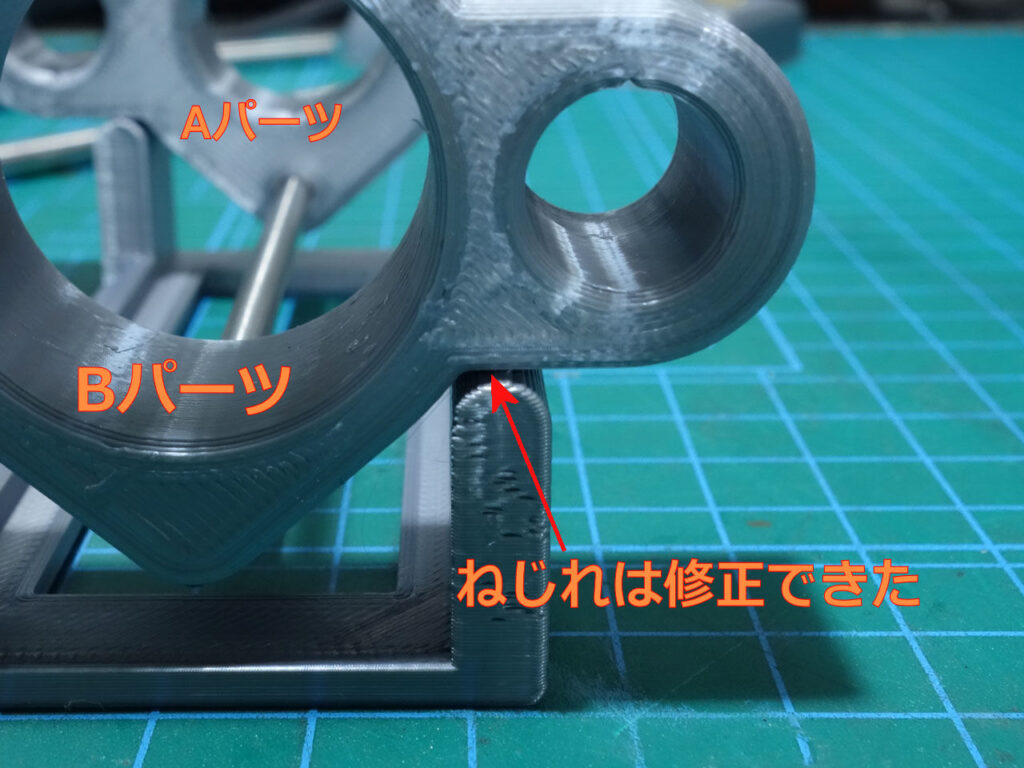
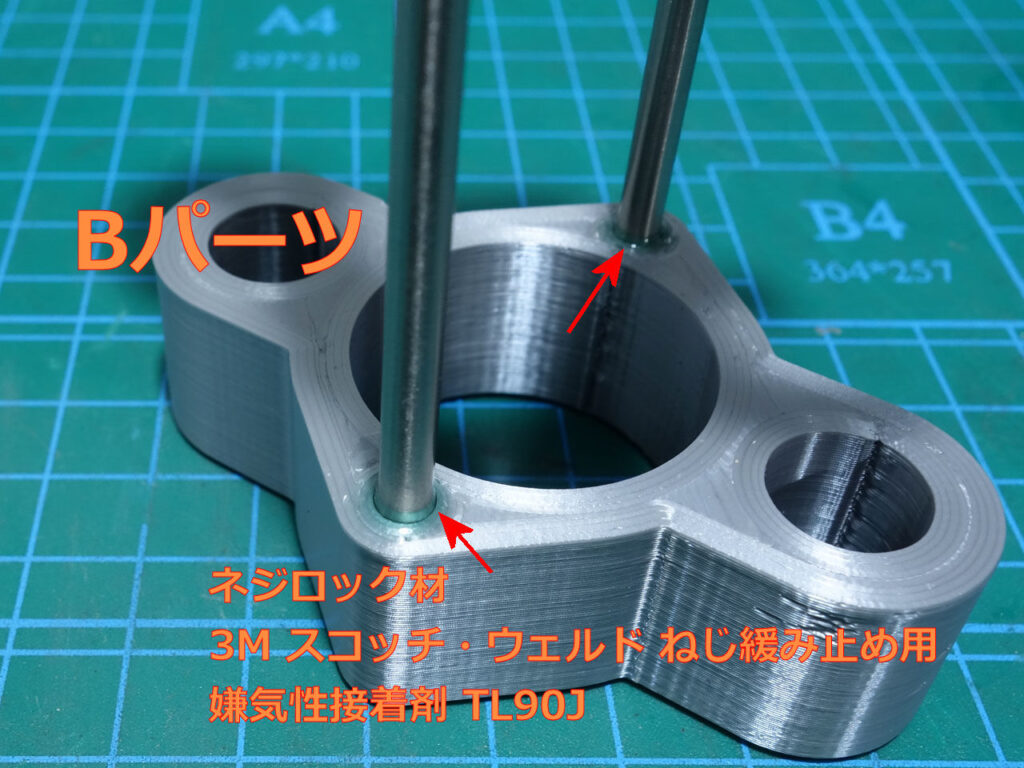
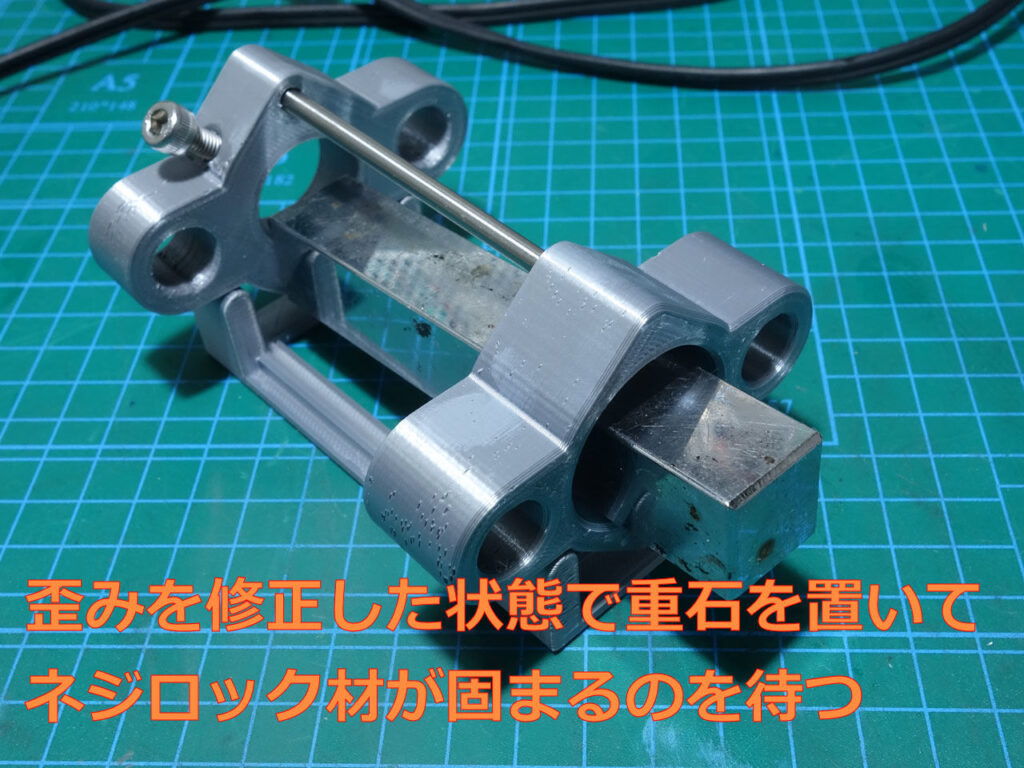
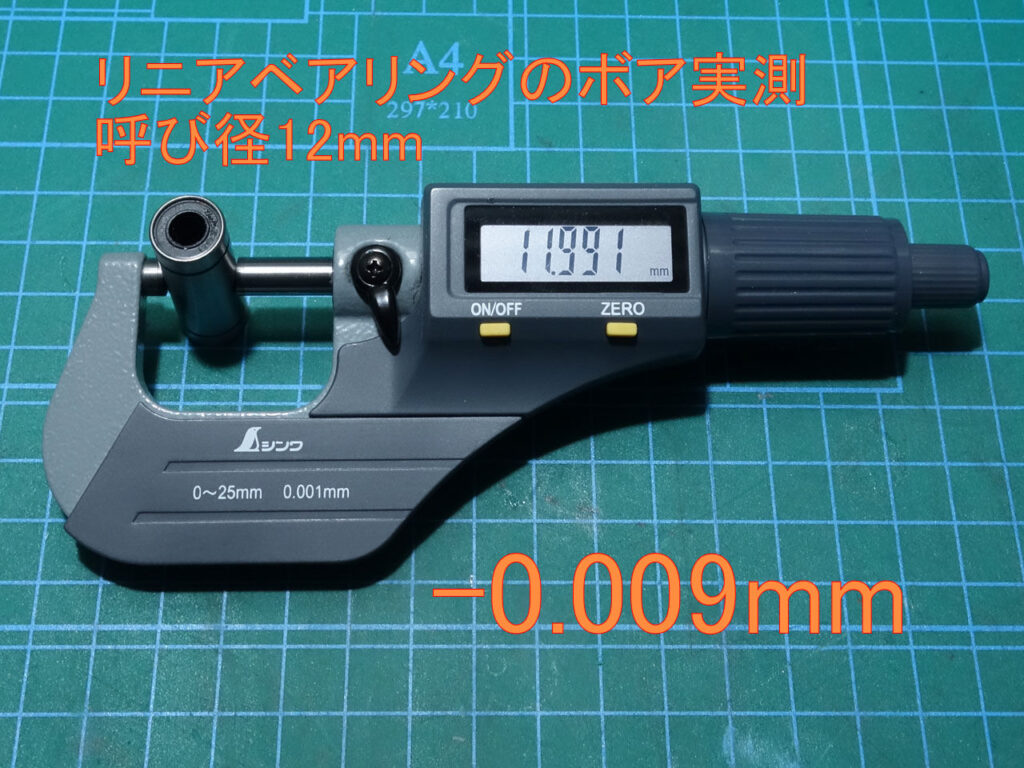
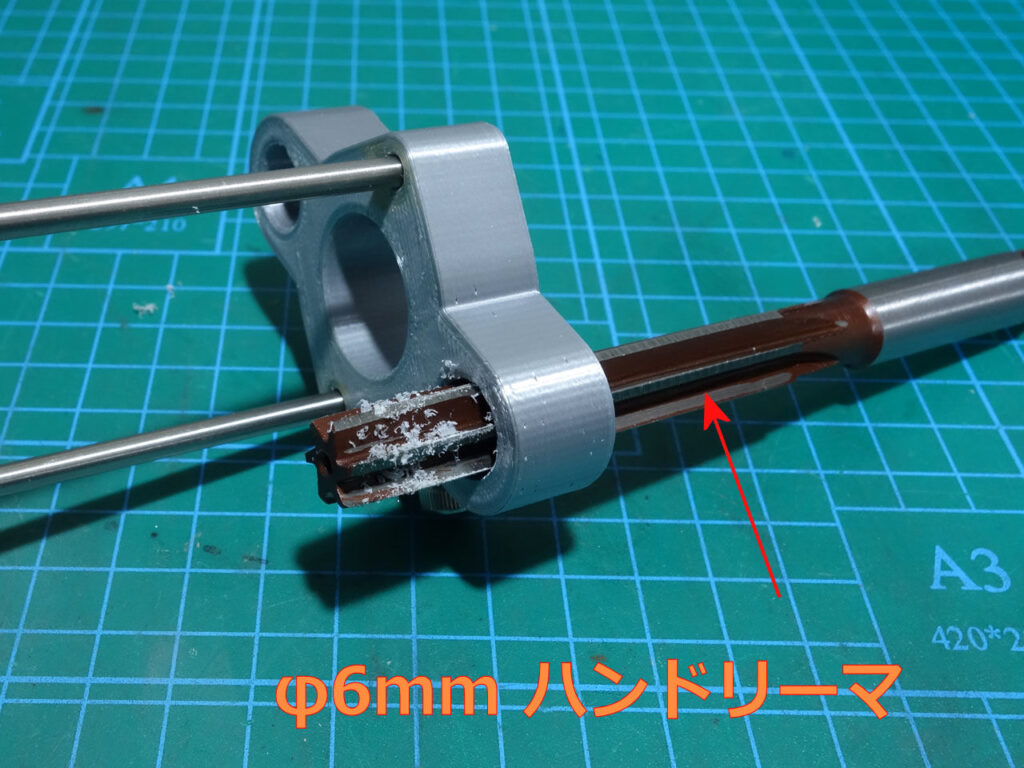
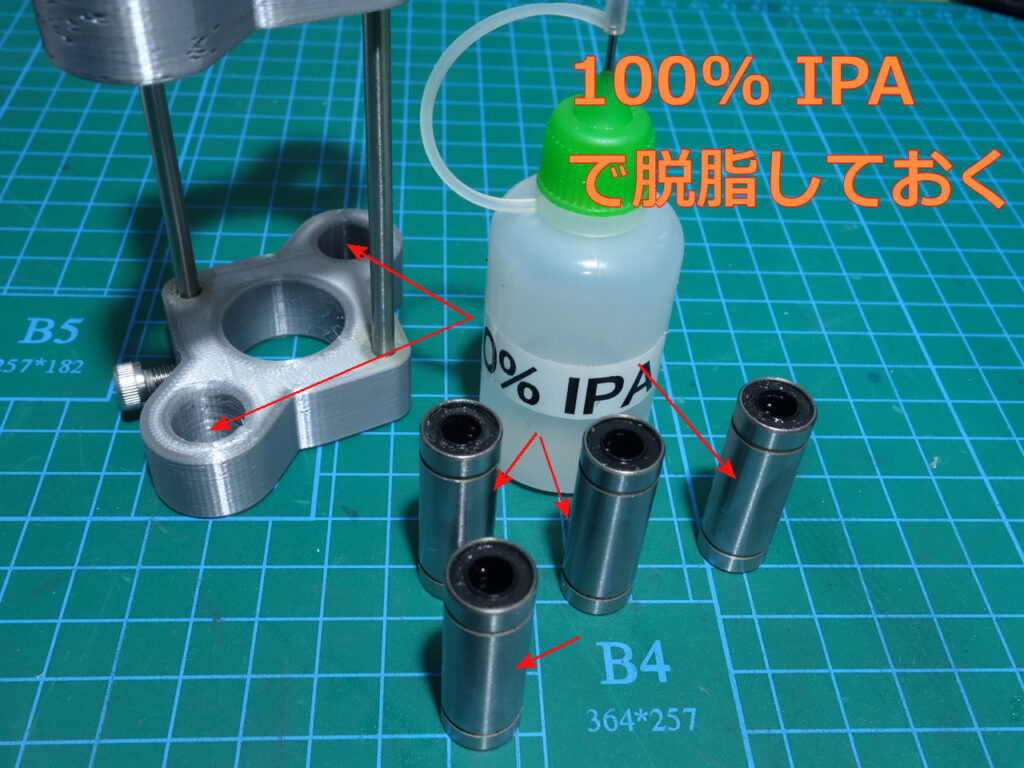
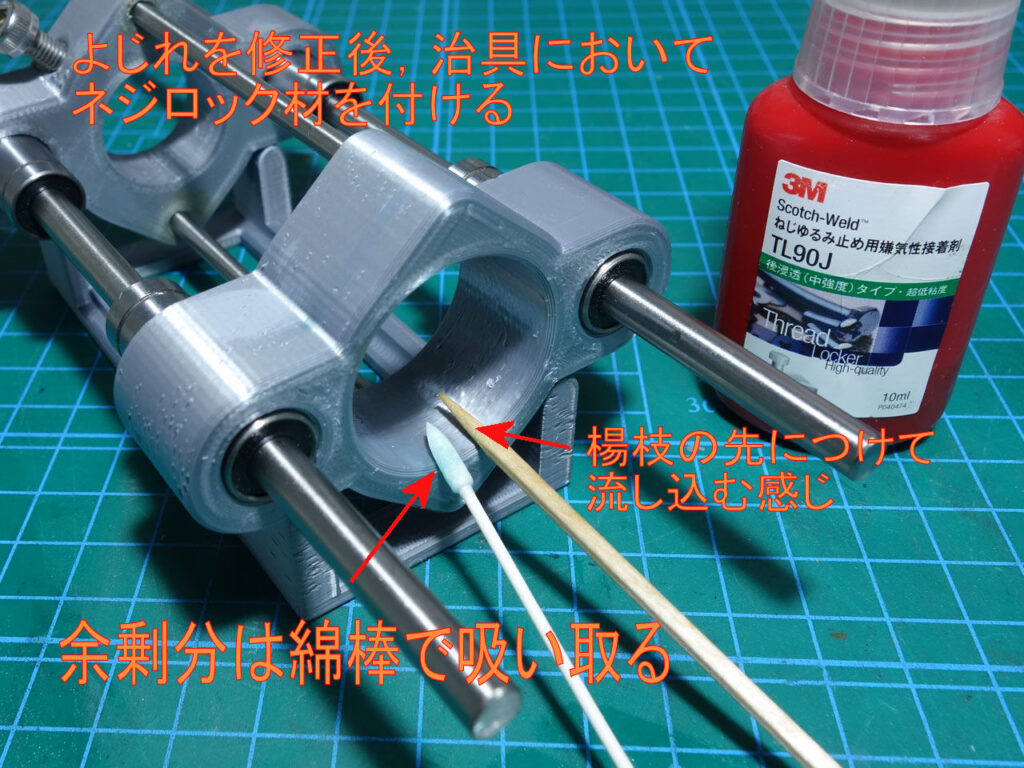
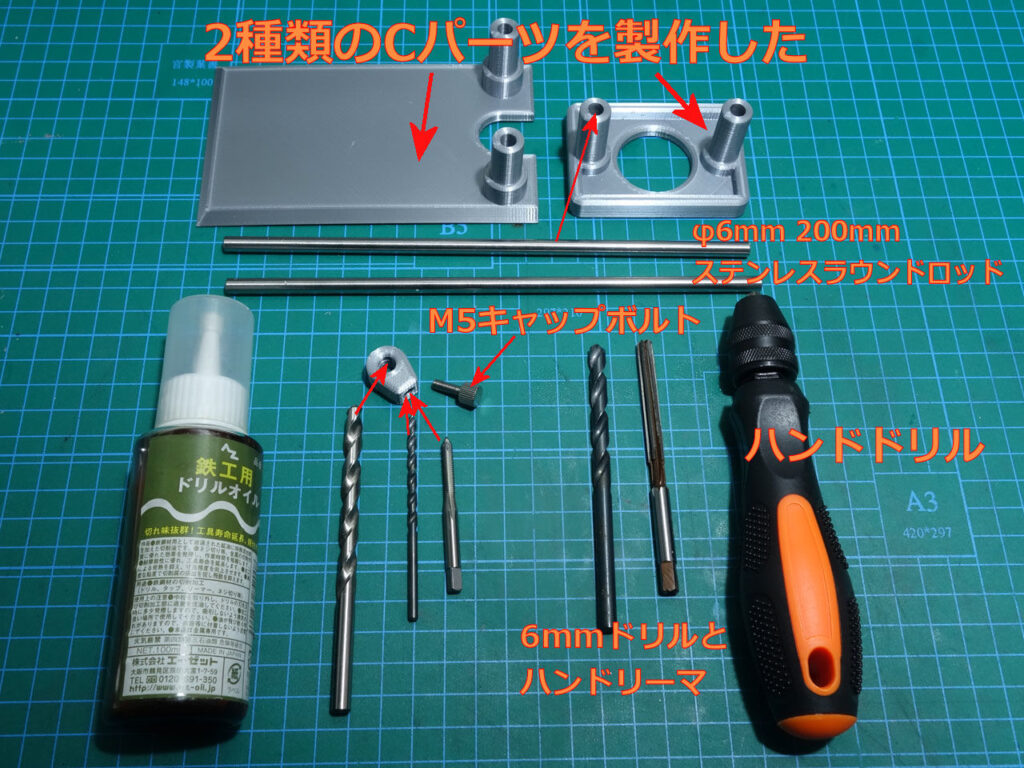
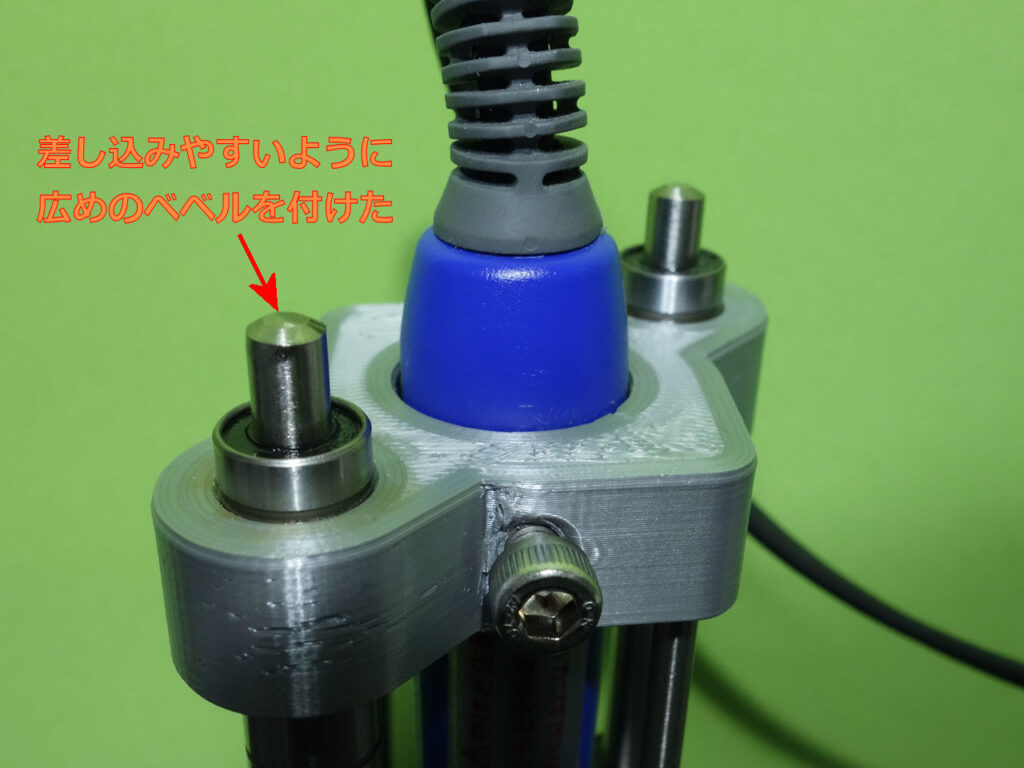
- Cパーツをワーク上にのせてハンダごてを下へスライドさせる.画像はPLAのテストピースにM4 8mmのインサートナットをおいて,370℃にセットしたFX600で圧入したものである.高めの温度だと圧力は容易だが,インサートナットの反対面のネジ穴から溶けたPLAが浸入してくる
- その場合貫通穴ならタップでさらえばよい.問題なのは閉じた下穴の場合である.厚みが十分あるワークならタップできるような長い下穴を付与しておけばいいが,そんなケースは少ないかもしれない.その辺りの対策は後々試して紹介しようと思う
- 35mm+25mmの押しバネを使用した.インサートナットの穴の真上を狙ってCパーツを保持する.ナット内にチップを挿入しすこし加圧する.PLAが軟化すると少しの力で沈んでいく.好みの圧入位置で加圧をやめて力を抜くと自然と真上にチップは離れていく
- PLAが硬化する前にワークをひっくり返し平面に押し付ける.あるいはワークはそのままで,金属製平らな板をナットの上に被せて押しつけてもよい.ワークの形状で色々と試してみるとよい
- 押しバネは内径さえ合えば,好みの線径や長さを替えてみるのもよい.あまり柔らかいとハンダごての自重で下がってしまうので注意が必要である
- ワークの上面にある程度Cパーツがのれば,垂直軸は確保できる.それも難しい場合はもう1つのCパーツが有効かもしれない.インサートナット上にオーバーハングするようにつき出して使うCパーツである.ワーク上のインサートナットとの高さ調整に適当な台の上にのせて反対側に重石をのせる.あわせて押しバネも適当な長さものを選択する.Cパーツの基底面から下方でも圧力可能である
- 水平に圧入する場合も,適当な台を使って位置決めする.Cパーツの基底面に両面テープを貼って,ワークに固定するとずれずに圧力できる.ワークの形状次第なのだが
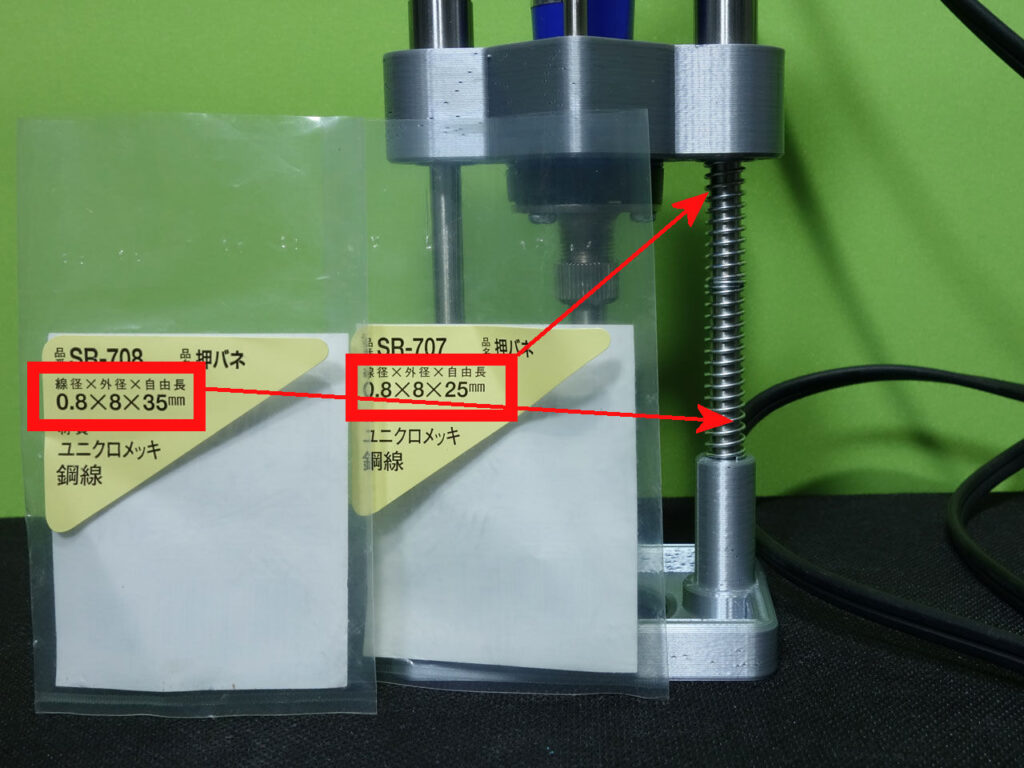
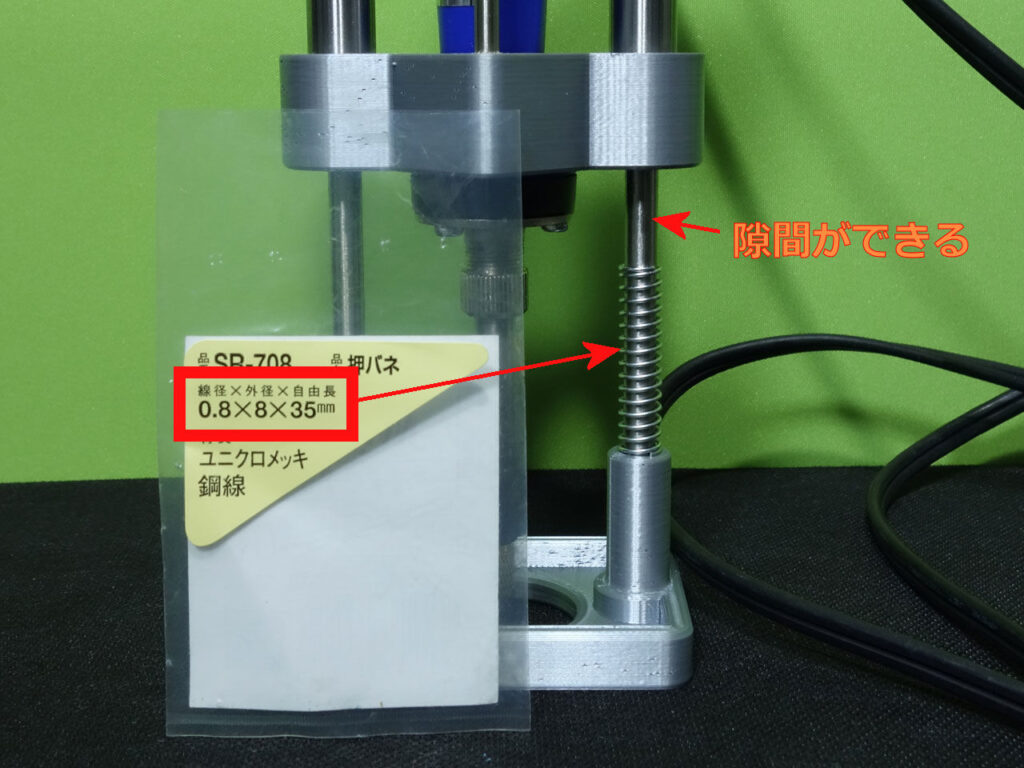
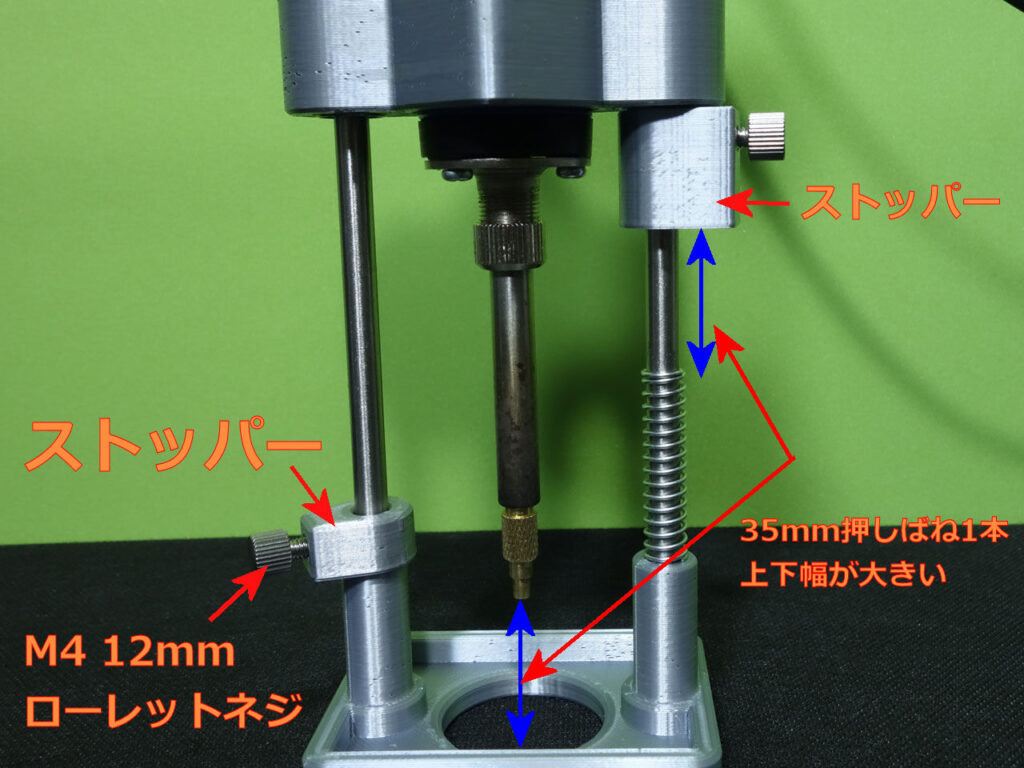
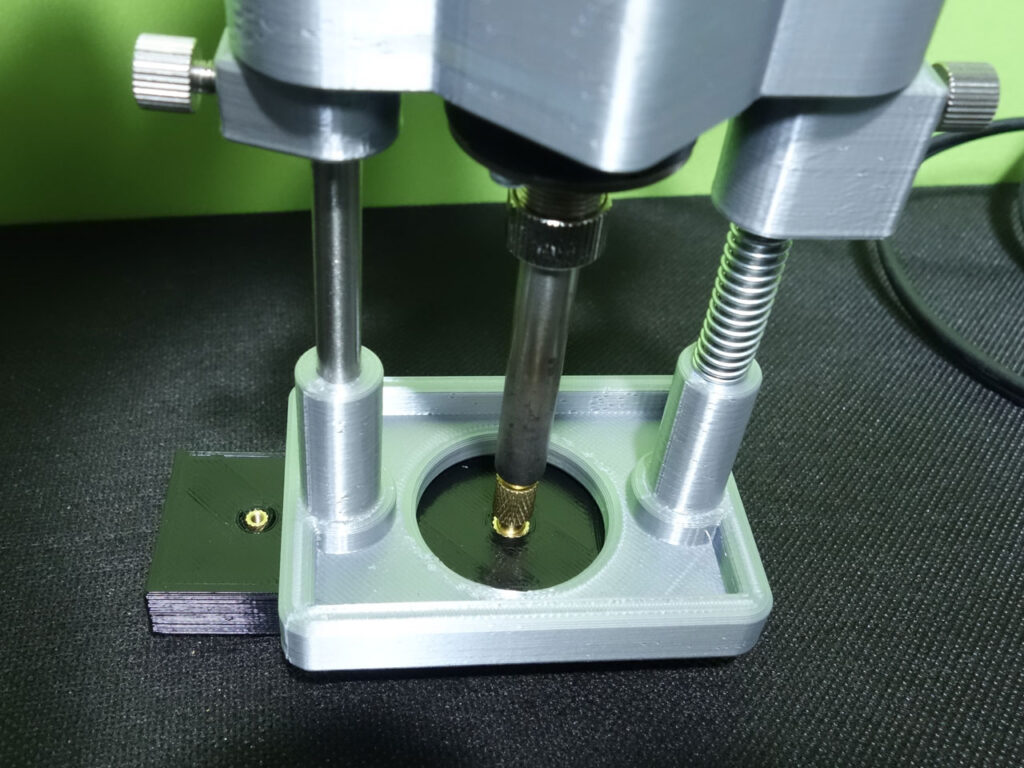
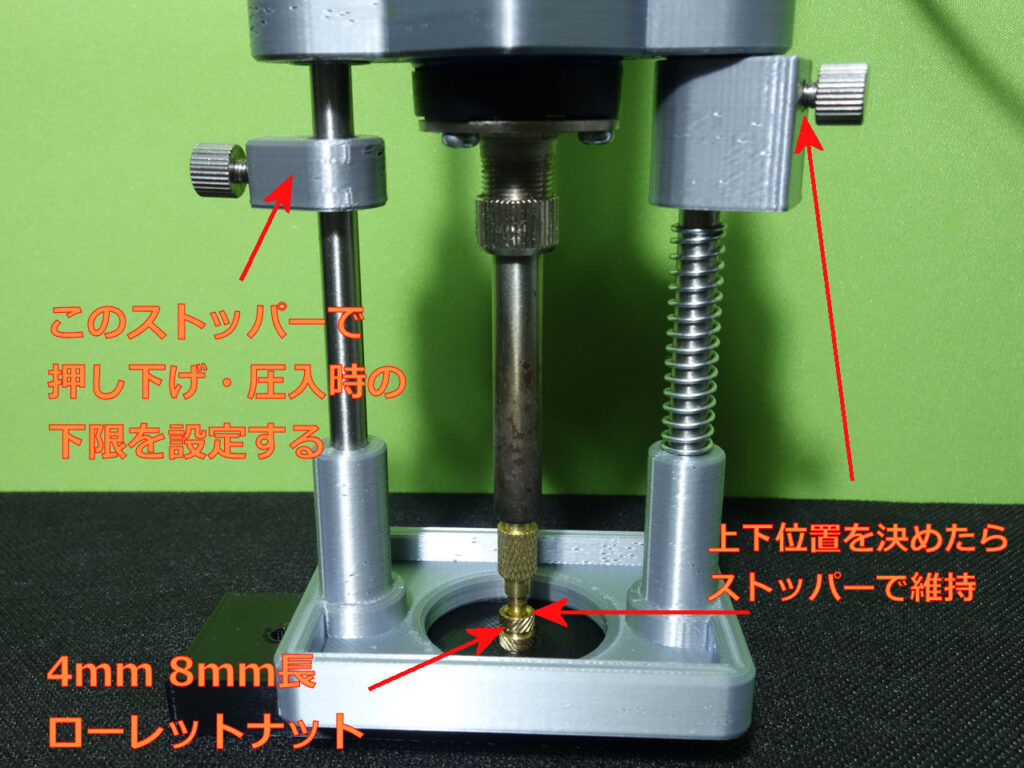
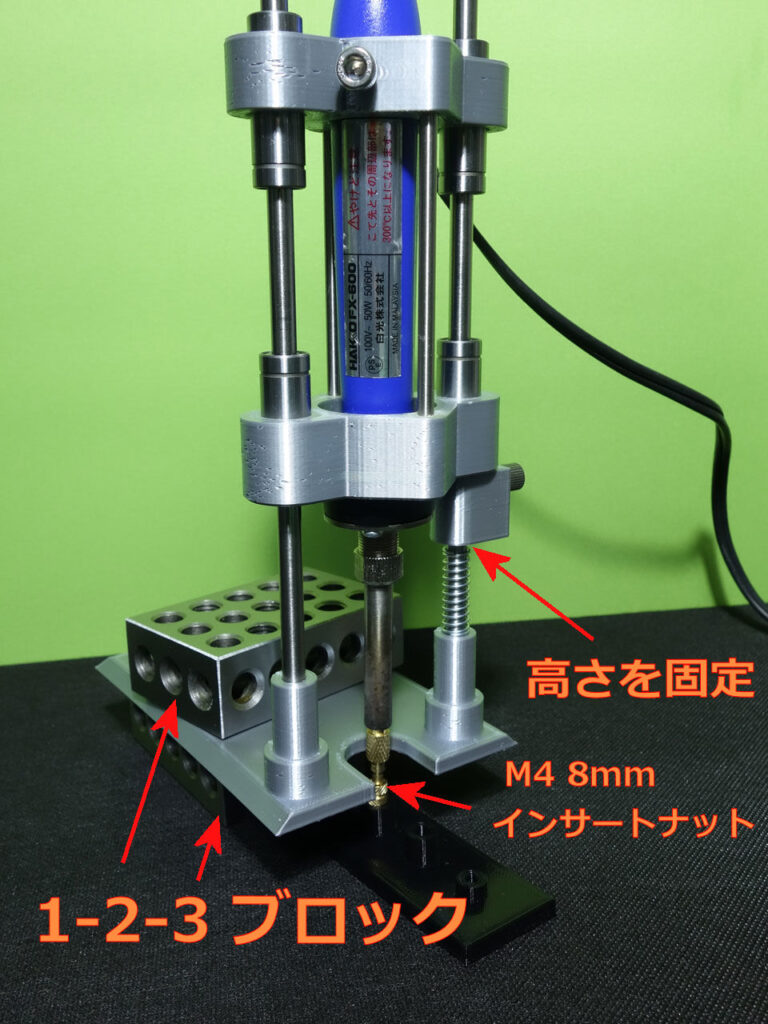
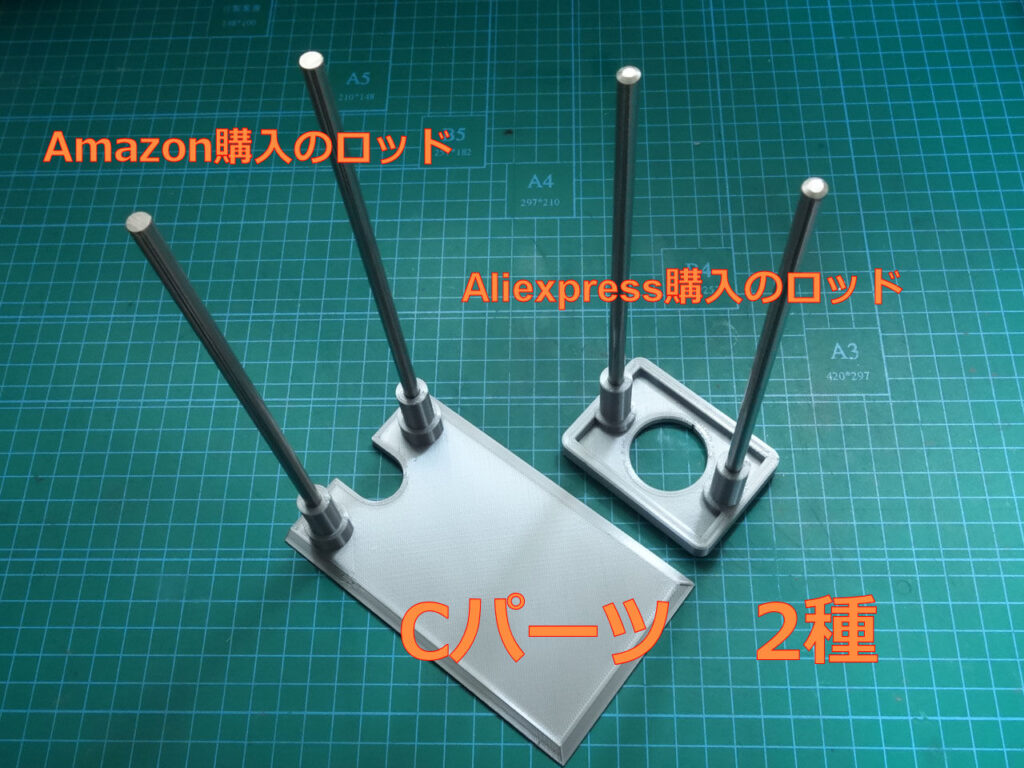
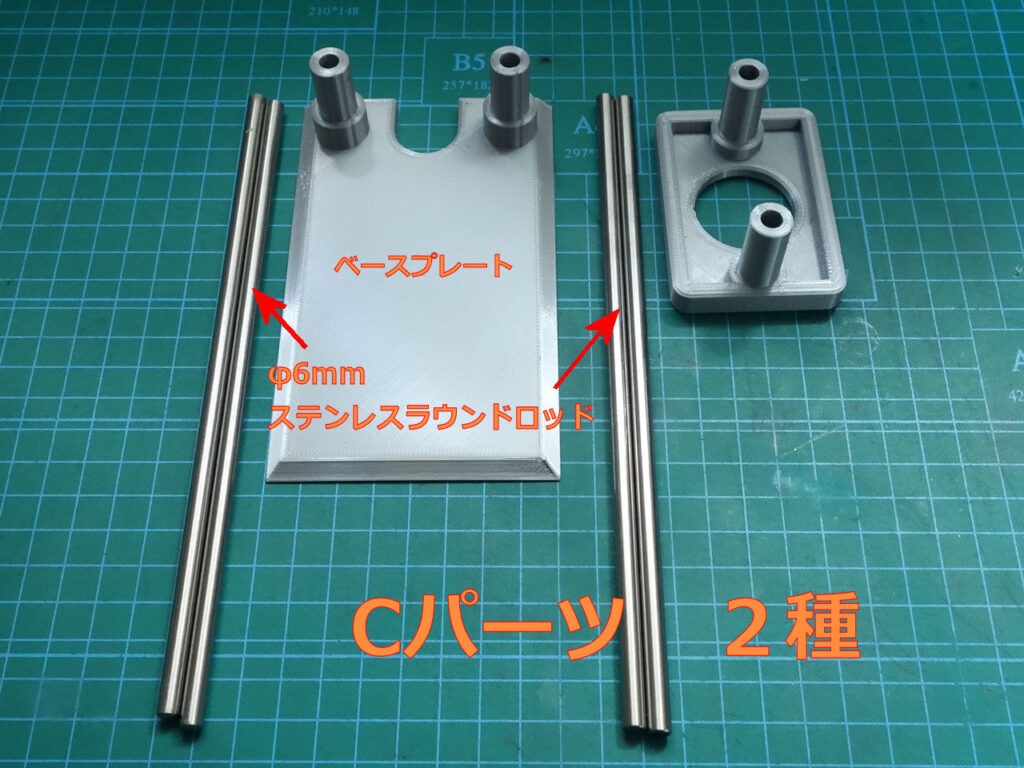
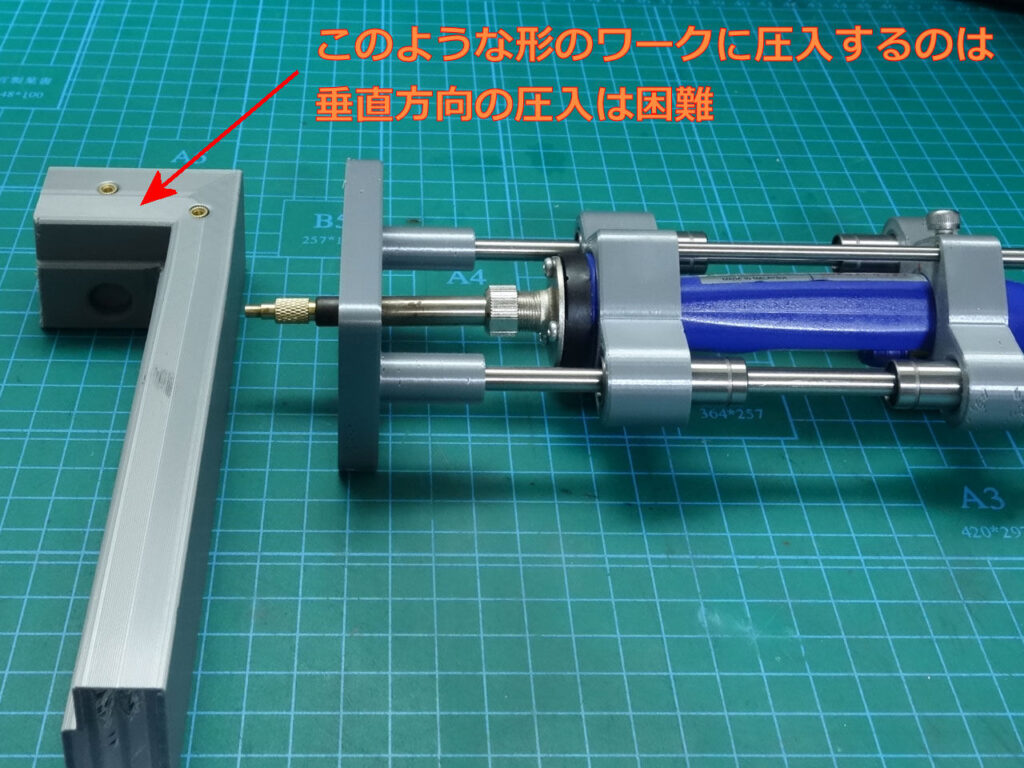
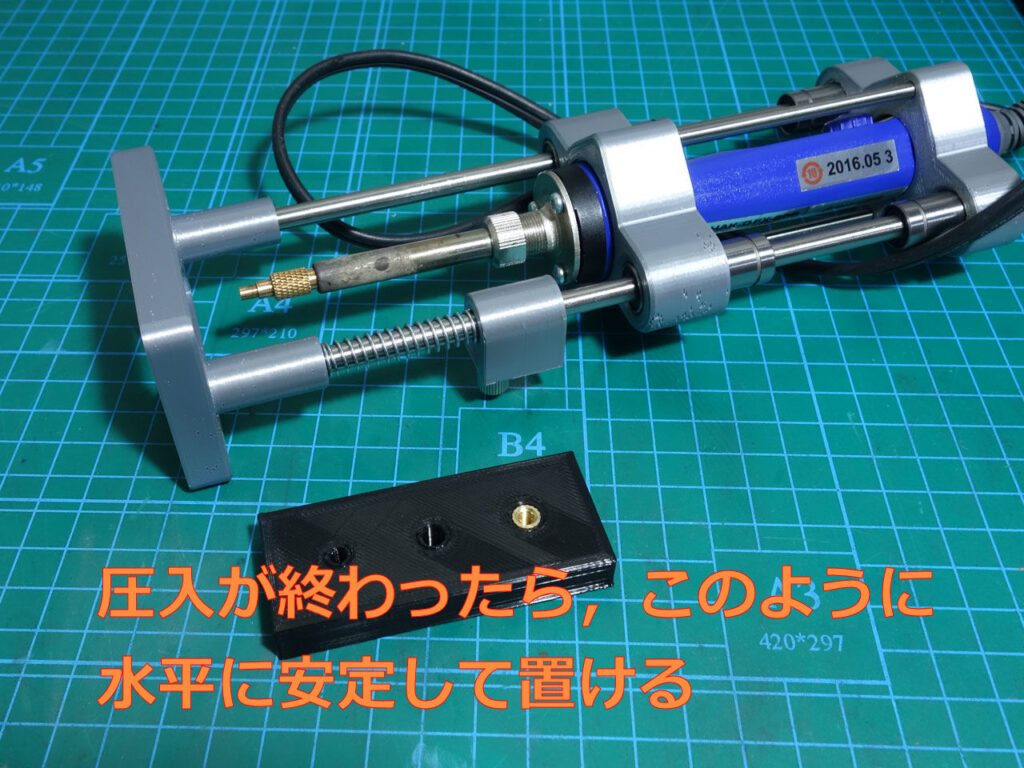
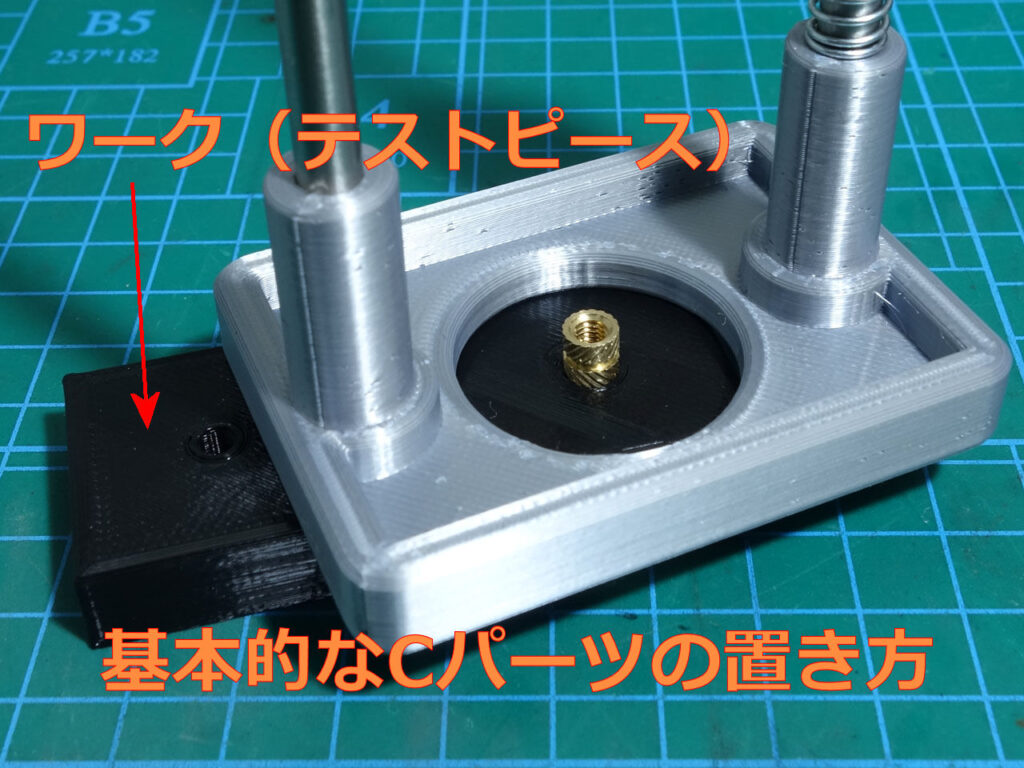
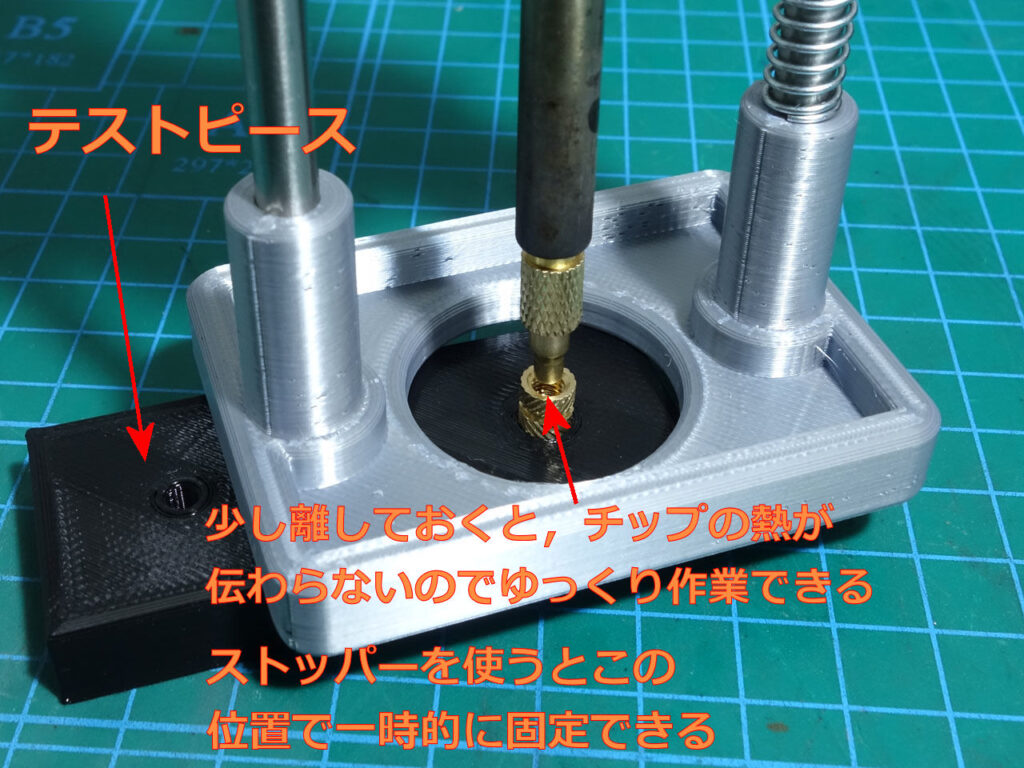
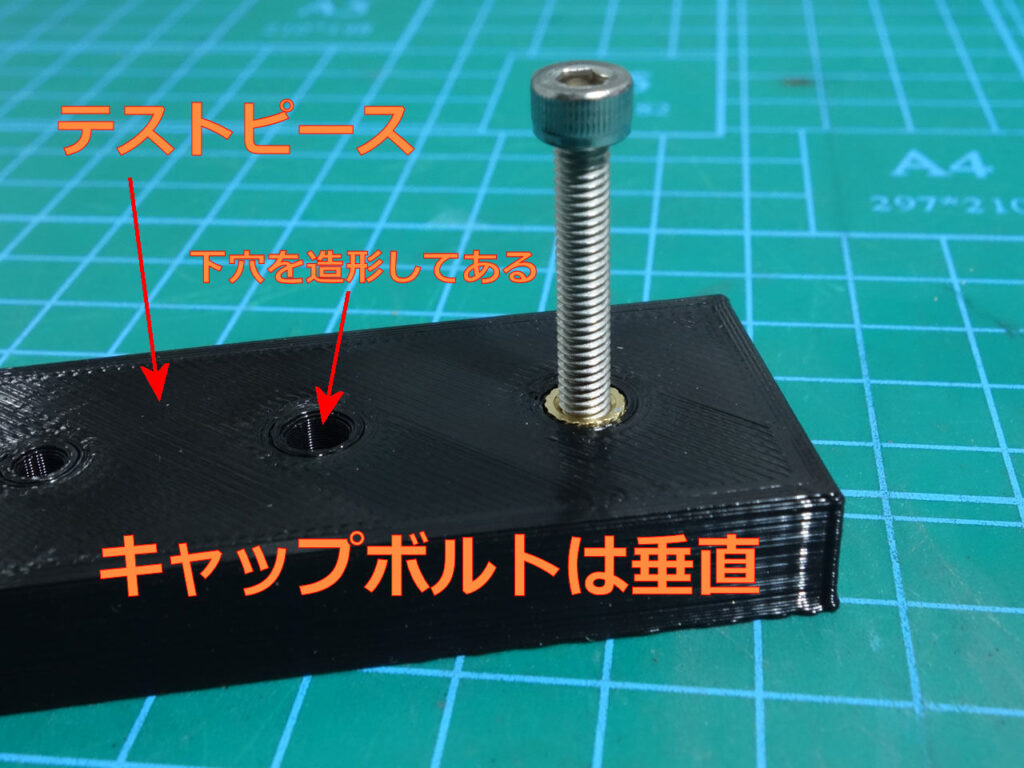
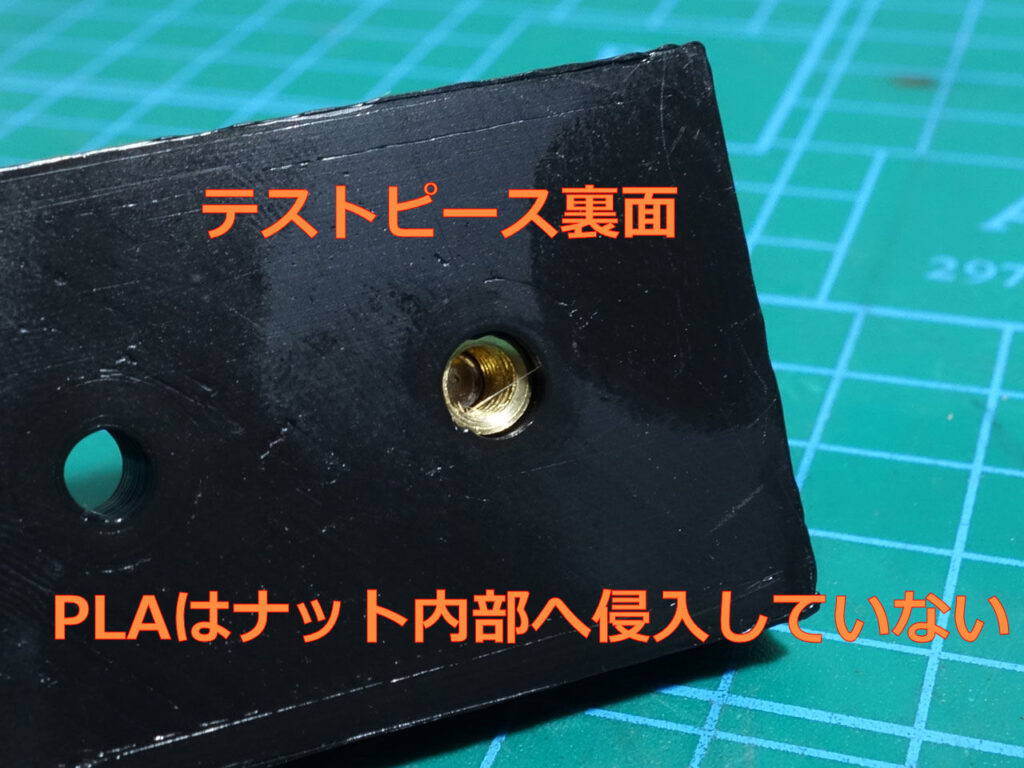
最終バージョンで購入した部材のリスト